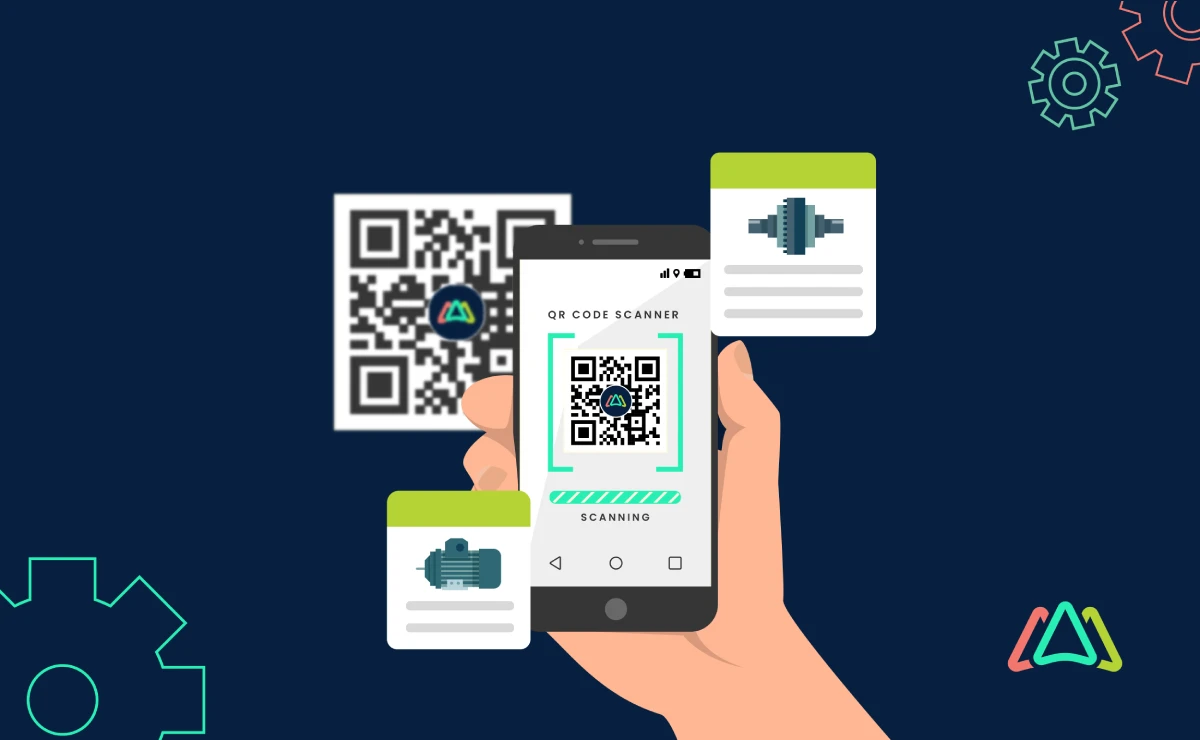
Integrating QR Codes with CMMS Software to Drive Maintenance Efficiency
Asset and inventory management are critical components of maintenance operations, enabling businesses to maintain visibility and control over their equipment and spare parts. Effective asset management involves tracking and monitoring the performance, condition, and lifecycle of assets throughout their lifespan. Inventory management ensures the availability of spare parts and supplies required for maintenance activities while minimizing inventory carrying costs and stockouts. By implementing effective asset and inventory management practices, businesses can enhance equipment reliability, reduce maintenance costs, and improve operational efficiency.
A Computerized Maintenance Management System (CMMS) helps with asset and inventory management by facilitating the centralization of maintenance data, including work orders, asset information, preventive maintenance schedules, and maintenance history, within a single platform. CMMS software enables maintenance managers to track maintenance activities, prioritize tasks, allocate resources efficiently, and generate actionable insights to optimize maintenance processes.
Mobile CMMS extends the functionality of traditional CMMS software to mobile devices, enabling maintenance technicians and managers to access maintenance data, update work orders, and perform inspections in the field. Mobile CMMS offers several benefits, including increased flexibility, real-time data access, improved communication, and enhanced productivity. Mobile CMMS users can receive work orders, access asset information, record maintenance activities, and capture asset data directly from their smartphones or tablets, regardless of their location. Furthermore, CMMS mobile apps have the advantage of additional capabilities not available on desktop CMMS software; capturing photos, GPS, voice-to-text, push notifications, offline mode, and QR and Barcode scanning. Mobile maintenance apps empower maintenance teams to respond quickly to maintenance requests, streamline workflow processes, and make informed decisions on the go.
The integration of Barcodes and Quick Response (QR) codes with CMMS software has the advantage of streamlining asset identification, tracking, and data capture processes. Barcodes consist of a series of parallel lines representing data encoded in a machine-readable format. QR codes are two-dimensional barcodes capable of storing more information, including URLs, text, or contact details. By affixing barcodes or QR codes to assets, equipment, or inventory items, maintenance personnel can quickly access relevant information, update maintenance records, and perform asset-related tasks using mobile devices or barcode scanners.
What are Barcodes (1D)?
Barcodes are linear symbols composed of parallel lines of varying widths that represent data in a machine-readable format. Common types of 1D barcodes include UPC (Universal Product Code), Code 39, Code 128, and EAN (European Article Numbering). Barcodes are primarily used for encoding product information, such as item numbers, serial numbers, and batch numbers.
What are QR Codes (2D)?
QR codes, or Quick Response codes, are two-dimensional symbols that can store significantly more data than traditional barcodes. QR codes consist of square patterns arranged in a grid, allowing them to encode alphanumeric text, URLs, contact information, and other types of data. QR codes are capable of storing up to several hundred times more information than 1D barcodes, making them versatile tools for various applications, including marketing, authentication, and maintenance management.
How Barcodes and QR Codes Differ in Maintenance Management
In maintenance management, barcodes and QR codes serve similar purposes but differ in their capabilities and applications:
Barcodes
Barcodes are suitable for encoding basic information, such as asset numbers or inventory identifiers. They are widely used for asset tagging, inventory tracking, and product identification in maintenance operations. Barcodes offer simplicity and cost-effectiveness, making them ideal for applications where limited data storage is sufficient.
QR Codes
QR codes provide enhanced data storage capabilities and versatility compared to barcodes. In maintenance management, QR codes can store additional information, such as equipment manuals, maintenance history, inspection records, and instructional videos. QR codes offer greater flexibility and functionality, allowing maintenance personnel to access comprehensive asset information and perform tasks more efficiently.
Advantages and Disadvantages of Using Barcodes and QR Codes for Asset and Inventory Tracking
Advantages of Barcodes
- Simplicity: Barcodes are straightforward to generate, print, and scan, requiring minimal training for users.
- Cost-Effective: Barcodes are cost-effective solutions for asset and inventory tracking, as they do not require specialized equipment or software.
- Universal Compatibility: Barcodes can be read by standard barcode scanners, making them compatible with existing scanning infrastructure.
Disadvantages of Barcodes
- Limited Data Storage: Barcodes have limited data storage capacity compared to QR codes, restricting the amount of information that can be encoded.
- Readability Issues: Barcodes may encounter readability issues due to damage, smudging, or poor printing quality, leading to errors in data capture.
Advantages of QR Codes
- Enhanced Data Storage: QR codes can store significantly more information than barcodes, including URLs, text, and multimedia content.
- Versatility: QR codes offer versatility in content types, allowing maintenance personnel to access detailed asset information, maintenance records, and multimedia resources.
- Dynamic Content: QR codes can contain dynamic content that can be updated or modified remotely, ensuring real-time access to the latest information.
Disadvantages of QR Codes
- Complexity: QR codes may require specialized software or equipment for generation and scanning, adding complexity to implementation and maintenance.
- Printing Limitations: QR codes may be less suitable for small or densely packed labels due to their larger size and complexity.
Comparison between Manual Documentation and Barcode/QR Code-Based Tracking
Accurate documentation is essential in maintenance management to ensure the reliability and safety of equipment. Implementing barcode and QR code-based tracking systems can significantly reduce documentation errors compared to manual methods.
Manual Documentation |
Barcode/QR Code-Based Tracking |
Relies on handwritten records, spreadsheets, or paper-based systems. |
Utilizes barcode or QR code labels affixed to assets, equipment, or inventory items. |
Prone to human errors such as illegible handwriting, data entry mistakes, and misplaced or lost documents. |
Enables automated data capture using barcode scanners or mobile devices equipped with camera capabilities. |
Time-consuming and labor-intensive, requiring manual data entry and verification. |
Provides instant access to asset information, maintenance history, and related documentation. |
Limited accessibility and visibility, making it challenging to track and update information in real time. |
Enhances accuracy and efficiency by eliminating manual data entry errors and streamlining documentation processes. |
Facilitates real-time updates and tracking of maintenance activities, ensuring data accuracy and completeness. |
Potential Errors in Manual Documentation and How Barcodes/QR Codes Mitigate Them
Scenario 1: Illegible Handwriting
- In a manual documentation scenario, maintenance technicians may struggle to decipher handwritten notes or records, leading to misinterpretation and errors.
- With barcode or QR code-based tracking, asset information is encoded in a machine-readable format, eliminating the risk of illegible handwriting and ensuring accurate data capture.
Scenario 2: Data Entry Mistakes
- Human errors during manual data entry, such as typos or transposed digits, can result in inaccuracies in maintenance records and inventory counts.
- Barcode or QR code scanning automates data capture, minimizing the risk of data entry mistakes and ensuring the integrity of documentation.
Scenario 3: Lost or Misplaced Documents
- Paper-based documentation systems are susceptible to document loss, misplacement, or damage, leading to gaps in maintenance records.
- Barcodes or QR codes provide a digital record of asset information and maintenance history, accessible from centralized databases or cloud-based systems, eliminating the risk of document loss or misplacement.
Benefits of Real-Time Data Capture and Accuracy in Maintenance Tasks
Improved Decision-Making
Real-time data capture enables maintenance managers to make informed decisions based on accurate and up-to-date information, minimizing the risk of downtime and optimizing resource allocation.
Enhanced Compliance
Accurate documentation ensures compliance with regulatory requirements and industry standards, reducing the risk of penalties or legal liabilities associated with non-compliance.
Increased Efficiency
Barcode and QR code-based tracking streamline maintenance processes, reducing administrative overhead and enabling maintenance personnel to focus on core tasks, ultimately improving operational efficiency.
Enhanced Asset Management
Real-time visibility into asset information and maintenance activities enables proactive asset management, extending equipment lifespan and maximizing return on investment.
The adoption of QR code-based tracking systems offers significant advantages over manual documentation methods, including improved accuracy, efficiency, and real-time data capture capabilities. By mitigating potential errors and providing instant access to accurate information, these technologies enhance the reliability and effectiveness of maintenance operations.
How CMMS Software Using QR Codes Facilitates Centralized Asset and Inventory Tracking
Barcode Integration
CMMS software integrated with QR code functionality allows assets and inventory items to be tagged with unique barcodes, enabling easy identification and tracking.
Real-Time Updates
QR code scanning capabilities enable real-time updates to asset and inventory records, ensuring data accuracy and completeness across the organization.
Mobile Accessibility
With mobile CMMS applications, maintenance technicians can scan QR codes using smartphones or tablets, capturing asset data and updating maintenance records on the go.
Centralized Database
CMMS software serves as a centralized database for storing asset information, maintenance history, and inventory levels, providing a single source of truth for maintenance data.
Advantages of Using Barcodes and QR Codes in Mobile CMMS Applications
Efficient Data Capture
QR code scanning enables quick and accurate data capture, allowing maintenance technicians to access asset information, update maintenance records, and perform tasks with ease.
Real-Time Updates
Mobile CMMS applications equipped with QR code functionality facilitate real-time updates to asset and inventory records, ensuring data accuracy and completeness.
Improved Productivity
By streamlining data entry and retrieval processes, QR code scanning enhances productivity, enabling maintenance teams to complete tasks more efficiently and reduce downtime.
Better Accuracy
QR code scanning minimizes the risk of manual data entry errors, ensuring the integrity of maintenance records and improving overall data accuracy.
Features to Look for in Mobile CMMS Platforms for Barcode/QR Code Integration
Barcode/QR Code Scanning
Look for mobile CMMS platforms that offer built-in QR code scanning capabilities. These allow maintenance technicians to scan labels using the device's camera.
Offline Functionality
Choose a CMMS solution that supports offline functionality. This enables maintenance technicians to scan barcodes and update records even in environments with limited or no internet connectivity.
Customizable Forms
Ensure the mobile CMMS platform allows for customizable forms and fields. This will allow organizations to tailor data capture processes to their specific asset and maintenance tracking needs.
Integration with CMMS
Select a CMMS vendor that offers mobile CMMS features enabling data captured via barcode and QR code scanning to sync automatically with the centralized database.
Choosing Barcode and QR Code Labels
Importance of Selecting Durable Labels for Long-Term Use
- Asset Protection: Durable labels help protect assets and equipment by maintaining legibility and functionality over extended periods, even in harsh environments.
- Cost Savings: Investing in durable labels upfront can lead to long-term cost savings by reducing the frequency of label replacements and minimizing downtime associated with label failures.
- Data Integrity: Labels that withstand wear and tear ensure the integrity of encoded information, preventing data loss or errors that may occur due to label deterioration.
Factors to Consider When Choosing Barcode and QR Code Labels
- Material: Select labels made from durable materials such as polyester, vinyl, or polypropylene, which offer resistance to moisture, chemicals, UV exposure, and abrasion.
- Adhesive: Choose labels with strong adhesive properties to ensure they adhere securely to various surfaces, including metal, plastic, and textured materials.
- Size: Opt for labels of appropriate size and dimensions to accommodate barcode and QR code readability requirements without compromising label visibility or aesthetics.
Examples of Best Practices to Ensure Label Longevity and Prevent Wear and Tear
- Surface Preparation: Ensure surfaces are clean, dry, and free of debris before applying labels to promote adhesion and prevent premature label detachment.
- Proper Application: Apply labels carefully and evenly, avoiding wrinkles, bubbles, or misalignment, which can compromise adhesion and readability.
- Lamination: Consider laminating labels for added protection against moisture, chemicals, and physical damage, extending their lifespan in challenging environments.
- Regular Inspection: Implement a routine inspection schedule to check for signs of label deterioration, such as fading, peeling, or damage, and replace labels as needed to maintain data integrity.
- Temperature Control: Stick labels in controlled environments to prevent exposure to extreme temperatures, which can degrade label materials and adhesive properties over time.
QR Codes in Click Maint CMMS
In Click Maint CMMS, QR Codes offer the versatility to streamline maintenance operations and access essential information with ease. By tapping on the QR Code icon in the bottom menu bar, users can utilize their mobile camera to scan QR Codes and perform various actions seamlessly. Learn more here.
Here's what you can do with QR Codes in Click Maint CMMS
1. Create a Work Order
Scanning a QR Code associated with an asset or equipment enables you to create a work order for maintenance tasks instantly. Whether you're scheduling preventive maintenance, addressing equipment breakdowns, or conducting inspections, creating a work order becomes swift and straightforward with Click Maint CMMS. By linking QR Codes to specific maintenance activities, you ensure efficient task management and timely resolution of maintenance issues.
2. Create a Request
QR Codes can also be linked to maintenance request forms, allowing users to quickly submit service requests or report maintenance issues by scanning the QR Code associated with the relevant asset or location. Whether it's a repair request, equipment malfunction, or facility maintenance issue, creating a request via QR Code simplifies the process and facilitates prompt response from maintenance teams. With Click Maint CMMS, managing maintenance requests becomes more efficient and transparent, enhancing communication and collaboration between stakeholders.
3. View Details Screen Associated with a QR Code
Scanning a QR Code not only enables you to initiate maintenance tasks but also provides access to detailed information associated with the scanned asset or location. By tapping into the QR Code functionality, you can seamlessly navigate to the detail screen within Click Maint CMMS, where you can view asset specifications, maintenance history, work order status, and other relevant details. This instant access to asset information empowers maintenance technicians and managers to make informed decisions, prioritize tasks, and optimize maintenance workflows for enhanced efficiency and productivity.
Challenges and Solutions
Implementing barcode and QR code systems in CMMS can present various challenges, but with the right strategies and solutions, these hurdles can be overcome effectively.
1. Common Challenges in Barcode/QR Code Implementation in CMMS
Label Degradation
Over time, barcode and QR code labels may degrade due to exposure to environmental factors like moisture, chemicals, and UV radiation, compromising their readability.
Scanning Errors
Scanning errors, such as misreads or failed scans, can occur due to factors like label damage, poor printing quality, or scanner malfunction.
Compatibility Issues
Compatibility issues may arise when integrating barcode and QR code systems with existing CMMS platforms, resulting in data synchronization issues or functionality limitations.
B. Strategies to Address Challenges
Label Degradation
- Use Durable Materials: Select labels made from durable materials like polyester or vinyl, which offer resistance to moisture, chemicals, and UV exposure.
- Lamination: Apply a protective laminate over labels to enhance durability and prolong their lifespan, particularly in harsh environments.
- Regular Inspection: Implement routine inspections to check for signs of label degradation and replace worn or damaged labels promptly.
Scanning Errors
- Optimize Printing Quality: Ensure labels are printed with high-quality resolution and adequate contrast to enhance readability and minimize scanning errors.
- Scanner Maintenance: Regularly maintain and calibrate barcode scanners to ensure optimal performance and accuracy during scanning operations.
- Proper Label Placement: Affix labels to clean, flat surfaces and avoid obstructions or damage that may interfere with scanning.
Compatibility Issues
- Select Compatible Solutions: Choose barcode and QR code systems that are compatible with the organization's existing CMMS platform, or invest in CMMS software that offers built-in barcode integration capabilities.
- API Integration: Utilize application programming interfaces (APIs) to facilitate seamless integration between barcode/QR code systems and CMMS software, ensuring data synchronization and interoperability.
Tips for Troubleshooting Barcode/QR Code-Related Problems
- Verify Label Integrity: Check for label damage or degradation that may impede scanning and replace labels as needed.
- Adjust Scanning Settings: To optimize scan accuracy, experiment with scanner settings such as scanning distance, angle, and lighting conditions.
- Update Software/Firmware: Ensure QR code scanners and CMMS software are updated to the latest versions to access bug fixes, performance improvements, and compatibility enhancements.
- User Training: Provide maintenance personnel with training on proper scanning techniques, troubleshooting procedures, and best practices for using barcodes/QR codes in CMMS.
In conclusion, while implementing barcode and QR code systems in CMMS may pose challenges, proactive strategies and solutions can mitigate these obstacles effectively. By addressing issues related to label degradation, scanning errors, and compatibility concerns, organizations can optimize the functionality and reliability of barcode/QR code systems in CMMS, ultimately enhancing maintenance operations and driving operational excellence.
TABLE OF CONTENTS
- What are Barcodes (1D)?
- What are QR Codes (2D)?
- How Barcodes and QR Codes Differ in Maintenance Management
- Advantages and Disadvantages of Using Barcodes and QR Codes for Asset and Inventory Tracking
- Comparison between Manual Documentation and Barcode/QR Code-Based Tracking
- Benefits of Real-Time Data Capture and Accuracy in Maintenance Tasks
- How CMMS Software Using QR Codes Facilitates Centralized Asset and Inventory Tracking
- Advantages of Using Barcodes and QR Codes in Mobile CMMS Applications
- Features to Look for in Mobile CMMS Platforms for Barcode/QR Code Integration
- Choosing Barcode and QR Code Labels
- QR Codes in Click Maint CMMS
- Challenges and Solutions
- 1. Common Challenges in Barcode/QR Code Implementation in CMMS
- B. Strategies to Address Challenges
- Tips for Troubleshooting Barcode/QR Code-Related Problems
Keep Reading
Introduction Maintenance management is the foundation of maintenance operations in industries ...
11 Feb 2025
Introduction A Computerized Maintenance Management System (CMMS) is software designed to help ...
7 Feb 2025
Ever find yourself checking into a luxury hotel and expecting a relaxing stay, only to find a ...
11 Apr 2025
Organizations are witnessing swift changes in the business environment and confronting a ...
8 Apr 2025
Last month, news outlets and the entire internet was abuzz with the return of NASA astronauts ...
3 Apr 2025
What comes first - CMMS or predictive maintenance? If your answer is either, it is correct. ...
28 Mar 2025
Artificial intelligence (AI) talk has become commonplace. Today, engaging in business-focused ...
27 Mar 2025
Imagine a world where machines predict, diagnose, and fix their issues before they fail. This ...
25 Mar 2025
A facility maintenance plan is at the core of a facility’s operations. This organized ...
21 Mar 2025
Think of managing your maintenance operations like managing a championship sports team. Just ...
21 Mar 2025
The maintenance sector is battling a severe talent shortage that threatens to undermine ...
7 Mar 2025
Manufacturing maintenance is the backbone of industrial efficiency, ensuring machines run ...
5 Mar 2025
No one likes playing a guessing game when equipment breaks down. Yet, maintenance teams often ...
4 Mar 2025
The size of the preventive maintenance software market is discussed in millions of dollars, ...
4 Mar 2025
The organizational structure and corporate hierarchy vary from company to company. Large ...
28 Feb 2025
Maintenance procedures are essential for ensuring the longevity and reliability of machinery ...
21 Feb 2025
Sustainability is no longer just a buzzword; it's a critical component of corporate social ...
20 Feb 2025
A Computerized Maintenance Management System (CMMS) relies on accurate, well-organized data ...
18 Feb 2025
In an era where technology drives operational efficiency, Computerized Maintenance Management ...
14 Feb 2025
A Computerized Maintenance Management System (CMMS) is a key component of modern maintenance ...
13 Feb 2025
Introduction Maintenance management is the foundation of maintenance operations in industries ...
11 Feb 2025
Introduction A Computerized Maintenance Management System (CMMS) is software designed to help ...
7 Feb 2025
Ever find yourself checking into a luxury hotel and expecting a relaxing stay, only to find a ...
11 Apr 2025
Organizations are witnessing swift changes in the business environment and confronting a ...
8 Apr 2025
Last month, news outlets and the entire internet was abuzz with the return of NASA astronauts ...
3 Apr 2025
What comes first - CMMS or predictive maintenance? If your answer is either, it is correct. ...
28 Mar 2025
Artificial intelligence (AI) talk has become commonplace. Today, engaging in business-focused ...
27 Mar 2025
Imagine a world where machines predict, diagnose, and fix their issues before they fail. This ...
25 Mar 2025
A facility maintenance plan is at the core of a facility’s operations. This organized ...
21 Mar 2025
Think of managing your maintenance operations like managing a championship sports team. Just ...
21 Mar 2025
The maintenance sector is battling a severe talent shortage that threatens to undermine ...
7 Mar 2025
Manufacturing maintenance is the backbone of industrial efficiency, ensuring machines run ...
5 Mar 2025
No one likes playing a guessing game when equipment breaks down. Yet, maintenance teams often ...
4 Mar 2025
The size of the preventive maintenance software market is discussed in millions of dollars, ...
4 Mar 2025
The organizational structure and corporate hierarchy vary from company to company. Large ...
28 Feb 2025
Maintenance procedures are essential for ensuring the longevity and reliability of machinery ...
21 Feb 2025
Sustainability is no longer just a buzzword; it's a critical component of corporate social ...
20 Feb 2025
A Computerized Maintenance Management System (CMMS) relies on accurate, well-organized data ...
18 Feb 2025
In an era where technology drives operational efficiency, Computerized Maintenance Management ...
14 Feb 2025
A Computerized Maintenance Management System (CMMS) is a key component of modern maintenance ...
13 Feb 2025
Introduction Maintenance management is the foundation of maintenance operations in industries ...
11 Feb 2025
Introduction A Computerized Maintenance Management System (CMMS) is software designed to help ...
7 Feb 2025