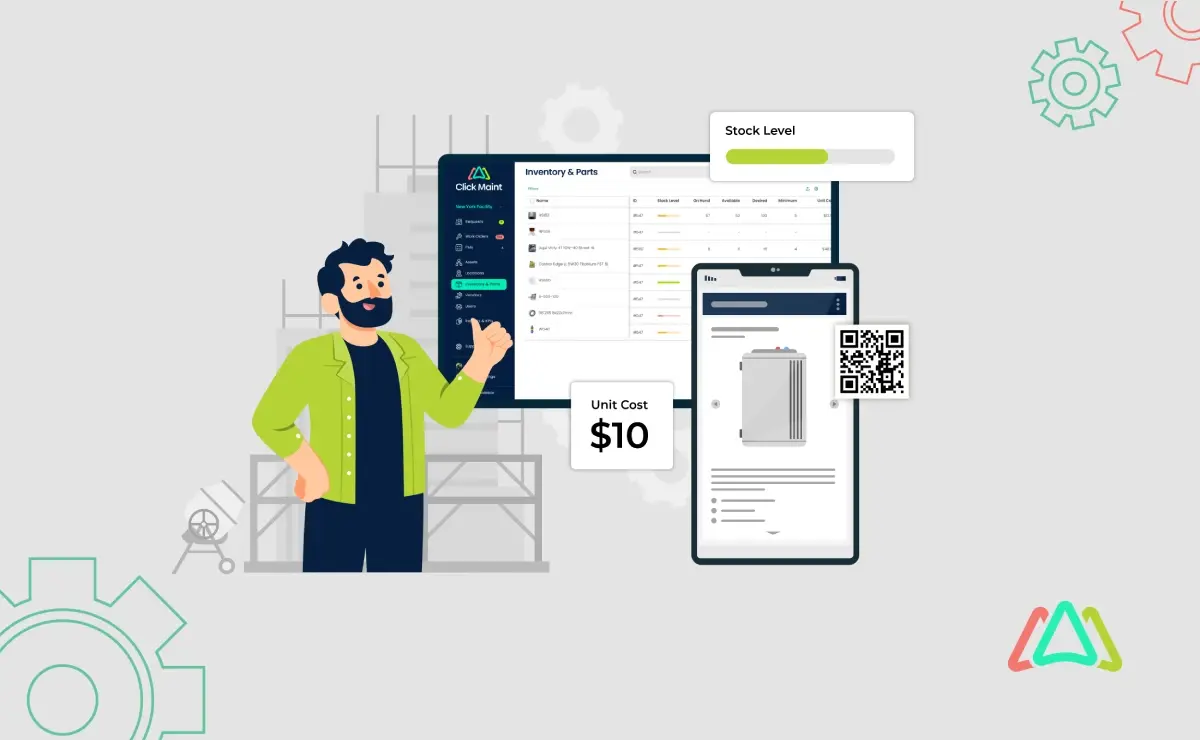
How Small Businesses Can Leverage CMMS for Inventory Management
Small enterprises often find themselves multitasking, striving to maintain operational efficiency while contending with limited resources. Among the numerous challenges they face, effective inventory management stands out as a key factor influencing their success. In this context, the adoption of Computerized Maintenance Management Systems (CMMS) emerges as a transformative solution, offering small businesses the tools they need to streamline their inventory processes and enhance overall productivity. Computerized Maintenance Management Systems (CMMS) software simplifies the management and maintenance of an organization's assets, equipment, and facilities. It empowers businesses to automate various maintenance tasks, including scheduling, tracking, and reporting.
Inventory management plays an important role in the daily operations of small businesses across diverse industries. Effectively managing inventory levels ensures that businesses can meet customer demand promptly, minimize stockouts, reduce carrying costs, and optimize cash flow. Additionally, efficient inventory management enhances accuracy in forecasting demand, enabling timely stock replenishment.
This article explores the functionalities and benefits of CMMS specifically tailored to the needs of small enterprises. It aims to equip small business owners and managers with actionable insights to optimize their inventory operations, improve efficiency, and drive business growth.
Benefits of Using CMMS for Small Businesses
The adoption of CMMS offers a multitude of benefits for small businesses striving to streamline their inventory management processes. These benefits include:
- Enhanced Efficiency: CMMS automates routine inventory tasks, such as stock tracking, replenishment, and reporting, reducing manual effort and minimizing errors.
- Cost Savings: By optimizing inventory levels and minimizing stockouts, CMMS helps small businesses reduce carrying costs and avoid overstocking, leading to significant cost savings.
- Improved Accuracy: Real-time inventory data provided by CMMS ensures greater accuracy in inventory tracking, enabling businesses to make informed decisions and prevent discrepancies.
- Resource Allocation: CMMS allows businesses to allocate resources more effectively by prioritizing maintenance tasks, optimizing inventory levels, and minimizing downtime.
- Enhanced Compliance: CMMS facilitates compliance with regulatory requirements and industry standards by providing documentation, audit trails, and maintenance records, ensuring adherence to best practices.
- Scalability: As small businesses grow and expand, CMMS can scale seamlessly to accommodate increased inventory volumes, additional locations, and evolving business needs.
Common Misconceptions about CMMS
Despite its numerous benefits, CMMS adoption among small businesses may be hindered by common misconceptions. Some of these misconceptions include:
- Complexity: Many small business owners perceive CMMS as overly complex and difficult to implement, assuming that it requires extensive technical expertise.
- Cost: There is a misconception that CMMS solutions are prohibitively expensive for small businesses, overlooking the potential return on investment and long-term cost savings.
- Limited Relevance: Some small business owners mistakenly believe that CMMS is only suitable for large enterprises with extensive asset portfolios, overlooking its scalability and adaptability to businesses of all sizes.
Challenges Faced by Small Businesses in Inventory Management
Despite its significance, small businesses often grapple with a myriad of challenges in managing their inventory effectively. Common challenges faced by maintenance leaders include:
- Limited Resources: Small businesses typically operate with constrained resources, including financial, human, and technological, making it challenging to implement sophisticated inventory management systems and processes.
- Inaccurate Forecasting: Inaccurate demand forecasting and inventory planning can result in stockouts, overstocking, and missed sales opportunities, leading to revenue loss and diminished customer satisfaction.
- Manual Processes: Many small businesses rely on manual inventory management processes, such as spreadsheets or pen-and-paper methods, which are prone to errors, time-consuming, and lack real-time visibility into inventory levels and movement.
- Lack of Scalability: Traditional inventory management methods may lack scalability, making it difficult for small businesses to accommodate growth, expand their product offerings, or adapt to changing market conditions effectively.
Traditional Methods vs. CMMS for Inventory Management
Traditionally, small businesses have relied on manual methods or basic inventory management software to track and manage their inventory. However, these traditional methods often lack the features and functionality required to address the complexities of modern inventory management. In contrast, CMMS offers a comprehensive solution tailored to the specific needs of small businesses, providing advanced CMMS features such as real-time inventory tracking, automated replenishment, predictive analytics, and integration with other business systems. By transitioning from traditional methods to CMMS, small businesses can streamline their inventory processes, improve accuracy, enhance efficiency, and gain a competitive edge in today's dynamic marketplace.
How CMMS Helps Small Businesses with Inventory Management
Centralized Inventory Tracking
CMMS provides small businesses with a centralized platform to track and manage their inventory efficiently. By consolidating inventory data into a single system, businesses gain real-time visibility into stock levels, locations, and movement across multiple warehouses or facilities. This centralized approach eliminates silos, reduces data duplication, and ensures consistency and accuracy in inventory tracking, enabling businesses to make informed decisions and optimize resource allocation.
Real-time Inventory Updates
One of the key advantages of CMMS is its ability to provide real-time inventory updates. Through integration with barcode scanners, RFID technology, or IoT devices, CMMS enables businesses to capture inventory transactions instantaneously, from receiving goods to shipping orders. This real-time visibility into inventory levels and movements empowers businesses to respond promptly to changes in demand, prevent stock outs or overstocking, and maintain optimal inventory levels at all times.
Automation of Inventory Tasks
CMMS automates various inventory management tasks, such as stock replenishment, reorder alerts, and inventory audits, reducing manual effort and minimizing human error. By automating routine tasks, businesses can improve efficiency, enhance accuracy, and free up valuable time for employees to focus on more strategic activities, such as forecasting demand or optimizing inventory strategies.
Streamlined Procurement Process
CMMS streamlines the procurement process by automating purchase orders, vendor management, and supplier communications. By implementing procurement workflows and centralizing vendor information, businesses can streamline the purchasing process, negotiate better terms with suppliers, and ensure timely delivery of goods. Additionally, CMMS provides insights into supplier performance and pricing trends, enabling businesses to make data-driven decisions and optimize procurement strategies for cost savings and efficiency gains.
Implementing CMMS for Small Business Inventory Management
Assessing Inventory Needs and Requirements
Before implementing a CMMS for inventory management, it is important for small businesses to assess their inventory needs and requirements thoroughly. This involves analyzing current inventory processes, identifying pain points and inefficiencies, and defining key objectives and goals for inventory management. By understanding their unique inventory challenges and requirements, businesses can tailor the implementation of CMMS to address specific pain points and achieve desired outcomes effectively.
Choosing the Right CMMS Solution for Your Business
Selecting the right CMMS software is paramount to successful inventory management implementation. Small businesses should evaluate CMMS providers based on factors such as features, scalability, ease of use, cost, and customer support. It's essential to choose a CMMS solution that aligns with the size, industry, and complexity of the business, ensuring it meets current needs while offering room for growth and scalability in the future.
Integration with Existing Systems
Integration of CMMS with existing systems, such as accounting software, ERP systems, or e-commerce platforms, is essential for seamless inventory management. Businesses should ensure that the chosen CMMS solution integrates smoothly with their existing systems to facilitate data exchange, eliminate data silos, and enable a unified view of inventory across the organization. Integration streamlines processes, enhances data accuracy, and improves overall efficiency in inventory management.
Training and Onboarding for Employees
Effective CMMS training and onboarding are critical for successful CMMS implementation and adoption. Businesses should invest in comprehensive training programs to educate employees on how to use the CMMS effectively for inventory management tasks. This includes hands-on training, user manuals, online resources, and ongoing support to ensure that employees feel confident and proficient in utilizing the CMMS to its fullest potential. By empowering employees with the necessary skills and knowledge, businesses can maximize the benefits of CMMS for inventory management and drive operational excellence.
Best Practices for Managing Inventory Using CMMS
Regular Inventory Audits and Reconciliations
Regular inventory audits and reconciliations are essential for maintaining accuracy and integrity in inventory data. By conducting periodic audits, businesses can identify discrepancies, detect errors, and reconcile inventory records with physical stock levels. This practice helps prevent stockouts, overstocking, and inventory shrinkage, ensuring optimal inventory management and financial accountability.
Setting up Alerts and Notifications for Low Stock Levels
CMMS allows businesses to set up alerts and notifications for low stock levels, ensuring timely replenishment of inventory. By configuring automated alerts based on predefined thresholds, businesses can monitor inventory levels, prevent stockouts, and avoid disruptions in production or customer service. This approach helps businesses maintain optimal inventory levels, minimize carrying costs, and meet customer demand effectively.
Utilizing Historical Data for Forecasting
Utilizing historical data for forecasting is a valuable practice enabled by CMMS. By analyzing past inventory trends, demand patterns, and seasonal fluctuations, businesses can make informed predictions about future inventory needs. This data-driven approach enables businesses to optimize inventory levels, improve demand forecasting accuracy, and reduce the risk of overstocking or stockouts, ultimately enhancing operational efficiency and profitability.
Establishing Backup and Recovery Procedures
Establishing backup and recovery procedures is essential for safeguarding inventory data and ensuring business continuity and CMMS data security. CMMS allows businesses to create backups of inventory data regularly and implement robust recovery procedures in the event of system failures, data loss, or security breaches. By addressing potential risks and implementing contingency plans, businesses can minimize downtime, protect sensitive inventory information, and maintain operational resilience in the face of unforeseen challenges.
Conclusion
CMMS transformed inventory management for small businesses, offering centralized tracking,
real-time updates, automation, and streamlined procurement. These benefits translate to enhanced efficiency, accuracy, cost savings, and scalability. Small businesses are urged to embrace CMMS to optimize inventory control, boost productivity, and gain a competitive edge in today's market, integrating CMMS empowers small businesses to unlock their full potential, driving growth and success through efficient inventory management.
TABLE OF CONTENTS
Keep Reading
Ever find yourself checking into a luxury hotel and expecting a relaxing stay, only to find a ...
11 Apr 2025
Organizations are witnessing swift changes in the business environment and confronting a ...
8 Apr 2025
Last month, news outlets and the entire internet was abuzz with the return of NASA astronauts ...
3 Apr 2025
What comes first - CMMS or predictive maintenance? If your answer is either, it is correct. ...
28 Mar 2025
Artificial intelligence (AI) talk has become commonplace. Today, engaging in business-focused ...
27 Mar 2025
Imagine a world where machines predict, diagnose, and fix their issues before they fail. This ...
25 Mar 2025
A facility maintenance plan is at the core of a facility’s operations. This organized ...
21 Mar 2025
Think of managing your maintenance operations like managing a championship sports team. Just ...
21 Mar 2025
The maintenance sector is battling a severe talent shortage that threatens to undermine ...
7 Mar 2025
Manufacturing maintenance is the backbone of industrial efficiency, ensuring machines run ...
5 Mar 2025
No one likes playing a guessing game when equipment breaks down. Yet, maintenance teams often ...
4 Mar 2025
The size of the preventive maintenance software market is discussed in millions of dollars, ...
4 Mar 2025
The organizational structure and corporate hierarchy vary from company to company. Large ...
28 Feb 2025
Maintenance procedures are essential for ensuring the longevity and reliability of machinery ...
21 Feb 2025
Sustainability is no longer just a buzzword; it's a critical component of corporate social ...
20 Feb 2025
A Computerized Maintenance Management System (CMMS) relies on accurate, well-organized data ...
18 Feb 2025
In an era where technology drives operational efficiency, Computerized Maintenance Management ...
14 Feb 2025
A Computerized Maintenance Management System (CMMS) is a key component of modern maintenance ...
13 Feb 2025
Introduction Maintenance management is the foundation of maintenance operations in industries ...
11 Feb 2025
Introduction A Computerized Maintenance Management System (CMMS) is software designed to help ...
7 Feb 2025