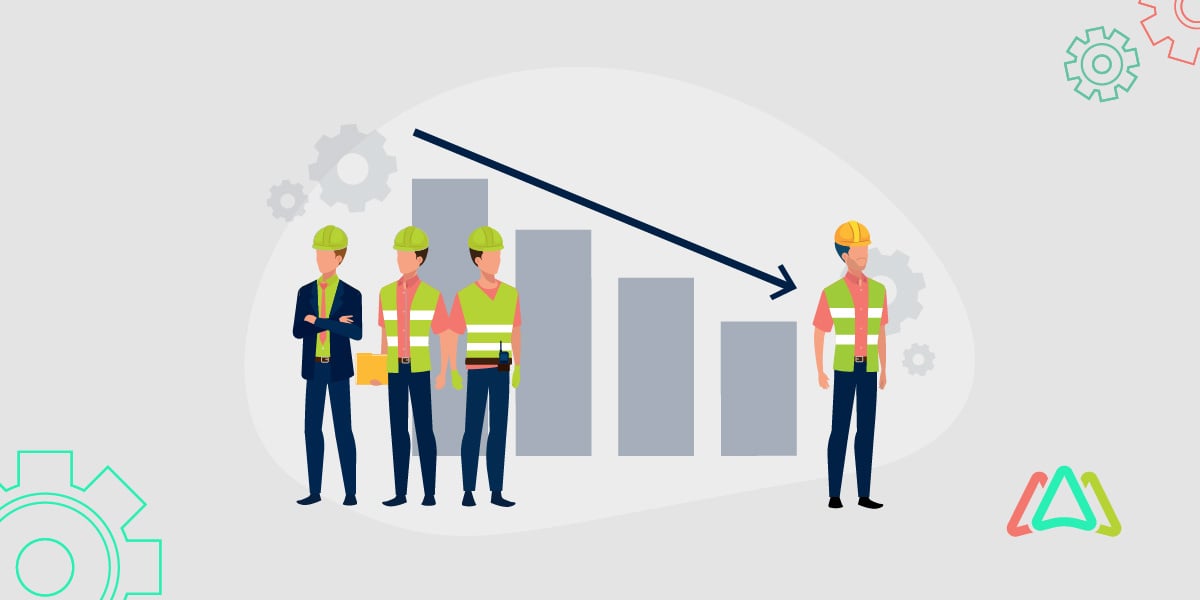
The Talent Shortage in Maintenance and Ways Businesses Can Cope
The maintenance sector is battling a severe talent shortage that threatens to undermine operational efficiency and bottom-line results. Studies show that in 2025, we're facing a staggering global shortfall of 2 million skilled maintenance technicians. Businesses stand or fall on the quality of their maintenance workforce, and today's industrial landscape faces a growing crisis that business leaders must strategically adapt to and cope with or risk costly downtime.
Maintenance professionals are the backbone of industry and manufacturing operations. Without these skilled workers keeping machinery running smoothly and facilities operating efficiently, even the most sophisticated business operations can halt. This isn't just another hiring challenge—it's a fundamental business crisis that demands innovative solutions from leadership.
The impact of this shortage is more than mere staffing headaches. From manufacturing plants to commercial facilities, organizations worldwide are feeling the pressure to evolve their maintenance strategies.
In this article, we'll dive into the causes of this maintenance staffing shortage, examine its real-world impact on business operations, and explore practical strategies that business leaders can implement to protect their operations in this challenging landscape.
Causes of Maintenance Staff Shortages
Before we discuss solutions or how businesses can cope with the talent shortage, let's examine the root causes of the workplace crisis in the maintenance world. Understanding these fundamental challenges is important for business owners and leaders who need to navigate this growing problem.
The talent shortage didn't appear overnight. It's the result of several key factors that have been building up over time. Let's explore four of the leading root causes of the maintenance workforce crisis that is reshaping our industry today.
1. Aging Workforce & Retirements
The demographic shift hitting the maintenance sector represents the most pressing challenge in our current talent crisis. As skilled maintenance professionals from the Baby Boomer generation reach retirement age, they're taking decades of irreplaceable hands-on experience with them. This current wave of retirements isn't just removing workers from the workforce – it's draining away institutional knowledge that kept operations running smoothly for decades.
Industry analysts estimate that nearly 40% of current maintenance technicians will retire within the next five years. Making matters worse, many organizations have failed to implement succession planning strategies. This creates a dangerous knowledge gap that threatens operational continuity and increases the risk of costly equipment failures.
2. Fewer Younger Professionals Entering the Field
The current talent crisis would not be such a pressing concern if there were vibrant replacements ready to step in as Baby Boomers retire. Unfortunately, that's not the case—fewer skilled and talented young professionals are entering the maintenance industry. The growing gap between the high demand for skilled technicians and a diminishing supply of qualified workers creates a perfect storm for businesses across all sectors.
Several factors contribute to this recruitment challenge. Today's young professionals often gravitate toward careers they perceive as more prestigious or technologically advanced, overlooking the sophisticated technical aspects of modern maintenance work. The misconception that maintenance careers offer limited growth potential further compounds this problem despite the field's increasing adoption of cutting-edge technologies and competitive compensation packages.
This perception problem hits businesses particularly hard because modern maintenance roles require more technical expertise than ever before.
3. Skills Gap: Industry Needs vs. Workforce Readiness
Even when companies find workers interested in maintenance careers, a significant challenge remains: the widening skills gap between industry requirements and workforce capabilities.
Modern maintenance professionals must master traditional mechanical skills and navigate complex digital systems. These include a solid understanding of computerized maintenance management systems (CMMS), Internet of Things (IoT) sensors, predictive maintenance, and automated diagnostic tools. The technical demands of the role have expanded dramatically.
For business leaders, this skills gap translates directly to operational risks. Having maintenance staff who can't fully utilize modern maintenance technologies means decreased equipment reliability, longer downtimes, and missed opportunities for predictive maintenance – all of which impact the bottom line and are essential for businesses to be competitive.
4. Impact of Automation and Digitalization
While the skills gap highlights the disconnect between current workforce capabilities and industry needs, the rapid advancement of automation and digitalization further compounds this challenge. The maintenance industry isn't just evolving – it's undergoing a fundamental transformation that's reshaping the very nature of maintenance work.
Traditional maintenance roles, which once relied primarily on mechanical expertise, are now being augmented or replaced by automated systems. This shift isn't just about replacing manual tasks—it represents a complete reimagining of how maintenance work is performed. Smart sensors, predictive analytics, and artificial intelligence are becoming standard tools in modern maintenance operations, creating a demand for a new breed of maintenance professionals.
The Effect of Talent Shortage on Businesses
Having explored the root causes of the talent shortage in the maintenance world, let's examine the reality of its impact on businesses. The effects of this growing crisis extend far beyond simple staffing challenges. They represent a fundamental threat to operational stability and profitability. It’s important for business leaders to fully grasp these implications to understand what's truly at stake if proper measures aren't implemented to address the maintenance talent shortage. Let's examine ways this shortage is impacting businesses today and what it means for their future sustainability.
1. Increased Downtime & Higher Costs
Equipment downtime is more than just a temporary operational hiccup—it's a direct threat to a company's bottom line and competitive position. The maintenance talent shortage has exasperated this challenge, as businesses lack enough skilled staff to maintain critical assets. Without adequate skilled personnel, businesses struggle to maintain optimal equipment performance.
The absence of qualified maintenance professionals creates a ripple effect of operational disruptions. Response times for both emergency repairs and routine preventive maintenance stretch longer than ever before, with large companies potentially losing between $100,000 and $300,000 or more per hour of downtime. Small and medium-sized companies may suffer losses in the range of $10,000 to $30,000 or more per hour.
2. Productivity Decline
The maintenance talent shortage doesn't just affect equipment performance; it takes a toll on the existing workforce. As maintenance teams are stretched thin, the pressure to maintain operational continuity often leads to unsustainable workloads. This creates a dangerous cycle where overworked maintenance professionals face an increased risk of burnout, leading to higher turnover rates and further worsening the staffing shortage.
3. Safety & Compliance Risks
This not only puts employees at risk but also exposes businesses to serious compliance issues and potential regulatory penalties. The cost of a single safety incident can far outweigh any short-term savings from operating with reduced maintenance staff.
4. Recruitment & Retention Struggles
As the talent pool continues to shrink, businesses find themselves caught in an increasingly competitive battle to hire the right people. The basic economics of supply and demand are driving up salary requirements for skilled maintenance professionals, forcing organizations to either increase their labor costs or risk losing critical talent to competitors who can offer more attractive compensation packages.
The challenge extends beyond just competitive salaries. The outdated perception of maintenance work as a low-tech, limited-growth career path makes it particularly difficult to attract young professionals to the field. This recruitment challenge persists despite the reality that modern maintenance roles often involve sophisticated technology and offer significant career advancement opportunities.
How to Overcome Maintenance Talent Shortage
After examining the causes and significant business impacts of the maintenance talent shortage, one thing becomes crystal clear: organizations can't afford to be passive. The challenges demand proactive solutions. Let's explore practical, proven strategies that business leaders can implement to overcome the shortage.
1. Invest in Training and Upskilling Programs
Developing internal talent has become as vital as recruiting new professionals. Forward-thinking organizations are discovering that comprehensive training and upskilling programs offer a powerful solution to bridge the growing skills gap while building a more resilient workforce.
Partnerships with trade schools and technical colleges represent a key step in this direction. For existing employees, in-house training and certification programs provide a structured path to mastery of new technologies and maintenance techniques.
2. Leverage Technology to Enhance Efficiency
While the talent shortage presents significant challenges, it also creates opportunities for technological innovation. Implementing advanced Computerized Maintenance Management Systems (CMMS) enables organizations to optimize their maintenance operations and make more efficient use of their existing workforce.
Also, the integration of IoT sensors and automation technologies offers another powerful tool for addressing workforce limitations. AI-driven diagnostic tools further enhance this capability, helping less experienced technicians identify and resolve issues more quickly while reducing the burden on senior staff.
3. Improve Recruitment and Employer Branding
As competition for maintenance talent intensifies, organizations must rethink their approach to recruitment and employer branding. Success in attracting new talent requires more than competitive salaries—it demands a compelling narrative about career growth and technological innovation in maintenance roles.
This approach helps counter outdated perceptions of maintenance work and appeals to tech-savvy younger professionals. Combining this with clear career advancement pathways and competitive benefits packages creates a powerful recruitment message that resonates with potential candidates.
Companies should take steps to get positive reviews from existing employees on websites like Indeed, Glassdoor, Workopolis, and LinkedIn to improve their brand image and reputation as a great place to be employed.
4. Retain Talent through Employee Engagement
Addressing the talent shortage isn't just about bringing in new workers – it's equally important to retain existing talent. Successful organizations are implementing comprehensive engagement strategies that go beyond traditional retention tools. Career development paths that include leadership training opportunities show employees they have a future with the organization, while recognition programs and performance incentives help maintain motivation and job satisfaction.
Companies should work towards creating a supportive, team-oriented culture. This positive environment can create a virtuous cycle, making it easier to attract new talent through employee referrals and positive word-of-mouth.
5. Consider Outsourcing and Contracted Maintenance Services
As organizations grapple with persistent talent shortages, many are finding success with hybrid workforce models that combine in-house teams with external resources. Strategic outsourcing of specialized maintenance tasks to third-party providers can help organizations maintain operational efficiency without overtaxing their core maintenance team. When implemented thoughtfully, these hybrid models can create more sustainable and resilient maintenance operations. Check out our article on Maintenance as a Service (MaaS), which has been gaining a lot of traction over the past few years.
Conclusion
The maintenance talent shortage is one of the most pressing challenges facing industry leaders today. With a projected global talent deficit of over 85 million skilled workers by 2030 and companies losing anywhere from $10,000 to $300,000 per hour due to equipment downtime, the financial implications of inaction are staggering.
However, forward-thinking organizations have proven that this challenge isn't insurmountable. By implementing comprehensive strategies—from robust training programs and adopting technological solutions like CMMS to improved recruitment practices and hybrid workforce models—businesses can build resilient maintenance operations for the future.
The question isn't whether to implement these strategies but rather how quickly they can be implemented to secure your organization's operational future.
TABLE OF CONTENTS
Keep Reading
Last month, news outlets and the entire internet was abuzz with the return of NASA astronauts ...
3 Apr 2025
What comes first - CMMS or predictive maintenance? If your answer is either, it is correct. ...
28 Mar 2025
Artificial intelligence (AI) talk has become commonplace. Today, engaging in business-focused ...
27 Mar 2025
Imagine a world where machines predict, diagnose, and fix their issues before they fail. This ...
25 Mar 2025
A facility maintenance plan is at the core of a facility’s operations. This organized ...
21 Mar 2025
Think of managing your maintenance operations like managing a championship sports team. Just ...
21 Mar 2025
Manufacturing maintenance is the backbone of industrial efficiency, ensuring machines run ...
5 Mar 2025
No one likes playing a guessing game when equipment breaks down. Yet, maintenance teams often ...
4 Mar 2025
The size of the preventive maintenance software market is discussed in millions of dollars, ...
4 Mar 2025
The organizational structure and corporate hierarchy vary from company to company. Large ...
28 Feb 2025
Maintenance procedures are essential for ensuring the longevity and reliability of machinery ...
21 Feb 2025
Sustainability is no longer just a buzzword; it's a critical component of corporate social ...
20 Feb 2025
A Computerized Maintenance Management System (CMMS) relies on accurate, well-organized data ...
18 Feb 2025
In an era where technology drives operational efficiency, Computerized Maintenance Management ...
14 Feb 2025
A Computerized Maintenance Management System (CMMS) is a key component of modern maintenance ...
13 Feb 2025
Introduction Maintenance management is the foundation of maintenance operations in industries ...
11 Feb 2025
Introduction A Computerized Maintenance Management System (CMMS) is software designed to help ...
7 Feb 2025
Introduction Due to a growing awareness of the need to combat climate change, the green ...
6 Feb 2025
When your organization decides to invest in a CMMS (Computerized Maintenance Management ...
4 Feb 2025
Introduction Selecting the right Computerized Maintenance Management System (CMMS) is a ...
31 Jan 2025