Maintenance Knowledge at Your Fingertips
Print or Download for Offline Access!
Equipment Management
Achieving Equipment Performance Excellence
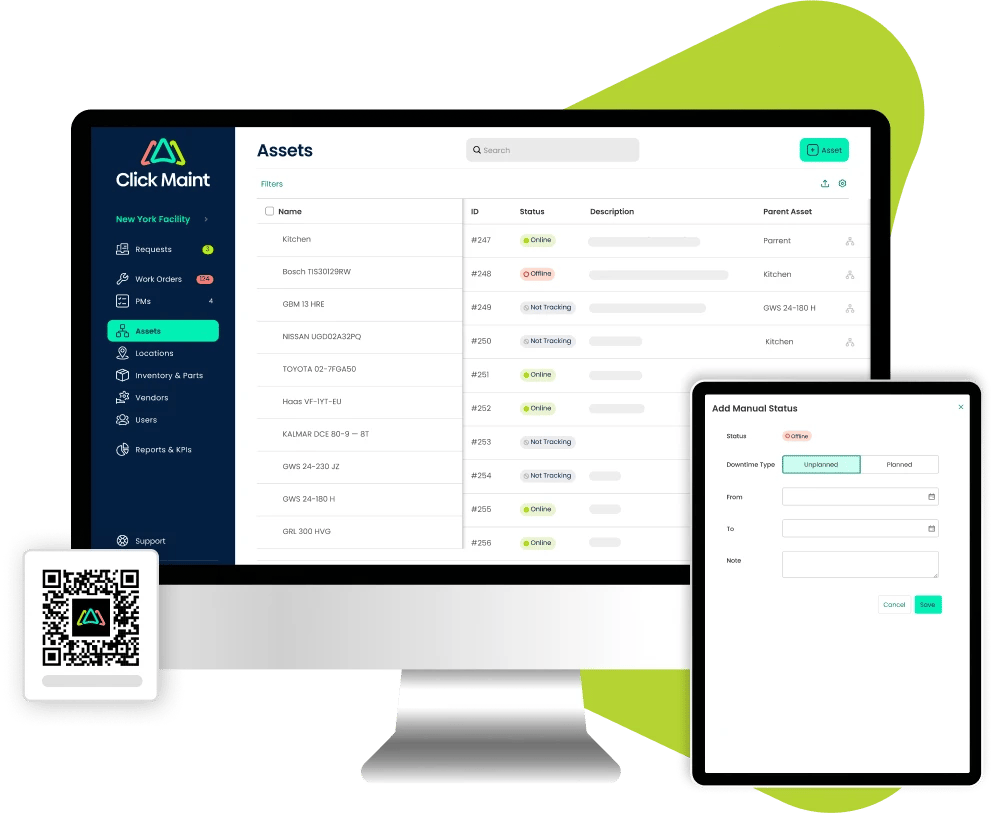
TABLE OF CONTENTS
WHAT IS EQUIPMENT MANAGEMENT?
Equipment management* is the process of acquiring, deploying, maintaining, optimizing the use of equipment and retiring equipment within an organization. It involves a number of tasks, including: purchasing, maintenance, repair, inventory tracking, transportation, storage, liquidation, and ordering new equipment. Essentially, it involves managing the entire lifecycle of equipment, from procurement to disposal, ensuring optimal performance, cost-efficiency, and compliance with safety regulations while maximizing return on investment (ROI).
Effective equipment management is crucial for businesses and industries that rely on equipment to operate efficiently. It is relevant for many industries including manufacturing, construction, healthcare, transportation, and others. It ensures that equipment is properly maintained, optimized for productivity, and aligned with operational goals.
THE NEED FOR EQUIPMENT MANAGEMENT
According to Aberdeen Research, unplanned downtime in manufacturing can cost a company as much as $260,000 an hour making it essential. Effective equipment management is crucial due to a number of challenges that organizations face in ensuring smooth operations and maximizing equipment utilization. These challenges include:
Maintenance and Repair
Timely and efficient maintenance is critical to prevent equipment breakdowns. However, scheduling and coordinating maintenance activities presents challenges, particularly when dealing with a diverse range of equipment.
Equipment Utilization
Many organizations struggle with underutilization or inefficient allocation of equipment, leading to unnecessary expenses and reduced productivity.
Asset Tracking & Inventory Management
Keeping track of numerous assets, their location, and maintenance status is complicated, especially for large organizations or those with assets across multiple locations.
Compliance & Safety
Equipment management involves adhering to safety standards, regulatory requirements, and ensuring equipment compliance, which is demanding, particularly in highly regulated industries.
Equipment Lifecycle Planning
Efficient asset lifecycle management, from acquisition to retirement, requires strategic decision-making and consideration of factors such as technological advancements, obsolescence, and depreciation.
Addressing these challenges bridges the gap between meeting diverse organizational needs and reaping the benefits of optimized operations, increased productivity, and improved safety.
See how affordable Click Maint CMMS is
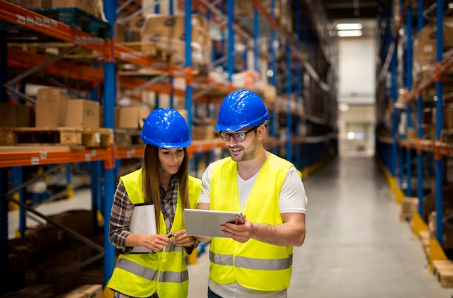
INDUSTRY-SPECIFIC BENEFITS OF EQUIPMENT MANAGEMENT
Equipment management plays an important role across various sectors, ensuring smooth operation and optimal performance of assets. The following are industry-specific benefits of equipment management:
Construction
In the construction industry, effective equipment management is vital to ensure timely project completion and cost control. Proper maintenance and tracking of construction equipment such as excavators, bulldozers, cranes, and concrete mixers help maximize their uptime and productivity. Equipment management also ensures compliance with safety regulations, reduces equipment downtime, and improves project efficiency.
Manufacturing
Equipment management is essential in the manufacturing industry to optimize production processes and maintain high-quality standards. Efficient maintenance and servicing of manufacturing equipment, such as assembly lines, CNC machines, presses, and robotic systems, help minimize unplanned downtime and enhance equipment effectiveness. Effective equipment tracking and inventory management also contribute to streamlined production operations and inventory control.
Healthcare Sector
In the healthcare sector, equipment management plays a critical role in ensuring patient care and safety. Proper maintenance and calibration of medical devices and instruments, including diagnostic equipment (MRI machines, X-ray machines), surgical instruments, and patient monitoring systems, are essential for accurate diagnosis and treatment. Equipment tracking and documentation facilitate efficient asset management, reduce equipment disruption, and ensure compliance with regulatory standards.
Transportation & Logistics
Equipment management is crucial in the transportation industry to maintain the reliability and safety of vehicles and infrastructure. Regular maintenance and inspections of transportation equipment, such as automobiles, trucks, aircraft, and ships, help prevent breakdowns and accidents. Effective equipment tracking and documentation assist in optimizing fleet management and reducing operational costs while ensuring compliance with regulatory requirements.
Other Sectors
Equipment management extends to other industries and sectors. In agriculture, equipment management for tractors, harvesters, and irrigation systems helps maximize productivity and minimize downtime during critical farming seasons. Energy equipment management focuses on ensuring reliable and efficient operation of generators, turbines, and power transmission systems. Industries like mining, oil and gas, and telecommunications also require specialized equipment management to maintain operational efficiency, safety, and compliance.
By implementing robust equipment management practices tailored to industry specific needs, organizations can enhance productivity, reduce costs, ensure regulatory compliance, and deliver higher-quality services.
Experience Click Maint CMMS now
30-Day Free Trial
No Credit Card needed.
Instant access to all features & modules with an optional live walk-through with a Click Maint expert
Book a live Demo
In this 30-minute demo, see firsthand how our easy CMMS can streamline your operations, enhance productivity, and reduce downtime.
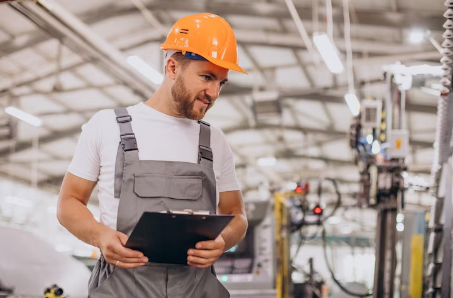
GETTING STARTED WITH EQUIPMENT MANAGEMENT
Understanding the specific requirements and nuances that shape an organizations’ equipment management strategy is required to get started with equipment management. One of the most critical steps to better equipment management is creating a reliable inventory of equipment.
Creating and Maintaining an Equipment Inventory
To establish a well-organized and reliable equipment inventory, organizations should follow these essential steps:
Identify and Track Equipment
Begin by conducting a comprehensive equipment audit to identify and list all equipment owned by the organization. Capture relevant details for each item, such as make, asset ID, model, serial number, life expectancy, acquisition date, and any other relevant information. This initial step lays the foundation for accurate equipment tracking.
Use Technology and Software
Implementing technology solutions such as a CMMS software can streamline equipment inventory management. Utilize barcode or RFID tagging systems to track equipment movements and updates in real-time. This software helps to automate data entry, generate reports, and maintain an up-to-date equipment database.
Establish a Standardized Equipment Coding System
Implement a standardized equipment coding system to categorize and label each item in the inventory. This coding system should be consistent and easy to understand for all staff members. It could include a combination of alphanumeric codes, such as equipment type, location, and unique identification numbers. This system facilitates quick identification, reduces errors, and simplifies inventory management.
By implementing these steps, organizations can create and maintain an accurate and reliable equipment inventory. This ensures effective resource management, streamlined operations, and informed decision-making when it comes to equipment utilization, maintenance, and budgeting.
Key Characteristics and Considerations for Each Equipment Type
Different equipment types possess unique characteristics and considerations that need to be taken into account for effective equipment management. The following are key factors to consider for each equipment type:
- Size and Capacity: Equipment size and capacity vary significantly across categories. It is essential to understand the dimensions, weight-bearing capacity, and space requirements of each equipment type to ensure proper storage, transportation, and operational compatibility.
- Complexity and Technology Requirements: Some equipment, such as advanced manufacturing machinery or IT systems, have complex technological components. Understanding the technology requirements, including software integration, maintenance of control systems, and connectivity considerations, is crucial.
- Maintenance and Servicing Needs: Construction and manufacturing equipment require routine inspections, lubrication, and component replacements. Healthcare equipment demand strict adherence to calibration, sterilization, and regulatory guidelines. Consider the maintenance schedules, spare parts availability, and specialized expertise needed for each equipment type.
- Lifespan and Depreciation Factors: The lifespan of equipment varies depending on usage, maintenance practices, and technological advancements. Assessing the expected lifespan and depreciation factors for each equipment type is important for financial planning, replacement strategies, and determining the equipment's overall value.
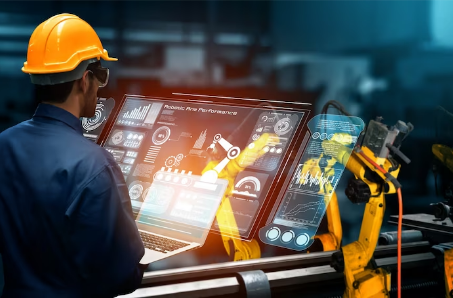
EQUIPMENT TRACKING AND DOCUMENTATION
Importance of Equipment Tracking and Documentation
Efficient equipment tracking and documentation are vital components of effective equipment management. By implementing robust tracking and documentation practices, organizations can reap the following benefits:
Asset Visibility and Accountability
Equipment tracking provides real-time visibility into the location, status, and condition of assets. It ensures accountability and minimizes the risk of loss, theft, or misplacement.
Operational Efficiency
Accurate equipment documentation facilitates resource planning, scheduling, and allocation, ensuring that equipment is available when and where it is needed. This minimizes downtime, optimizes productivity, and reduces unnecessary costs.
Regulatory Compliance
Equipment tracking and documentation are essential for regulatory compliance. Many industries have specific regulations regarding equipment safety, maintenance, and calibration. By maintaining accurate records, organizations can demonstrate compliance and mitigate legal and safety risks.
Inventory Management Systems
To enhance equipment tracking and documentation processes, organizations can leverage inventory management software like a CMMS or EAM. These tools offer a range of features and capabilities designed to streamline operations and improve visibility. Consider the following aspects of equipment tracking software:
- Features and Capabilities of Equipment Tracking Software: Equipment tracking software provides functionalities such as asset identification, location tracking, maintenance scheduling, and reporting. It allows for centralized data storage, automated record updates, and real-time visibility into equipment status.
- Barcoding, RFID, and Other Identification Methods: Equipment tracking software often integrates with and or generates identification methods like barcodes, QR codes or RFID (Radio Frequency Identification). These technologies enable efficient scanning and data capture, ensuring accurate and reliable tracking of equipment throughout its lifecycle.
- Integration with Other Management Systems: Equipment tracking software often integrates with other management systems, such as Enterprise Resource Planning (ERP) or Computerized Maintenance Management Systems (CMMS). Integration enables seamless data exchange, ensuring equipment information is synchronized across multiple platforms.
Maintenance and Service Records
Recording and maintaining comprehensive maintenance and service records are essential for effective equipment management. Consider the following aspects of maintenance and service documentation:
- Record Routine Maintenance Activities: Documentation of routine maintenance activities, such as inspections, lubrication, and calibration is essential. These records provide a history of maintenance performed that helps ensure equipment stays in optimal condition and minimizes the risk of breakdowns.
- Track Repairs and Spare Parts Usage: When repairs are necessary, tracking repair activities and spare parts usage is vital. Detailed records of repairs performed, parts replaced, and associated costs help analyze equipment performance, identify trends, and improve maintenance strategies.
- Document Warranties and Service Contracts: Keeping records of warranties and service contracts for each equipment item is important. This documentation ensures that equipment remains under warranty coverage and helps manage service agreements effectively. They also provide valuable information for budgeting, future planning, and decision-making regarding equipment replacement and upgrades.
By emphasizing equipment tracking and documentation, organizations can maximize operational efficiency and make informed decisions regarding maintenance, repairs, and replacements. Utilizing inventory management systems, integrating with other applications, and maintaining comprehensive records further enhances the effectiveness of equipment management practices.
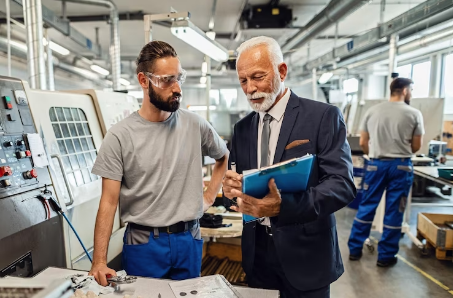
PREVENTIVE MAINTENANCE AND INSPECTION FOR EQUIPMENT MANAGEMENT
Preventive maintenance is a proactive approach to equipment management that focuses on scheduled maintenance tasks and inspections to prevent equipment failures and optimize performance. Key benefits of implementing preventive maintenance practices include increased equipment reliability, extended equipment lifespan, and improved safety to name a few.
Develop a Preventive Maintenance Plan
To establish an effective preventive maintenance plan, organizations should follow these steps. A preventive maintenance software can enable such a plan.
Identify Critical Equipment and Components
Identify the equipment and components that are critical to the organization's operations. Focus on assets that, if they fail, would significantly impact productivity, safety, or customer satisfaction.
Establish Maintenance Schedules and Checklists
Create a maintenance schedule outlining the frequency and specific tasks to be performed. Develop checklists that detail step-by-step instructions for each maintenance activity. This ensures consistency and adherence to maintenance protocols.
Conduct Regular Inspections and Assessments
Regular inspections are essential to identify potential issues and assess equipment condition. Inspections may include visual checks, fluid analysis, lubrication, and performance testing. Document inspection findings and track any abnormalities or areas that require attention.
Predictive Maintenance
Implement predictive maintenance to complement preventive maintenance efforts. Techniques such as vibration analysis, thermography, and oil analysis help detect early signs of equipment deterioration and guide maintenance decisions.
Equipment Calibration and Testing
Proper equipment calibration and testing are critical to maintaining accurate and reliable measurements. Calibration ensures that equipment readings and measurements are accurate and consistent. It is especially crucial for equipment used in scientific research, manufacturing, and quality control processes where precise measurements are required.
- Create Calibration Schedules and Procedures: Develop calibration schedules based on manufacturer recommendations, industry standards, and regulatory requirements. Establish procedures for performing calibrations, including the use of reference standards, calibration intervals, and documentation of calibration activities.
- Document Calibration Results: Maintain thorough records of calibration activities, including calibration dates, results, and any adjustments made. Documentation should also include traceability to calibration standards and certificates to demonstrate compliance with quality assurance requirements.
A well-structured preventive maintenance program, coupled with calibration and testing protocols, contributes to a safe, reliable, and productive work environment.
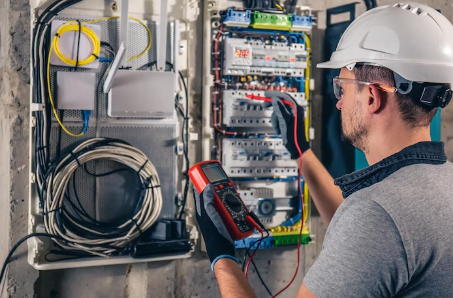
EQUIPMENT REPAIR AND TROUBLESHOOTING
Identify Repair Needs and Prioritize
When equipment issues arise, it is important to assess their impact on operations and prioritize repair needs accordingly. Factors to consider include the severity of the issue, the equipment's criticality to operations, safety implications, and potential downtime. Promptly identifying and prioritizing repair needs helps allocate resources effectively and minimize disruptions.
In-house vs. Outsourced Repairs
Determining whether to handle repairs in-house or outsource them depends on factors such as the organization's capabilities, expertise, equipment complexity, and cost considerations. In-house repairs provide control, faster response times, and cost savings for simple issues. However, outsourcing repairs may be beneficial for specialized equipment or complex issues that require specific expertise or tools.
According to a maintenance management survey, 76.06% of companies outsource services related to preventive and corrective activities.
Spare Parts Management and Inventory Control
Efficient management of spare parts is crucial to minimize equipment downtime and ensure timely repairs.
Stock Critical Spare Parts
Identify critical spare parts for each equipment item based on historical failure rates, lead times for ordering, and the impact on operations. Keep sufficient stock levels of these parts to ensure their availability when needed, reducing downtime and improving repair turnaround times.
Establish Reorder Points and Lead Times
Determine reorder points and lead times for stock spare parts to ensure they are replenished before stock depletes. This involves monitoring stock levels, tracking usage patterns, and establishing relationships with reliable suppliers to minimize lead times.
Making informed decisions about in-house or outsourced repairs and implementing efficient spare parts management processes further enhances equipment repair capabilities and ensures uninterrupted operations.
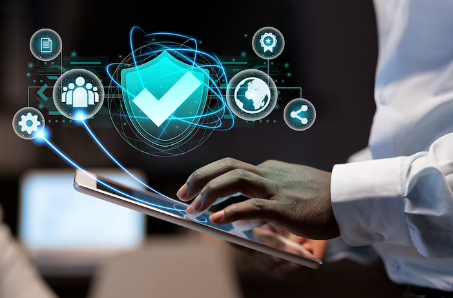
SAFETY AND COMPLIANCE IN EQUIPMENT MANAGEMENT
Regulatory and Legal Considerations
When managing equipment, organizations must adhere to various regulatory and legal requirements to ensure the safety of personnel and customers, protect the environment, and comply with industry-specific standards. Key considerations include:
Environmental Regulations
Organizations must comply with environmental regulations pertaining to equipment operation, waste management, emissions control, and the handling of hazardous substances. Compliance helps minimize the environmental impact and ensures responsible practices.
Industry-Specific Compliance Standards
Different sectors have specific compliance standards that organizations must adhere to. Common industry-specific compliance considerations include:
Compliance considerations for the Manufacturing Industry:
- Occupational Safety and Health Administration (OSHA) standards for worker safety.
- Environmental regulations for waste management and pollution control.
- Compliance with industry-specific standards such as ISO 9001 for quality management.
Compliance considerations for the Healthcare Sector:
- Adherence to healthcare regulations, including HIPAA (Health Insurance Portability and Accountability Act) for data privacy and security.
- Compliance with medical device regulations, such as FDA (U.S. Food and Drug Administration) guidelines for equipment safety and efficacy.
- Accreditation requirements for healthcare facilities, such as Joint Commission standards.
Compliance considerations for the Construction Industry:
- Compliance with OSHA regulations to ensure worker safety on construction sites.
- Adherence to building codes and regulations specific to the region or country.
- Compliance with environmental regulations for construction waste management.
Compliance considerations for Transportation Industry:
- Compliance with transportation safety regulations, such as the Federal Motor Carrier Safety Administration (FMCSA) regulations for commercial vehicles.
- Adherence to aviation safety standards set by regulatory bodies like the Federal Aviation Administration (FAA) or International Civil Aviation Organization (ICAO).
- Compliance with maritime regulations, including International Maritime Organization (IMO) standards for ship safety and environmental protection.
Safety Protocols and Training for Equipment Operators
To maintain a safe work environment, organizations should establish comprehensive safety protocols and provide adequate training for equipment operators. These include:
Safety Protocols
Develop and implement safety protocols specific to types of equipment. These protocols should cover safe operating procedures, emergency response plans, personal protective equipment (PPE) requirements, and equipment-specific hazards.
Operator Training
Provide thorough training programs to equip equipment operators with the knowledge and skills necessary to operate equipment safely. Training should cover equipment functionality, maintenance procedures, safety precautions, and hazard awareness.
Regular Inspections and Audits for Compliance
Regular inspections and audits are vital for ensuring ongoing compliance with safety regulations and identifying potential hazards or non-compliant practices. Key considerations include:
Routine Equipment Inspections
Conduct regular inspections of equipment to identify any maintenance or safety issues. Inspections should cover areas such as electrical systems, moving parts, safety guards, and overall equipment condition.
Compliance Audits
Periodically conduct compliance audits to assess adherence to safety regulations and industry standards. Audits may involve reviewing documentation, observing equipment operations, and interviewing personnel to ensure compliance with safety protocols.
Documentation of Safety Procedures and Incidents
Maintaining accurate documentation of safety procedures and incidents is essential for record-keeping, incident analysis, and demonstrating compliance. The following should be documented:
Safety Procedures
Document all safety protocols, including standard operating procedures (SOPs), maintenance checklists, safety training materials, and emergency response plans. Ensure accessibility to relevant personnel and regularly update these documents as needed.
Incident Reports
Document and investigate all safety incidents, accidents, close calls, and equipment failures. Incident reports should be detailed including date, time, location, individuals involved, nature of the incident, and any corrective actions taken.
Adhering to regulatory requirements, implementing safety protocols and training, conducting inspections and audits, and documenting safety procedures and incidents contribute to a safe work environment that complies with regulatory standards.
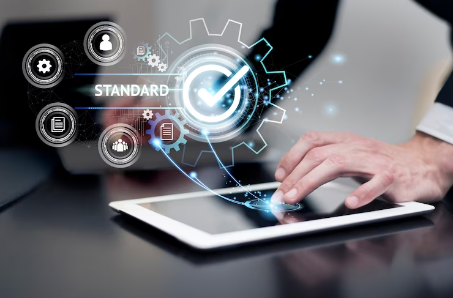
LEVERAGING TECHNOLOGY FOR EQUIPMENT MANAGEMENT
Lucky for us, there is an abundance of new technology available that helps maintenance professionals manage critical assets. Specialized software designed for equipment management enables organizations to track, monitor, and maintain equipment throughout its lifecycle. These solutions offer features such as asset tracking, maintenance scheduling, work order management, parts and inventory management and robust reporting and analytics.
Features and Benefits of Equipment Management Software
Equipment maintenance software offers a wide range of features and benefits that enhance the efficiency and effectiveness of equipment management processes. Some key features include:
- Asset Tracking: Software allows organizations to track equipment location, status, and usage history. It provides visibility into equipment availability and helps prevent loss or theft. Many asset management software platforms are capable of tracking equipment downtime, stock-levels of necessary parts and visibility into asset health.
- Maintenance Scheduling: Software facilitates the scheduling and tracking of preventive maintenance tasks, ensuring equipment is serviced at regular intervals to prevent breakdowns and extend its lifespan. Work Order Management: The software streamlines the process of generating and tracking work orders for equipment repairs, inspections, or maintenance tasks. It ensures timely completion of work and provides a centralized system for tracking progress.
- Reporting and Analytics: Software generates detailed reports and analytics on equipment performance, maintenance history, and costs. These insights enable data-driven decisions and help optimize equipment management strategies.
Select and Implement the Right Software Solution
When selecting equipment management software, it’s important to consider the specific needs and requirements of the organization. Key factors to consider include:
Scalability
Ensure the software can accommodate the organization's current and future equipment inventory, being able to scale as the business grows.
Integration
Determine if the software can integrate with other systems, such as enterprise resource planning (ERP), accounting or HR systems, or other business applications to streamline data sharing.
Ease of Use
Choose software that is user-friendly and intuitive like Click Maint and make it easy for equipment managers and operators to navigate and utilize its features effectively.
Support and Training
Assess the level of support and training provided by the software vendor to ensure a smooth implementation process and ongoing assistance.
Innovations in Equipment Management Technology
- Internet of Things (IoT) and Equipment Connectivity: IoT is revolutionizing equipment management by enabling real-time data collection and remote monitoring. IoT sensors and devices attached to equipment collect data on various parameters, such as temperature, vibration, and energy consumption. This data is transmitted to a centralized system such as CMMS, where workflows are triggered based on sensor readings.
- Predictive Analytics and Machine Learning Applications: Predictive analytics and machine learning applications are increasingly being utilized in equipment management to optimize maintenance strategies and enhance equipment performance. These applications analyze historical data, equipment sensor readings, and maintenance records to identify patterns and predict potential failures. By leveraging these insights, organizations can schedule maintenance activities more effectively, reduce downtime, and lower maintenance costs.
- Augmented and Virtual Reality (AR/VR) Applications: AR/VR technologies offer immersive experiences and visualization capabilities in equipment management. These technologies facilitate remote collaboration, training simulations, and virtual equipment inspections, enhancing productivity, safety, and training effectiveness. According to IDC’s Spending Guide, it is projected that about $4.1 billion will be invested in augmented and virtual reality (AR/VR) for industrial maintenance by 2024.
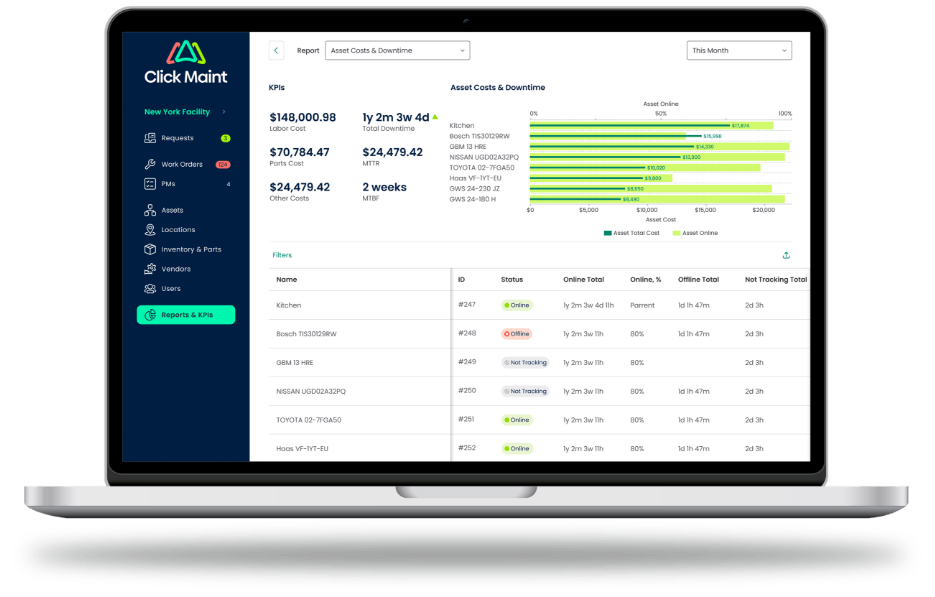
DATA ANALYSIS AND PERFORMANCE METRICS
Importance of Data Analysis in Equipment Management
Data analysis allows organizations to gain insights into equipment performance, identify trends and patterns, and make data-driven decisions. Data analysis helps equipment and asset managers with;
Performance Monitoring
Data analysis enables organizations to monitor equipment performance in real-time, track key metrics, and identify deviations from expected performance. This helps detect potential issues early and take proactive measures to prevent equipment failures or downtime.
Optimization of Maintenance Practices
By analyzing equipment data, organizations can optimize maintenance practices. Data-driven insights allow for the development of preventive maintenance schedules, identification of optimal maintenance intervals, and improved allocation of maintenance resources.
Cost Optimization
Data analysis helps organizations identify cost-saving opportunities related to equipment management. By analyzing maintenance records, equipment usage patterns, and performance metrics, organizations can optimize maintenance activities, reduce unplanned downtime, and improve equipment reliability and efficiency.
Key Performance Metrics for Evaluating Equipment Performance
To assess equipment performance, organizations utilize various key performance metrics or indicators (KPIs) that provide valuable insights into equipment reliability, availability, and overall effectiveness. Some KPIs include:
- Equipment Uptime and Availability: Uptime and availability metrics measure the percentage of time equipment is operational and available for use. These metrics indicate the reliability and accessibility of equipment and are crucial for minimizing downtime and optimizing productivity.
- Mean Time Between Failures (MTBF) and Mean Time to Repair (MTTR): MTBF measures the average time between equipment failures, while MTTR represents the average time required to repair equipment after a failure. These metrics help organizations understand equipment reliability, assess repair efficiency, and identify opportunities for improvement.
- Overall Equipment Effectiveness (OEE): OEE is a metric that assesses the performance of equipment. It takes into account factors such as availability, performance efficiency, and quality to provide a holistic view of equipment effectiveness. OEE helps organizations identify areas for improvement and optimize equipment performance.
Using Data for Predictive Maintenance and Decision-Making
Data analysis enables organizations to implement predictive maintenance strategies and make informed decisions regarding equipment management. Some key applications include:
- Trend Analysis and Anomaly Detection: By analyzing historical data, organizations can identify trends and patterns in equipment performance. Data analysis techniques such as trend analysis and anomaly detection help predict potential failures, allowing for timely preventive maintenance actions and reducing unplanned downtime.
- Equipment Replacement and Upgrade Strategies: Data analysis aids in determining optimal equipment replacement or upgrade strategies. By analyzing equipment performance metrics, cost of repairs, and overall lifecycle costs, organizations can make informed decisions regarding equipment replacement, upgrades, or retrofits.
The ability to monitor performance metrics, implement predictive maintenance strategies, and assess equipment replacement strategies contributes to increased efficiency, reduced downtime, and enhanced overall equipment performance.
TRAINING AND SKILL DEVELOPMENT
Identifying training needs and providing appropriate programs help develop the necessary skills and knowledge for effective and safe equipment management.
Equipment-Specific Training Programs
Organizations should develop equipment-specific training programs tailored to the needs of operators and technicians. These programs can cover a range of topics, including:
Equipment-Specific Safety Training
Safety training should focus on the unique risks associated with operating or maintaining each type of equipment. It should cover safety protocols, hazard identification, emergency procedures, and the proper use of personal protective equipment (PPE).
Operation and Maintenance Training
Equipment operation and maintenance training should provide in-depth knowledge of equipment controls, functions, maintenance tasks, and best practices. This training ensures operators and technicians understand the equipment's capabilities and perform maintenance tasks effectively.
Troubleshooting and Repair Training
Equipment troubleshooting and repair training should equip technicians with the skills to diagnose equipment issues, perform necessary repairs, and restore equipment functionality. This training includes hands-on exercises, case studies, and practical applications.
Continuous Learning and Skill Development Opportunities
To keep up with evolving technology and industry practices, organizations should invest in continuous learning and skill development opportunities for equipment operators and technicians. Some options include:
- Industry Conferences and Workshops: Encourage attendance at industry conferences, workshops, and seminars focused on equipment management. These events provide access to the latest trends, technologies, and best practices in the field, fostering professional growth and knowledge sharing.
- Online Resources and e-Learning Platforms: Utilize online resources and e-learning platforms to offer self-paced training modules, webinars, and video tutorials. These resources allow operators and technicians to enhance their skills conveniently and access up-to-date information on equipment management practices. e-Learning platforms and onlines resources are economical as well.
Investing in training and skill development ensures that operators and technicians have the knowledge and expertise necessary to handle equipment safely and effectively.
Embracing industry-specific strategies, leveraging new technology and promoting a culture of continuous improvement helps businesses not only advance their equipment management practices but also stay ahead of the competition in an ever-evolving landscape. Investing in the management and maintenance of equipment today yields long-term benefits tomorrow, paving the way for sustainable growth, increased efficiency, and a safer work environment. The future of equipment management is bright, and organizations that seize opportunities are set to become industry leaders.
Proactive Maintenance with Equipment Maintenance Software
Instead of reacting to equipment failures, organizations can schedule maintenance activities based on real-time data, usage patterns, or manufacturer recommendations. This significantly extends the lifespan of assets, reduces downtime, and minimizes repair costs. By predicting potential issues before they lead to breakdowns, equipment maintenance software ensures that your operations continue running smoothly, ultimately saving time and boosting productivity.
Additionally, real-time equipment performance tracking allows for better decision-making by providing instant feedback on the health and efficiency of each asset. Managers and technicians can access dashboards that display key metrics like usage, wear-and-tear, and energy consumption, which can be invaluable for optimizing resource allocation. These insights empower businesses to maintain operational efficiency, reduce waste, and stay compliant with industry regulations.
Finally, seamless integration with mobile devices ensures that maintenance teams can stay connected in the field. Through mobile apps, technicians can receive instant alerts about equipment issues, update maintenance logs, and access repair histories from any location. This mobility improves response times, reduces paperwork, and enhances collaboration across teams. Whether you're managing a fleet of vehicles, manufacturing machinery, or any type of equipment, this software provides a centralized platform to keep everything running at peak performance.