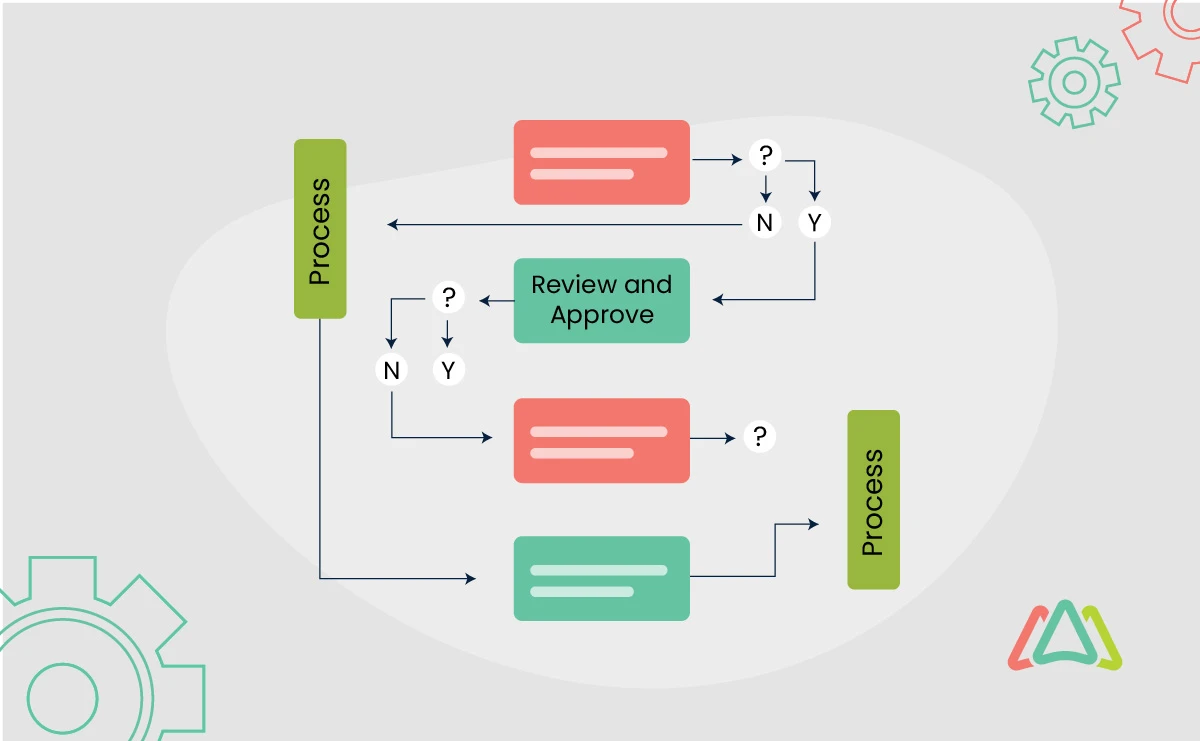
Standard Operating Procedures: Maximizing Maintenance Efficiency and Reliability
Maintenance tasks, whether they involve routine inspections, preventive maintenance, or corrective actions, must be executed with precision and adherence to safety protocols. SOPs provide maintenance teams with clear instructions on how to carry out these tasks, ensuring consistency in approach and minimizing the risk of equipment failure or downtime.
The importance of SOPs cannot be overstated, particularly in industries where precision and consistency are critical. They provide a standardized approach to performing tasks, leaving no room for ambiguity or error. By clearly defining the steps to be taken, SOPs help minimize variation in performance, reducing the likelihood of mistakes and enhancing overall operational efficiency.
Moreover, SOPs serve as a reference point for training new maintenance personnel, enabling them to quickly get up to speed with the organization's maintenance protocols. They also facilitate effective communication and collaboration among team members, as everyone follows the same standardized procedures.
What are Standard Operating Procedures (SOPs)?
Standard Operating Procedures (SOPs) are the documented guidelines that outline the specific steps to be followed when performing routine tasks or processes within an organization. In the context of maintenance management, SOPs provide a standardized approach to conducting maintenance activities, ensuring consistency, efficiency, and safety
SOPs are detailed, step-by-step instructions that define how tasks should be executed, including the sequence of actions, required resources, safety precautions, and quality standards. They cover a wide range of activities, from routine maintenance inspections to complex repair procedures, and are typically documented in written or electronic formats for easy reference.
The scope of SOPs in maintenance management may vary depending on the organization's industry, size, and specific requirements. However, common areas covered by maintenance SOPs include:
- Preventive Maintenance: Procedures for conducting scheduled inspections, lubrication, calibration, and other preventive maintenance tasks to keep equipment and facilities in optimal condition.
- Corrective Maintenance: Guidelines for addressing equipment breakdowns or malfunctions, including troubleshooting steps, repair techniques, and spare parts management.
- Safety Protocols: Instructions for ensuring the safety of maintenance personnel and equipment, such as wearing personal protective equipment (PPE), following lockout/tagout procedures, and handling hazardous materials.
- Quality Assurance: Procedures for maintaining quality standards during maintenance activities, including verification and validation processes, documentation requirements, and compliance with regulatory standards.
Challenges Without Standardization
Without standardized maintenance procedures and practices, organizations may face several challenges, including:
- Inconsistency in Maintenance Practices: Variations in how maintenance tasks are performed can lead to inconsistencies in results, reduced reliability, and increased risk of equipment failure.
- Lack of Efficiency: Without standardized procedures and workflows, maintenance activities may take longer to complete, leading to increased downtime, higher costs, and decreased productivity.
- Safety Risks: Inadequate or inconsistent safety protocols can pose risks to maintenance personnel, equipment, and the surrounding environment, potentially resulting in accidents or injuries.
- Difficulty in Training and Onboarding: Without standardized procedures, training new maintenance personnel becomes challenging, as there may be no clear guidelines or reference materials to follow, leading to longer onboarding times and increased training costs.
Objectives of SOPs in Maintenance Management
The objectives of SOPs in maintenance management are multifaceted and align with the broader goals of optimizing equipment reliability, minimizing downtime, and maximizing operational efficiency. Some key objectives include:
- Standardization: To establish consistent and uniform procedures for performing maintenance tasks, regardless of the individual or team carrying them out, ensuring reliability and quality.
- Efficiency: To streamline maintenance processes, reduce unnecessary downtime, and maximize resource utilization by providing clear, structured guidelines for task execution.
- Safety: To promote a safe working environment by defining safety protocols, hazard mitigation measures, and emergency procedures to protect maintenance personnel, equipment, and the surrounding environment.
- Compliance: To ensure compliance with regulatory requirements, industry standards, and organizational policies governing maintenance activities, reducing the risk of non-compliance and associated penalties.
- Training and Knowledge Transfer: To serve as a reference tool for training new maintenance personnel, facilitating knowledge transfer, skill development, and competency enhancement within the maintenance team.
Overall, SOPs play a critical role in driving operational excellence, mitigating risks, and enhancing the overall effectiveness of maintenance management strategies.
Relationship between SOPs and Best Practices
SOPs and best practices are closely intertwined, with SOPs often serving as a means for implementing and institutionalizing best practices within an organization. While SOPs provide specific instructions and guidelines for performing tasks, best practices represent the most effective and efficient methods or approaches for achieving desired outcomes.
The relationship between SOPs and best practices can be summarized as follows:
- Integration: SOPs incorporate best practices into their procedural guidelines, ensuring that tasks are performed using the most effective methods identified through industry research, benchmarking, and experience.
- Continuous Improvement: SOPs are dynamic and evolve over time based on feedback, lessons learned, and changes in technology or regulations. As new best practices emerge, SOPs should be updated accordingly to reflect the latest standards and methodologies.
- Standardization of Best Practices: SOPs standardize the application of best practices across the organization, ensuring consistency and uniformity in performance regardless of personnel changes or location variations.
- Benchmarking: SOPs provide a basis for benchmarking performance against industry standards and competitors, allowing organizations to identify areas for improvement and adopt new best practices to stay competitive.
In essence, SOPs serve as the mechanism for operationalizing best practices within an organization, guiding employees on how to implement these practices effectively to achieve desired outcomes and maintain high standards of performance.
How to Create Effective SOPs for Maintenance?
Creating effective Standard Operating Procedures (SOPs) for maintenance is necessary for ensuring consistency, reliability, and safety in maintenance operations.
1. Identifying Critical Maintenance Tasks
- Asset Prioritization: Begin by identifying critical assets within your organization based on factors such as impact on production, safety considerations, and regulatory requirements.
- Failure Modes Analysis: Conduct a thorough failure modes effects and criticality analysis (FMECA) of each critical asset to identify potential failure modes, their causes, and the consequences of failure. This analysis helps prioritize maintenance tasks based on risk and criticality.
- Maintenance History Review: Review historical maintenance records to identify recurring issues, common maintenance tasks, and best practices for addressing them.
- Input from Maintenance Personnel: Consult with maintenance personnel who have firsthand experience with equipment and facilities to gather insights into routine maintenance tasks, challenges encountered, and suggestions for improvement.
2. Involving Stakeholders in SOP Development
- Cross-Functional Collaboration: Involve stakeholders from different departments, including maintenance, operations, safety, and quality assurance, to ensure that SOPs are comprehensive and aligned with organizational goals.
- Workshop and Brainstorming Sessions: Organize workshops or brainstorming sessions with key stakeholders to gather input, identify requirements, and define the scope of SOPs.
- Pilot Testing: Before finalizing SOPs, test them with a small group of maintenance personnel to gather feedback, identify potential issues, and make necessary revisions.
- Training and Education: Provide training and education to all stakeholders on the purpose, content, and implementation of SOPs to ensure buy-in and adherence.
3. Documentation and Formatting Guidelines
- Clear and Concise Language: Use clear, simple language that is easily understood by all stakeholders, avoiding technical jargon or ambiguous terms.
- Structured Format: Organize SOPs in a logical, step-by-step format, with each task or procedure clearly defined and numbered for easy reference.
- Visual Aids: Incorporate diagrams, flowcharts, or photographs where necessary to illustrate complex procedures or clarify instructions.
- Version Control: Implement a version control system to track changes, revisions, and updates to SOPs, ensuring that all stakeholders have access to the latest version.
- Accessibility: Make SOPs readily accessible to all relevant personnel, either through a centralized document management system, intranet portal, or printed copies in designated work areas.
Implementing SOPs in Maintenance Management using a CMMS
Implementing SOPs in maintenance management using a Computerized Maintenance Management System (CMMS) can significantly improve the efficiency, reliability, and safety of maintenance operations.
1. Integration of SOPs into CMMS
- Centralized Repository: A CMMS serves as a centralized repository for storing, accessing, and managing SOPs, ensuring that all relevant documents are readily available to maintenance personnel.
- Document Linking: SOPs can be linked directly to equipment records, work orders, or maintenance tasks within the CMMS, providing quick and easy access to relevant procedures during the execution of maintenance activities.
- Version Control: CMMS software enables version control for SOPs, ensuring that maintenance personnel always have access to the latest revisions and updates.
- Audit Trail: CMMS systems maintain an audit trail of changes made to SOPs, including revisions, approvals, and comments, providing transparency and accountability in the documentation process.
2. Training and Onboarding
- Training Modules: CMMS platforms often include built-in training modules or learning management systems (LMS) that allow organizations to create and deliver training materials related to SOPs directly within the system.
- Interactive Tutorials: CMMS software may offer interactive tutorials or walkthroughs to familiarize users with the SOPs and demonstrate how to navigate the system effectively.
- Certification Tracking: CMMS systems can track and manage certifications and qualifications required for performing specific maintenance tasks, ensuring that personnel are adequately trained and authorized to follow SOPs.
3. Workflow Automation
- Task Assignment: SOPs can be integrated into automated workflow processes within the CMMS, streamlining the assignment of maintenance tasks and ensuring that personnel follow the prescribed procedures.
- Notification and Alerts: CMMS software can generate automatic notifications and alerts to remind maintenance personnel of upcoming tasks, deadlines, or changes to SOPs, ensuring timely compliance with procedures.
- Escalation Procedures: In the event of non-compliance with SOPs or unresolved issues, CMMS systems can escalate notifications to higher-level management or supervisors for resolution, ensuring adherence to established protocols.
4. Performance Monitoring and Compliance
- KPI Tracking: CMMS platforms allow organizations to track maintenance KPIs, such as adherence to SOPs, mean time to repair (MTTR), and equipment downtime, enabling continuous improvement and optimization.
- Compliance Reporting: CMMS systems can generate compliance reports and audit trails to demonstrate adherence to SOPs, regulatory requirements, and industry standards, facilitating regulatory compliance and audit readiness.
- Root Cause Analysis: CMMS software provides tools for conducting root cause analysis of maintenance issues or failures, enabling organizations to identify underlying causes, update SOPs accordingly, and prevent the recurrence of similar incidents in the future.
By leveraging the capabilities of CMMS software, organizations can effectively implement SOPs in maintenance management, streamline operations, improve compliance, and ultimately enhance the reliability and performance of their assets.
Benefits of Implementing SOPs in Maintenance
Implementing Standard Operating Procedures (SOPs) in maintenance management offers a wide many benefits, ranging from improved operational efficiency to enhanced safety measures. The following are the key advantages of integrating SOPs into maintenance practices:
1. Improved Operational Efficiency
- Streamlined Processes: SOPs provide standardized guidelines and procedures for performing maintenance tasks, reducing ambiguity, and streamlining workflows.
- Reduced Downtime: By following SOPs, maintenance activities are carried out more efficiently, minimizing equipment downtime and maximizing production uptime.
- Optimized Resource Allocation: SOPs help allocate resources such as manpower, materials, and equipment more effectively, reducing waste and improving resource utilization.
- Faster Response to Issues: With predefined procedures in place, maintenance personnel can respond more quickly to equipment breakdowns or malfunctions, minimizing the impact on operations.
2. Consistency in Performance
- Uniformity Across Teams: SOPs ensure consistency in how maintenance tasks are performed, regardless of the individual or team carrying them out.
- Quality Assurance: By adhering to standardized procedures, maintenance activities are performed to a consistent level of quality, reducing variability and improving overall reliability.
- Compliance Adherence: SOPs help ensure compliance with regulatory requirements, industry standards, and organizational policies, reducing the risk of non-compliance and associated penalties.
- Documentation and Traceability: SOPs provide a documented record of maintenance activities, facilitating traceability and accountability for actions taken.
3. Enhanced Safety Measures
- Defined Safety Protocols: SOPs include safety procedures and protocols to mitigate risks and ensure the safety of maintenance personnel, equipment, and the surrounding environment.
- Training and Education: SOPs serve as a reference tool for training new maintenance personnel - promoting awareness of safety hazards and best practices.
- Risk Reduction: By following standardized safety protocols outlined in SOPs, the risk of accidents, injuries, and occupational hazards is minimized.
- Emergency Preparedness: SOPs include procedures for responding to emergencies or hazardous situations, ensuring that maintenance personnel are adequately prepared to handle unexpected events.
4. Cost Reduction and Resource Optimization
- Preventive Maintenance: SOPs facilitate the implementation of preventive maintenance programs, reducing the likelihood of costly equipment failures and unplanned downtime.
- Efficient Resource Management: By following SOPs, organizations can optimize resource allocation, minimize wastage, and reduce unnecessary expenditures.
- Extend Asset Life Expectancy: SOPs help extend the lifespan of equipment and facilities by ensuring that maintenance tasks are performed at regular intervals and according to manufacturer recommendations.
- Improved Budget Planning: With SOPs in place, organizations can better predict maintenance costs, plan budgets, and allocate funds for critical maintenance activities.
Common Mistakes to Avoid in SOP Implementation
The following are three mistakes to avoid when implementing SOPs in maintenance operations:
1. Unclear Communication
- Unclear Instructions: One of the most common pitfalls in SOP implementation is the use of vague or ambiguous language in procedure documentation. Unclear instructions can lead to confusion among maintenance personnel, resulting in errors or deviations from the intended process.
- Failure to Communicate Changes: Changes to SOPs, whether due to process improvements, regulatory updates, or feedback from frontline workers, must be communicated clearly and promptly to all relevant stakeholders. Failure to do so can result in outdated or inaccurate procedures being followed, compromising safety and efficiency.
- Inadequate Training on SOPs: Simply providing SOP documentation is not sufficient; organizations must ensure that maintenance personnel are adequately trained on how to interpret and apply the procedures in practice. Lack of training can lead to misunderstandings, non-compliance, and suboptimal performance.
2. Insufficient Training and Education
- Limited Training Resources: Organizations often underestimate the importance of investing in training resources for SOP implementation. Inadequate training materials, lack of training sessions, or insufficient support for on-the-job training can hinder the successful adoption of SOPs.
- Ineffective Training Methods: Training programs must be tailored to the needs and learning styles of maintenance personnel. A One-size-fits-all approach is often ineffective, leading to disengagement or poor understanding of SOPs.
- Insufficient Training: SOPs should evolve over time to reflect changes in technology, best practices, and organizational requirements. However, without ongoing training initiatives, maintenance personnel may not be aware of updates or changes to SOPs, leading to non-compliance and outdated procedures being followed.
3. Failure to Update SOPs in a Timely Manner
- Lack of Revision Schedule: SOPs should be regularly reviewed and updated to ensure their relevance and effectiveness. However, without a clear revision schedule or process in place, SOPs become outdated, leading to inefficiencies and potential safety hazards.
- Resistance to Change: Maintenance personnel may be resistant to changes in SOPs, particularly if they have been following the same procedures for an extended period. Organizations must address resistance to change through effective communication, training, and stakeholder engagement strategies.
- Overlooking Feedback from Frontline Workers: Frontline maintenance personnel are often the first to identify issues or inefficiencies with SOPs. Organizations must actively solicit feedback from these workers and incorporate their insights into the revision process to ensure that SOPs remain relevant and practical.
Continuous Improvement Strategies
Continuous improvement is essential for ensuring the long-term effectiveness and relevance of Standard Operating Procedures (SOPs) in maintenance management. By implementing continuous improvement strategies, organizations can identify areas for enhancement, optimize existing processes, and adapt to evolving industry standards and best practices.
1. Feedback Mechanisms
- Regular Feedback Sessions: Organize regular feedback sessions with maintenance personnel to gather insights, suggestions, and concerns regarding SOPs. Encourage open communication and constructive feedback to identify areas for improvement.
- Anonymous Surveys: Implement anonymous surveys or suggestion boxes to allow maintenance personnel to provide feedback anonymously, facilitating honest and candid responses.
2. Performance Monitoring
- Key Performance Indicators (KPIs): Define and track KPIs related to maintenance activities, such as adherence to SOPs, mean time between failures (MTBF), and overall equipment effectiveness (OEE). Analyze performance metrics to identify trends, patterns, and areas for improvement.
Root Cause Analysis: Conduct root cause analysis of maintenance issues or failures to identify underlying causes and systemic issues that may require process improvements or updates to SOPs.
3. Continuous Training and Education
- Ongoing Training Programs: Offer ongoing training programs and workshops to ensure that maintenance personnel are aware of updates to SOPs, changes in industry standards, and emerging best practices. Provide opportunities for skill development and competency enhancement.
- Cross-Training Initiatives: Implement cross-training initiatives to broaden the skills of maintenance personnel and increase flexibility in task assignments. Cross-trained employees can provide valuable insights and perspectives for improving SOPs.
4. Process Optimization
- Lean Principles: Apply principles of lean maintenance, such as value stream mapping and waste reduction techniques, to identify inefficiencies and streamline maintenance processes. Eliminate unnecessary steps, reduce lead times, and optimize resource utilization.
- Kaizen Events: Organize Kaizen events or rapid improvement workshops focused on specific areas of maintenance operations. Encourage participation from cross-functional teams to generate innovative solutions and implement process improvements.
5. Collaboration and Knowledge Sharing
- Communities of Practice: Establish communities of practice or knowledge-sharing forums where maintenance personnel can exchange ideas, best practices, and lessons learned related to SOP implementation. Encourage collaboration and cross-functional learning.
- Lessons Learned Sessions: Conduct lessons learned sessions following maintenance activities or projects to capture valuable insights, identify successes and challenges, and document best practices for future reference.
By implementing these continuous improvement strategies, organizations can ensure that SOPs remain relevant, effective, and aligned with the evolving needs of maintenance management. Continuous improvement fosters a culture of innovation, learning, and excellence, driving ongoing enhancements in maintenance practices and performance.
TABLE OF CONTENTS
Keep Reading
Ever find yourself checking into a luxury hotel and expecting a relaxing stay, only to find a ...
11 Apr 2025
Organizations are witnessing swift changes in the business environment and confronting a ...
8 Apr 2025
Last month, news outlets and the entire internet was abuzz with the return of NASA astronauts ...
3 Apr 2025
What comes first - CMMS or predictive maintenance? If your answer is either, it is correct. ...
28 Mar 2025
Artificial intelligence (AI) talk has become commonplace. Today, engaging in business-focused ...
27 Mar 2025
Imagine a world where machines predict, diagnose, and fix their issues before they fail. This ...
25 Mar 2025
A facility maintenance plan is at the core of a facility’s operations. This organized ...
21 Mar 2025
Think of managing your maintenance operations like managing a championship sports team. Just ...
21 Mar 2025
The maintenance sector is battling a severe talent shortage that threatens to undermine ...
7 Mar 2025
Manufacturing maintenance is the backbone of industrial efficiency, ensuring machines run ...
5 Mar 2025
No one likes playing a guessing game when equipment breaks down. Yet, maintenance teams often ...
4 Mar 2025
The size of the preventive maintenance software market is discussed in millions of dollars, ...
4 Mar 2025
The organizational structure and corporate hierarchy vary from company to company. Large ...
28 Feb 2025
Maintenance procedures are essential for ensuring the longevity and reliability of machinery ...
21 Feb 2025
Sustainability is no longer just a buzzword; it's a critical component of corporate social ...
20 Feb 2025
A Computerized Maintenance Management System (CMMS) relies on accurate, well-organized data ...
18 Feb 2025
In an era where technology drives operational efficiency, Computerized Maintenance Management ...
14 Feb 2025
A Computerized Maintenance Management System (CMMS) is a key component of modern maintenance ...
13 Feb 2025
Introduction Maintenance management is the foundation of maintenance operations in industries ...
11 Feb 2025
Introduction A Computerized Maintenance Management System (CMMS) is software designed to help ...
7 Feb 2025