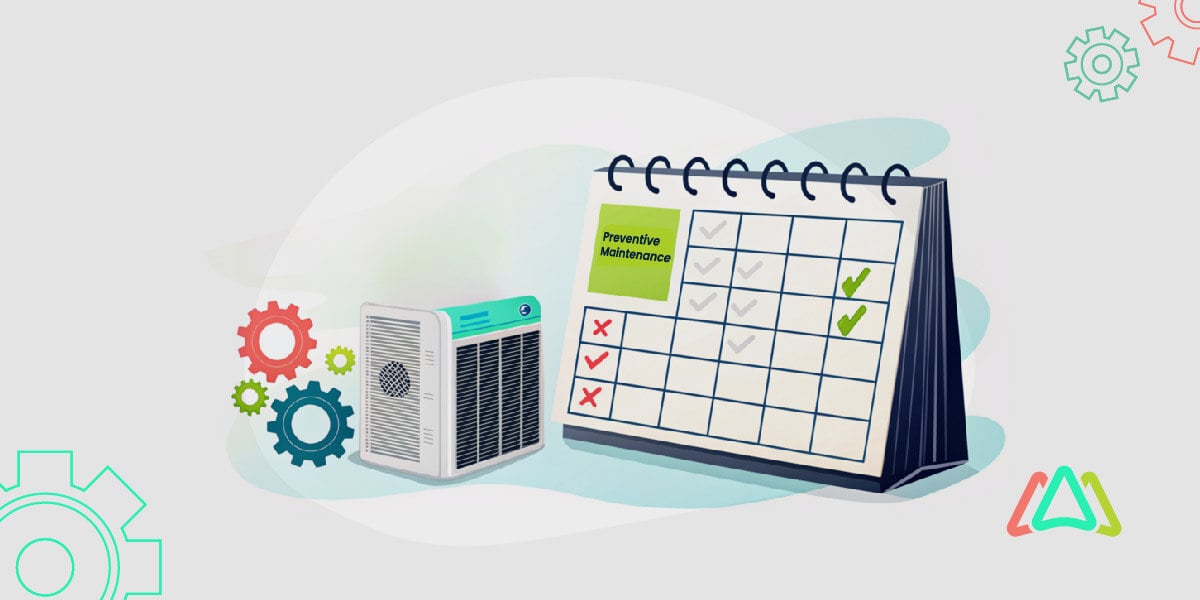
A Step-by-step Guide to Creating a Preventive Maintenance Work Order
Think of managing your maintenance operations like managing a championship sports team. Just like every team player needs to be in peak condition to win, so does every asset, tool, and machine to achieve high-performance outcomes. When one player falters due to neglect, the whole team’s performance can take a nosedive, leading to missed goals and losses.
That’s where preventive maintenance comes in, acting as your strategic coach, keeping every part of your operation in top shape through proactive care and timely adjustments.
Preventive maintenance is a proactive approach to equipment upkeep designed to keep assets running smoothly and efficiently. Rather than waiting for machines to break down, PM involves regular, scheduled maintenance tasks to catch and fix potential issues before they escalate. By maintaining equipment on a routine basis, businesses can minimize downtime, extend the lifespan of their assets, and avoid costly emergency repairs.
In many industries, equipment downtime translates directly into lost revenue, whether it’s due to halted production, delayed services, or compromised safety. Preventive maintenance addresses this by increasing asset uptime and reducing unplanned breakdowns and failures. Routine checks, adjustments, cleaning, and part replacements become regular operations activities, reducing the chance of unexpected breakdowns. As a result, preventive maintenance is essential for any business that relies on equipment to maintain productivity, quality, and customer satisfaction.
What is a Preventive Maintenance Work Order?
A preventive maintenance work order is a documented request to perform specific maintenance tasks at designated intervals. These work orders outline each preventive task, such as inspections, lubrications, or part replacements, ensuring that maintenance teams can carry out the necessary work with clear instructions and within a set timeframe. Preventive maintenance work orders serve as powerful tools to schedule and track maintenance activities, allowing businesses to:
- Extend Equipment Lifespan: Routine maintenance keeps machinery in peak condition, preventing wear and tear from accelerating over time.
- Reduce Unexpected Downtime: By addressing potential issues before they become failures, preventive maintenance work orders help prevent unplanned outages that could disrupt operations.
- Enhance Safety and Compliance: Regular maintenance reduces the risk of accidents and keeps equipment in compliance with industry regulations and safety standards.
Overall, preventive maintenance work orders offer a structured way to maintain asset health, improve operational efficiency, and help businesses avoid the risks associated with equipment failure.
Common Industries and Assets that use Preventive Maintenance Work Orders
Preventive maintenance work orders are essential across various industries that rely on machinery and equipment for daily operations. Some of the most common industries that benefit from preventive maintenance work orders include:
- Manufacturing: Machinery, conveyors, and robotic equipment require regular upkeep to avoid production delays.
- Healthcare: Medical devices, HVAC systems, and emergency power supplies need preventive maintenance to ensure patient safety and compliance.
- Hospitality: Hotels use preventive maintenance work orders for HVAC, plumbing, and kitchen equipment to maintain guest comfort and prevent disruptions.
- Transportation and Logistics: Fleets of trucks, airplanes, and ships depend on preventive maintenance to ensure reliability and safety.
- Facilities Management: Office buildings, warehouses, and schools require routine checks for HVAC, electrical systems, elevators, and safety equipment.
Overall, any industry that depends on reliable equipment can benefit from preventive maintenance work orders. By proactively addressing maintenance needs, companies can keep operations running smoothly, reduce costs, and create a safer, more efficient workplace.
Best Practices for Creating a Preventive Maintenance Work Order
A Computerized Maintenance Management System (CMMS) streamlines the process of creating, tracking, and managing preventive maintenance (preventive maintenance) work orders. By utilizing a CMMS, organizations can automate workflows, improve efficiency, and ensure maintenance tasks are completed on time.
Here’s a step-by-step guide to creating a preventive maintenance work order within a CMMS:
1. Identify Assets and Maintenance Needs
The first step in creating a preventive maintenance work order within a CMMS is to identify the assets that need regular maintenance. In the CMMS, you'll typically have a list of all assets, such as equipment, machinery, or systems.
Review the asset history and usage data to determine which ones require preventive maintenance based on factors like age, operational demands, or manufacturer guidelines.
Ensure that each asset’s details are up to date in the CMMS, including their specifications, maintenance history, and previous work orders. This information will help you tailor the work order to each asset’s specific needs.
2. Set the Frequency and Scheduling
After identifying the assets, you’ll need to determine how often maintenance should be performed for each one. CMMS systems often have built-in features to set recurring maintenance schedules based on time intervals (e.g., daily, weekly, monthly, or yearly) or usage-based triggers (e.g., operating hours, cycles, or production output).
Use the CMMS to schedule these tasks automatically, considering factors such as asset usage patterns, manufacturer recommendations, and seasonal impacts.
The system will notify you when the work order is due, ensuring that maintenance is conducted proactively and avoiding unnecessary delays.
3. Set Work Order Priorities and Assign Technicians
Once the schedule is in place, the next step is to prioritize the work orders based on the urgency and importance of each task. In the CMMS, you can assign priority levels (e.g., high, medium, or low) to each preventive maintenance work order. Critical assets that impact operations or safety should be given higher priority.
The CMMS allows you to assign specific technicians or maintenance teams to each work order. You can select technicians based on their skillset, certifications, or availability. By automating these assignments, you ensure that the right technician is dispatched for the job, improving maintenance quality and reducing delays.
4. Define Tasks and Attach Checklists
A key feature of a CMMS is the ability to create detailed work orders with specific tasks and checklists. Each preventive maintenance work order should outline the maintenance procedures, including steps like inspections, cleaning, lubricating, replacing parts, or testing.
CMMS platforms allow you to create standardized preventive maintenance checklists or procedures that can be reused for different work orders, ensuring consistency and quality.
Ensure that each task is clearly defined, with specific instructions and safety guidelines where necessary. This will help technicians complete the work accurately and reduce the risk of errors or missed steps.
Procedure checklists in the CMMS can also include photos, diagrams, or technical manuals for reference.
5. Set Completion Deadlines
Once the tasks are defined, it's important to set realistic completion timelines for each work order. The CMMS can help you determine deadlines based on task complexity and technician availability.
Setting clear deadlines ensures that maintenance is completed on time and doesn’t cause disruptions to operations.
The system can automatically notify technicians of upcoming deadlines, track the progress of the work order, and flag any delays. This enables better time management and ensures that maintenance activities do not interfere with production or service delivery.
6. Gather and Track Required Resources
A successful preventive maintenance work order requires proper planning for the resources needed. In a CMMS, you can track the parts, tools, and materials required for each task.
The system will alert you when parts are low or need to be ordered, ensuring that technicians have everything they need before beginning maintenance.
Additionally, CMMS platforms often include an inventory management feature, where you can monitor stock levels, manage suppliers, and reorder necessary items in advance. This feature reduces downtime caused by shortages of critical parts or equipment.
7. Document and Review Work Orders
The final step in the process is documenting the work completed and reviewing the outcomes. After a technician completes a preventive maintenance task, they can input the results into the CMMS, noting any issues encountered, parts replaced, or repairs made. This documentation is crucial for tracking asset performance and maintenance history.
The CMMS can generate reports on completed work orders, providing insights into maintenance trends, asset performance, and technician efficiency. Regular reviews of this data can help identify areas for improvement in maintenance scheduling, asset utilization, or technician performance.
You can also analyze historical work orders to predict future maintenance needs and adjust your preventive maintenance program accordingly.
Step-by-Step Guide to Creating a Preventive Maintenance Work Order in Click Maint
Click Maint CMMS is an easy-to-use and intuitive computerized maintenance management system designed to help businesses streamline their maintenance processes. It provides an efficient platform for managing all aspects of maintenance, from preventive tasks to reactive repairs. Follow the following steps to create a Preventive Maintenance Work Order:
Step 1: Access the Work Orders Module
To get started, navigate to the Work Orders module in Click Maint. In the top right corner, click the +Work Order button to open the New Work Order form.
Step 2: Enter Required and Optional Information
Once the New Work Order form is open, you’ll need to fill out both required and optional fields.
Admin users have the ability to customize which fields are marked as required, and they can also configure which fields should appear on the form. Fields marked with an asterisk (*) are mandatory to create the work order:
- Title: Provide a brief but clear title that explains the task (e.g., "Monthly HVAC Filter Replacement").
- Description: Offer a detailed explanation of the work to be done (e.g., "Replace air filters in HVAC units, check airflow, and clean ducts").
- Priority: Set the priority level—High, Medium, or Low—to reflect how urgent the task is.
- Category: Select the appropriate department or work category (e.g., Electrical, Plumbing, or Facility Maintenance).
- Assign To: Choose the technician or team responsible for completing the task.
- Work Type: Select Preventive to categorize the work order as part of your scheduled maintenance program.
Optional Fields:
- Upload Images or Files: Attach any relevant documents, images, or files that can help with completing the work order (e.g., diagrams, manuals, or inspection reports).
Step 3: Configure the Schedule
Now, configure the scheduling options for the preventive maintenance work order. Click Maint offers three different scheduling methods to suit your needs:
- One-Time: Select this option for a single, one-off preventive maintenance task.
- Persistent: This option is ideal for tasks that repeat regularly, based on a specific calendar date (e.g., monthly, quarterly).
- Floating: Choose this for tasks that should repeat after a set time period from the last completed task (e.g., every 6 months after the previous maintenance was finished).
In addition to the schedule type, you can also set:
- Starting From: Specify the date in the future when the first work order should be generated.
- Time to Complete: Set the estimated time frame for when the work order should be completed, ensuring it doesn’t affect other operations.
Step 4: Add Additional Information
To complete the work order and ensure all aspects are covered, you can add further details:
- Location: Specify where the work needs to be done (e.g., Warehouse A or the Main Building).
- Asset: Select the asset or equipment that requires maintenance (e.g., HVAC System, Conveyor Belt, etc.).
- Vendor: If external contractors are required, you can specify a vendor here.
- Checklist: Add a checklist of tasks that need to be completed during the maintenance job. This helps ensure all required actions are performed.
- Status: Set the current status of the work order (e.g., Pending, In Progress, or Completed).
- Time: Log the amount of time the technician spends on the task.
- Parts: Indicate the quantity and replacement needs for parts required for the maintenance task.
- Other Costs: Add any additional costs associated with the work order, such as external labor, special tools, or replacement parts.
Step 5: Save and Finalize the Work Order
Once you’ve filled in all the necessary information, click the Save button in the top right corner of the form to finalize the creation of the preventive maintenance work order. The task will be scheduled according to your chosen settings, and notifications will be sent to the assigned technician or team.
Click Maint also allows you to track the progress of the work order in real-time, providing automatic updates as the status changes (e.g., when the task is approaching, in progress, or completed). You can also track them in the calendar view:
Interactive Product Tours to Create and Update a Preventive Maintenance Work Order
1. Create a Preventive Maintenance Work Order for Rooftop Unit
Learn how to create a preventive maintenance work order for a rooftop unit by following the interactive tour. This guide covers everything from setting up your work order to selecting the appropriate schedule and assigning tasks to technicians.
2. Create a Preventive Maintenance Work Order for CNC Lathe
This product tour focuses on creating a preventive maintenance work order for a CNC lathe, ensuring that all relevant details are added to the work order. Get familiar with the system’s scheduling options, asset selection, and more.
3. Update an existing Preventive Maintenance Work Order
If you need to make updates to an existing preventive maintenance work order, this tour will guide you through the process. Learn how to adjust scheduling, include progress updates, add additional tasks, or modify the priority as needed.
Wasn’t that easy? Start a Free Trial today.
Start your 30-day FREE trial
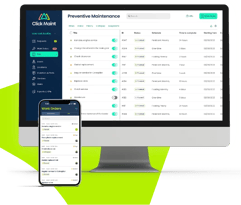
Tips for Effective Preventive Maintenance Management
Effective preventive maintenance (preventive maintenance) management is key to extending the life of equipment, minimizing downtime, and ensuring operational efficiency. Here are some valuable tips to help optimize your preventive maintenance program:
1. Schedule maintenance during off-peak times to minimize disruption
One of the best ways to ensure preventive maintenance doesn’t interfere with operations is to schedule tasks during off-peak hours. This could mean scheduling maintenance during the evening, weekends, or other periods when production or services are at a low. By minimizing disruption to daily operations, you reduce the potential impact on productivity and maintain smoother workflows. In Click Maint CMMS, you can set specific time frames for maintenance work, making it easier to coordinate tasks without disrupting critical functions.
2. Use analytics to monitor preventive maintenance effectiveness and adjust schedules
Preventive maintenance is not a “one-size-fits-all” process. It requires continuous assessment and adaptation.
Use the analytics features in your CMMS, like Click Maint, to track maintenance KPIs such as equipment downtime, repair frequency, and work order completion times. These insights will allow you to evaluate how effective your preventive maintenance program is.
If certain tasks are frequently delayed or need to be rescheduled, you can adjust the frequency or timing of those preventive maintenance tasks. Monitoring the performance of your assets and maintenance efforts ensures that you are optimizing resources and preventing unnecessary maintenance costs.
3. Keep an updated inventory of parts to avoid delays
Having the right parts available when needed is critical to ensuring maintenance tasks are completed on time. Delays in sourcing or waiting for parts can significantly impact asset reliability and prolong downtime. Keep a real-time, updated inventory of spare parts and materials in your CMMS. With Click Maint, you can track parts usage, monitor stock levels, and automate reordering when items are running low. This proactive approach helps you avoid disruptions caused by shortages and ensures your technicians have what they need to complete their tasks efficiently.
4. Train technicians on proper preventive maintenance protocols and Click Maint CMMS functionality
For a preventive maintenance program to be successful, your technicians must be properly trained on both the equipment and the systems they use. Ensure that all technicians are well-versed in preventive maintenance best practices, as well as how to effectively use the Click Maint CMMS to create, update, and track work orders.
CMMS training should cover everything from accessing work orders, filling out checklists, and documenting completed tasks to understanding how to monitor schedules and inventory. The more familiar your team is with the system, the more efficiently maintenance tasks will be executed, leading to improved asset reliability and faster response times.
Benefits of Using CMMS Software for Preventive Maintenance
Implementing a Computerized Maintenance Management System (CMMS) for preventive maintenance offers numerous benefits that can significantly improve the efficiency and effectiveness of your maintenance processes. Here's a closer look at the key advantages of using CMMS software like Click Maint:
1. Automation - Simplifies scheduling and task assignment
One of the greatest advantages of using CMMS software is automation. A CMMS like Click Maint allows you to automate the scheduling of preventive maintenance tasks based on time intervals, usage patterns, or equipment needs. This eliminates manual tracking, reduces the risk of missing scheduled maintenance, and ensures tasks are automatically assigned to the right technicians. Automation ensures your preventive maintenance program is consistent and efficient, helping prevent equipment breakdowns before they occur.
2. Data-Driven Insights - Uses historical data to improve scheduling and reduce costs
A CMMS captures valuable data about the performance and maintenance history of your assets. By analyzing historical data, you can identify trends and patterns that help improve your maintenance scheduling. For example, if certain assets tend to fail more frequently at specific intervals, you can adjust your preventive maintenance schedules to address these issues proactively. Data-driven insights also help optimize inventory management so you only order parts when necessary, reducing unnecessary stock and minimizing costs.
3. Enhanced Tracking - Tracks Work Order status, technician performance, and asset health
CMMS software provides real-time tracking capabilities, which can enhance the oversight of maintenance activities. You can track the status of work orders, monitor technician performance, and assess the health of assets over time. This visibility allows maintenance managers to identify bottlenecks, inefficiencies, or areas for improvement in the maintenance process. Additionally, the ability to track asset performance and maintenance history helps you make informed decisions about asset replacement or upgrades.
4. Cost Savings - Reduces equipment failures, unplanned downtime, and repair costs
By adhering to a structured preventive maintenance schedule, CMMS software helps reduce the risk of unexpected equipment failures, which can be costly and disruptive. By catching issues early and performing maintenance on time, you can avoid expensive repairs and unplanned downtime that could otherwise halt production or services. Additionally, with better tracking of parts and materials, you can prevent over-ordering, optimize inventory levels, and minimize unnecessary costs. The overall cost savings of using a CMMS for preventive maintenance are significant, leading to a more sustainable and efficient maintenance program.
Conclusion
A structured preventive maintenance work order process is essential to keeping your assets in optimal condition, reducing downtime, and extending the lifespan of equipment. The benefits of using CMMS software, such as Click Maint, to streamline this process are undeniable: from automation and data-driven insights to enhanced tracking and cost savings, a CMMS simplifies maintenance management and ensures that tasks are completed on time and with precision.
If you're looking to improve your preventive maintenance efforts, consider exploring a CMMS like Click Maint. It provides the tools and functionality to make your maintenance program more efficient, reliable, and cost-effective.
TABLE OF CONTENTS
Keep Reading
Ever find yourself checking into a luxury hotel and expecting a relaxing stay, only to find a ...
11 Apr 2025
Organizations are witnessing swift changes in the business environment and confronting a ...
8 Apr 2025
Last month, news outlets and the entire internet was abuzz with the return of NASA astronauts ...
3 Apr 2025
What comes first - CMMS or predictive maintenance? If your answer is either, it is correct. ...
28 Mar 2025
Artificial intelligence (AI) talk has become commonplace. Today, engaging in business-focused ...
27 Mar 2025
Imagine a world where machines predict, diagnose, and fix their issues before they fail. This ...
25 Mar 2025
A facility maintenance plan is at the core of a facility’s operations. This organized ...
21 Mar 2025
The maintenance sector is battling a severe talent shortage that threatens to undermine ...
7 Mar 2025
Manufacturing maintenance is the backbone of industrial efficiency, ensuring machines run ...
5 Mar 2025
No one likes playing a guessing game when equipment breaks down. Yet, maintenance teams often ...
4 Mar 2025
The size of the preventive maintenance software market is discussed in millions of dollars, ...
4 Mar 2025
The organizational structure and corporate hierarchy vary from company to company. Large ...
28 Feb 2025
Maintenance procedures are essential for ensuring the longevity and reliability of machinery ...
21 Feb 2025
Sustainability is no longer just a buzzword; it's a critical component of corporate social ...
20 Feb 2025
A Computerized Maintenance Management System (CMMS) relies on accurate, well-organized data ...
18 Feb 2025
In an era where technology drives operational efficiency, Computerized Maintenance Management ...
14 Feb 2025
A Computerized Maintenance Management System (CMMS) is a key component of modern maintenance ...
13 Feb 2025
Introduction Maintenance management is the foundation of maintenance operations in industries ...
11 Feb 2025
Introduction A Computerized Maintenance Management System (CMMS) is software designed to help ...
7 Feb 2025
Introduction Due to a growing awareness of the need to combat climate change, the green ...
6 Feb 2025