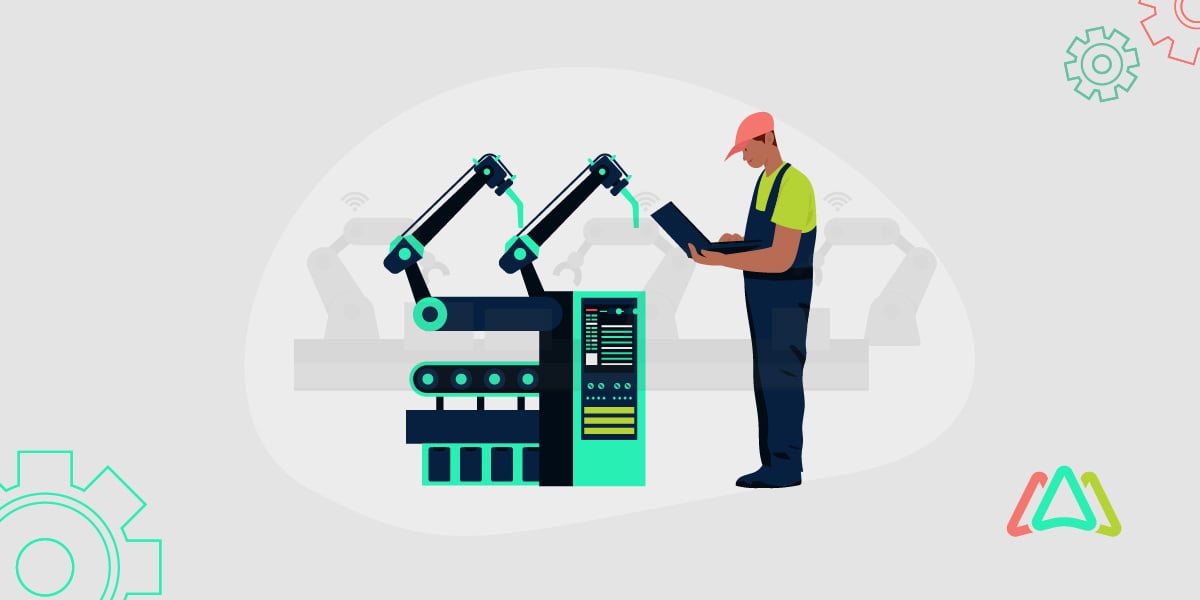
How CMMS Enables Predictive Maintenance
What comes first - CMMS or predictive maintenance? If your answer is either, it is correct.
The relationship between CMMS and predictive maintenance causes confusion among many maintenance professionals. Both are essential for organizations pursuing maintenance excellence. These two systems complement each other, driving the overall maintenance strategy. The coordination between CMMS and predictive maintenance accelerates the maturity curve of an organization's maintenance processes.
Feature | CMMS | Predictive Maintenance (PdM) |
Definition |
A Computerized Maintenance Management System (CMMS) is a software application that helps organizations manage their maintenance operations by keeping track of all the assets, equipment, and facilities that need maintenance. CMMS software is designed to be a centralized database that stores all the maintenance-related information, including work orders, maintenance history, spare parts inventory, and preventive maintenance schedules. |
Predictive Maintenance (PdM) is a proactive maintenance strategy that utilizes data and technology to anticipate equipment failures. By continuously monitoring and analyzing equipment health, predictive maintenance (PdM) enables businesses to take preventive actions before significant breakdowns occur, unlike preventive maintenance, which happens according to a schedule. |
Function |
Work order management, asset tracking, inventory control, compliance tracking. |
Real-time condition monitoring, predictive analytics, and automated alerts. |
Industry Example |
Suited for preventive maintenance scheduling use cases |
Best for proactive, data-driven maintenance use cases |
Cost |
Lower upfront cost; subscription-based or one-time licensing. |
Higher initial investment; long-term cost savings. |
ROI Timeline |
Short-term immediate efficiency gains. |
Long-term strategic cost reduction with a continuous improvement approach to achieve the pinnacle of maintenance excellence |
It’s important to note that predictive maintenance and CMMS software are not used interchangeably. They are distinct components of a well-thought-out maintenance strategy. In many organizations’ maintenance strategies, you can expect a CMMS but not predictive maintenance. Organizations that adopt strategies that involve predictive maintenance are few.
The Predictive Maintenance Lifecycle
Fundamentally, CMMS is a maintenance management software, while predictive maintenance represents a high-level intervention within the overall maintenance strategy. The differences between these two are summarized in the following table.
This lifecycle encompasses all steps from asset monitoring to corrective action, feeding back into the data loop to improve asset monitoring continuously. The lifecycle involves three main steps:
- Data acquisition
- Analysis comprising diagnostics and prognostics, and
- Action through work order management.
Data Acquisition
During the data acquisition step, sensors attached to equipment detect abnormalities from the control conditions. This equipment data is sent to a CMMS system (when available); otherwise, it is archived in a computer database.
Data sources include vibration analysis, acoustic analysis, and infrared analysis. Vibration analysis suits high-rotating equipment and identifies board looseness and equipment imbalance issues. Acoustic analysis uses sound to identify mechanical and electrical problems like friction and stress. Infrared analysis uses temperature as an indicator to identify issues like overheating and motor stress. Data is also incorporated from maintenance work order history, inventory management systems, and external third-party benchmarking tools.
Analysis
Diagnostics and prognostics are performed in the analysis phase. Predictive maintenance requires defining normal parameters (control) against which asset conditions are compared. This helps measure abnormalities based on sensor data. An alert is generated when a deviation exceeds the threshold, kickstarting the corrective action.
Action
The action phase involves work order management. A work order is created based on predictions from collected data, including past maintenance orders and schedules. Typically generated through CMMS software, a technician executes the work order. Once closed, information from the work order feeds back into the system, enhancing the predictive engine's accuracy.
The cycle continues until the organization achieves the north star regarding its maintenance management goals. Organizations can effectively implement CMMS software and predictive maintenance by understanding these processes to enhance their overall maintenance strategy. CMMS implementations are never fully complete; they only initiate a continuous improvement cycle, motivating organizations to achieve higher maintenance management goals.
CMMS and PdM Go Well Together
The role of a CMMS is a key component in the maintenance management journey from preventive to predictive to proactive. CMMS software forms the bedrock of a continuously improving maintenance strategy. The Click Maint article on automated data collection using a CMMS highlights this.
Robust CMMS software supports equipment tracking and condition monitoring, automatically generating work orders when an alert is triggered. This alert could be caused by any of the conditions that are being monitored - temperature increase, vibration, noise, or a combination of these. By using the CMMS to track data related to all maintenance activities that are being performed, the maintenance and reliability teams gain more insight into the overall health of equipment and machine assets. Maintenance and operations managers can make better data-driven decisions to maximize uptime and reduce machine life cycle losses and life cycle costs.
Beyond Predictive: Machines That Think and Act
Traditional maintenance relies on scheduled checkups or predictive AI, which alerts humans about potential failures. Nowadays, with the advent of smart sensors and cloud computing, machines can analyze their condition in time and adjust where it is concerned.
For example, imagine an engine detecting overheating and automatically cooling itself down or a factory machine sensing a worn-out part and ordering a replacement before it breaks. Indeed, this is superb!
But this transition is more than just a matter of convenience — it will absolutely overhaul industries. The decreased incidence of outages, lower repair costs, and near-zero human involvement mean businesses can run quicker, smarter, and more efficiently than ever before.
The Role of CMMS in Predictive Maintenance
Data generated for predictive maintenance purposes is of limited use if it is not linked to a Computerized Maintenance Management System (CMMS). With this data in the CMMS, maintenance professionals perform analysis to substantiate their decisions and confidently make predictive decisions, empowering them in their roles.
A CMMS performs several key functions that build up to predictive maintenance.
Preventive Maintenance
Scheduling preventive maintenance is a core function of the CMMS. This also serves as a data collection touchpoint, thus adding to the predictive maintenance data repository. The data points include but are not restricted to the following:
- Work order date
- Assigned technician
- Issue
In addition to providing important data points, this also ensures that no work order gets missed.
Work Order Automation
A CMMS helps automate work order management with custom workflows and ultimately makes work order management more efficient. CMMS (with AI) can automate the creation of work orders based on real-time data from IoT sensors and predictive maintenance analytics. When an anomaly or failure is detected, the system can automatically generate a work order specifying the tasks required to deal with the issue. This reduces manual effort and ensures timely interventions.
Archiving Data
The data the CMMS continuously collects can be put into the following two categories.
- Maintenance data: Scheduled maintenance and breakdown maintenance collect valuable data. This information is registered in the CMMS, which allows for the analysis of breakdown reasons and serves as a data repository.
- Performance data: Industrial sensors continuously feed data points. Integrating the CMMS with all the sensors will ensure that the sensor data points are also captured with the CMMS. CMMS vendors can facilitate this integration through their open API systems. In most situations, a development project will be indispensable to get all the integrations going, covering CMMS, industrial sensors, and other data lake applications, if present.
Data Analysis
The CMMS functions as a data repository, enabling basic analysis related to maintenance management. This analysis is commonly referred to as the Management Information System (MIS), which generates reports for executive management, providing an overview of progress toward maintenance management goals.
An advanced analysis layer is required to perform complex analyses, such as pattern identification and deeper insight extraction. This layer enhances the ability to identify patterns and produce more detailed insights.
Ultimately, a predictive engine layer will further refine the analysis by offering predictions regarding future equipment performance and life cycles.
The Future is PdM with CMMS.
The future of maintenance management, enabled by systems and software, is trending toward an optimal combination of Computerized Maintenance Management Systems (CMMS) and predictive maintenance. With the integration of predictive maintenance (PdM) and CMMS, automated analysis and real-time reporting provide accurate information on assets at all times.
As these systems mature, they will facilitate the creation of advanced workflows. CMMS capabilities can be configured based on inputs from predictive maintenance systems. For example, email notification triggers and mobile app alerts can address problems detected in real time.
Ultimately, this combination could perform more complex strategic business functions, such as accurate capital forecasting. Forecasting is a vulnerability for most maintenance operations and strategic business plans. This is primarily due to the absence of relevant data and corresponding analysis. Predicting equipment failure or the end of its helpful life allows for better budgeting and cost projections, which improves financial planning accuracy.
TABLE OF CONTENTS
Keep Reading
Ever find yourself checking into a luxury hotel and expecting a relaxing stay, only to find a ...
11 Apr 2025
Organizations are witnessing swift changes in the business environment and confronting a ...
8 Apr 2025
Last month, news outlets and the entire internet was abuzz with the return of NASA astronauts ...
3 Apr 2025
Artificial intelligence (AI) talk has become commonplace. Today, engaging in business-focused ...
27 Mar 2025
Imagine a world where machines predict, diagnose, and fix their issues before they fail. This ...
25 Mar 2025
A facility maintenance plan is at the core of a facility’s operations. This organized ...
21 Mar 2025
Think of managing your maintenance operations like managing a championship sports team. Just ...
21 Mar 2025
The maintenance sector is battling a severe talent shortage that threatens to undermine ...
7 Mar 2025
Manufacturing maintenance is the backbone of industrial efficiency, ensuring machines run ...
5 Mar 2025
No one likes playing a guessing game when equipment breaks down. Yet, maintenance teams often ...
4 Mar 2025
The size of the preventive maintenance software market is discussed in millions of dollars, ...
4 Mar 2025
The organizational structure and corporate hierarchy vary from company to company. Large ...
28 Feb 2025
Maintenance procedures are essential for ensuring the longevity and reliability of machinery ...
21 Feb 2025
Sustainability is no longer just a buzzword; it's a critical component of corporate social ...
20 Feb 2025
A Computerized Maintenance Management System (CMMS) relies on accurate, well-organized data ...
18 Feb 2025
In an era where technology drives operational efficiency, Computerized Maintenance Management ...
14 Feb 2025
A Computerized Maintenance Management System (CMMS) is a key component of modern maintenance ...
13 Feb 2025
Introduction Maintenance management is the foundation of maintenance operations in industries ...
11 Feb 2025
Introduction A Computerized Maintenance Management System (CMMS) is software designed to help ...
7 Feb 2025
Introduction Due to a growing awareness of the need to combat climate change, the green ...
6 Feb 2025