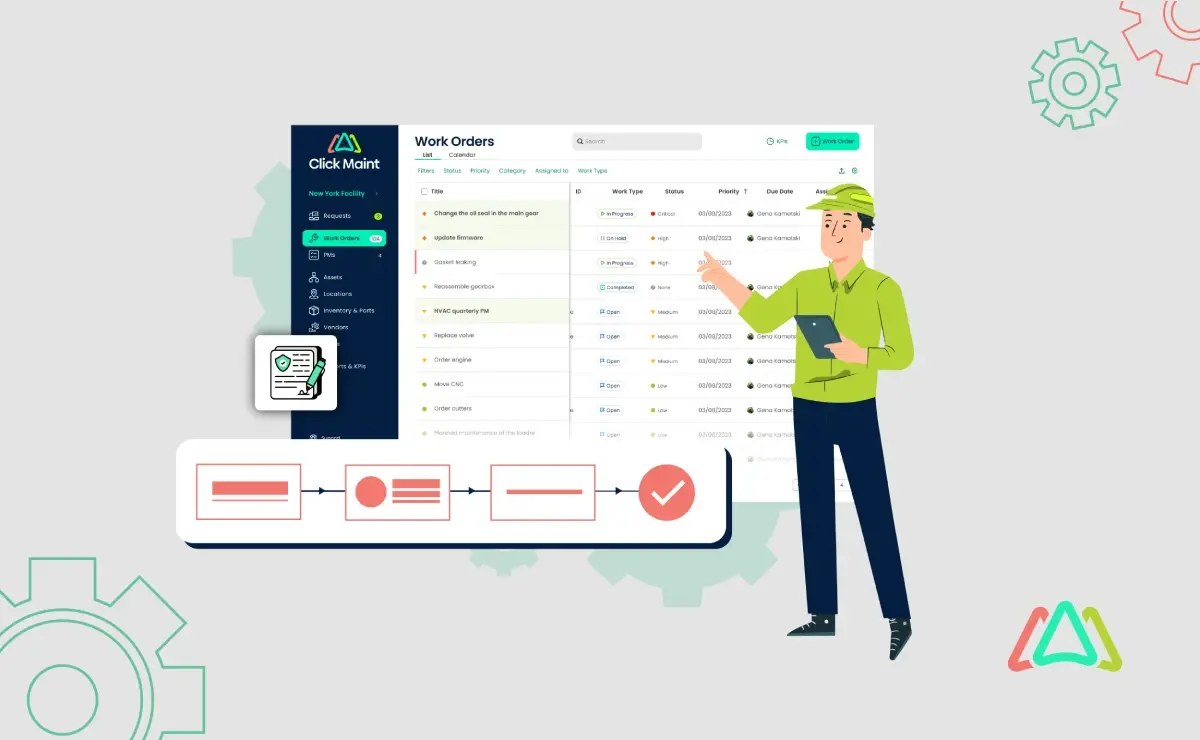
Work Order Programs: A Step-by-Step Implementation Guide
Effective work order management is important for businesses of all sizes and industries. It ensures that maintenance and repair tasks are prioritized and completed on time, reducing downtime and increasing operational efficiency. Work order software plays an important role in modernizing maintenance operations, improving productivity, and optimizing resource utilization within organizations. However, by using an integrated work order program, businesses can avoid costly errors, improve communication among team members, and maintain a clear record of all maintenance activities. This not only enhances the reliability of equipment and facilities but also contributes to better customer satisfaction and overall business performance.
Work Order Software: The Digital Tools for Efficient Maintenance Management
1. Definition and Characteristics
1.1 Specific Application Designed for Managing Work Orders Digitally
Work order software refers to specialized applications designed to streamline the management of work orders within organizations. It provides digital tools and functionalities that facilitate the creation, assignment, tracking, and reporting of work orders. These software solutions are instrumental in optimizing maintenance tasks, repairs, and other operational workflows.
1.2 How does Work Order Management Software work?
It works by allowing users to create, assign, and track work orders through a centralized system.
1.3 Features: Work Order Creation, Assignment, Tracking, Reporting, etc.
Key features of work order software include:
- Work Order Creation: Allows users to generate work orders quickly and efficiently.
- Assignment: Facilitates assigning tasks to specific individuals or teams.
- Tracking: Enables real-time monitoring of work order progress and status updates.
- Reporting: Provides comprehensive reports on work order completion, maintenance history, and performance metrics.
- Integration: Often integrates with other systems such as asset management and inventory software for seamless operations.
2. Examples of Work Order Software
1. Click Maint
Click Maint CMMS offers a user-friendly platform for managing work orders, scheduling maintenance tasks, and tracking asset performance.
2. Limble
Limble CMMS provides comprehensive maintenance management solutions, including work order management, preventive maintenance scheduling, and asset tracking.
3. Fiix
Fiix CMMS offers a cloud-based CMMS solution that simplifies maintenance management, work order tracking, and reporting for businesses of all sizes.
3. Benefits of Work Order Software
1. Streamlined Processes and Enhanced Efficiency
Work order software streamlines workflows by automating the creation, assignment, and tracking of work orders. This leads to increased operational efficiency and reduced downtime.
2. Real-time Tracking and Reporting Capabilities
The ability to track work orders in real-time and generate detailed reports allows organizations to gain insights into maintenance activities. It improves decision-making, facilitates proactive maintenance strategies, and ensures compliance with regulatory requirements.
Work Order Programs: Comprehensive Systems for Integrated Management
1. Definition and Scope
1.1 Encompasses Software Tools, Processes, and Organizational Procedures
Work order programs are comprehensive systems designed to manage and optimize work order processes within an organization. Unlike standalone software, these programs integrate software tools with organizational procedures and workflows to provide a holistic approach to work order management. They are designed to streamline operations, enhance communication, and ensure that all maintenance and repair activities are conducted efficiently and effectively.
1.2 Customized to Fit Specific Organizational Needs and Workflows
Work order programs are highly customizable, allowing organizations to tailor them to meet their unique needs and workflows. This customization can involve adjusting software configurations, developing specific processes and policies, and CMMS integration with existing systems and tools. The goal is to create a cohesive system that aligns with the organization's operational goals and enhances overall productivity.
2. Components of Work Order Programs
2.1 Software Applications
Software applications are a critical component of work order programs. These tools provide the digital infrastructure needed to create, assign, track, and report on work orders. They often include features for scheduling, resource allocation, real-time asset tracking, and analytics. These applications can be customized to integrate seamlessly with other business systems such as ERP (Enterprise Resource Planning) and CMMS (Computerized Maintenance Management System).
2.2 Workflow Processes and Policies
Workflow processes and policies define how work orders are managed from initiation to completion. This includes the procedures for creating work orders, assigning tasks, prioritizing activities, and closing out completed jobs. Well-defined workflows ensure consistency, efficiency, and accountability in work order management. Policies may also cover compliance with regulatory requirements, safety protocols, and quality standards.
2.3 Human Resource Elements and Training
Human resources and training are essential to the successful implementation and operation of work order programs. This involves ensuring that staff are adequately trained to use the Fworsoftware applications and understand the workflow processes and policies. Ongoing CMMS training and support help maintain high levels of competence and ensure that the program continues to meet the evolving needs of the organization. Additionally, clear roles and responsibilities should be established to ensure effective coordination and communication among team members.
3. Examples of Work Order Programs
3.1 Custom-Built Systems in Manufacturing and Facility Management
In industries such as manufacturing and facility management, custom-built work order programs are often developed to address specific operational challenges. These programs integrate specialized software tools with tailored workflow processes to manage complex maintenance schedules, equipment repairs, and facility upkeep. For example, a manufacturing plant might use a custom-built system to coordinate preventive maintenance on machinery, ensuring minimal downtime and optimal production efficiency.
3.2 Integrated Systems Combining Software Tools with Manual Processes
Some organizations utilize integrated work order programs that combine advanced software tools with manual processes. This approach can be particularly useful in environments where certain tasks require hands-on management or where existing manual processes need to be incorporated into the digital system. For instance, a facility management company might use a work order program that includes digital tools for scheduling and tracking work orders, along with manual checklists and inspections to ensure compliance with safety standards.
Key Differences Between Work Order Software and Work Order Programs
1. Scope and Focus
Work Order Software:
Work order software primarily focuses on providing digital tools for managing work orders efficiently. It typically includes features such as work order creation, assignment, tracking, and reporting. The scope of work order software is centered around automating and streamlining the management of maintenance tasks and repair jobs within an organization.
Work Order Programs:
Work order programs encompass entire systems that go beyond just software. They include integrated processes, policies, and sometimes hardware components. The focus is not only on digital tools but also on establishing comprehensive systems and methodologies for managing work orders effectively. Work order programs aim to optimize workflows, enhance communication among stakeholders, and improve overall operational efficiency.
2. Customization and Flexibility
Work Order Software:
Work order software is generally standardized with predefined features and workflows. While some level of customization may be possible, it is often limited to configuring settings and templates within the software. Users can typically adjust settings to align with their specific needs but may have less flexibility in modifying core functionalities.
Work Order Programs:
Work order programs offer high levels of customization and flexibility. Organizations can tailor the program to fit their unique requirements, workflows, and business processes. This customization may involve configuring workflows, adding or removing modules, integrating with existing systems, and even developing bespoke solutions to address specific challenges. The flexibility of work order programs allows organizations to adapt the system as their needs evolve over time.
3. Implementation and Integration
Work Order Software:
Implementing work order software involves deploying a software product within the organization. It typically includes installation, configuration, and setup of the software by the vendor or IT team. Vendor support is often available to assist with technical issues, updates, and maintenance of the software.
Work Order Programs:
Implementing a work order program is a more extensive process that goes beyond software deployment. It requires comprehensive planning, deployment, and integration of both software and associated processes. This may involve assessing current workflows, defining new procedures, training staff, and ensuring seamless integration with other organizational systems such as ERP (Enterprise Resource Planning) or CMMS (Computerized Maintenance Management System). The goal is to create a cohesive system that enhances operational efficiency and supports organizational objectives.
Steps to Implementing a Work Order Program
1. Assessing Organizational Needs and Goals
1.1 Identifying Current Challenges
Evaluate existing work order management processes and pinpoint inefficiencies.
Begin by thoroughly examining your current work order management practices to identify any gaps or areas where processes are not functioning optimally. Look for bottlenecks, redundant tasks, and communication breakdowns.
Gather input from stakeholders across different departments.
Engage with stakeholders from various departments to gather their perspectives on the current system's shortcomings. This holistic view ensures that all pain points are addressed and that the new system meets the needs of all users.
1.2 Setting Objectives
Define clear goals for what the work order program should achieve (e.g., improved efficiency, cost reduction, better resource allocation).
Establish specific, measurable objectives that the work order program should accomplish. These goals should align with broader organizational objectives and address the challenges identified.
Establish key performance indicators (KPIs) to measure success.
Determine the KPIs that will help track the performance of the work order program. These could include metrics such as work order completion times, cost savings, resource utilization, and user satisfaction.
2. Researching and Selecting Components
2.1 Evaluating Work Order Software Options
Compare features, usability, and integration capabilities of various software tools.
Research different work order software options, focusing on their features, ease of use, and how well they integrate with your existing systems. Look for software that can scale with your business and offers robust support and updates.
Consider vendor reputation, support, and future scalability.
Evaluate the reputation of software vendors, their customer support quality, and the software's ability to scale as your organization grows. Choose a vendor with a proven track record of reliability and customer satisfaction.
Check out our list of Top 10 CMMS Software for Efficient Work Order Management
2.2 Designing Workflow Processes
Map out the desired workflow processes that the program will support.
Design the workflow processes that the work order program will facilitate. Ensure these workflows are efficient, align with industry best practices, and meet the organization's specific needs.
Ensure alignment with organizational goals and industry best practices.
Verify that the designed workflows support your organizational goals and adhere to best practices in your industry. This alignment ensures the program will deliver the intended benefits.
3. Planning and Preparation
3.1 Developing an Implementation Plan
Create a detailed project plan outlining phases, timelines, and responsibilities.
Develop a comprehensive project plan that outlines each phase of the implementation, timelines for completion, and responsibilities for each task. This plan should provide a clear roadmap for the entire implementation process.
Allocate necessary resources, including budget and personnel.
Identify and allocate the resources required for the implementation, including budget and personnel. Ensure that you have the necessary financial and human resources to support the project.
3.2 Engaging Stakeholders
Communicate the plan and its benefits to all relevant stakeholders.
Clearly communicate the implementation plan and its benefits to all stakeholders. Ensure that everyone understands how the new work order program will improve operations and what their role will be in the process.
Gather feedback and make adjustments as needed.
Collect feedback from stakeholders and be prepared to make adjustments to the plan. Engaging stakeholders early and often helps ensure buy-in and smooth implementation.
4. Customizing the Work Order Program
4.1 Configuring Software Tools
Customize the chosen software to fit the specific needs of the organization.
Tailor the work order software to meet the specific requirements of your organization. This customization might include setting up workflows, configuring user roles, and adjusting system settings.
Set up integrations with other systems (e.g., inventory management, ERP).
Integrate the work order software with other critical systems such as inventory management and ERP. These integrations ensure seamless CMMS data import and improve overall efficiency.
4.2 Developing Policies and Procedures
Establish clear policies and procedures for work order management.
Develop and document clear policies and procedures that govern work order management. These should define how work orders are created, assigned, tracked, and closed.
Document workflows, roles, and responsibilities.
Create detailed documentation of the workflows, roles, and responsibilities associated with the work order program. This documentation serves as a reference for users and ensures consistency in operations.
5. Training and Onboarding
5.1 Conducting User Training
Provide comprehensive training sessions for all users, including hands-on practice.
Organize thorough training sessions that cover all aspects of the new work order program. Include hands-on practice to help users become comfortable with the system.
Offer ongoing training resources and support.
Provide ongoing access to training resources and support to ensure users can continually improve their skills and resolve any issues that arise.
5.2 Ensuring User Adoption
Address user concerns and resistance to change.
Proactively address any concerns or resistance to the new system. Listen to user feedback and make necessary adjustments to ease the transition.
Promote the benefits of the new system to encourage adoption.
Highlight the benefits of the new work order program to encourage CMMS user adoption. Show how the system improves efficiency, reduces workload, and contributes to the organization's success.
6. Monitoring and Optimization
6.1 Tracking Performance
Monitor the performance of the work order program using established KPIs.
Regularly track the performance of the work order program using the established KPIs. This monitoring helps you understand how well the system is functioning and where improvements may be needed.
Collect and analyze feedback from users.
Continuously collect feedback from users to identify any issues or areas for enhancement. User insights are valuable for optimizing the program.
6.2 Continuous Improvement
Identify areas for improvement and make necessary adjustments.
Use performance data and user feedback to identify areas for improvement. Make the necessary adjustments to workflows, processes, or system configurations to enhance performance.
Regularly update the program to adapt to changing needs and technologies.
Keep the work order program up-to-date with the latest technologies and evolving organizational needs. Regular updates ensure the program remains effective and relevant.
7. Reviewing and Scaling the Program
7.1 Periodic Review
Conduct regular reviews to assess the effectiveness of the program.
Schedule regular reviews to evaluate the effectiveness of the work order program. These reviews should analyze performance data and user feedback to determine if the program is meeting its goals.
Make strategic adjustments based on performance data and user feedback.
Based on the review findings, make strategic adjustments to improve the program. This may include changes to workflows, training, or system configurations.
7.2 Scaling and Expansion
Plan for scaling the program as the organization grows.
Develop a plan for scaling the work order program to accommodate organizational growth. This might involve adding new users, expanding features, or integrating additional systems.
Explore additional features or modules that can enhance the program’s capabilities.
Consider implementing additional features or modules that can enhance the capabilities of the work order program. Continuous innovation ensures the program remains a valuable asset to the organization.
Challenges, Implementation Process, and Benefits of Work Order Programs across Different Industries
1. Manufacturing Industry
1.1 Initial Challenges
Complexity of Operations:
Manufacturing environments often involve complex machinery and processes, making it challenging to manage maintenance activities efficiently.
Downtime Impact:
Any downtime cost in manufacturing includes significant losses, so timely and effective maintenance is essential.
Integration with Existing Systems:
Many manufacturing facilities have legacy systems in place, which can complicate the integration of new work order programs.
1.2 Implementation Process
Assessment and Planning:
Conduct a thorough assessment of the current maintenance processes and identify areas for improvement. Define clear objectives and KPIs.
Selecting the Right Software:
Choose a work order software that integrates well with existing systems (e.g., ERP, CMMS) and supports the complex workflows of the manufacturing process.
Customization and Integration:
Customize the software to fit specific manufacturing needs and integrate it with other operational systems to ensure seamless data flow.
Training and Onboarding:
Provide comprehensive training to maintenance staff and other relevant personnel. Ensure ongoing support and resources are available.
Pilot Testing and Rollout:
Conduct a pilot test in a specific area to identify any issues and make necessary adjustments before a full-scale rollout.
1.3 Results and Benefits
Increased Efficiency:
Streamlined processes and automated workflows lead to faster response times and reduced downtime.
Enhanced Predictive Maintenance:
Improved data collection and analysis enable better predictive maintenance, reducing unexpected breakdowns.
Cost Savings:
Reduced downtime and efficient resource allocation lead to significant cost savings.
Improved Compliance:
Enhanced tracking and documentation ensure better compliance with industry regulations and standards.
2. Healthcare Sector
2.1 Initial Challenges
Stringent Regulatory Requirements:
Healthcare facilities must comply with strict regulations, making maintenance management complex.
Critical Nature of Equipment:
The reliability of medical equipment is essential, as failures can directly impact patient care.
High Volume of Work Orders:
Healthcare facilities often have a high volume of work orders, which can be challenging to manage without an efficient system.
2.2 Implementation Process
Needs Assessment:
Identify the specific maintenance needs of the healthcare facility and any regulatory requirements that must be met.
Software Selection:
Choose a work order program that offers robust tracking, documentation, and compliance features.
Customization and Policy Development:
Customize the software to align with healthcare workflows and develop clear policies and procedures for work order management.
Training and Support:
Provide extensive training to ensure all users are proficient with the new system. Establish a support system to address any ongoing issues.
Gradual Implementation:
Implement the program in phases to ensure a smooth transition and allow time to address any challenges that arise.
2.3 Results and Benefits
Enhanced Equipment Reliability:
Improved tracking and maintenance ensure medical equipment is always in optimal condition, directly benefiting patient care.
Regulatory Compliance:
Better documentation and tracking help meet regulatory requirements, reducing the risk of non-compliance penalties.
Efficient Resource Management:
Streamlined processes allow for better allocation of maintenance resources, improving overall efficiency.
Cost Management:
Reduced equipment downtime and optimized maintenance schedules lead to cost savings.
3. Facility Management
3.1 Initial Challenges
Diverse Range of Tasks:
Facility management involves a wide range of tasks, from HVAC maintenance to cleaning, making work order management complex.
Coordination Across Teams:
Coordinating work orders across different teams and departments can be challenging.
Real-time Tracking and Reporting:
Ensuring real-time tracking and reporting of maintenance activities is important for effective facility management.
3.2 Implementation Process
Comprehensive Needs Analysis:
Conduct a thorough analysis of the facility’s maintenance needs and identify key areas for improvement.
Choosing the Right Solution:
Select a work order program that can handle the diverse tasks involved in facility management and offers real-time tracking features.
Customizing Workflows:
Customize the software to fit the specific workflows of the facility management team, ensuring all tasks are efficiently managed.
Staff Training:
Train all facility management staff on how to use the new system effectively. Provide ongoing training to ensure continuous improvement.
Pilot Program and Full Deployment:
Start with a pilot program to test the new system and make any necessary adjustments. Once successful, proceed with a full-scale deployment.
3.3 Results and Benefits
Improved Task Coordination:
Enhanced coordination across different teams leads to more efficient completion of maintenance tasks.
Real-time Visibility:
Real-time tracking and reporting provide better visibility into ongoing and completed work orders, allowing for proactive management.
Enhanced Productivity:
Streamlined workflows and automated processes boost overall productivity.
Cost Efficiency:
Better resource allocation and reduced downtime lead to significant cost savings.
Conclusion
Implementing a work order program in these diverse industries helps address specific challenges, streamlines processes, and ultimately leads to enhanced efficiency, cost savings, and improved operational outcomes.
A robust work order program not only improves maintenance management but also supports strategic objectives, such as cost reduction, increased productivity, and compliance with regulatory standards. From assessing organizational needs and evaluating potential solutions to planning, training, and continuous optimization, each step plays a vital role in the successful implementation of a work order program.
As businesses evolve and face new challenges, a well-implemented work order program provides the flexibility and scalability needed to adapt and thrive. Leveraging technology and best practices in maintenance management ensures that organizations can maintain their assets efficiently, minimize downtime, and achieve long-term success.
TABLE OF CONTENTS
Keep Reading
Ever find yourself checking into a luxury hotel and expecting a relaxing stay, only to find a ...
11 Apr 2025
Organizations are witnessing swift changes in the business environment and confronting a ...
8 Apr 2025
Last month, news outlets and the entire internet was abuzz with the return of NASA astronauts ...
3 Apr 2025
What comes first - CMMS or predictive maintenance? If your answer is either, it is correct. ...
28 Mar 2025
Artificial intelligence (AI) talk has become commonplace. Today, engaging in business-focused ...
27 Mar 2025
Imagine a world where machines predict, diagnose, and fix their issues before they fail. This ...
25 Mar 2025
A facility maintenance plan is at the core of a facility’s operations. This organized ...
21 Mar 2025
Think of managing your maintenance operations like managing a championship sports team. Just ...
21 Mar 2025
The maintenance sector is battling a severe talent shortage that threatens to undermine ...
7 Mar 2025
Manufacturing maintenance is the backbone of industrial efficiency, ensuring machines run ...
5 Mar 2025
No one likes playing a guessing game when equipment breaks down. Yet, maintenance teams often ...
4 Mar 2025
The size of the preventive maintenance software market is discussed in millions of dollars, ...
4 Mar 2025
The organizational structure and corporate hierarchy vary from company to company. Large ...
28 Feb 2025
Maintenance procedures are essential for ensuring the longevity and reliability of machinery ...
21 Feb 2025
Sustainability is no longer just a buzzword; it's a critical component of corporate social ...
20 Feb 2025
A Computerized Maintenance Management System (CMMS) relies on accurate, well-organized data ...
18 Feb 2025
In an era where technology drives operational efficiency, Computerized Maintenance Management ...
14 Feb 2025
A Computerized Maintenance Management System (CMMS) is a key component of modern maintenance ...
13 Feb 2025
Introduction Maintenance management is the foundation of maintenance operations in industries ...
11 Feb 2025
Introduction A Computerized Maintenance Management System (CMMS) is software designed to help ...
7 Feb 2025