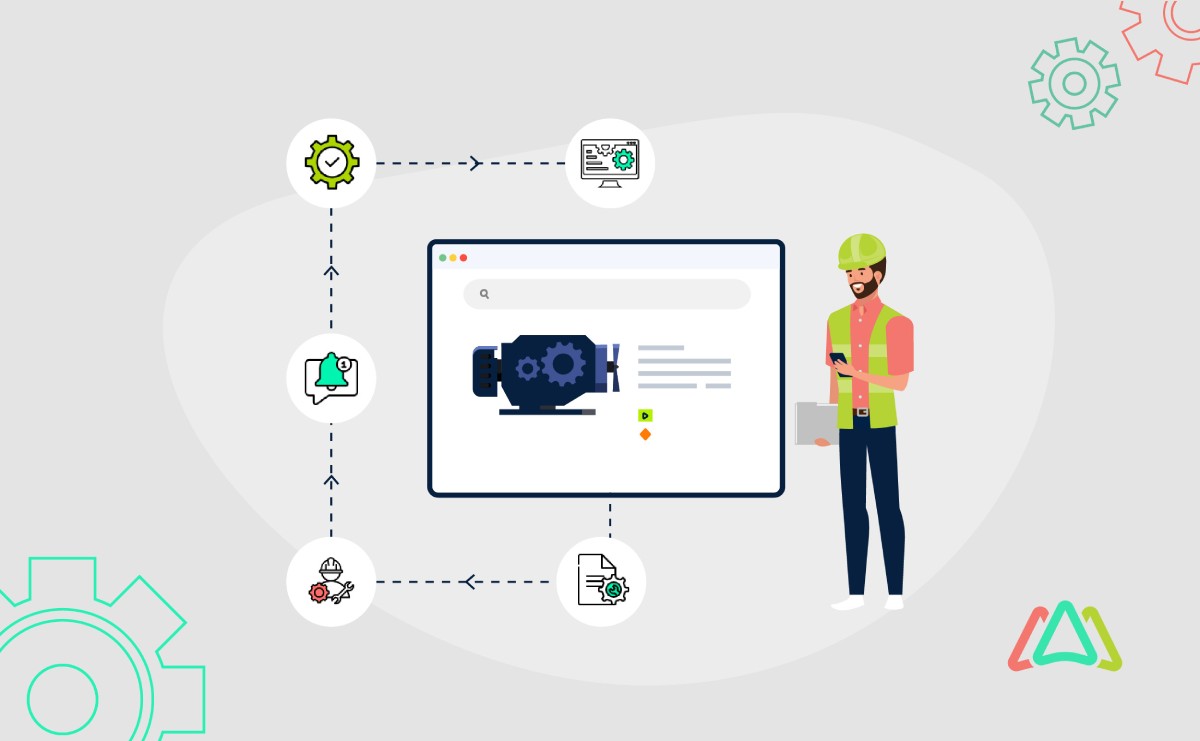
A Guide to Building Your Work Order Process
In maintenance, deadlines are non-negotiable. Whether dealing with client deliverables, internal projects, or routine maintenance tasks, meeting deadlines is vital. A disorganized work order process can lead to extended downtime and missed deadlines, causing dissatisfaction among clients and internal stakeholders. A well-structured process ensures that every task is prioritized, scheduled, and completed on time, resulting in an enhanced reputation for reliability and efficiency.
This article will take you through the process of building a well-structured work order process, from understanding its fundamental elements to the step-by-step creation and successful implementation.
What is a Work Order?
A work order is a written document that serves as a directive, instructing the completion of a specific task or project. This directive can include various activities, from routine maintenance and repairs to complex projects, installations, and service requests.
A work order typically includes critical details such as:
- Work Order Title and Description: A brief yet comprehensive description of the task or project to be completed.
- Priority and Deadline: The level of urgency and the date by which the task must be finished.
- Scope of Work: An outline of the work to be performed, including specifics about the materials, labor, and equipment required.
- Resource Allocation: Information regarding the allocation of manpower, time, and budget to complete the task.
- Attachments and Documentation: Any necessary attachments, such as blueprints, schematics, or guidelines, that provide additional context for the work.
Why do Organizations Need a Work Order Process?
While a work order might appear straightforward, its significance within an organization cannot be overstated. A well-structured work order process is an essential component of productivity and efficiency, and here's why:
- Clarity and Direction: Work orders provide clear and concise instructions for tasks, leaving little room for ambiguity. This ensures that everyone involved understands their role and what is expected of them.
- Prioritization and Time Management: By assigning priorities and due dates, work orders help organizations manage their resources efficiently. This enables teams to focus on high-priority tasks and ensures that deadlines are met.
- Accountability: In an effective work order process, accountability is established from the outset. Each work order outlines the responsible parties, fostering a culture of ownership within the organization.
- Documentation and Traceability: Work orders serve as a documented trail of tasks, making it easier to track progress and ensure work is completed to the required standards. This documentation can be valuable for auditing, compliance, and future reference.
- Data for Decision-Making: Work orders generate data that can be analyzed to improve processes, identify areas for cost savings, and enhance operational efficiency.
Planning Your Work Order Process
1. Who is involved in the work order process?
Before you build a well-structured work order process, it's essential to identify and understand the key stakeholders involved. The work order process doesn't exist in isolation; it's a collaborative effort that requires the involvement and coordination of various individuals and departments within your organization. These stakeholders can include:
- Requesters: Those who initiate the service request by identifying the need for a specific task or project. Requests must be reviewed and approved before becoming a work order.
- Approvers: Individuals responsible for reviewing and approving service requests and work orders. This may include supervisors, managers, or project leads.
- Technicians/Workers: The individuals or teams responsible for carrying out the work outlined in the work order.
- Managers and Supervisors: Those who oversee and manage the execution of work orders, ensuring that tasks are completed as per specifications.
- Administrative Staff: Those responsible for maintaining records and documentation and ensuring the process flows smoothly.
- Vendors: 3rd party vendors outside of the organization who are assigned to specific work orders. Vendors are often used for specialized work and maintenance tasks. Some organizations with large dispersed real estate portfolios will rely on 3rd party vendors for work orders.
Understanding these stakeholders and their roles is essential to building a work order process that effectively serves the needs of your organization. It promotes clear communication and collaboration among all parties involved.
2. What are the primary goals of your work order process?
A well-structured work order process should be aligned with the overarching objectives and goals of your organization. These objectives can vary depending on your industry, the nature of your work, and your specific challenges. Common goals that a work order process can help you achieve include:
- Improved Productivity: Streamlining tasks and processes to ensure work is completed efficiently, reducing response time, time to complete, downtime, and resources used.
- Cost Reduction: Managing resources effectively to control operational costs, minimize waste, and prevent unnecessary expenditures.
- Improved Customer Satisfaction: Ensuring that work is completed on time and to the satisfaction of clients, stakeholders, or internal departments.
- Compliance and Accountability: Meeting industry regulations and standards while establishing a culture of accountability within your organization.
- Data-Driven Decision Making: Gathering data from the work order process that can be analyzed to make informed decisions and continuously improve operations.
- Efficient Resource Allocation: Optimizing the allocation of resources, including time, manpower, and budget, to meet project or task requirements.
3. Metrics for measuring the success of your process
Key Performance Indicators (KPIs) are measurable metrics that enable you to evaluate the process's performance and make data-driven decisions. The choice of KPIs should be tailored to your organization's goals. Common KPIs for a work order process include:
- Task Completion Time: How quickly are work orders turned into completed tasks or projects?
- Resource Utilization: Are resources being used efficiently, and are there areas where resource allocation can be optimized?
- Cost per Work Order: What is the cost of processing each work order, and can it be reduced?
- Customer Satisfaction Scores: How satisfied are your clients or internal stakeholders with the work order process and its outcomes?
- Number of Work Orders Completed: The volume of work orders successfully processed over a defined period.
- Mean Time to Repair: Measures the average time to repair a failed asset or system. It indicates how quickly issues are resolved. A lower MTTR implies faster and more efficient repairs, while a higher MTTR suggests slower repair times.
Establishing and regularly monitoring these KPIs allows you to measure the success of your work order process, identify areas for improvement, and make informed decisions to enhance your organization's efficiency and productivity.
Designing the Work Order Template
A well-structured work order process relies on a clear and comprehensive work order template. This template serves as the blueprint for each task or project, ensuring that all essential details are captured, and everyone involved understands their roles and responsibilities.
The critical components of a well-designed work order template:
1. Work Order Title and Description
The work order title and description serve as the first point of reference for anyone involved. It should provide a clear and concise overview of the task or project to be completed. The title should be descriptive but concise, while the description should elaborate on the specifics of the work, including any special requirements or considerations.
2. Priority and Deadline
Work orders often come with varying levels of urgency. Prioritizing tasks and setting deadlines are critical components of the template. Priorities can be categorized as "critical," "high," "medium," and "low," while deadlines should specify the date and time by which the work should be completed. This ensures that all parties understand the sense of urgency and time constraints.
3. Scope of Work
The scope of work section is where you outline, in detail, what the task or project entails. This should include a step-by-step breakdown of the work, a list of specific deliverables, and any instructions or guidelines that need to be followed. A well-defined scope of work prevents misunderstandings and misinterpretations, promoting efficiency and accuracy.
4. Resource Allocation
Efficient resource allocation is vital to the success of a work order. In this section, specify the resources required to complete the task. This includes the personnel responsible and any parts, materials, or supplies that must be on hand. The allocation of resources ensures that the right people and materials are available for the job.
5. Budget and Cost
To maintain control over costs and budgets, work orders should include a budget and cost section. This details the financial aspects of the task, including the estimated costs of labor, materials, and any other relevant expenses. It allows for better financial planning and oversight throughout the process.
6. Attachments and Documentation
In many cases, work orders require additional documentation, such as blueprints, schematics, safety guidelines, or previous work history. This section provides a space to attach or reference such documents, ensuring that all relevant information is readily available to those executing the work. Technicians and requesters can also upload images related to the work that is required.
Creating Work Orders in Click Maint is EASY AS 1 - 2 - 3!
A well-designed work order template serves as a vital tool in ensuring that every work order is not only executed efficiently but also consistently. It promotes clear communication, accountability, and adherence to guidelines, and it's the foundation upon which a well-structured work order process is built.
Workflow and Process Flowchart
1. Creating a Visual Representation of Your Work Order Process
A visual representation, like a flowchart or workflow diagram, is a powerful tool for understanding, optimizing, and communicating your work order process. It provides a clear, at-a-glance view of how tasks move from initiation to completion.
- Identify Process Stages: Break down your work order process into distinct stages, starting from the initiation of a request to the final approval and completion of the task.
- Map the Workflow: For each stage, create a visual representation that includes the steps, actions, and decision points involved. Use symbols, shapes, and arrows to illustrate the flow of tasks, decisions, and information.
- Document Dependencies: Highlight the interdependencies between different stages and actions. This is essential for understanding how tasks should be carried out.
- Clarify Roles and Responsibilities: Indicate who is responsible for each step in the process. This helps in establishing clear accountability.
2. Identifying Decision Points and Approval Steps
Within your work order process, various decision points and approval steps play a significant role in ensuring that work orders progress smoothly and meet the organization's requirements. These decision points often involve considerations such as:
- Approvals: Identify which process stages require approvals from designated individuals or teams. Approval ensures that the work aligns with the organization's standards and objectives.
- Quality Control: Determine where and how quality checks should be performed to ensure work meets the required standards. This might involve inspections, testing, or peer reviews.
- Escalation: Define the conditions under which issues or obstacles should be escalated to higher authorities or specialized teams. Escalation paths help in resolving problems quickly and effectively.
- Rejection Criteria: Specify the criteria that would lead to a work order being rejected or put on hold. This could be due to safety concerns, budget constraints, or other valid reasons.
3. Defining Escalation Paths for Issues
- Issue Identification: Determine how issues will be identified, whether through regular checks, worker feedback, or other means.
- Escalation Levels: Define a hierarchy of escalation levels, indicating which issues can be resolved at a lower level and which require escalation to higher authorities.
- Response Time: Specify the expected response time for each level of escalation. This ensures that issues are addressed promptly.
- Communication Protocol: Describe the communication channels and methods to be used when issues are escalated. Clarity in communication prevents misunderstandings and delays.
- Resolution Process: Outline the steps that should be taken to resolve issues at each level of escalation. This may involve reassessment, reassignment, or even halting the work order.
Using a Work Order Management Software
Work order management software is a cornerstone for organizations seeking maximum efficiency and productivity. It offers a centralized platform for creating, tracking, and managing work orders. When choosing software, it's important to pick a vendor that follows best practices for work order templates. Here's why this software is vital and what to look for in a vendor:
- Centralization: Work order management software centralizes all work orders, making it easy to create, track, and manage tasks from a single interface. This reduces manual data entry and simplifies the process.
- Standardization: The software can enforce standardized work order templates, ensuring that all critical details are consistently captured in every work order.
- Automation: It automates various aspects of the process, such as sending notifications to stakeholders, tracking work order progress, and generating reports.
- Reporting and Analytics: Work order management software often comes with robust reporting and analytics capabilities, allowing you to extract valuable data for decision-making and continuous improvement.
- Customization: Choose a vendor that allows you to customize work order templates to match your organization's unique requirements. This flexibility is essential for tailoring the process to your specific needs.
Collaboration Tools
Collaboration tools facilitate communication and cooperation among team members, stakeholders, and decision-makers. They enable real-time interactions, document sharing, and feedback loops. Tools such as project management software, team messaging platforms, and shared cloud storage systems can streamline communication and ensure everyone is on the same page.
Mobile Apps for Field Work
Fieldwork often requires a mobile solution to ensure that technicians and workers have access to work orders, instructions, and documentation while on-site. Work order apps designed for field work enable real-time updates, data collection, and instant communication with the central system. These apps enhance efficiency, reduce paperwork, and promote accurate reporting from the field.
Integration with Other Systems
Your work order process doesn't exist in isolation. It often needs to integrate with other systems, such as inventory management, financial software, and customer relationship management (CRM) systems. Integration ensures that data flows seamlessly between these systems, reducing manual data entry, minimizing errors, and enhancing efficiency.
Training and Onboarding
A well-structured work order process is only as effective as the team that executes it. Proper training and onboarding of your team are essential to ensure that everyone understands their roles and responsibilities within the process.
Training Your Team on the New Work Order Process
Implementing a new work order process often represents a significant organizational change. To ensure a smooth transition and successful adoption, thorough training is essential. Here's how to go about it:
- Identify Training Needs: Begin by identifying the training needs of your team. This involves understanding the current skill levels, knowledge gaps, and areas where additional training is necessary.
- Customized Training Programs: Develop customized training programs that cater to different roles within your organization. For example, technicians might require technical training, while managers might need training on the process's oversight and management.
- Hands-on Workshops: Conduct workshops or training sessions that provide practical experience with the new work order process. This can include scenarios, simulations, and real-world examples.
- Online Learning Resources: Create online resources such as video tutorials, e-learning modules, or webinars to accommodate different learning styles and provide ongoing support.
- Feedback and Assessment: Encourage team members to provide feedback on the training process and use assessments or quizzes to gauge their understanding. Adjust training programs as needed based on this feedback.
- Continuous Learning: Recognize that training is an ongoing process. Provide opportunities for continuous learning, including refresher courses and advanced training for those who want to deepen their skills.
- Lean on your Software Vendor: Your software provider can assist with developing a training program for your team and provide you with digital resources like videos, webinars, product tours, and access to its knowledge base.
Documentation and User Manuals
Work Order Templates: Clearly document the work order template, including instructions on completing each section. This ensures consistency and helps team members understand what is expected.
- Role-based Manuals: Create role-specific user manuals that detail the responsibilities, tasks, and expectations for each role involved in the process. These manuals serve as quick references for team members.
- Frequently Asked Questions (FAQs): Develop a list of frequently asked questions and provide answers to common queries. This can be a valuable resource for team members seeking quick solutions.
- Visual Aids: Incorporate visuals, diagrams, and flowcharts in your documentation to make it more engaging and easier to understand.
- Access and Distribution: Ensure all team members have access to the documentation. You can use digital formats, printed manuals, or an online knowledge base, depending on your organization's preferences.
- Updates and Revisions: Regularly update and revise your documentation to align with any changes or improvements made to the work order process.
Launching a Pilot Program to Test the New Process
- Select a Representative Group: Choose a group of team members or a department that represents the diverse roles and responsibilities within your organization. This group should reflect the various stakeholders involved in the work order process.
- Define Objectives: Clearly define the objectives of the pilot program. What do you aim to achieve by testing the new process, and what specific outcomes are you looking for? These objectives should align with the broader goals of your organization.
- Communicate the Purpose: Inform the selected group about the purpose and scope of the pilot program. Make it clear that this is an opportunity to test and provide feedback on the new work order process.
- Provide Training: Ensure that the participants in the pilot program receive adequate training on the new process. This training should cover how to use the updated work order template, roles and responsibilities, and how to navigate any new technology or tools.
- Run Parallel Systems: During the pilot, run the new work order process in parallel with the existing process. This allows for a direct comparison and helps identify areas of improvement.
Gathering Feedback and Making Adjustments
- Feedback Mechanisms: Establish clear feedback mechanisms, such as surveys, focus groups, one-on-one interviews, or feedback forms. Make it easy for participants to share their thoughts and concerns.
- Regular Check-Ins: Schedule regular check-in sessions with the pilot group to discuss their experiences and challenges while using the new process.
- Document Feedback: Keep detailed records of the feedback received, categorizing it into different areas, such as process flow, documentation, tools, and communication.
- Assess Feedback: Assess the feedback and identify common themes or recurring issues. Look for both positive feedback on what is working well and constructive criticism on areas that need improvement.
- Adjustments and Refinements: Based on the feedback received, make necessary adjustments and refinements to the work order process. This might involve updating the work order template, clarifying roles and responsibilities, or addressing technology or tool-related issues.
- Iterative Testing: Continue to run the pilot program with the updated process, and gather additional feedback to ensure the adjustments have resolved the identified issues.
- Evaluation: After the pilot program is completed, conduct a thorough evaluation to determine whether the new work order process is now meeting the predefined objectives and is ready for full implementation.
Pilot testing is an important phase that allows you to address potential issues and ensure that the new work order process aligns with your organization's needs and objectives. It should be noted that pilot testing may not be required for small operations and teams, but should be considered for larger, more complex operations. The feedback gathered and adjustments made during this phase contribute to a successful and smooth rollout of the process to the entire organization.
TABLE OF CONTENTS
Keep Reading
Ever find yourself checking into a luxury hotel and expecting a relaxing stay, only to find a ...
11 Apr 2025
Organizations are witnessing swift changes in the business environment and confronting a ...
8 Apr 2025
Last month, news outlets and the entire internet was abuzz with the return of NASA astronauts ...
3 Apr 2025
What comes first - CMMS or predictive maintenance? If your answer is either, it is correct. ...
28 Mar 2025
Artificial intelligence (AI) talk has become commonplace. Today, engaging in business-focused ...
27 Mar 2025
Imagine a world where machines predict, diagnose, and fix their issues before they fail. This ...
25 Mar 2025
A facility maintenance plan is at the core of a facility’s operations. This organized ...
21 Mar 2025
Think of managing your maintenance operations like managing a championship sports team. Just ...
21 Mar 2025
The maintenance sector is battling a severe talent shortage that threatens to undermine ...
7 Mar 2025
Manufacturing maintenance is the backbone of industrial efficiency, ensuring machines run ...
5 Mar 2025
No one likes playing a guessing game when equipment breaks down. Yet, maintenance teams often ...
4 Mar 2025
The size of the preventive maintenance software market is discussed in millions of dollars, ...
4 Mar 2025
The organizational structure and corporate hierarchy vary from company to company. Large ...
28 Feb 2025
Maintenance procedures are essential for ensuring the longevity and reliability of machinery ...
21 Feb 2025
Sustainability is no longer just a buzzword; it's a critical component of corporate social ...
20 Feb 2025
A Computerized Maintenance Management System (CMMS) relies on accurate, well-organized data ...
18 Feb 2025
In an era where technology drives operational efficiency, Computerized Maintenance Management ...
14 Feb 2025
A Computerized Maintenance Management System (CMMS) is a key component of modern maintenance ...
13 Feb 2025
Introduction Maintenance management is the foundation of maintenance operations in industries ...
11 Feb 2025
Introduction A Computerized Maintenance Management System (CMMS) is software designed to help ...
7 Feb 2025