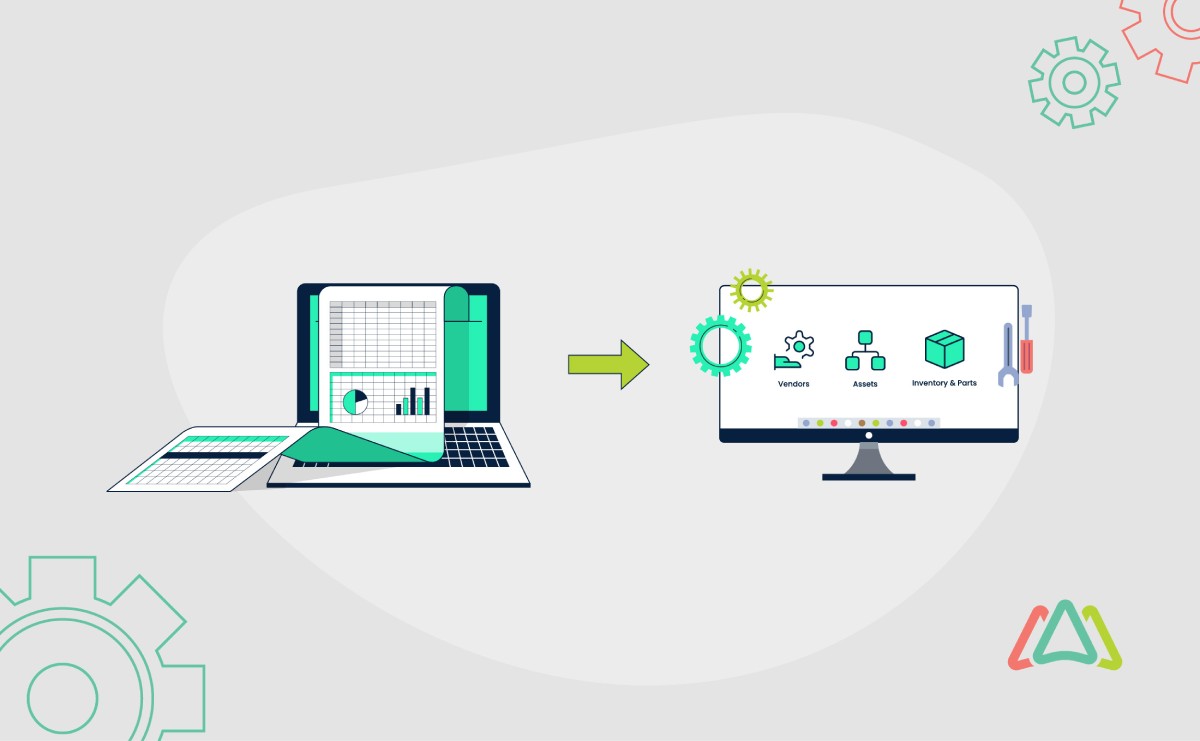
SMB's Handbook: Transitioning from Spreadsheets to CMMS
For many small and medium-sized businesses (SMBs), spreadsheets and pen-and-paper are the standard approaches for managing maintenance tasks. These manual methods are being used for tracking everything from equipment schedules to logging service histories and are the backbone of many SMBs’ maintenance operations.
However, the reliance on spreadsheets and pen-and-paper comes with a set of challenges that hinder the seamless functioning of maintenance tasks. The manual data entry is not only time-consuming but also prone to errors, leading to inconsistencies in information. Real-time updates are a distant dream, causing delays in decision-making, and the difficulty in tracking asset life cycles can result in unforeseen breakdowns. The time it takes to input data manually is another major limitation that costs SMBs a lot. The limitations of these traditional methods are becoming increasingly apparent as businesses strive for efficiency and competitiveness.
Limitations of Spreadsheets and Pen-and-Paper
The traditional reliance on spreadsheets and pen-and-paper for maintenance tasks has always had its limitations. The following are five limitations experienced by most businesses using manual methods for tracking maintenance activities.
1. Inefficiency and Time-Consuming Data Entry
One of the primary drawbacks of relying on spreadsheets and pen-and-paper is the inherent inefficiency and time-consuming nature of manual data entry. Imagine technicians spending valuable hours manually inputting data, increasing the likelihood of errors and diverting their attention from more critical tasks. This inefficiency poses a significant barrier to the optimal functioning of maintenance operations.
2. Lack of Real-time Updates and Synchronization
Spreadsheets and pen-and-paper methods often fail to provide real-time updates and synchronization capabilities. With spreadsheets, there are some workarounds, but with paper and pen, “synchronization” and “real-time” are excluded from the conversation. Changes made in one document don’t immediately reflect in others, leading to delays in information dissemination. This lack of real-time synchronization inhibits swift decision-making, a critical aspect in the fast-paced world of maintenance where timely responses can make a significant impact.
3. Proneness to Errors and Data Inconsistencies
The human element in manual data entry introduces a considerable risk of errors and data inconsistencies. Whether it's a mistyped figure or an overlooked entry, the margin for inaccuracies is substantial. These discrepancies can have cascading effects, leading to misguided maintenance decisions, potentially causing equipment failures or unnecessary downtime.
4. Difficulty in Tracking and Managing Asset Lifecycle
Maintaining a comprehensive record of equipment life cycles is a critical aspect of effective maintenance management. Spreadsheets and pen-and-paper methods fall short with providing a systematic and easily accessible means of tracking assets from acquisition to retirement. This difficulty in managing the asset lifecycle can result in suboptimal maintenance planning and increased operational costs.
5. Limited Collaboration and Communication Capabilities
Collaboration and communication are important in any business operation, and the limitations of spreadsheets and pen-and-paper shine in this regard. These manual methods lack the collaborative features necessary for team members to efficiently share information, discuss maintenance issues, or collectively resolve challenges. This is especially true for maintenance professionals entering the job market. Using the internet, software, and mobile apps is all they know.
The Case for CMMS Adoption
The adoption of a Computerized Maintenance Management System (CMMS) has many advantages over manual methods. In the past, CMMS software was seen as an option for larger enterprises and not a viable option for SMBs. CMMSs were expensive, complex, and took months (in some cases years) to implement. This is not the case today. According to G2 Crowd (a buyer’s guide for B2B software), there are over 300 CMMS software products available. Small and Medium-sized Businesses (SMBs). Many of these products are web-based, can be implemented within 30-60 days, and have competitive user-based pricing. Investing in CMMS software is not just a technological upgrade but a strategic investment with far-reaching implications. For many SMBs that are using manual methods to track maintenance activities, it is realistic to see a return on investment with a CMMS within the first year.
1. Improved Efficiency and Workforce Productivity
One of the primary drivers for SMBs to adopt CMMS is the significant improvement in operational efficiency. The system streamlines workflow processes, automates repetitive tasks, and minimizes manual interventions, allowing maintenance teams to focus on value-added activities. This boost in efficiency translates directly into improved workforce productivity, ensuring that every hour invested in maintenance tasks yields optimal results.
2. Cost-effectiveness and Resource Optimization
Cost-effectiveness lies at the core of the benefits derived from CMMS adoption. SMBs often grapple with tight budgets and limited resources. CMMS streamlines maintenance processes, reducing the reliance on manual labor and minimizing the risk of unnecessary expenditures. The system's ability to optimize resource allocation ensures that every dollar invested in maintenance activities yields maximum value, contributing directly to the overall financial health of the SMB. The CMMS market is very competitive, with hundreds of solutions to choose from. With that, many CMMS providers offer their products at prices suitable for SMBs.
Check out our Top 10 CMMS Software List!
3. Improved Maintenance Planning and Scheduling
CMMS empowers SMBs with a level of control and foresight that is unparalleled with traditional maintenance methods. The system facilitates improved maintenance planning and scheduling, allowing organizations to allocate resources efficiently, minimize downtime, and extend the lifespan of equipment. By strategically planning maintenance activities, SMBs can proactively address issues before they escalate, contributing to a more streamlined and effective operation.
4. Enhanced Preventive Maintenance Strategies
Preventive maintenance is a cornerstone of effective asset management, and CMMS elevates this practice to new heights. SMBs can implement preventive maintenance strategies seamlessly through the automated features of CMMS. The system enables the creation of comprehensive maintenance schedules, automates routine inspections, and generates alerts for upcoming tasks. This proactive approach not only reduces the likelihood of unplanned downtime but also contributes to increased equipment reliability.
5. Increased Equipment Reliability and Uptime
CMMS is a catalyst for increased equipment reliability and uptime. By adopting proactive maintenance strategies, SMBs can address potential issues before they lead to equipment failures. Real-time tracking, automated alerts, and swift responses to maintenance needs contribute to a significant reduction in downtime. Increased equipment reliability ensures that assets operate at peak efficiency, contributing directly to the overall productivity of the SMB.
6. Reduction in Downtime
CMMS enables SMBs to transition from reactive to proactive maintenance strategies, minimizing unplanned downtime. By implementing preventive maintenance schedules and predictive maintenance techniques, potential issues are identified and addressed before they escalate, leading to a reduction in downtime and associated operational costs. This proactive approach results in a more reliable and resilient operation.
7. Optimal Inventory Management and Cost Savings
Precision is key when managing inventory and spare parts, and a well-implemented CMMS does just that, ensuring that SMBs maintain optimal stock levels. Automated alerts and reordering features prevent overstocking or stockouts, leading to cost savings through efficient resource utilization. The ability to track and manage inventory more effectively translates directly into reduced procurement costs and improved financial sustainability. A 2019 survey by Plant Engineering found that companies using CMMS software saw a 20-25% reduction in inventory and parts costs. (Plant Engineering, "CMMS/EAM Best Practices Survey," 2019)
8. Extended Asset Lifespan and Reduced Capital Expenditure
CMMS facilitates comprehensive asset lifecycle management, allowing SMBs to maximize the lifespan of their equipment. By proactively addressing maintenance needs, SMBs can extend the lifespan of assets, reducing the need for frequent replacements. This leads to substantial savings in capital expenditure, as investments in new equipment are deferred, and existing assets are utilized to their full potential. A 2017 study by the ARC Advisory Group found that organizations using CMMS software reported an average 10-15% increase in asset life expectancy. (Source: ARC Advisory Group, "Maintenance Management Systems for Process Industries," 2017)
9. Compliance with Industry Regulations
In industries subject to stringent regulations, compliance is not just a legal requirement but a critical aspect of business continuity. CMMS provides a robust framework for ensuring compliance with industry regulations. The system automates documentation processes, maintains a centralized repository of compliance records, and generates reports for audits. This meticulous approach not only mitigates the risk of regulatory penalties but also enhances the overall reputation and trustworthiness of the SMB within its industry. The mitigation of regulatory risks through adherence to standards and regulations contributes significantly to the overall ROI.
Steps for Seamless CMMS Adoption
The adoption of CMMS software can be a significant undertaking for Small and Medium-sized Businesses (SMBs). To avoid pitfalls and maximize the benefits, the following are some best practices and guidelines to follow.
1. Conduct a Thorough Needs Assessment
Before diving into the world of CMMS, SMBs must conduct a thorough needs assessment to understand their unique requirements. This involves evaluating current maintenance practices, identifying pain points, and defining specific goals for CMMS implementation. The assessment should include input from maintenance teams, IT departments, and other relevant stakeholders to ensure a comprehensive understanding of the organization's needs and challenges.
2. Identify Key Stakeholders and Obtaining Their Support
The success of CMMS adoption hinges on obtaining support from key stakeholders within the organization. Identify individuals and departments that will be directly impacted by the CMMS, such as maintenance teams, IT personnel, and upper management. Communicate the benefits of CMMS clearly, addressing any concerns or misconceptions. Building a coalition of support ensures a smoother transition and increased engagement throughout the implementation process.
3. Select the Right CMMS Solution Based on Requirements
Choosing the right CMMS solution is a critical step in the adoption process. SMBs should evaluate available options based on their specific requirements, budget constraints, and scalability needs. Consider factors such as the system's user-friendliness, integration capabilities with existing software, and the level of technical support provided by the vendor. A well-informed decision during this stage sets the foundation for a successful CMMS implementation.
4. Plan and Execute a Phased Implementation
This may not be necessary for small teams and departments but for larger operations, a phased implementation approach helps mitigate risks and allows SMBs to adapt gradually to the new system. Develop a detailed implementation plan that outlines the sequence of deployment, considering factors such as departmental priorities, training schedules, and potential workflow disruptions. By breaking down the implementation into manageable phases, SMBs can identify and address challenges early in the process, ensuring a smoother transition.
5. Provide Comprehensive Training for Users
User training is a cornerstone of successful CMMS adoption. Ensure that all users, from maintenance technicians to administrators, receive comprehensive training on the functionalities of the CMMS. In the past, most CMMS software training involved the trainer coming to the customer’s location and spending a couple of days with the team. Today, with web-conferencing apps like Zoom, Microsoft Teams, and Google Meets, training has become easier, better, and less costly. Almost all Software as a Service (SaaS) CMMS include some level of ongoing support in their subscription plans. Investing in user education ensures that the full potential of the CMMS is realized and that all team members are equipped to leverage its capabilities. For SMBs, what’s great is that training and support are more accessible and less costly than they once were.
Overcoming Adoption Challenges
1. Resistance to Change and Employee Training
Challenge:
One of the primary hurdles in CMMS adoption is the resistance to change from employees accustomed to traditional methods. This resistance often stems from fear of the unknown, lack of understanding of the new system, or concerns about job security.
Solution:
Addressing resistance requires a two-pronged approach. Firstly, provide comprehensive training to employees on the functionalities and benefits of the CMMS. Secondly, communicate the positive impact of CMMS on daily workflows, emphasizing increased efficiency, reduced workload, and improved job satisfaction.
2. Selecting the Right CMMS for SMB Needs
Challenge:
The market is flooded with CMMS options, and selecting the right one tailored to SMB needs can be overwhelming. A mismatch between the chosen CMMS and the specific requirements of the organization can lead to inefficiencies and suboptimal results.
Solution:
Begin by conducting a thorough needs assessment to identify specific requirements. Consider factors such as the size of the organization, industry-specific needs, and scalability requirements. Engage in a detailed evaluation of CMMS options, seeking demos, and obtaining user feedback. Choose a solution that aligns with SMB goals, ensuring maximum utility and ROI.
3. Ensuring Buy-in from Key Stakeholders
Challenge:
Without buy-in from key stakeholders, CMMS adoption may face resistance and limited support, hindering its effectiveness.
Solution:
Engage stakeholders early in the process, presenting a clear case for how CMMS aligns with organizational goals. Address concerns, gather input, and demonstrate the tangible benefits through pilot programs or case studies. Establishing a sense of ownership and involvement ensures that key stakeholders champion the CMMS adoption, paving the way for a more successful implementation.
The ROI of CMMS adoption for SMBs is multifaceted, encompassing improvements in efficiency, cost savings, asset management, and risk mitigation. While the initial investment in CMMS or the adoption challenges may seem substantial, the long-term benefits position it as a strategic and lucrative decision for SMBs aiming for sustained growth and operational excellence. For SMBs considering the moving from manual methods like spreadsheets and paper and pen, there are so many opportunities to cut costs and improve efficiencies with CMMS software. The key to making this a reality is doing a bit of research, selecting the best provider, and having a good game plan for implementation.
TABLE OF CONTENTS
Keep Reading
Ever find yourself checking into a luxury hotel and expecting a relaxing stay, only to find a ...
11 Apr 2025
Organizations are witnessing swift changes in the business environment and confronting a ...
8 Apr 2025
Last month, news outlets and the entire internet was abuzz with the return of NASA astronauts ...
3 Apr 2025
What comes first - CMMS or predictive maintenance? If your answer is either, it is correct. ...
28 Mar 2025
Artificial intelligence (AI) talk has become commonplace. Today, engaging in business-focused ...
27 Mar 2025
Imagine a world where machines predict, diagnose, and fix their issues before they fail. This ...
25 Mar 2025
A facility maintenance plan is at the core of a facility’s operations. This organized ...
21 Mar 2025
Think of managing your maintenance operations like managing a championship sports team. Just ...
21 Mar 2025
The maintenance sector is battling a severe talent shortage that threatens to undermine ...
7 Mar 2025
Manufacturing maintenance is the backbone of industrial efficiency, ensuring machines run ...
5 Mar 2025
No one likes playing a guessing game when equipment breaks down. Yet, maintenance teams often ...
4 Mar 2025
The size of the preventive maintenance software market is discussed in millions of dollars, ...
4 Mar 2025
The organizational structure and corporate hierarchy vary from company to company. Large ...
28 Feb 2025
Maintenance procedures are essential for ensuring the longevity and reliability of machinery ...
21 Feb 2025
Sustainability is no longer just a buzzword; it's a critical component of corporate social ...
20 Feb 2025
A Computerized Maintenance Management System (CMMS) relies on accurate, well-organized data ...
18 Feb 2025
In an era where technology drives operational efficiency, Computerized Maintenance Management ...
14 Feb 2025
A Computerized Maintenance Management System (CMMS) is a key component of modern maintenance ...
13 Feb 2025
Introduction Maintenance management is the foundation of maintenance operations in industries ...
11 Feb 2025
Introduction A Computerized Maintenance Management System (CMMS) is software designed to help ...
7 Feb 2025