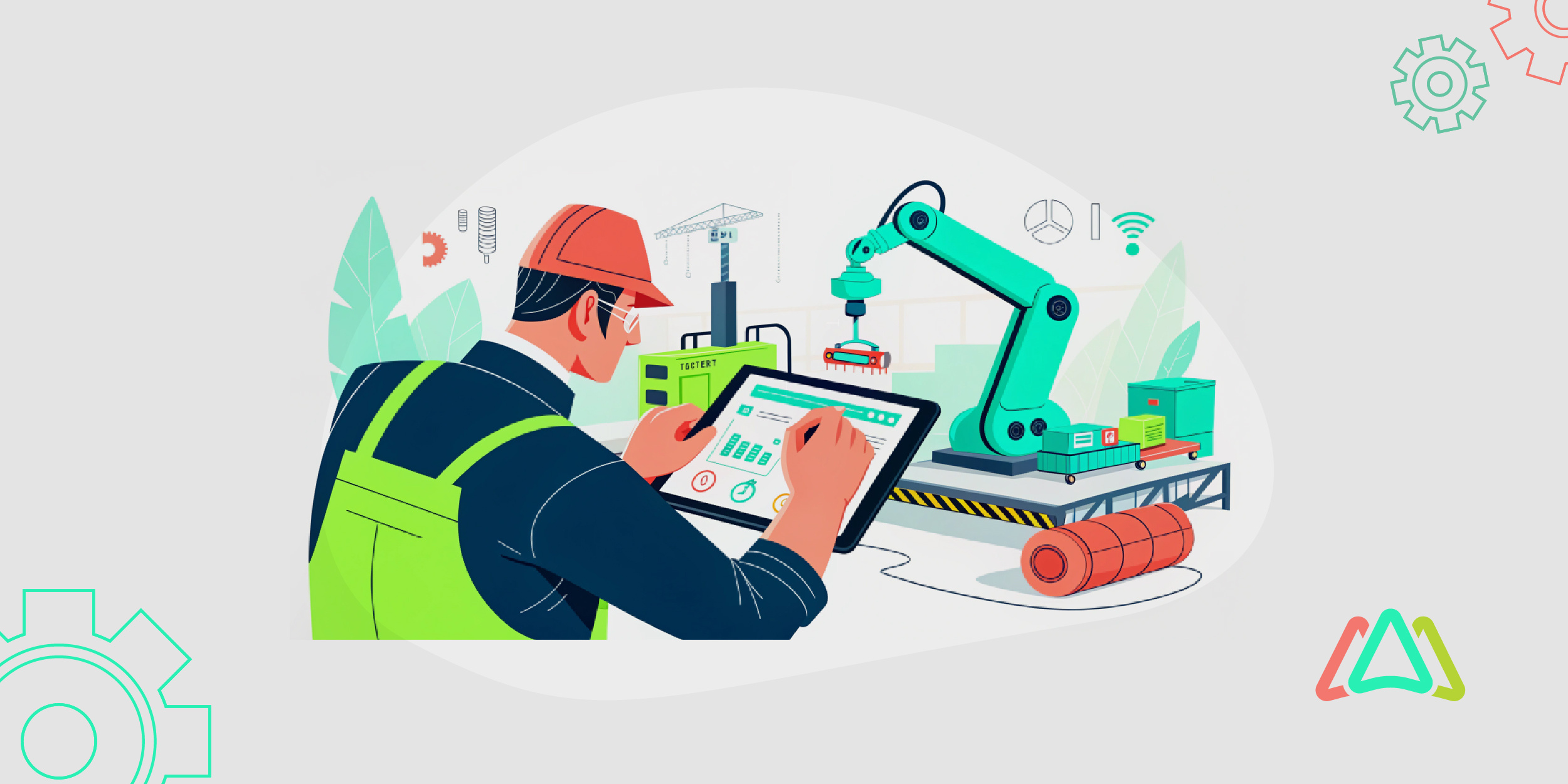
The 5 Best CMMS Products for Small Manufacturers
Computerized Maintenance Software Systems (CMMS) entered the marketplace during the 1960s, offering companies a way to streamline their maintenance operations using a centralized platform to plan, schedule, and track maintenance activities. When they were first introduced, CMMSs were recognized as a tool that helped maintenance managers conduct routine maintenance tasks more efficiently and track maintenance activities on critical assets.
Back then, the available CMMS solutions were primarily geared toward larger organizations with many assets, employees, and challenging workflows. The problem is that businesses come in all shapes and sizes and industry sectors. And no two organizations are alike. Because of that, there is no one-size-fits-all solution for managing maintenance operations. Over the past few decades, CMMS providers recognized this gap in the market. They began developing solutions to meet the unique needs of organizations of all sizes with differing operational needs.
Today’s CMMSs embrace adaptability by addressing the maintenance management needs across the board. Various CMMS products are well-suited for SMBs with their ability to provide streamlined solutions tailored to smaller-scale operations' specific challenges and requirements. These maintenance management software products aren’t just suited for smaller enterprises and are designed to scale. When organizations experience growth, today’s CMMSs can accommodate businesses’ changing needs by offering enterprise functionality within the same application if and when needed.
Here, we’ll zero in on five CMMS products suited explicitly for small manufacturing companies' needs.
Small Manufacturers’ Maintenance Needs
Small manufacturing organizations are typically described as organizations that produce goods on a smaller scale, most often with limited resources and a more localized market focus than larger manufacturing enterprises. To provide a context while also understanding that small manufacturing organizations can vary widely in size, according to the U.S. Small Business Administration (SBA) definition, a small manufacturing company is considered to have fewer than 500 employees. Nevertheless, smaller companies often operate with a more compact team to reflect their scale and focus on specialized production than large manufacturing companies. Specifically, small manufacturers have smaller teams, less complex workflows, fewer assets, and stocked inventory. Given these factors, they don’t require the same robust functionality that larger enterprise global manufacturers require. Instead, they need solutions that help manage work orders, preventive maintenance, inspections, assets, and light inventory.
Small manufacturers often face several challenges. For example, they need more resources in terms of budget and personnel, which can impact their ability to implement sophisticated maintenance strategies. They also rely more on reactive maintenance, addressing issues arising due to limited resources for preventive maintenance. While cost-effective up front, this strategy does not offer the long-term benefits of production efficiency or enhanced equipment lifespan.
While small manufacturers have to deal with these constraints, there are CMMSs explicitly designed to meet their needs because vendors recognize that their maintenance operations are just as crucial as those of their larger counterparts. The bottom line is that small manufacturers, like larger companies, need to ensure the efficient functioning of production equipment and facilities.
Small manufacturers’ needs encompass the following:
- Preventive maintenance to avoid unexpected breakdowns
- Routine inspections to identify and address potential issues
- Timely repairs to minimize downtime
- Cost-effective maintenance solutions that align with their budget constraints, making efficient and reliable equipment upkeep essential for sustained productivity and competitiveness in their respective markets
The Solution for Small Manufacturers
For small manufacturers grappling with limited resources, many CMMS vendors offer scaled-down and lower-cost options. These systems are designed to be user-friendly, ensuring smaller teams with potentially fewer technical experts can quickly implement and navigate them. CMMSs for small organizations often focus on essential functionalities, emphasizing simplicity and efficiency. While more prominent manufacturers may leverage CMMS for intricate predictive maintenance and sophisticated analytics, those designed for small organizations prioritize core features like work order management, preventive maintenance scheduling, asset management, and inventory control.
CMMS Vendors Best Suited for Small Manufacturing Organizations
In keeping with the idea that one size doesn’t fit all, several CMMS vendors offer solutions for small manufacturing organizations. The following are five CMMS software products that are well-suited for small manufacturing businesses.
Click Maint
Look no further if you want ease of use, affordability, and fast and easy implementation. Click Maint is a simple CMMS with an intuitive interface, ensuring users can navigate the system effortlessly, promoting quick adoption, and reducing training time. There's no need to fumble around figuring things out. It’s right there. At the same time, the platform's commitment to user-friendliness doesn't compromise its functionality, making it an ideal choice for small manufacturers seeking a powerful yet accessible maintenance management solution.
What sets Click Maint apart is the ease of use, simple setup, affordability, and speed to value. The leadership team has 40 years of experience in facilities, asset management, and CMMS technology. With seasoned professionals at the helm, Click Maint brings a wealth of knowledge and understanding of maintenance challenges across various industries, ensuring the software is finely tuned to meet the specific needs of diverse businesses.
Click Maint offers users all the key features needed to streamline maintenance operations. Software features include a request portal, work orders, preventive maintenance, asset and parts management, vendor management, reports and KPIs, and a user-friendly mobile app. Click Maint offers affordability, making it an accessible solution for organizations of all sizes. The ease of adoption further solidifies Click Maint as a top choice for small manufacturers seeking a powerful, easy-to-use CMMS that's affordable.
Pricing:
Pricing is always a consideration for small manufacturing organizations, and Click Maint meets that challenge. Click Maint costs only USD 35/month per user. Pricing is straightforward and includes the following features: request and work order management, preventive maintenance, asset and inventory management, reports, and KPIs. This price includes access to the mobile app and API for integrating with other applications.
Pros:
Click Maint offers excellent value for small manufacturers. Click Maint should be considered if you are looking for an easy-to-use CMMS that is affordable and easy to implement. If you’re struggling with tracking work orders, requests, and preventive maintenance and need something simple and inexpensive, Click Maint is an excellent solution. Click Maint’s support team focuses on ensuring user adoption and speed to value.
Cons:
Click Maint is geared toward small to medium-sized businesses (SMB) and mid-market organizations. Enterprise features like condition-based monitoring, multi-language, tool crib, global support, and 21 CFR compliance are currently unavailable.
Upkeep
Upkeep Technologies was founded in 2014 by Ryan Chan in Los Angeles, California. They were the first CMMS that started as an exclusive mobile app geared toward enabling technicians to manage work and tasks easily. Upkeep quickly expanded its capabilities to run on desktops and cater to mid and enterprise-sized businesses. There are currently over 4,000 businesses using Upkeep.
Upkeep exceeded standard CMMSs and developed its capabilities, positioning itself as an EAM (Enterprise Asset Management) and APM (Asset Performance Management) platform. Aside from standard CMMS features (work orders, PMs assets, and inventory), Upkeep offers Asset Optimization Capabilities with enhanced reporting and analytics, predictive maintenance, condition monitoring, and more. These advanced features allow asset managers to predict potential failures and monitor asset health and lifecycle.
Pricing:
Upkeep offers four plans based on the complexity and size of the maintenance operation; pricing ranges from USD 20/month to USD 75/month for the Lite and Professional Plans. For pricing info on Upkeep’s Business Plus (Enterprise) plan, it’s best to speak to their sales team. Upkeep’s Data Hub and Edge (IoT) Remote Condition Monitoring are available add-ons to the user subscription fees.
Pros:
Upkeep has all the features required to manage small and large operations. They are at the forefront of developing complete asset management software that improves MRO. Compared to other robust enterprise software, Upkeep is intuitive and user-friendly. The mobile app is full-featured and very intuitive.
Cons:
Although Upkeep offers a Lite version of its software and a low-cost onboarding option, its software might be too expensive for some small businesses. The Lite version does not allow users to track requests, labor, costs, and parts. This is only a viable option for some maintenance operations. The Starter plan at USD 45/month per user has quite a bit of functionality, but maintenance history reports are limited to the last 30 days. Reports beyond the previous 30 days are only available in the Professional plan, costing USD 75/month per user. Organizations looking to manage work orders, track costs, and run complete maintenance history reports will require the Professional Plan at USD 75/user per month. If integrations or SSO are needed, the Business Plus plan is required and comes at a higher price tag.
Fiix
Fiix CMMS was founded in 2008 and is located in Toronto, Canada. Initially, they entered the CMMS market as Maintenance Assistant and rebranded as Fiix in 2016. In 2017, Rockwell Automation acquired Fiix. Fiix has approximately 4,000 customers.
Fiix comes with all the standard features in a CMMS: work order management, preventive maintenance, asset and inventory management, KPIs and reports, API for integrations, and a full-featured mobile app. Fiix goes beyond many other CMMS platforms by offering more predictive capabilities. They are investing in leveraging AI and IoT technology and have developed Asset Risk Predictor and Fiix Foresight. This is an exceptional value for organizations that require this level of sophistication. In addition, they have an Integrations Hub that makes it easier for larger enterprises to integrate their CMMS and workflows into ERPs, CRM, and other business platforms.
Fiix is well-suited for oil and gas, energy, construction, transportation, and manufacturing industrial businesses. They offer enhanced capabilities suitable for enterprise global operations but can also be used by more mid-market organizations with more complex processes.
Pricing:
Fiix offers four plans based on the complexity and size of an organization’s maintenance operations. Aside from the free option that serves primarily as a trial, pricing ranges from USD 45/month to USD 75/month for the Basic and Professional Plans. For pricing info on Fiix’s Enterprise plan, it’s best to speak to their sales team.
Pros:
Fiix has a long history of delivering powerful maintenance management software. They are easy to do business with, allowing businesses to purchase directly through their website. They are at the forefront of developing CMMS capabilities incorporating AI and predictive analytics. Fiix is well-suited for industrial operations. Fiix’s price point is very competitive, given the functionality included in each plan.
Cons:
Fiix may be overly complex for smaller operations that require a more cost-effective and straightforward solution for tracking maintenance requests, work orders, PMs, and assets. The user interface appears to be lacking and may pose challenges for users who are not tech-savvy. Fiix is best suited for businesses focusing on industrial equipment and spare parts but less for facility maintenance.
Limble CMMS
Limble is located in Lehi, Utah, and was founded in 2015. Its software caters to all industries but is best suited for organizations for mid to large-size companies in manufacturing, food and beverage processing, oil and gas, and transportation. Small manufacturers should also check out Limble if they are snowballing and operating in highly regulated sectors. Limble’s deep feature capability and security and compliance measures allow small manufacturers to scale as they grow.
Limble CMMS comes with all the standard features you would expect in a CMMS: work order management, preventive maintenance, asset and inventory management, KPIs and reports, API for integrations, and a full-featured mobile app. Limble surpasses other CMMS platforms by offering predictive maintenance and condition monitoring. Limble can be integrated with IoT sensors, triggering alerts and tasks based on sensor data. For global operations, Limble supports multiple languages aside from English.
Pricing:
Limble offers four plans depending on the complexity and size of the maintenance operation. Aside from the Free Option that serves more as a trial, pricing ranges from USD 28/month to USD 69/month for the Standard and Premium Plans. For pricing info on Limble’s Enterprise plan, it’s best to speak directly to their sales team.
Pros:
At its mid-priced level (Premium), USD 69/month per user, Limble offers robust features, including those designed for preventive maintenance. Limble can meet the needs of enterprise-sized businesses with multi-language, 21 CFR Compliance, SSO, and predictive maintenance and, at the same time, has a great UI and appears easy to use compared to other enterprise CMMS.
Cons:
Limble can be expensive for smaller operations like manufacturers. The Basic and Starter plans need more functionality to effectively manage work orders and preventive maintenance. These plans do not include the ability to track costs, parts, and inventory, and reports are limited to 3 months. Most small manufacturers will have to pay USD 69/month per user to use the most beneficial features of the CMMS.
Conclusion
For small manufacturing companies looking to invest in a CMMS, the bottom line is finding a solution that offers improved operational efficiency, reduced downtime, and enhanced maintenance management at a price you can afford. Small manufacturing companies looking for a CMMS that aligns with their budget constraints can take several steps to find a suitable solution.
- Conduct thorough research to identify CMMS providers that cater specifically to their type of organization or offer scalable pricing models. The five CMMS providers covered in this article should be considered.
- Explore cloud-based CMMS options as they are cost-effective. They eliminate the need for extensive hardware investments and IT support and are faster to implement.
- Seek out free trials and demos to assess the functionality and compatibility of the CMMS with operation needs before committing.
- Compare pricing structures, including subscription fees and implementation fees, and potential costs for higher-level customer support.
- Seek recommendations from industry peers or look at online reviews. These resources provide insights into the performance and reliability of different CMMS options.
Ultimately, by balancing functionality with budget considerations, small manufacturing companies can make informed decisions that contribute to improved operational efficiency without exceeding financial constraints.
TABLE OF CONTENTS
Keep Reading
Ever find yourself checking into a luxury hotel and expecting a relaxing stay, only to find a ...
11 Apr 2025
Organizations are witnessing swift changes in the business environment and confronting a ...
8 Apr 2025
Last month, news outlets and the entire internet was abuzz with the return of NASA astronauts ...
3 Apr 2025
What comes first - CMMS or predictive maintenance? If your answer is either, it is correct. ...
28 Mar 2025
Artificial intelligence (AI) talk has become commonplace. Today, engaging in business-focused ...
27 Mar 2025
Imagine a world where machines predict, diagnose, and fix their issues before they fail. This ...
25 Mar 2025
A facility maintenance plan is at the core of a facility’s operations. This organized ...
21 Mar 2025
Think of managing your maintenance operations like managing a championship sports team. Just ...
21 Mar 2025
The maintenance sector is battling a severe talent shortage that threatens to undermine ...
7 Mar 2025
Manufacturing maintenance is the backbone of industrial efficiency, ensuring machines run ...
5 Mar 2025
No one likes playing a guessing game when equipment breaks down. Yet, maintenance teams often ...
4 Mar 2025
The size of the preventive maintenance software market is discussed in millions of dollars, ...
4 Mar 2025
The organizational structure and corporate hierarchy vary from company to company. Large ...
28 Feb 2025
Maintenance procedures are essential for ensuring the longevity and reliability of machinery ...
21 Feb 2025
Sustainability is no longer just a buzzword; it's a critical component of corporate social ...
20 Feb 2025
A Computerized Maintenance Management System (CMMS) relies on accurate, well-organized data ...
18 Feb 2025
In an era where technology drives operational efficiency, Computerized Maintenance Management ...
14 Feb 2025
A Computerized Maintenance Management System (CMMS) is a key component of modern maintenance ...
13 Feb 2025
Introduction Maintenance management is the foundation of maintenance operations in industries ...
11 Feb 2025
Introduction A Computerized Maintenance Management System (CMMS) is software designed to help ...
7 Feb 2025