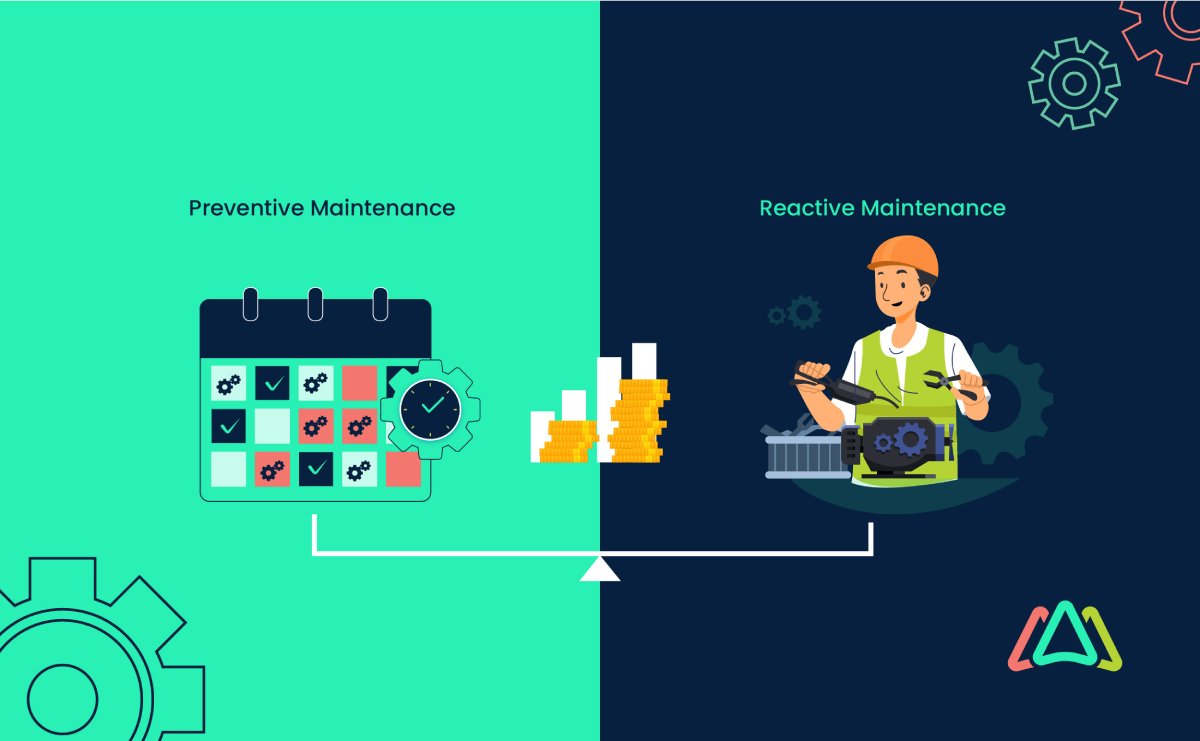
Cost-Benefit Analysis of Preventive Maintenance vs. Reactive Maintenance
Maintenance is a critical aspect of ensuring the optimal functioning and longevity of equipment and systems across various industries. It involves a proactive effort to preserve assets and prevent unexpected breakdowns that can disrupt operations. Two primary approaches to maintenance are Preventive Maintenance and Reactive Maintenance, each offering distinct methodologies for managing assets.
Preventive maintenance is a systematic approach that involves scheduled inspections, repairs, and replacements to ensure the continued operational efficiency of equipment. It aims to prevent failures before they occur, typically based on predefined time intervals, equipment usage, or specific conditions.
Reactive maintenance, on the other hand, is a corrective approach where maintenance activities are performed in response to equipment failures or breakdowns. Instead of scheduled interventions, repairs are initiated as a reaction to identified issues, often resulting in unexpected downtime.
Maintenance plays a pivotal role in the functionality, safety, and overall performance of assets across diverse industries. Key aspects include:
- Operational Continuity: Maintenance ensures that equipment and systems remain in optimal condition, minimizing the risk of unexpected failures and downtime that could disrupt regular operations.
- Safety: Regular maintenance is important for ensuring the safety of both personnel and the surrounding environment. It helps identify and address potential hazards, reducing the likelihood of accidents.
- Compliance: Many industries operate under strict regulatory frameworks. Maintenance activities are often required to comply with safety standards, environmental regulations, and other legal requirements.
- Asset Longevity: Well-maintained equipment tends to have a longer lifespan, optimizing the return on investment and reducing the need for premature replacements.
Significance of Cost-Benefit Analysis
Decisions regarding whether to adopt preventive or reactive strategies are important and have significant financial implications. Conducting a thorough cost-benefit analysis is essential for several reasons:
1. Resource Allocation
Limited resources, whether financial or manpower, need to be strategically allocated. Cost-benefit analysis assists in determining the most efficient use of resources to achieve maintenance goals.
2. Risk Mitigation
Understanding the potential costs associated with equipment failures allows businesses to proactively mitigate risks through preventive measures, reducing the overall impact on operations.
3. Long-Term Savings
While preventive maintenance may involve upfront costs, the long-term savings, including reduced downtime and extended equipment lifespan, can outweigh the immediate expenses. Cost-benefit analysis helps in evaluating these long-term financial implications.
The Financial Impact of Preventive Maintenance
Preventive Maintenance is a proactive strategy designed to prevent equipment failures and optimize operational efficiency. While it involves some upfront costs, the financial impact of preventive maintenance is multi-faceted, offering long-term benefits that often outweigh the costs.
1. Initial Investment
Equipment and Tools:
Preventive maintenance necessitates the acquisition of specialized tools and equipment tailored to the needs of different assets. While this incurs an initial investment, these tools are important for conducting regular inspections, lubrications, and minor repairs. The upfront cost is an essential consideration, but the efficiency gained in maintenance processes can lead to substantial savings over time.
Training and Education:
Properly implementing preventive maintenance requires a skilled workforce. Investing in training and education programs for maintenance personnel ensures that they are proficient in utilizing the latest techniques, tools, and technologies. Though this involves upfront costs, the enhanced skill set contributes to more effective and efficient maintenance practices, ultimately reducing the likelihood of errors and minimizing downtime.
2. Ongoing Costs
Labor Expenses:
Regular inspections and maintenance activities demand dedicated labor resources. While this incurs ongoing costs, it is important to view labor expenses as an investment in the operational health of the equipment. Skilled personnel can identify potential issues early on, preventing major breakdowns and reducing the need for costly emergency repairs. Over time, the proactive nature of preventive maintenance can contribute to a more stable and predictable labor cost structure.
Replacement Parts and Materials:
Ongoing preventive maintenance requires a steady supply of replacement parts and materials. While there is a continuous cost associated with procuring these items, they are typically less expensive than the major components required for reactive repairs. The strategic replacement of parts before they fail can prevent costly disruptions in operations, leading to a more predictable and controlled budget for replacement materials.
3. Potential Savings
Reduced Downtime:
One of the most significant financial advantages of preventive maintenance is the reduction in downtime. Scheduled maintenance activities are planned in advance, minimizing the impact on production schedules. The proactive identification and resolution of potential issues during preventive maintenance prevent unexpected breakdowns, ensuring that equipment is consistently available for use. This reduction in downtime translates directly into increased operational efficiency and revenue generation.
Extended Equipment Lifespan:
Regular maintenance contributes to the prolonged lifespan of equipment. By addressing wear and tear before it escalates, preventive maintenance minimizes the need for premature replacements. While this may not yield immediate savings, the long-term benefit is substantial. Businesses can maximize their return on investment as equipment continues to function optimally well beyond its expected lifespan, reducing the frequency of capital expenditures for replacements.
The Financial Impact of Reactive Maintenance
Reactive Maintenance involves addressing equipment failures after they occur, and while it may seem like a cost-effective approach initially, the financial implications can be substantial in the long run. Understanding the various financial aspects associated with reactive maintenance is important for organizations aiming to strike a balance between cost-effectiveness and operational efficiency.
1. Immediate Costs
Emergency Repairs:
One of the most notable immediate costs of reactive maintenance is the expense incurred during emergency repairs. These repairs are often unplanned and require swift action to restore equipment functionality. Emergency repairs can involve the need for specialized technicians, overnight shipping of parts, and expedited services, all of which contribute to elevated costs compared to scheduled maintenance activities.
Overtime Wages:
Reactive maintenance often requires immediate attention, and this urgency may lead to overtime work for maintenance personnel. Overtime wages can significantly escalate the labor expenses associated with reactive repairs. While it may be necessary to address critical issues promptly, the financial impact of overtime work should be carefully considered when evaluating the overall cost-effectiveness of maintenance strategies.
2. Indirect Costs
Production Losses:
Probably the most significant indirect cost of reactive maintenance is the loss of production. When equipment fails unexpectedly, production lines come to a halt, resulting in downtime that directly translates to revenue losses. The longer it takes to address and rectify the issue, the more significant the impact on production schedules and, subsequently, the bottom line.
Customer Dissatisfaction:
Downtime and delays caused by reactive maintenance can lead to customer dissatisfaction. Unfulfilled orders, missed deadlines, and inconsistent service delivery can damage a company's reputation and customer relationships. The intangible cost of customer dissatisfaction can have lasting consequences, affecting future business opportunities and customer loyalty.
3. Long-Term Implications
Increased Replacement and Repair Costs:
Reactive maintenance often leads to higher replacement and repair costs over time. When equipment is allowed to run to fail, the damage may extend beyond the initial issue, impacting multiple components. This can result in more extensive repairs or the need for complete equipment replacement, both of which come with significant financial implications.
Impact on Overall Business Profitability:
The cumulative effect of immediate and indirect costs associated with reactive maintenance can have a profound impact on overall business profitability. Unplanned expenses, coupled with production losses and potential customer dissatisfaction, erode profit margins and hinder the organization's ability to invest in growth opportunities. As reactive maintenance becomes a pattern, the business may find itself caught in a cycle of increased costs and diminished profitability.
While reactive maintenance may seem like a cost-saving measure in the short term, its financial implications extend far beyond immediate repair expenses. Businesses should carefully weigh the costs of emergency repairs, overtime wages, production losses, and customer dissatisfaction against the potential benefits of a proactive and preventive maintenance strategy. Adopting a strategic and forward-thinking approach to maintenance is essential for long-term financial sustainability and operational success.
Long-Term Benefits of Preventive Maintenance
Preventive Maintenance offers a range of long-term benefits that extend beyond immediate cost considerations. By proactively managing equipment health, businesses can cultivate a more reliable and sustainable operational environment.
1. Improved Equipment Reliability
Minimization of Unplanned Downtime:
One of the key long-term benefits of preventive maintenance is the substantial reduction in unplanned downtime. By systematically addressing potential issues before they escalate, organizations can ensure that their equipment operates with greater reliability. This translates into consistent production schedules, fewer disruptions, and a more predictable workflow.
Extended Equipment Lifespan:
Regular, proactive maintenance contributes to the extended lifespan of equipment. By identifying and addressing wear and tear early on, preventive maintenance prevents the premature failure of critical components. This not only reduces the frequency of replacements but also maximizes the return on investment for capital-intensive assets.
According to a study by the Aberdeen Group, organizations that implement preventive maintenance programs through CMMS experience a 32% improvement in equipment reliability.
2. Enhanced Safety and Compliance
Identification and Mitigation of Safety Hazards:
Preventive maintenance involves thorough inspections, allowing organizations to identify and address safety hazards before they become critical issues. This commitment to safety not only protects personnel and the surrounding environment but also ensures compliance with stringent regulatory requirements. Avoiding accidents and maintaining a safe working environment can lead to cost savings related to legal consequences and damage control.
Adherence to Regulatory Standards:
Many industries operate under strict regulatory frameworks. Preventive maintenance aids in consistently meeting and exceeding these standards. By regularly inspecting equipment and ensuring compliance with safety regulations, organizations mitigate the risk of regulatory fines and penalties. Proactive measures demonstrate a commitment to industry best practices, fostering a positive relationship with regulatory bodies.
3. Better Planning and Resource Allocation
Predictable Budgeting:
Implementing preventive maintenance allows organizations to predict and control maintenance costs more effectively. With scheduled inspections and repairs, businesses can plan for maintenance expenses in advance, avoiding the financial uncertainties associated with reactive approaches. This predictability enables better budgeting and financial management.
Optimized Resource Allocation:
Proactive maintenance fosters a culture of optimization in resource allocation. By identifying and addressing issues before they escalate, organizations can allocate resources, including labor and replacement parts, more efficiently. This reduces waste and ensures that resources are directed toward necessary work rather than avoidable emergency situations.
Enhanced Operational Planning:
Preventive maintenance provides a foundation for better operational planning. With equipment reliability and safety assured, businesses can develop more robust production schedules and project timelines. The ability to plan effectively contributes to increased overall efficiency, customer satisfaction, and a positive impact on the bottom line.
Balancing Act: Finding the Optimal Maintenance Strategy
Organizations must navigate industry-specific requirements, assess equipment criticality, and work within budget constraints to determine the most effective maintenance management strategy.
1. Factors Influencing the Decision
Industry-Specific Requirements:
Different industries have unique operational demands and regulatory standards. The nature of equipment usage, environmental conditions, and safety protocols varies significantly. As such, industry-specific requirements play a pivotal role in shaping the maintenance strategy. For instance, industries with high safety standards may lean towards preventive maintenance to ensure compliance, while others may prioritize cost-effectiveness.
Equipment Criticality:
Not all equipment within an organization carries the same level of criticality. Some assets may be mission-critical, directly impacting production schedules and revenue generation, while others may have a lower impact on operations. Understanding the criticality of each piece of equipment is essential for tailoring maintenance strategies accordingly. Critical assets may benefit from more frequent preventive measures, while less critical ones may lean towards a reactive approach. For example, preventive maintenance should be applied to boilers but is not necessary for inexpensive printers.
Budget Constraints:
Budgetary considerations inevitably shape maintenance decisions. Organizations must balance the desire for comprehensive preventive maintenance with financial constraints. The upfront costs associated with preventive measures need to be weighed against potential long-term savings and the impact of reactive strategies on overall profitability. A careful evaluation of budget constraints ensures that the chosen maintenance strategy aligns with the financial realities of the organization.
2. Developing a Hybrid Approach
Combining Preventive and Predictive Elements:
The optimal maintenance strategy often lies in combining elements of preventive and predictive maintenance. Preventive maintenance provides a structured framework for routine inspections and repairs, addressing known issues. On the other hand, predictive maintenance leverages data and technology to anticipate failures based on equipment condition and usage patterns. Integrating both approaches creates a comprehensive strategy that maximizes equipment reliability while minimizing unnecessary interventions.
Adaptive Strategies Based on Equipment Condition and Usage:
Maintenance strategies need to be adaptive, responding to the condition and usage patterns of each asset. Rather than adhering rigidly to a single approach, organizations can tailor their maintenance strategies based on real-time data. Utilizing sensors, Internet of Things (IoT) devices and data analytics allows businesses to assess equipment health, predict potential failures, and adjust maintenance schedules accordingly. This adaptability optimizes resource allocation and ensures that maintenance efforts are focused where they are most needed.
Financial Aspects of Investing in a CMMS for Effective Maintenance Management
Organizations are increasingly turning to Computerized Maintenance Management Systems (CMMS) as a strategic investment. A well-implemented CMMS not only streamlines both preventive and reactive maintenance but also yields substantial financial benefits.
1. Initial Investment in CMMS Implementation
Software Acquisition Costs:
Implementing CMMS software involves an initial investment in software acquisition. While this involves upfront costs, they pale in comparison to the long-term benefits of improved maintenance efficiency, reduced downtime, and better resource utilization.
Training and Onboarding:
Training staff on CMMS usage is an important component of implementation. Although there are associated costs with training and onboarding, this investment pays dividends in terms of increased user proficiency, minimized errors, and the effective utilization of CMMS features. Most modern CMMS platforms are SaaS (Software as a Service), and they offer many training and customer support services that are delivered remotely and can be accessed 24/7, lowering costs compared to the past.
Data Migration and Integration:
Migrating existing maintenance data and integrating the CMMS with other enterprise systems may incur additional costs. However, the streamlined data management and interoperability gained from such integration contribute to better decision-making and enhanced overall operational efficiency. Data migration costs are largely a function of the size and complexity of the operation. Migrating data for companies with 500 assets or less will be lower than those that have assets in the thousands.
2. Ongoing Costs and Maintenance Efficiency Gains
Labor Savings:
CMMS automates many routine tasks, reducing the need for manual data entry and paperwork. This leads to labor savings as maintenance personnel can focus on more value-added activities, ultimately contributing to increased productivity and cost-effectiveness.
Predictive Maintenance Benefits:
Advanced CMMS solutions often include predictive maintenance capabilities. By leveraging data analytics and machine learning, organizations can anticipate equipment failures, schedule maintenance activities proactively, and avoid costly unplanned downtime. This predictive approach significantly reduces reactive maintenance costs and also reduces the costs of performing unnecessary preventive maintenance.
Reduced Downtime and Production Losses:
CMMS facilitates efficient scheduling of preventive maintenance tasks, minimizing downtime and preventing unexpected breakdowns. The direct financial impact of reduced downtime includes increased production output and revenue generation, contributing to a positive return on investment.
3. Cost Savings through Better Resource Allocation
Optimized Inventory Management:
CMMS enables organizations to track inventory levels, manage stock efficiently, and reduce excess inventory costs. With real-time insights into spare parts usage and availability, businesses can optimize inventory levels, ensuring that necessary parts are on hand without unnecessary surplus.
Strategic Resource Allocation:
CMMS provides data-driven insights into equipment performance, helping organizations allocate resources more strategically. By identifying critical assets and prioritizing maintenance efforts, businesses can maximize the impact of their resources on overall operational efficiency.
The U.S. Department of Energy conducted a study indicating that preventive maintenance programs, when supported by CMMS, can lead to cost savings of up to 12-18% compared to reactive maintenance.
4. Improved Decision-Making and Reporting
Data-Driven Decision-Making:
CMMS generates comprehensive reports and analytics, offering insights into maintenance performance, equipment health, and resource utilization. Informed decision-making based on real-time data allows organizations to continuously optimize maintenance strategies for maximum efficiency and cost-effectiveness.
Improved Compliance and Documentation:
CMMS helps organizations maintain compliance with industry regulations and standards by providing a centralized platform for documentation and audit trails. Avoiding non-compliance penalties and fines contributes to overall financial well-being.
5. Long-Term Financial Sustainability and ROI
Extended Equipment Lifespan:
The combination of preventive maintenance scheduling and predictive insights provided by CMMS contributes to the extended lifespan of equipment. This leads to long-term savings by reducing the frequency of major repairs and premature replacements.
Positive Return on Investment (ROI):
While there are initial costs associated with implementing a CMMS, the long-term financial benefits often far exceed these expenses. Increased operational efficiency, reduced downtime, and optimized resource allocation contribute to a positive return on investment over the equipment’s lifecycle.
TABLE OF CONTENTS
Keep Reading
Ever find yourself checking into a luxury hotel and expecting a relaxing stay, only to find a ...
11 Apr 2025
Organizations are witnessing swift changes in the business environment and confronting a ...
8 Apr 2025
Last month, news outlets and the entire internet was abuzz with the return of NASA astronauts ...
3 Apr 2025
What comes first - CMMS or predictive maintenance? If your answer is either, it is correct. ...
28 Mar 2025
Artificial intelligence (AI) talk has become commonplace. Today, engaging in business-focused ...
27 Mar 2025
Imagine a world where machines predict, diagnose, and fix their issues before they fail. This ...
25 Mar 2025
A facility maintenance plan is at the core of a facility’s operations. This organized ...
21 Mar 2025
Think of managing your maintenance operations like managing a championship sports team. Just ...
21 Mar 2025
The maintenance sector is battling a severe talent shortage that threatens to undermine ...
7 Mar 2025
Manufacturing maintenance is the backbone of industrial efficiency, ensuring machines run ...
5 Mar 2025
No one likes playing a guessing game when equipment breaks down. Yet, maintenance teams often ...
4 Mar 2025
The size of the preventive maintenance software market is discussed in millions of dollars, ...
4 Mar 2025
The organizational structure and corporate hierarchy vary from company to company. Large ...
28 Feb 2025
Maintenance procedures are essential for ensuring the longevity and reliability of machinery ...
21 Feb 2025
Sustainability is no longer just a buzzword; it's a critical component of corporate social ...
20 Feb 2025
A Computerized Maintenance Management System (CMMS) relies on accurate, well-organized data ...
18 Feb 2025
In an era where technology drives operational efficiency, Computerized Maintenance Management ...
14 Feb 2025
A Computerized Maintenance Management System (CMMS) is a key component of modern maintenance ...
13 Feb 2025
Introduction Maintenance management is the foundation of maintenance operations in industries ...
11 Feb 2025
Introduction A Computerized Maintenance Management System (CMMS) is software designed to help ...
7 Feb 2025