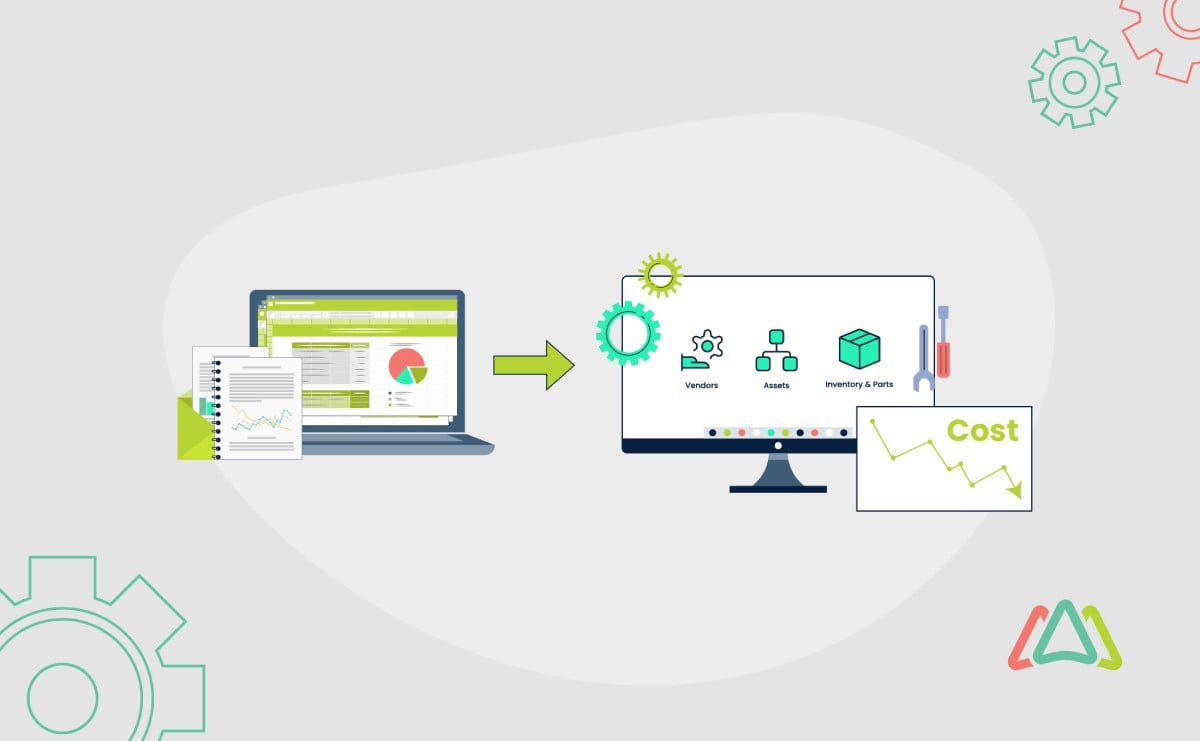
Balancing the Books: How CMMS Adoption Translates to Tangible Cost Savings for SMBs
Maintenance practices have a direct and material impact on the financial health of small and medium-sized businesses (SMBs). When equipment breakdowns or unexpected maintenance issues arise, they disrupt operations, leading to downtime and pressure on SMBs. Traditional reactive approaches, often characterized by unpredictable breakdowns and emergency repairs, can lead to escalated costs. On the flip side, proactive and strategic maintenance can result in significant cost savings by preventing unplanned downtime, reducing repair expenses, and extending the lifespan of critical assets. The financial implications of maintenance practices extend beyond immediate costs, influencing the overall profitability and sustainability of SMBs.
SMBs often rely on manual methods for tracking and managing maintenance activities. Spreadsheets and pen-and-paper systems for many SMBs are the go-to tools for recording maintenance schedules, tracking work orders, and managing inventory. While these manual methods are easy and inexpensive to implement, they come with inherent inefficiencies that can hinder operational and financial success.
The Financial Drawbacks of Traditional Maintenance Methods
SMBs relying on spreadsheets and pen-and-paper systems to track and manage maintenance activities often find themselves facing various financial drawbacks.
1. Inherent Inefficiencies in Manual Tracking
1.1 Data Inaccuracies and Human Errors
The susceptibility to data inaccuracies and human errors in manual maintenance tracking is a persistent challenge. Handwritten notes or spreadsheet entries can easily be misinterpreted or contain mistakes that go unnoticed until a critical issue arises. These inaccuracies not only compromise the reliability of maintenance records but can also lead to misguided decisions, resulting in unnecessary expenses.
1. 2 Time-Consuming Data Entry and Retrieval
The manual entry of data into spreadsheets or paper-based systems is a time-consuming process. Maintenance personnel spend valuable hours recording information and retrieving relevant details when needed. This not only slows down the overall maintenance workflow but also contributes to increased labor costs. In an SMB where time and resources are precious commodities, inefficiencies like these can have a direct impact on the bottom line.
2. Reactive Nature Leading to Increased Downtime
2.1 Unplanned Maintenance Costs
One of the primary financial drawbacks of relying on spreadsheets and pen-and-paper tracking is the reactive nature of maintenance. When equipment breaks down unexpectedly, the ensuing repairs often come with higher costs. Urgent callouts, expedited shipping for replacement parts, and overtime wages for maintenance personnel can significantly inflate the overall cost of unplanned maintenance. This reactive approach can strain an SMB's budget, impacting its ability to allocate funds to growth initiatives or other priorities.
2.2 Impact on Productivity and Revenue
Increased downtime due to unplanned maintenance has a cascading effect on productivity and revenue. Every hour of equipment downtime represents potential revenue loss for an SMB. Beyond the immediate repair costs, the longer-term impact on production schedules, customer satisfaction, and overall business performance can be substantial. The financial consequences of reduced productivity can be especially burdensome for SMBs with tight profit margins.
3. Limited Insights and Forecasting Capabilities
3.1 Inability to Analyze Historical Data
Manual tracking systems often lack the capability to analyze historical maintenance data effectively. Without the ability to review past performance, identify recurring issues, or track trends over time, SMBs miss out on valuable insights. This limitation hinders the development of proactive maintenance strategies and keeps the business stuck in a reactive cycle.
3.2 Challenges in Predicting Maintenance Needs
Forecasting maintenance needs becomes a challenging endeavor when relying on spreadsheets and pen-and-paper systems. The absence of predictive analytics tools means that SMBs are left to grapple with unexpected breakdowns, making it difficult to plan and allocate resources efficiently. This uncertainty can lead to higher overall maintenance costs and a lack of control over the maintenance budget.
The Financial Advantages of Adopting CMMS Software
For SMBs currently grappling with the inefficiencies of spreadsheets and pen-and-paper methods for maintenance tracking, the adoption of a CMMS offers the following financial advantages:
1. Cost Savings through Efficient Work Order Management
1.1 Streamlined Request Generation and Processing
CMMS brings a higher level of efficiency to work order management. Through a centralized platform, maintenance requests can be generated and processed seamlessly. Automated workflows eliminate the need for manual data entry and reduce the likelihood of errors. This streamlined process not only saves time but also ensures that maintenance tasks are initiated promptly, preventing potential equipment failures or disruptions.
1.2 Minimized Downtime and Associated Costs
Efficient work order management directly translates into minimized downtime. With CMMS, maintenance tasks are scheduled and executed proactively, reducing the likelihood of unexpected breakdowns. This proactive approach not only safeguards against unplanned downtime but also mitigates the associated costs such as urgent repairs, expedited shipping of replacement parts, and overtime wages. The result is a significant reduction in overall maintenance expenses and a more predictable budget for SMBs.
According to a study by Jones Lang LaSalle (JLL), effective CMMS implementation can lead to a 15-20% reduction in downtime. (Source: JLL Research, "CMMS Implementation: A Case Study," 2018)
2. Enhanced Labor Productivity
2.1 Automated Task Assignment and Scheduling
CMMS automates the assignment of maintenance tasks based on predefined schedules, priority levels, and skill sets. This automation ensures that the right personnel are assigned to the right tasks at the right time. The result is enhanced labor productivity, as maintenance teams can focus on preventive and proactive measures rather than reacting to sudden issues. This shift from a reactive to a proactive stance contributes to long-term cost savings and improved operational efficiency.
On average, companies using CMMS systems experience a 20-30% reduction in time to complete work orders. (Source: Aberdeen Group, "Enterprise Asset Management: A Buyer’s Guide," 2016)
2.2 Reduction in Overtime Expenses
The ability to schedule and prioritize maintenance tasks effectively through CMMS reduces the need for overtime work. With tasks distributed efficiently and maintenance needs addressed before they escalate, SMBs can avoid the costs associated with overtime wages. This not only contributes to immediate savings but also fosters a healthier work-life balance for maintenance personnel.
3. Optimal Inventory Management
3.1 Preventing Overstock and Stockouts
CMMS empowers SMBs to optimize their inventory management by providing real-time insights into the availability of spare parts and consumables. This prevents overstocking, which ties up capital and leads to unnecessary carrying costs. Simultaneously, CMMS ensures that critical parts are readily available, preventing stockouts and subsequent rush orders that bring higher costs.
3.2 Lowering Carrying Costs through Inventory Optimization
By maintaining an optimal level of inventory, SMBs can significantly lower carrying costs. CMMS software enables businesses to track usage patterns, forecast future needs, and implement just-in-time inventory practices. This strategic approach to inventory management ensures that capital is not tied up in excess stock, freeing up resources for other important aspects of the business.
Tangible Return on Investment (ROI)
1. Initial Investment vs. Long-term Savings
1.1 Comparative Analysis of CMMS and Traditional Methods
Traditional methods, relying on spreadsheets and pen-and-paper, incur hidden costs in terms of time, errors, and the consequences of reactive maintenance. A comparative analysis between the upfront costs of CMMS implementation and the long-term expenses associated with manual methods unveils a stark contrast.
Upfront Costs of CMMS:
- Software acquisition and implementation
- Employee training and onboarding
Long-term Costs of Traditional Methods:
- Labor costs for manual data entry and retrieval
- Emergency repairs and associated downtime
- Overtime expenses due to reactive maintenance
- Inefficiencies leading to potential revenue loss
1.2 Demonstrating a Clear and Measurable ROI
The ROI of CMMS adoption becomes evident as SMBs experience streamlined processes, reduced downtime, and improved asset longevity. The measurable benefits include:
- Time Savings: Automation of maintenance workflows leads to substantial time savings compared to manual data entry and retrieval.
- Reduced Downtime: Proactive maintenance scheduling minimizes downtime, resulting in direct cost savings and increased productivity.
- Lower Labor Costs: Efficiency gains and reduced overtime expenses contribute to lower overall labor costs.
- Preventive Cost Reduction: By preventing emergency repairs and addressing issues proactively, CMMS helps avoid costly breakdowns.
2. Long-term Financial Benefits
2.1 Sustainable Cost Reduction Over the Years
The financial benefits of adopting a CMMS extend beyond the initial implementation phase. SMBs can realize sustainable cost reduction over the years through:
- Predictable Budgeting: CMMS enables SMBs to forecast maintenance needs, allowing for better budget planning and allocation of resources.
- Extended Asset Lifespan: Proactive and preventive maintenance facilitated by CMMS extends the lifespan of critical assets, reducing the frequency of replacements and associated costs. A report by the ARC Advisory Group found that companies with effective preventive maintenance strategies, often facilitated by CMMS, reported an average of 20% extension in the lifespan of their critical assets. (ARC Advisory Group, "Asset Performance Management: Global Market Research Study," 2019)
- Continuous Improvement: CMMS provides insights into performance metrics, allowing SMBs to identify and address inefficiencies continuously.
2.2 Increased Profitability through Optimized Operations
Optimized maintenance operations contribute directly to increased profitability for SMBs:
- Enhanced Productivity: Reduced downtime and efficient task management enhance overall operational productivity.
- Improved Customer Satisfaction: Reliable and consistent services, facilitated by proactive maintenance, lead to increased customer satisfaction and retention.
- Competitive Advantage: SMBs adopting CMMS software position themselves competitively by offering streamlined and reliable services, attracting more business opportunities. In addition, the savings due to lowering overall maintenance costs as a result of implementing a CMMS can be put toward growth initiatives like marketing, research and development, or other business functions.
The International Journal of Operations & Production Management suggests that CMMS implementation can result in a 10-15% reduction in overall maintenance costs. (International Journal of Operations & Production Management, "Effect of CMMS Implementation on Maintenance Management Performance," 2014)
Manual maintenance tracking systems present inherent limitations. They are prone to data inaccuracies, delays, and inefficiencies. As SMBs aim for growth and sustainability, these challenges become bottlenecks to operational success. The financial advantage of transitioning from spreadsheets and pen-and-paper to CMMS lies in the transformative impact on efficiency and cost-effectiveness. CMMS automates and centralizes maintenance processes, eliminating the pitfalls of manual systems and providing real-time insights for informed decision-making.
TABLE OF CONTENTS
Keep Reading
Ever find yourself checking into a luxury hotel and expecting a relaxing stay, only to find a ...
11 Apr 2025
Organizations are witnessing swift changes in the business environment and confronting a ...
8 Apr 2025
Last month, news outlets and the entire internet was abuzz with the return of NASA astronauts ...
3 Apr 2025
What comes first - CMMS or predictive maintenance? If your answer is either, it is correct. ...
28 Mar 2025
Artificial intelligence (AI) talk has become commonplace. Today, engaging in business-focused ...
27 Mar 2025
Imagine a world where machines predict, diagnose, and fix their issues before they fail. This ...
25 Mar 2025
A facility maintenance plan is at the core of a facility’s operations. This organized ...
21 Mar 2025
Think of managing your maintenance operations like managing a championship sports team. Just ...
21 Mar 2025
The maintenance sector is battling a severe talent shortage that threatens to undermine ...
7 Mar 2025
Manufacturing maintenance is the backbone of industrial efficiency, ensuring machines run ...
5 Mar 2025
No one likes playing a guessing game when equipment breaks down. Yet, maintenance teams often ...
4 Mar 2025
The size of the preventive maintenance software market is discussed in millions of dollars, ...
4 Mar 2025
The organizational structure and corporate hierarchy vary from company to company. Large ...
28 Feb 2025
Maintenance procedures are essential for ensuring the longevity and reliability of machinery ...
21 Feb 2025
Sustainability is no longer just a buzzword; it's a critical component of corporate social ...
20 Feb 2025
A Computerized Maintenance Management System (CMMS) relies on accurate, well-organized data ...
18 Feb 2025
In an era where technology drives operational efficiency, Computerized Maintenance Management ...
14 Feb 2025
A Computerized Maintenance Management System (CMMS) is a key component of modern maintenance ...
13 Feb 2025
Introduction Maintenance management is the foundation of maintenance operations in industries ...
11 Feb 2025
Introduction A Computerized Maintenance Management System (CMMS) is software designed to help ...
7 Feb 2025