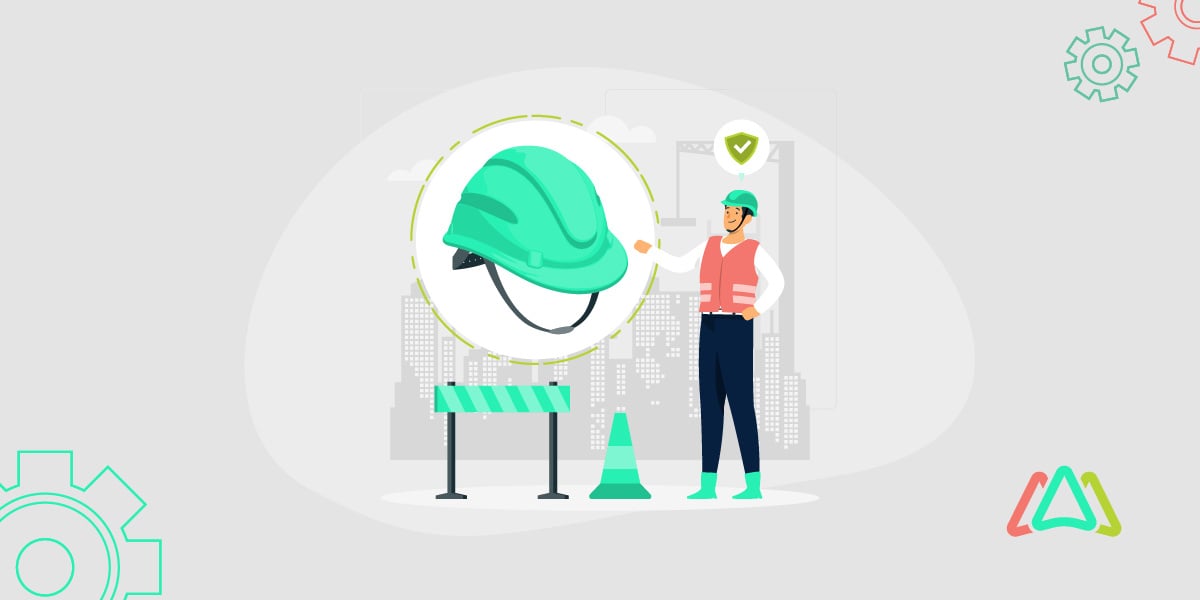
Safety First: Integrating Safety Protocols into Maintenance Procedures
Maintenance procedures are essential for ensuring the longevity and reliability of machinery and equipment in industrial settings such as manufacturing plants, construction sites, and energy facilities. However, these activities often expose workers to significant hazards, including moving machine parts, high-voltage systems, hazardous chemicals, and extreme temperatures. Without strict safety measures, routine maintenance can lead to severe injuries, fatalities, or costly equipment failures.
According to the EU-OSHA, approximately 20% of workplace injuries occur during maintenance activities due to a lack of proper safety protocols. Poor risk assessment, inadequate safety training, and insufficient documentation are common factors contributing to these incidents.
This article explores the importance of safety in maintenance procedures, examines key risk assessment methods, discusses safety compliance training and documentation, and outlines best practices for integrating safety into maintenance operations.
Importance of Safety in Maintenance Procedures?
The following are 4 reasons why policies and processes to improve safety need to be incorporated into maintenance procedures.
1. Reducing Workplace Injuries and Fatalities
Many manufacturing and industrial accidents occur during maintenance activities, exposing workers to various risks. Electrical hazards, such as accidental contact with live wires, can lead to severe injuries or fatalities. Mechanical hazards, such as getting limbs caught in moving machinery, pose significant dangers in industrial settings. Workers may also face chemical hazards, such as exposure to toxic fumes from industrial cleaning solvents, which can cause respiratory issues or poisoning. Additionally, physical hazards, like falls from heights or extreme temperatures, further increase the risk of workplace injuries.
A 2023 report by the International Labour Organization (ILO) estimated that over 2.3 million workers die annually from work-related accidents and diseases, with a significant portion linked to unsafe maintenance practices.
2. Legal and Regulatory Compliance
Failure to implement effective safety measures can result in non-compliance with OSHA, ISO 45001, and NFPA standards, which can result in hefty fines and legal penalties, increased insurance costs, and significant reputational damage to the organization.
3. Enhancing Equipment Longevity and Performance
Beyond compliance, safety protocols also contribute to equipment longevity and performance.
Unsafe maintenance practices can damage machinery, leading to unplanned downtime and expensive repairs. A safety-first approach ensures that equipment is serviced correctly, reducing wear and tear and extending operational life.
4. Boosting Workforce Morale and Productivity
Employees are more engaged and productive in workplaces where they feel safe. Implementing robust safety measures ensures a culture of responsibility and trust, reducing absenteeism and improving overall efficiency.
Key Maintenance Safety Procedures
Maintenance activities in industrial and manufacturing settings involve numerous risks, including exposure to hazardous energy, mechanical failures, and workplace accidents; the below procedures are needed for safety:
1. Risk Assessment Methods for Maintenance Safety
Before performing maintenance activities, organizations must assess potential hazards. Several risk assessment methods can be used:
Hazard Identification and Risk Assessment (HIRA)
The HIRA process is a critical safety measure in manufacturing and industrial settings. It involves systematically identifying potential hazards that could threaten workers and operations.
Once hazards are identified, the next step is evaluating the probability and severity of these risks to determine their potential impact.
Based on this assessment, organizations implement appropriate control measures, such as personal protective equipment (PPE), engineering controls, or administrative changes, to minimize risks and enhance workplace safety.
Job Safety Analysis (JSA)
JSA breaks down maintenance tasks into smaller steps, identifying risks at each stage and providing recommendations to mitigate them.
Failure Modes and Effects Analysis (FMEA)
FMEA evaluates potential machinery failure points, their impact on worker safety, and strategies for preventing failures.
What-If Analysis
This method explores hypothetical worst-case scenarios and determines appropriate safety measures.
Bowtie Analysis
This is a visual risk management tool used to identify, assess, and control workplace hazards in maintenance operations. It provides a clear illustration of how hazards originate, the preventive controls in place to reduce risk, the potential consequences of an incident, and the mitigation strategies designed to minimize impact.
For instance, a Bowtie Analysis could map out a scenario where an overheated machine leads to a fire. When combined with other risk assessment methods, such as Job Safety Analysis (JSA) and Hazard Identification and Risk Assessment (HIRA), Bowtie Analysis contributes to a more comprehensive safety strategy for maintenance teams, reducing the likelihood of accidents and ensuring regulatory compliance.
2. Implementing Lockout/Tagout (LOTO) Procedures
In 2021, as reported by Vigilant, a major automotive manufacturer was fined $1.5 million for failing to follow proper Lockout/Tagout (LOTO) procedures, which led to a fatal accident in one of its manufacturing plants.
Implementing LOTO prevents unexpected equipment startups and energy releases during maintenance. The process begins with shutdown, where equipment is powered down, followed by isolation to disconnect all energy sources. Next, lockout devices secure power sources, while tagout adds warning labels to prevent accidental operation. Finally, verification ensures the system is fully de-energized before work begins. Proper LOTO implementation enhances workplace safety and regulatory compliance.
3. Use of Personal Protective Equipment (PPE)
Personal protective equipment (PPE) minimizes safety risks in maintenance activities by providing essential protection against various hazards. Required PPE may include protective eyewear to shield against sparks, dust, and chemical splashes, gloves to protect hands from heat, chemicals, and sharp objects, respirators to filter out hazardous airborne particles, and flame-resistant clothing for safety in high-heat environments.
4. Standard Operating Procedures (SOPs) for Maintenance
A well-documented Standard Operating Procedure (SOP) is essential for maintaining safety and consistency in maintenance operations. It should include step-by-step maintenance guidelines to ensure tasks are performed correctly, a list of required PPE and safety tools to protect workers from potential hazards, and emergency response procedures to address incidents effectively. Additionally, SOPs must outline compliance requirements to meet industry regulations and workplace safety standards. By following SOPs, organizations can minimize errors, enhance worker safety, and ensure consistent adherence to best practices.
Safety Compliance Training and Documentation
Regular safety training is important for equipping workers with the knowledge to identify hazards and implement effective risk management strategies. Comprehensive training programs should cover risk assessment methods to evaluate and mitigate workplace dangers, emergency response protocols to ensure swift action during incidents, and safe handling of hazardous materials to prevent exposure-related injuries.
By prioritizing safety education, organizations can reduce workplace accidents and enhance overall operational safety.
Importance of Safety Compliance Training
Safety compliance training is essential for ensuring that workers understand and follow industry regulations, reducing workplace accidents and legal risks. It equips employees with the knowledge to identify hazards, use protective equipment correctly, and respond effectively to emergencies. Regular training also promotes a safety-first culture, improves operational efficiency, and ensures compliance with standards like OSHA and ISO 45001. By investing in continuous safety education, organizations can protect their workforce, minimize liabilities, and maintain a safe working environment.
The Role of Safety Documentation
Accurate safety documentation is essential for tracking compliance with OSHA and ISO regulations, identifying recurring hazards, and improving training programs. Key documents include incident reports that log workplace accidents, equipment maintenance records that track repairs and inspections, and employee training records that verify compliance with safety protocols. Implementing a digital safety management system can streamline documentation, reduce errors, and improve accessibility, ensuring a more efficient and compliant safety process.
Best Practices for Integrating Safety into Maintenance
The following are best practices that should be followed and integrated into maintenance processes and policies.
1. Building a Safety-First Culture
Creating a strong safety-first culture starts with leadership commitment and clear communication of safety expectations. Leaders should actively promote safety-first policies, provide ongoing training, and encourage employees to report unsafe conditions without fear of repercussions. Regular safety meetings and workshops help reinforce best practices, while open communication channels ensure workers feel empowered to raise concerns. Recognizing and rewarding employees who adhere to safety standards promotes a proactive approach to workplace safety.
Additionally, integrating safety metrics into performance evaluations ensures that safety remains a priority at all organizational levels. By cultivating a culture where safety is ingrained in daily operations, companies can reduce workplace hazards and enhance overall maintenance efficiency.
2. Leveraging Technology for Safety Compliance
Advanced technology plays a key role in enhancing maintenance safety by providing real-time monitoring and predictive insights. IoT sensors detect hazardous conditions like overheating or gas leaks, allowing for early intervention. Augmented Reality (AR) offers real-time safety guidance, helping workers follow procedures accurately. Meanwhile, AI-powered predictive maintenance analyzes data to anticipate machine failures, reducing unexpected breakdowns and improving overall safety. By integrating these technologies, organizations can create a safer and more efficient maintenance environment.
3. Emergency Preparedness and Response Plans
A well-defined emergency response plan is vital for protecting workers and minimizing risks during unforeseen incidents. Companies should establish fire drills and evacuation procedures to ensure employees can exit safely in case of a fire or hazardous situation. Emergency shutdown protocols must be in place to quickly and safely power down equipment, preventing further damage or injuries.
Additionally, providing first aid training and strategically placing medical support stations ensures immediate assistance is available during emergencies. Proper planning and regular drills enhance workplace safety and preparedness.
Future Trends in Maintenance Safety
Emerging technologies are revolutionizing maintenance safety by introducing AI-driven predictive measures that analyze workplace patterns to identify and prevent potential hazards. Autonomous maintenance robots are being developed to handle hazardous tasks, minimizing worker exposure to risks. Additionally, blockchain technology enhances safety compliance by securing documentation, ensuring transparency, and maintaining regulatory adherence.
Conclusion
Integrating safety protocols into maintenance procedures is essential for preventing workplace injuries, ensuring regulatory compliance, and enhancing operational efficiency. By adopting risk assessment methods, prioritizing safety training, maintaining accurate documentation, and leveraging emerging technologies, organizations can establish a safety-first culture that benefits both employees and business operations.
TABLE OF CONTENTS
Keep Reading
Ever find yourself checking into a luxury hotel and expecting a relaxing stay, only to find a ...
11 Apr 2025
Organizations are witnessing swift changes in the business environment and confronting a ...
8 Apr 2025
Last month, news outlets and the entire internet was abuzz with the return of NASA astronauts ...
3 Apr 2025
What comes first - CMMS or predictive maintenance? If your answer is either, it is correct. ...
28 Mar 2025
Artificial intelligence (AI) talk has become commonplace. Today, engaging in business-focused ...
27 Mar 2025
Imagine a world where machines predict, diagnose, and fix their issues before they fail. This ...
25 Mar 2025
A facility maintenance plan is at the core of a facility’s operations. This organized ...
21 Mar 2025
Think of managing your maintenance operations like managing a championship sports team. Just ...
21 Mar 2025
The maintenance sector is battling a severe talent shortage that threatens to undermine ...
7 Mar 2025
Manufacturing maintenance is the backbone of industrial efficiency, ensuring machines run ...
5 Mar 2025
No one likes playing a guessing game when equipment breaks down. Yet, maintenance teams often ...
4 Mar 2025
The size of the preventive maintenance software market is discussed in millions of dollars, ...
4 Mar 2025
The organizational structure and corporate hierarchy vary from company to company. Large ...
28 Feb 2025
Sustainability is no longer just a buzzword; it's a critical component of corporate social ...
20 Feb 2025
A Computerized Maintenance Management System (CMMS) relies on accurate, well-organized data ...
18 Feb 2025
In an era where technology drives operational efficiency, Computerized Maintenance Management ...
14 Feb 2025
A Computerized Maintenance Management System (CMMS) is a key component of modern maintenance ...
13 Feb 2025
Introduction Maintenance management is the foundation of maintenance operations in industries ...
11 Feb 2025
Introduction A Computerized Maintenance Management System (CMMS) is software designed to help ...
7 Feb 2025
Introduction Due to a growing awareness of the need to combat climate change, the green ...
6 Feb 2025