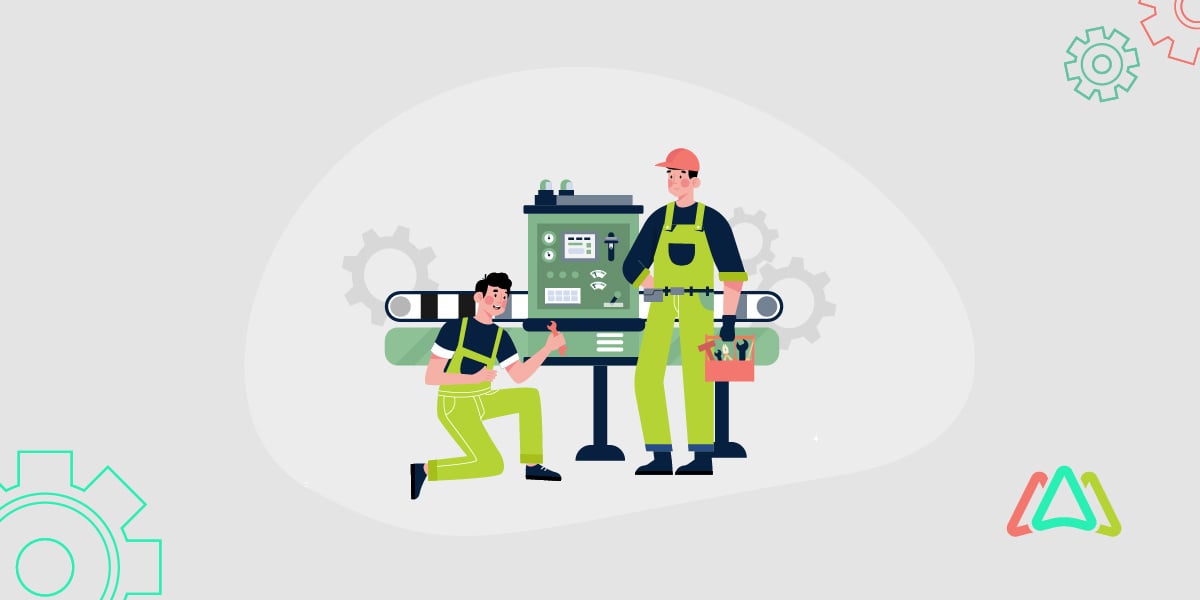
The Human Side of Manufacturing Maintenance
Manufacturing maintenance is the backbone of industrial efficiency, ensuring machines run smoothly, production targets are met, and operational downtime is minimized. In recent years, automation and predictive maintenance technologies have transformed the industry, reducing human error and improving efficiency. However, despite these advancements, human expertise still remains irreplaceable. No machine can match a skilled technician's experience, intuition, and problem-solving skills.
This article explores why people are the most valuable asset in manufacturing maintenance. It delves into their expertise, the impact of safety and well-being, the importance of training, and how employee engagement influences maintenance success. Despite the rise of automation, human expertise remains the cornerstone of a successful maintenance strategy.
The Role of Human Expertise in Maintenance
While automation and technology have transformed manufacturing maintenance, human expertise remains irreplaceable. Skilled technicians bring problem-solving abilities, critical thinking, and intuition that machines simply can’t replicate. From making quick decisions in unexpected situations to identifying potential failures before sensors do, their role is essential in ensuring efficiency, safety, and reliability in industrial operations.
The Power of Skilled Technicians
Even in an era of advanced machinery, skilled technicians are the heartbeat of manufacturing maintenance. Their ability to diagnose and resolve complex issues surpasses what automation can achieve. For example, a machine might indicate a misalignment in a conveyor belt. However, only a trained professional can determine whether it stems from excess vibration, improper installation, or wear and tear.
Human Judgment vs. Automation
While automated systems can detect patterns, human judgment remains essential for troubleshooting. Consider an AI-powered predictive maintenance system that flags a possible overheating issue in a manufacturing plant. The system might recommend shutting down the machine, but an experienced technician may recognize that a minor adjustment to airflow or lubrication can resolve the problem without halting production.
Intuition: Preventing Downtime Before Sensors Do
There are instances where experienced maintenance workers detect early signs of failure that sensors miss. Subtle vibrations, unusual odors, or minor deviations in performance often signal a problem before it escalates. These cues, honed over years of experience, allow technicians to intervene proactively.
Safety and Well-Being: The Cost of Poor Maintenance
Poor maintenance leads to equipment failures and puts workers at risk. Faulty machinery, overlooked hazards, and rushed repairs can result in serious injuries or even fatalities. Prioritizing maintenance isn’t just about efficiency; it’s about protecting the people who keep operations running and ensuring a safe, sustainable work environment.
Maintenance and Workplace Safety
According to OSHA’s 2023 report, the manufacturing sector accounted for 17% of reported workplace injuries and illnesses. While the report does not explicitly link poor maintenance as a primary cause, inadequate safety measures and hazardous conditions are known contributors to workplace incidents.
Manufacturing environments are already high-risk, with heavy machinery, high temperatures, and hazardous materials. Without a proactive maintenance strategy, workers are vulnerable to preventable dangers such as electrical failures, mechanical malfunctions, and exposure to harmful substances. Ensuring a well-maintained work environment isn’t just about compliance but also about protecting lives.
Stress and Burnout: The Hidden Cost of Reactive Maintenance
A purely reactive maintenance approach, where maintenance is only performed after a failure occurs, places immense pressure on workers. Constant firefighting, long hours, and unexpected breakdowns contribute to burnout, stress, and job dissatisfaction.
A Deloitte survey found that 91% of employees reported that excessive stress or burnout negatively affected their work quality, while 83% stated that workplace burnout also strained their relationships. This highlights the widespread impact of burnout on professional performance and personal well-being.
How Preventive Maintenance Improves Workers’ Well-Being
Manufacturers can significantly improve worker well-being by shifting from reactive to preventive maintenance. Preventive maintenance strategies reduce emergency repairs, allow for better workload distribution, and create a safer, more predictable work environment. Studies show that implementing preventive maintenance programs significantly improves technician job satisfaction, productivity, and operational efficiency.
Training and Workforce Development in Maintenance
A well-trained maintenance team is key for reliable operations. Continuous skill development ensures technicians can adapt to new technologies, troubleshoot complex issues, and maintain safety standards. Investing in training improves efficiency and boosts job satisfaction and retention, creating a stronger, more capable workforce.
The Maintenance Skills Gap and Labor Shortage
One of the biggest challenges in manufacturing today is the shortage of skilled maintenance professionals. As experienced technicians retire, younger workers often lack the necessary expertise. A 2023 report by the Manufacturing Institute estimates that 2.1 million manufacturing jobs could go unfilled by 2030 due to skill gaps.
Mentorship and Training
To address the growing skills gap in maintenance, companies must invest in structured mentorship programs and continuous training initiatives. Pairing experienced technicians with new hires accelerates learning and promotes a sense of belonging and professional growth. When employees feel supported and see clear career development opportunities, they are more likely to stay, reducing turnover and strengthening the overall maintenance team.
The Role Of CMMS In Enhancing Human Expertise.
A Computerized Maintenance Management System (CMMS) does not replace technicians. Rather, it improves performance and efficiency when combined with a skilled, well-trained workforce. By providing real-time insights, automated maintenance schedules, and historical data, CMMS empowers technicians to make informed, data-driven decisions. However, to fully leverage its benefits, companies must ensure accurate and detailed reporting of faults and failures.
Many organizations underutilize CMMS data, missing valuable insights that could refine preventive maintenance and reduce recurring breakdowns. When properly analyzed, historical maintenance records can help identify common failure patterns, optimize work order processes, and improve overall equipment reliability. To take full advantage of CMMS software capabilities, maintenance leaders should work with their CMMS providers and ensure that the company is up to date on all features and modules and that end users are trained on how to use them.
Employee Engagement and Maintenance Culture
A strong maintenance culture goes beyond routine repairs—it thrives on employee engagement. When technicians feel valued, heard, and involved in decision-making, they take greater ownership of their work. This sense of responsibility leads to fewer errors, higher efficiency, and a proactive approach to equipment care. Engaged teams don’t just fix problems; they anticipate and prevent them, driving long-term operational success.
Encouraging collaboration, recognizing contributions, and promoting a proactive mindset can transform maintenance from a reactive task into a strategic advantage. By nurturing an environment where maintenance professionals feel empowered and appreciated, companies can improve both reliability and overall operational performance.
Leadership’s Role In Building a Strong Maintenance Culture
Creating a thriving maintenance culture starts at the top. Leaders must actively promote an environment where maintenance is seen as a strategic priority rather than a routine task. This means recognizing and rewarding technicians for their contributions, offering career growth opportunities, and promoting open communication. When leadership champions maintenance excellence, teams feel motivated to uphold higher standards, ultimately improving reliability and efficiency.
The Future: Balancing Automation with Human Skills
As automation advances, the role of human expertise in maintenance is evolving rather than disappearing. While machines handle data analysis and repetitive tasks, skilled technicians provide the critical thinking, adaptability, and problem-solving abilities that automation lacks. The future of maintenance lies in balancing cutting-edge technology with human insight to create more efficient, resilient operations.
How AI and Predictive Maintenance Enhance Human Roles
AI and predictive maintenance are revolutionizing manufacturing, but they work best alongside human expertise. While AI can analyze vast amounts of data and detect potential issues before they escalate, technicians provide the contextual understanding needed to interpret and act on those insights.
For example, AI-driven predictive maintenance systems can flag anomalies in equipment performance, but human technicians validate these predictions, assess real-world conditions, and determine the best course of action. Rather than replacing workers, AI serves as a powerful tool that enhances decision-making, improves efficiency, and reduces unexpected downtime.
Human Expertise: The Key to Smart Maintenance
While automation streamlines processes, machines lack the adaptability, intuition, and problem-solving skills of humans. Maintenance decision-making often involves trade-offs that require human judgment—such as balancing cost, efficiency, and long-term reliability. Even with AI-driven predictive maintenance, human expertise remains irreplaceable in interpreting data, making real-time adjustments, and responding to unexpected challenges.
As technology evolves, maintenance professionals must also evolve. Continuous learning is essential to keep pace with automation, new tools, and advanced diagnostics. Companies that invest in ongoing education and cross-training programs not only future-proof their workforce but also enhance their ability to integrate automation effectively. The strongest maintenance teams will be those that combine technological proficiency with human expertise, leveraging the best of both worlds.
Conclusion - The True Strength Behind Maintenance
Machines may power production, but it’s the people behind them who keep everything running smoothly. A strong maintenance culture requires ongoing training to keep teams skilled, strict safety measures to protect workers, and a culture of recognition that values their contributions. By investing in these areas, manufacturers can reduce downtime, improve efficiency, and build a motivated workforce that drives long-term success. After all, the real strength of any manufacturing facility isn’t just in its machine; it’s in the people who maintain them.
TABLE OF CONTENTS
Keep Reading
Ever find yourself checking into a luxury hotel and expecting a relaxing stay, only to find a ...
11 Apr 2025
Organizations are witnessing swift changes in the business environment and confronting a ...
8 Apr 2025
Last month, news outlets and the entire internet was abuzz with the return of NASA astronauts ...
3 Apr 2025
What comes first - CMMS or predictive maintenance? If your answer is either, it is correct. ...
28 Mar 2025
Artificial intelligence (AI) talk has become commonplace. Today, engaging in business-focused ...
27 Mar 2025
Imagine a world where machines predict, diagnose, and fix their issues before they fail. This ...
25 Mar 2025
A facility maintenance plan is at the core of a facility’s operations. This organized ...
21 Mar 2025
Think of managing your maintenance operations like managing a championship sports team. Just ...
21 Mar 2025
The maintenance sector is battling a severe talent shortage that threatens to undermine ...
7 Mar 2025
No one likes playing a guessing game when equipment breaks down. Yet, maintenance teams often ...
4 Mar 2025
The size of the preventive maintenance software market is discussed in millions of dollars, ...
4 Mar 2025
The organizational structure and corporate hierarchy vary from company to company. Large ...
28 Feb 2025
Maintenance procedures are essential for ensuring the longevity and reliability of machinery ...
21 Feb 2025
Sustainability is no longer just a buzzword; it's a critical component of corporate social ...
20 Feb 2025
A Computerized Maintenance Management System (CMMS) relies on accurate, well-organized data ...
18 Feb 2025
In an era where technology drives operational efficiency, Computerized Maintenance Management ...
14 Feb 2025
A Computerized Maintenance Management System (CMMS) is a key component of modern maintenance ...
13 Feb 2025
Introduction Maintenance management is the foundation of maintenance operations in industries ...
11 Feb 2025
Introduction A Computerized Maintenance Management System (CMMS) is software designed to help ...
7 Feb 2025
Introduction Due to a growing awareness of the need to combat climate change, the green ...
6 Feb 2025