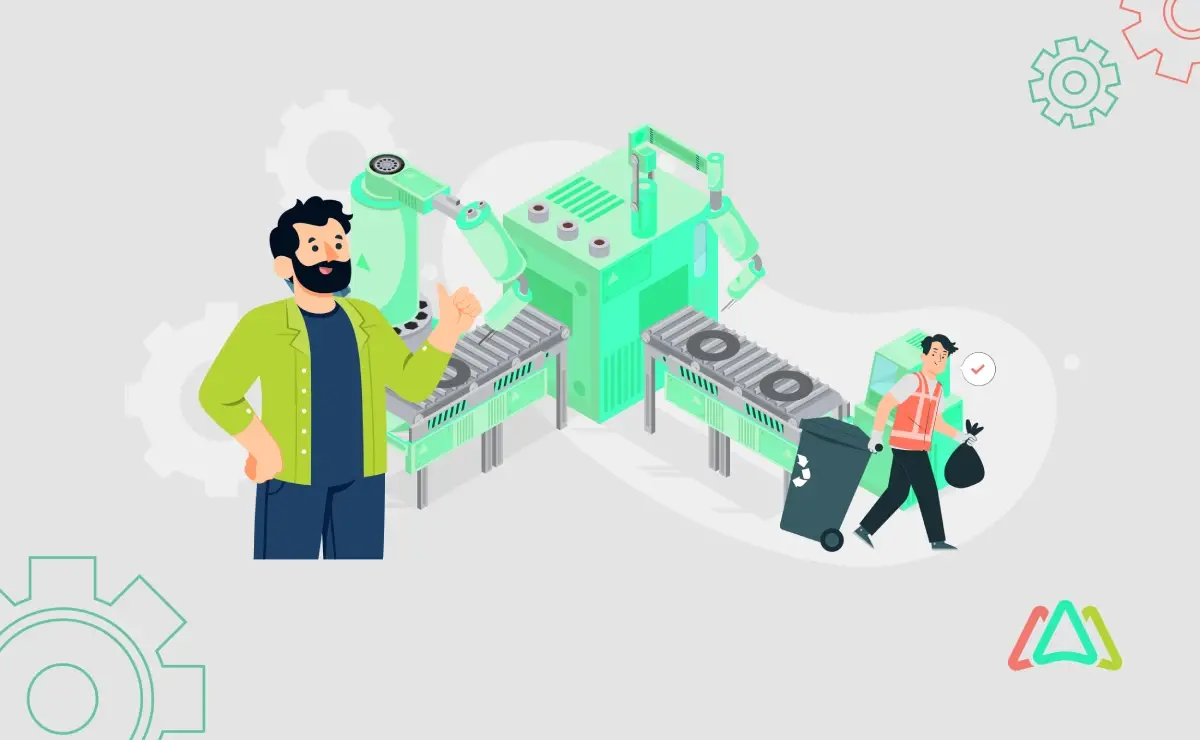
Sustainability and Additive Manufacturing - Reducing Waste in Production
Sustainability has become a key focus in modern manufacturing, with industries seeking innovative ways to reduce waste and minimize environmental impact. Additive Manufacturing (AM) emerges as a transformative solution, offering opportunities for waste reduction, energy efficiency, and resource conservation. According to research, the Additive Manufacturing market is projected to grow at a CAGR of 20.3% from 2024 to 2031, reaching $93.36 billion. AM's role in driving sustainable practices is becoming increasingly significant. By building products layer by layer, Additive Manufacturing minimizes excess material use. It supports greener production methods across various industries, making it a key technology for the future of sustainable manufacturing.
Benefits of Sustainability in Additive Manufacturing
Additive Manufacturing (AM) plays a vital role in advancing sustainability within the manufacturing sector by promoting the use of eco-friendly materials and optimizing energy efficiency. AM provides substantial environmental benefits through material reuse, reduced waste, and energy conservation. The following are some of the benefits of Additive Manufacturing:
Circular Economy Principles
Additive Manufacturing aligns seamlessly with the principles of a circular economy by encouraging the use of recyclable, biodegradable, or reusable materials. This helps create a closed-loop system where resources are continuously repurposed, minimizing waste and environmental impact. By reducing dependency on virgin materials, AM promotes a sustainable manufacturing ecosystem.
Bio-Based Materials
A growing trend in Additive Manufacturing is the adoption of bio-based thermoplastics derived from renewable sources like plant-based polymers. These materials not only cut down on the use of non-renewable resources but also enhance the environmental advantages of AM by offering biodegradable and sustainable alternatives to traditional materials.
Innovative Material Recycling
One of the key advantages of Additive Manufacturing is its ability to recycle materials during the production process. By reusing excess material, such as the unfused powder from a laser powder bed fusion (LPBF) build job, manufacturers can lower overall waste, conserve resources, and improve production efficiency. This significantly contributes to reducing the carbon footprint of manufacturing operations.
Material Efficiency
Unlike traditional subtractive manufacturing, where large amounts of material are wasted, Additive Manufacturing's precise layer-by-layer approach dramatically reduces material waste. Industries like aerospace benefit from reduced buy-to-fly ratios, meaning more efficient resource utilization and less environmental impact.
Energy Conservation
The design capabilities of Additive Manufacturing allow for the production of lightweight components that consume less energy both during manufacturing and throughout the product’s lifecycle. In industries such as aerospace and automotive, these lighter components lead to reduced fuel consumption, enhancing energy efficiency and further supporting sustainability.
How to Achieve Sustainability through Additive Manufacturing
Additive Manufacturing serves as a transformative force in advancing sustainability across industries. Through procedural innovations and advanced design capabilities, AM minimizes material waste, optimizes resource use, and significantly improves energy efficiency. Below are key ways in which AM maximizes sustainability at various stages of the production lifecycle, from design to material use and beyond.
Life Cycle Sustainability Analysis
Life Cycle Sustainability Assessment (LCSA) is essential for evaluating the environmental, social, and economic impacts of Additive Manufacturing (AM) across the entire product life cycle. This comprehensive approach helps guide decision-making towards more sustainable outcomes. However, despite its significance, the availability of LCSA data for AM remains limited, and wider industry adoption is crucial to fully measuring and understanding the sustainability benefits AM offers.
Layer-by-Layer Production Process
The layer-by-layer approach in Additive Manufacturing minimizes material waste by using only what is needed, unlike traditional subtractive manufacturing, which removes excess material. This precision leads to significant resource efficiency, contributing to a more sustainable production process.
Lightweight Components & Energy Efficiency
Additive Manufacturing processes use up to 25% less energy when compared to conventional manufacturing methods. Industries like aerospace and automotive particularly benefit from lightweight AM components, which help reduce fuel consumption during operation, improving energy efficiency and reducing emissions.
Design Innovation
AM offers unmatched design flexibility, enabling the creation of complicated geometries, hollow structures, and optimized designs that use less material without compromising strength. Siemens Energy, for instance, achieved a 30% emissions reduction through innovative AM designs.
Efficient Use of Raw Materials
By minimizing waste, AM aligns with lean manufacturing principles, optimizing the use of raw materials during design and production stages, which enhances overall resource efficiency.
Localized, On-Demand Production
AM promotes localized, on-demand production, reducing transportation emissions by limiting the need for long-distance shipping. This also cuts down on overproduction and excess inventory, making supply chains more resilient.
Extending Product Life through Additive Manufacturing
Additive Manufacturing facilitates easy repair and replacement of parts, significantly extending product lifespans. In sectors like automotive and aerospace, spare parts can be printed on demand, aligning with circular economy principles by prolonging the use of products.
Challenges to Achieving Full Sustainability with Additive Manufacturing
While Additive Manufacturing offers significant sustainability benefits, several challenges remain in realizing its full potential. The following are some of these challenges:
Material Challenges
The extraction and processing of materials, particularly oil-based and mined resources, pose environmental concerns. Many AM materials are derived from non-renewable sources, which impacts sustainability efforts. Furthermore, the availability of standardized, eco-friendly materials for AM is limited, and recycling specialized materials used in AM processes is complex and inefficient. These issues make it difficult for the industry to embrace fully.
Process Challenges
AM processes such as heating, melting, and fusing materials require substantial energy, limiting the overall sustainability gains. Although AM can reduce waste, the high energy consumption involved offsets some of these benefits. Additionally, scaling AM for mass production while maintaining energy efficiency is a significant hurdle. The technology excels in small-scale, customized production but faces limitations in energy conservation when applied at industrial levels.
Knowledge and Data Challenges
There is a shortage of comprehensive data on the environmental impact of AM processes and materials. More robust life cycle analysis (LCA) tools and sustainability metrics are needed to assess AM's environmental footprint and guide best practices accurately. The lack of standardized data hinders the industry's ability to measure and improve sustainability efforts.
Sustainable Design Strategies in Additive Manufacturing
Sustainability in Additive Manufacturing (AM) is being advanced through innovative design strategies that not only extend product life but also reduce waste and optimize resource use. These approaches are reshaping how products are developed, ensuring that environmental impact is minimized without compromising performance or functionality.
Design for Life Extension
One of the core strategies in sustainable design is leveraging topology optimization and generative design. These advanced techniques use algorithms to craft structures that are both lightweight and durable, ensuring products last longer. By minimizing the amount of material required while maintaining structural integrity, AM reduces the need for frequent replacements. This approach not only conserves materials but also supports a more sustainable product lifecycle, ultimately reducing waste over time.
Waste Reduction and Material Substitution
Additive Manufacturing excels in material efficiency, particularly through the creation of complex lattice structures that reduce material usage without sacrificing strength. These designs lower production waste and enhance overall material efficiency. Additionally, AM enables part consolidation, merging multiple components into a single, streamlined piece, further reducing production steps and material use. Moreover, the substitution of high-density materials with low-density alternatives contributes to lower energy consumption during production and product use, driving sustainability from both a material and operational standpoint.
Modular and Reusable Design
Another key sustainability strategy in AM is the focus on modular and reusable designs. Products are increasingly being engineered with components of varying lifespans, allowing for easy disassembly and replacement of individual parts. This modularity ensures that entire products don’t need to be discarded when one part fails, conserving resources and extending product lifespans. Such an approach aligns with circular economy principles by promoting repair, reuse, and recycling.
Exploring Alternative Materials
The future of Additive Manufacturing is deeply tied to the development of renewable, bio-based, and recyclable materials. These alternatives offer significant potential for reducing reliance on non-renewable resources and cutting down on waste. However, scaling the production of these sustainable materials while maintaining the required functionality and cost-effectiveness remains a considerable challenge for the industry.
Recycling and Waste Infrastructure
For Additive Manufacturing to fully embrace its role in a circular economy, improved recycling infrastructure is essential. Establishing systems for material identification and standardized labeling of AM parts will greatly streamline recycling efforts, ensuring materials can re-enter the production cycle. Such advances will promote circular material flows, closing the loop on resource use and significantly reducing waste.
Embracing Sustainable Additive Manufacturing
Additive Manufacturing (AM) offers significant benefits, such as reducing waste, improving energy efficiency, and promoting a circular economy. By utilizing advanced design strategies and sustainable materials, AM helps businesses optimize production and minimize environmental impact. As the future of manufacturing shifts toward sustainability, AM stands out as a transformative technology capable of driving this change. Now is the time for businesses to explore and invest in AM to contribute to a more sustainable and resource-efficient world.
“Small acts, when multiplied by millions of people, can transform the world.” — Howard Zinn
TABLE OF CONTENTS
Keep Reading
Edge computing is an innovative technology that enables data to be processed at the source, ...
24 Jun 2025
Facility management has undergone a significant transformation in recent times. Take, for ...
20 Jun 2025
A facility maintenance plan is at the core of a facility’s operations. This organized ...
19 Jun 2025
In the early days, preventive maintenance could be done effectively with a trained eye and a ...
17 Jun 2025
Sticky notes fall off, whiteboard grids get wiped, and spreadsheets never beep when a ...
13 Jun 2025
Handing a slice of your maintenance workload to a contractor is less about “giving up ...
12 Jun 2025
Downtime in enterprise environments doesn’t just mean a stop in operations; it means lost ...
10 Jun 2025
Understanding equipment functionality is crucial for effective repairs. A clear, systematic ...
6 Jun 2025
Maintenance managers know that every unplanned equipment failure is more than a simple ...
5 Jun 2025
What keeps a facility running smoothly? Initially, many of us may zoom in on its equipment, ...
29 May 2025
In today's digital world, every decision needs to pass the test of strategic and operational ...
27 May 2025
The business world is very different from a decade ago. Technological advancements have grown ...
23 May 2025
Picture this: a maintenance technician inspects a complex pump system. Instead of typing a ...
20 May 2025
For most of the 20th century, maintenance teams mainly applied a reactive approach to ...
9 May 2025
Imagine visiting a manufacturing plant where maintenance technicians gather around a large ...
8 May 2025
Maintenance management faces complexities across all industries, escalating with ...
6 May 2025
Ever find yourself checking into a luxury hotel and expecting a relaxing stay, only to find a ...
11 Apr 2025
Organizations are witnessing swift changes in the business environment and confronting a ...
8 Apr 2025
Last month, news outlets and the entire internet was abuzz with the return of NASA astronauts ...
3 Apr 2025
What comes first - CMMS or predictive maintenance? If your answer is either, it is correct. ...
28 Mar 2025