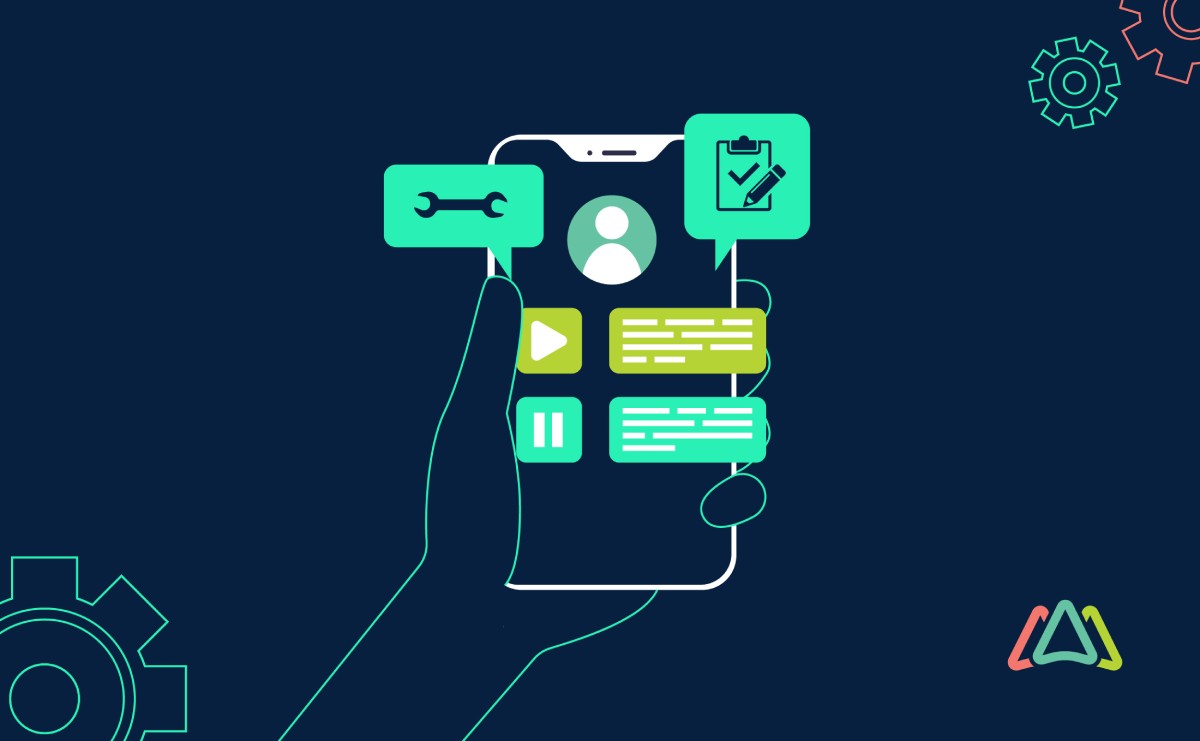
Work Order Apps: Optimizing Maintenance Operations
Effective work order management is essential for businesses across industry sectors, ranging from manufacturing and construction to facilities management and service-oriented sectors. Work order apps have emerged as powerful tools that streamline and optimize the entire work order process regardless of the industry.
Work order apps are software applications designed to digitize and automate the creation, tracking, and management of work orders. These apps provide a centralized platform ensuring that tasks are completed promptly and efficiently. Work order apps often come with features such as real-time updates, notifications, analytics, and integration capabilities, thus enhancing productivity and collaboration within organizations.
Key Features and Benefits of Work Order Apps
Work order apps are indispensable tools for businesses striving to improve efficiency, collaboration, and overall productivity. Organizations can optimize their work order processes and achieve better outcomes in their daily operations by leveraging the features offered by these applications.
Work Order Creation and Tracking
Work order apps provide intuitive interfaces where users can easily generate detailed work orders, including information such as task descriptions, priority levels, assigned personnel, and due dates. By centralizing these data, work order apps enable seamless tracking of work progress, ensuring that tasks are completed on time and with nothing falling through the cracks.
Real-Time Updates and Notifications
Work order apps keep all relevant parties informed about the status of work orders. Through push notifications or email alerts, users receive instant updates whenever there are changes in task assignments, completion status, or any other relevant information. This feature enhances communication and collaboration, allowing teams to adapt quickly to changing circumstances and make timely data-driven decisions.
Integration with other Business Systems
Work order apps often offer integration capabilities, allowing them to connect with other essential business systems. This integration can include customer relationship management (CRM) software, asset management systems, inventory management tools, and more. By integrating work order apps with existing systems, businesses can synchronize data, streamline processes, and avoid redundant data entry. This seamless integration enhances overall operational efficiency and reduces the chance of errors.
Automation and Efficiency Improvements
Work order apps automate various aspects of work order management, such as task assignment, scheduling, and reminders. By reducing manual effort and human error, automation frees up valuable time for employees to focus on more critical and strategic activities during their workday.
Data Analytics and Reporting Capabilities
Work order apps often come equipped with robust data analytics and reporting features. These capabilities enable businesses to gain valuable insights into their work order processes, performance metrics, and resource utilization. With customizable dashboards and reports, organizations can track key performance indicators (KPIs), identify bottlenecks in operations, and make decisions that optimize their work order management.
It’s important to note that there is a difference between a work order app and work order software. Understanding this difference is crucial for organizations as they navigate the decision-making process when selecting the most suitable solution for their specific business needs.
Differences between Work Order Apps & Work Order Software
A work order app and work order software are similar in that they both serve the purpose of managing work orders efficiently. However, there are some key differences between the two as shown below.
Work Order Apps |
Work Order Software |
|
Platform |
Mobile devices (smartphones, tablets) |
Web-based (desktop, laptop) |
Mobility |
Optimized for mobile environments |
May not offer the same level of mobile optimization |
User Interface |
Mobile-friendly, touch controls, simplified navigation |
Comprehensive interface with additional functionalities |
Accessibility |
Download from app stores and install on devices |
Accessed through web browsers from any device with internet connectivity |
Integration |
Limited integration options, may focus on specific mobile features |
Extensive integration capabilities with other business systems |
Scalability |
Suitable for smaller to medium-sized organizations |
Designed for larger organizations with complex workflows |
Customization |
Limited customization capabilities |
Offers a higher degree of customization options |
When deciding between a work order app and work order software, organizations should consider their organization’s size, growth stage, and specific operational requirements.
Tips for Selecting the Best Work Order App for Your Business
Identify Your Business Requirements
Consider the unique aspects of your organization's work order management needs, such as the volume of work orders, complexity of tasks, team size, and any industry-specific requirements. By having a clear understanding of your requirements, you can effectively evaluate work order apps that align with your business goals.
Evaluate Key Features and Functionality
Prioritize the features that are most critical to your organization and compare different apps based on their offerings. Some crucial features to consider include work order creation and tracking, real-time updates, task assignment capabilities, mobile accessibility, integration with other systems, reporting and analytics, and customizable workflows.
Consider User Interface and Ease of Use
Consider the app's usability, navigation, and overall user experience. Look for an app that offers a clean and intuitive design, clear workflows, and easily accessible features.
Click Maint’s interface is built to improve user adoption through an intuitive user interface.
Additionally, consider whether the app provides training or user support resources to help your employees get up to speed quickly and access assistance, if needed.
Pricing Models and Budget Considerations
Some apps may charge a flat rate, while others may have a subscription-based model or offer tiered pricing based on the number of users or features. Take into account any additional costs, such as implementation, customization, or ongoing support. Consider the scalability of the app as well, especially if your business is expected to grow in the future.
Read Reviews and Seek Recommendations
Look for reviews from businesses similar to yours and pay attention to feedback regarding ease of use, customer support, reliability, and overall satisfaction. Engage with industry communities, forums, or professional networks to seek recommendations from peers who have firsthand experience with work order apps.
List of Work Order Apps to Choose from
App Provider |
Key Features |
Apple App Store Rating |
Google Play Rating |
---|---|---|---|
Fiix (Rockwell) |
|
4.3/5 |
3.1/5 |
UpKeep |
|
4/5 |
3.9/5 |
Limble CMMS |
|
5/5 |
3.8/5 |
MaxPanda |
|
5/5 |
2.9/5 |
MVP Plant |
|
N/A |
2.7/5 |
Hippo CMMS |
|
3/5 |
3/5 |
eMaint (Fluke) |
|
N/A |
3.7/5 |
(App Rating as of 6/13/2023)
As you go through the list above, it’s recommended that you research and evaluate each app based on your specific requirements before making a decision
Implementation and Adoption of Work Order Apps
This is a critical stage that sets the foundation for the app’s success. Even the most highly rated app won’t reach its potential unless the time is taken to ensure proper implementation and adoption. The following are the recommended steps:
Plan the Implementation Process
Begin by defining the implementation goals, timeline, and scope of the project. Identify key stakeholders and establish a project team responsible for overseeing the implementation process. Create a roadmap outlining the steps involved, such as data migration, system configuration, and user training. Assign clear roles and responsibilities to team members and allocate sufficient resources for a smooth implementation.
Train Employees and Promote Adoption
Provide comprehensive training sessions to familiarize employees with the app's features and functionalities. Tailor the training to different user roles and provide hands-on practice. Create user guides, video tutorials, or an internal knowledge base to serve as ongoing resources for employees. Encourage open communication and address any concerns or questions that may arise during the training process. Offer incentives to encourage early adopters and create a positive culture around using the app.
Overcome Challenges and Address Resistance
Common challenges include workers’ resistance to change, concerns about job security, and fear of technology. To overcome them, involve employees from the beginning and actively listen to their feedback. Address their concerns, provide reassurance, and communicate the positive impact the app will have on their work. Utilize a change management strategy that involves clear communication, transparent decision-making processes, and ongoing support.
Integrate Work Order Apps with Existing Workflows
Assess how the app can fit within your current processes and identify areas where it can add value. Determine the necessary data integration points with other systems, such as CRM or asset management tools. Work closely with the app provider to ensure a smooth integration, and consider customization options, if needed.
Collaborate with relevant teams, such as IT or operations, to align the work order app with existing workflows. Map out the new workflow process, clearly defining how work orders will be created, assigned, tracked, and closed within the app. Conduct thorough testing and validation before fully integrating the app into your operations.
Monitor and Evaluate the App's Effectiveness
Set key performance indicators (KPIs) aligned with your business goals and track metrics such as response time, task completion rates, and overall productivity. Analyze the data provided by the app's reporting and analytics capabilities to gain insights into performance and identify areas for improvement.
Regularly solicit feedback from users to understand their experience and any challenges they may face. Use this feedback to make improvements, and address any usability or functionality issues.
Best Practices for Work Order Management with Apps
Standardize Work Order Processes within Apps
Establish clear guidelines and procedures for creating, assigning, and completing work orders within the app. Define required fields, checklists, asset categorizations, and documentation standards to ensure consistency. This standardization promotes efficiency, reduces errors, and facilitates easier tracking and reporting, specifically within the work order app environment.
Establish Clear Communication Channels
Utilize the communication features within the work order app to establish clear and open channels between technicians, supervisors, and other stakeholders involved in the work order process. Leverage in-app messaging or comments to facilitate real-time collaboration, address questions or issues, and keep all parties informed about the progress of work orders.
Encourage Mobile Capabilities for Field Work
Encourage technicians to utilize the app on their mobile devices, specifically for accessing work orders, updating statuses, and uploading important details directly from the field. Leverage mobile features such as GPS tracking, barcode scanning, and photo attachments within the work order app. By utilizing these features, technicians can reduce paperwork and minimize the need for manual data entry later on.
Review and Optimize Workflows within Work Order Apps
Monitor the effectiveness of the app's features and workflows by collecting feedback from technicians and analyzing performance data within the work order app. Identify any bottlenecks, areas of inefficiency, or recurring issues specific to the app and seek opportunities to streamline processes within the app environment.
Continuously optimizing work order workflows within the app ensures that its capabilities align with the evolving needs of your maintenance operations as well as overall organization production.
Work Order Apps in the Age of A.I., Machine Learning, and Predictive Maintenance
The field of work order management is constantly evolving, driven by advancements in technology and changing industry demands. Work order apps, as integral tools for efficient maintenance operations, are at the forefront of these developments.
Organizations need to explore incorporating AI and ML capabilities into work order apps to optimize scheduling, detect anomalies, and predict equipment failures. By doing so, it will further enable proactive maintenance and improve overall efficiency. These added capabilities can analyze equipment performance data, identify potential failures, and schedule maintenance activities in advance through predictive maintenance functions. A shift from reactive to proactive maintenance makes it possible to improve resource planning, minimize downtime, and extend the lifespan of critical assets.
TABLE OF CONTENTS
Keep Reading
Ever find yourself checking into a luxury hotel and expecting a relaxing stay, only to find a ...
11 Apr 2025
Organizations are witnessing swift changes in the business environment and confronting a ...
8 Apr 2025
Last month, news outlets and the entire internet was abuzz with the return of NASA astronauts ...
3 Apr 2025
What comes first - CMMS or predictive maintenance? If your answer is either, it is correct. ...
28 Mar 2025
Artificial intelligence (AI) talk has become commonplace. Today, engaging in business-focused ...
27 Mar 2025
Imagine a world where machines predict, diagnose, and fix their issues before they fail. This ...
25 Mar 2025
A facility maintenance plan is at the core of a facility’s operations. This organized ...
21 Mar 2025
Think of managing your maintenance operations like managing a championship sports team. Just ...
21 Mar 2025
The maintenance sector is battling a severe talent shortage that threatens to undermine ...
7 Mar 2025
Manufacturing maintenance is the backbone of industrial efficiency, ensuring machines run ...
5 Mar 2025
No one likes playing a guessing game when equipment breaks down. Yet, maintenance teams often ...
4 Mar 2025
The size of the preventive maintenance software market is discussed in millions of dollars, ...
4 Mar 2025
The organizational structure and corporate hierarchy vary from company to company. Large ...
28 Feb 2025
Maintenance procedures are essential for ensuring the longevity and reliability of machinery ...
21 Feb 2025
Sustainability is no longer just a buzzword; it's a critical component of corporate social ...
20 Feb 2025
A Computerized Maintenance Management System (CMMS) relies on accurate, well-organized data ...
18 Feb 2025
In an era where technology drives operational efficiency, Computerized Maintenance Management ...
14 Feb 2025
A Computerized Maintenance Management System (CMMS) is a key component of modern maintenance ...
13 Feb 2025
Introduction Maintenance management is the foundation of maintenance operations in industries ...
11 Feb 2025
Introduction A Computerized Maintenance Management System (CMMS) is software designed to help ...
7 Feb 2025