- Case Studies
- Southern Carton Company
Quick and seamless CMMS adoption at Southern Carton

Company Size: 50 Employees
Industry: Manufacturing; Packaging & Containers
Location: Lewisburg, Tennessee
Number of users: Approx. 5 Users
Using Click Maint since: August 2024
About Southern Carton Company
Southern Carton Company, established in 1977, is a leading provider of corrugated box manufacturing solutions located in Lewisburg, Tennessee. With a team of approximately 50 employees, the company specializes in producing high-quality, custom corrugated packaging for a wide range of industries. Southern Carton is committed to delivering reliable, cost-effective packaging solutions that meet the unique needs of their clients. Through decades of experience, they have built a strong reputation for quality, service, and innovation, continuously adapting to market demands and striving for excellence in all aspects of their operations.
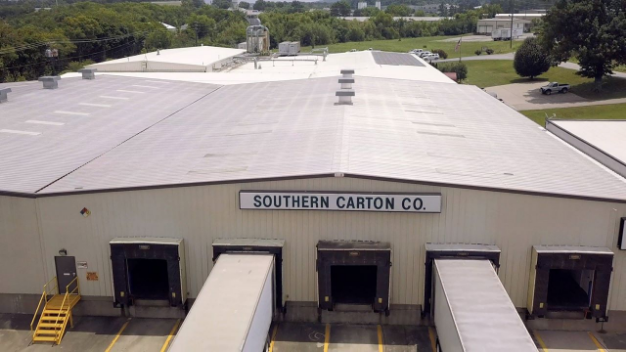
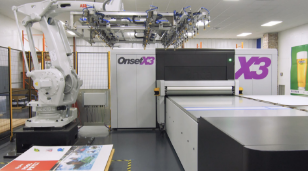
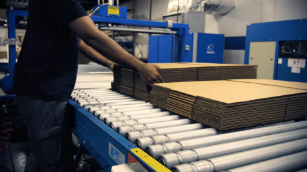
Maintenance Challenges
Before using Click Maint, Southern Carton Company relied on manual processes to track maintenance and repairs, which led to several challenges. The company struggled with tracking repairs, especially recurring issues with machinery. Communication breakdowns, such as “he said/she said” or “I told so and so,” made it difficult to ensure that all maintenance activities were documented and addressed. Additionally, keeping track of parts for each machine was a challenge, leading to inefficiencies and delays.
These challenges significantly impacted operations and productivity. The lack of a proper maintenance tracking system at Southern Carton Company led to significant operational inefficiencies. Without proper documentation, many maintenance tasks would fall through the cracks, resulting in unaddressed issues that caused downtime and disrupted production schedules. The lack of a clear record system also meant it was harder to track the performance of equipment, leading to preventable breakdowns that could affect overall efficiency and increase costs.
Without documentation, critical maintenance tasks were often overlooked, resulting in recurring equipment failures and unplanned downtime. When a machine broke down, delays in identifying previous repairs or ordering the right parts extended the time it took to get production back on track. The absence of a centralized record also made it difficult to detect patterns in machinery failures, preventing proactive maintenance and leading to costly, repetitive breakdowns. Additionally, miscommunication between team members meant that urgent repairs were sometimes delayed or forgotten, further impacting productivity. These inefficiencies not only slowed operations but also increased maintenance costs, as emergency repairs and extended downtime disrupted workflow and led to lost production time.
Why Click Maint?
Southern Carton Company chose Click Maint primarily for its affordability and ease of implementation. The company needed a maintenance management solution that was both cost-effective and simple to integrate into daily operations without causing disruptions. Click Maint checked all the boxes, offering a user-friendly platform that streamlined maintenance processes from day one.
One of the most impactful features has been the mobile app, which allows team members to request work orders directly from their phones. The ability to upload pictures of issues or specific parts has significantly improved communication and troubleshooting, ensuring that maintenance tasks are handled efficiently and with the right resources.
The implementation process was smooth and required minimal time investment. The Click Maint team provided exceptional support, guiding Southern Carton through onboarding with hands-on assistance. Weekly meetings during the first few months were particularly valuable, helping the team get fully up to speed and ensuring a seamless transition to the new system. With Click Maint, Southern Carton has gained a powerful tool that enhances maintenance coordination, reduces downtime, and improves overall operational efficiency.
Outcomes and Benefits
Since implementing Click Maint, Southern Carton Company has experienced improved organization and efficiency in its maintenance operations. Work orders are now tracked systematically, ensuring that tasks are completed on time, with only a few delays due to waiting on parts. The streamlined process has minimized miscommunications and made it easier to manage ongoing maintenance tasks.
One of the most notable successes has been how quickly and seamlessly the team adopted the new system. Employees and requesters have embraced Click Maint, appreciating the ease of submitting work orders. The mobile-friendly interface and ability to attach images have made reporting issues more intuitive, leading to faster response times and improved maintenance workflows. The transition to Click Maint has not only enhanced operational efficiency but also fostered better communication and accountability within the team, ultimately contributing to a more proactive and organized approach to maintenance management.
“Click Maint was the missing link to our maintenance department, from tracking to giving the maintenance team the insight of what to expect before they get to a breakdown.”
John McClenney
Southern Carton
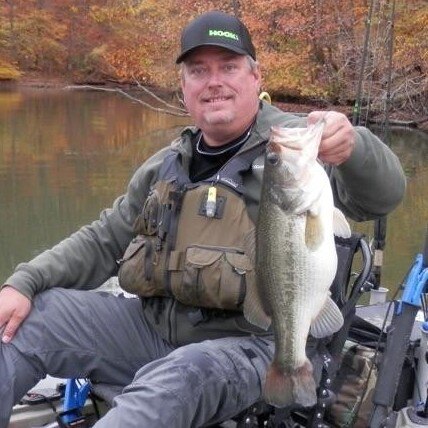
More Success Stories
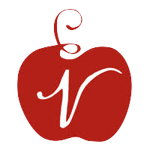
Virtue Cider
Intuitive CMMS design has made day-to-day operations smoother
“Click Maint has been outstanding for managing maintenance in our facility.”
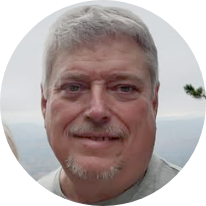
Steve Fries
Maintenance Manager
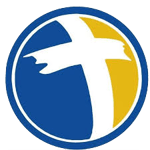
Trinity Lutheran
No more lost notes and scattered spreadsheets
“Click Maint has been a game-changer for our maintenance operations. It's interface and features have streamlined our workflow and productivity.”
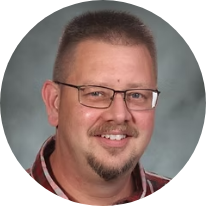
Richard Hackbarth
Facilities & Maintenance Manager
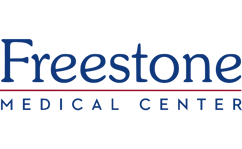
Freestone Medical Center
Maintenance technician’s workflow goes from physical to digital
“Click Maint has the most supportive team and is the easiest work order system to use, saving staff so much time. Because it is so easy and fast, they are all willing to use the system!”
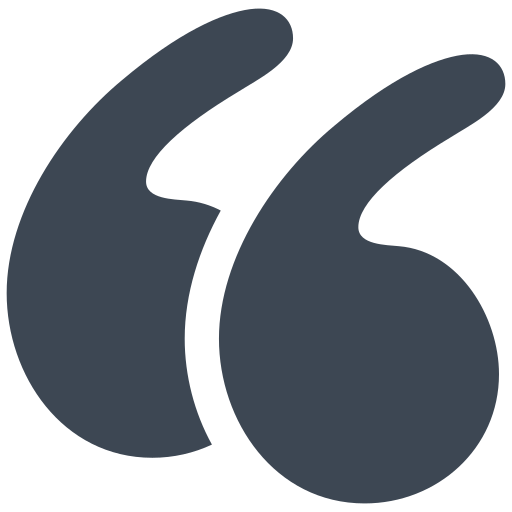
Maegen Bass
Admin Assistant
TRUSTED BY THOUSANDS OF MAINTENANCE AND FACILITIES PROFESSIONALS
Leading the way to a better future for Maintenance and Reliability
Click Maint’s objective is to offer organizations a CMMS that’s simple and easy to implement so that users get value fast. Our goal is to eliminate a lot of the friction that companies face when implementing maintenance management software.