Inventory Management
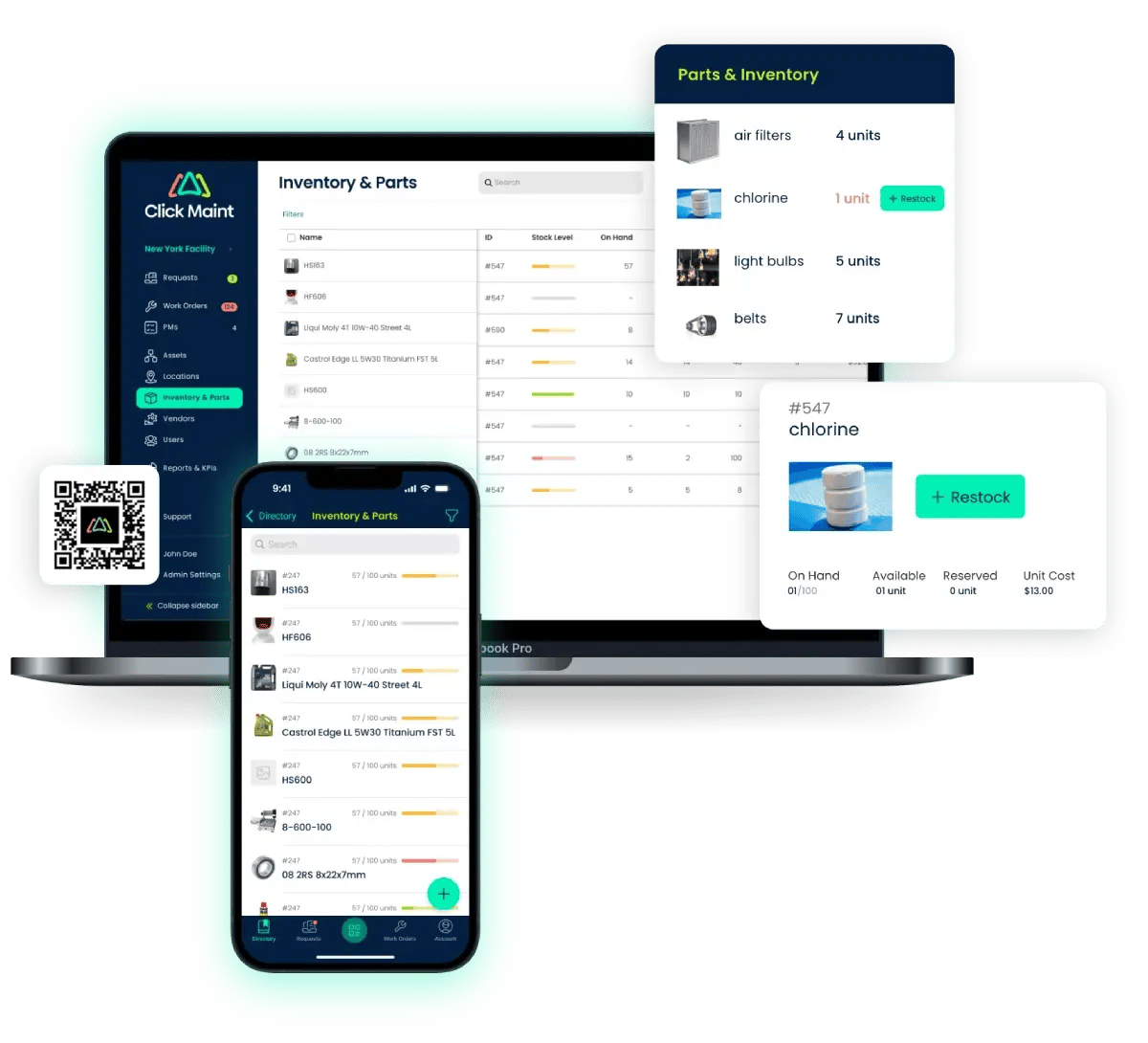
Maintenance Knowledge at Your Fingertips
Print or Download for Offline Access!
TABLE OF CONTENTS
- Significance of Inventory Management
- Minimizing Downtime
- Cost Control
- Efficient Repairs and Maintenance
- Improved Productivity
- Types of Maintenance Inventory
- Inventory Management Strategies for Maintenance
- 1. Preventive Maintenance
- 2. Predictive Maintenance
- 3. Condition-Based Monitoring
- 4. Just-in-Time (JIT) Inventory for Maintenance
- Inventory Optimization Techniques
- 1. ABC Analysis
- 2. Economic Order Quantity (EOQ)
- 3. Two-Bin System
- Inventory Tracking and Control Systems
- 1. CMMS (Computerized Maintenance Management System)
- 2. RFID and IoT Solutions
- 3. Barcoding and QR Code Scanning Systems
- Best Practices for Inventory Management in Maintenance Departments
- 1. Demand Forecasting for Maintenance
- 2. Vendor and Supplier Relationship Management
- 3. Maintenance Storeroom Organization
- 4. Inventory Audits and Cycle Counts
- 5. Standardization and Rationalization of Parts
- Challenges in Maintenance Inventory Management
- Balancing Stock Levels
- Spare Parts Obsolescence
- Budget Constraints
- Data Accuracy and Integration
- Future Trends in Inventory Management
- 3D Printing for Spare Parts
- Augmented Reality (AR) for Inventory Management Training
Inventory management in maintenance refers to the systematic control, organization, and optimization of spare parts, consumables, and materials essential for maintaining and repairing machinery, equipment, and infrastructure. Effective inventory management is an important aspect of maintenance operations that ensures that the right parts and materials are available at the right time to keep machinery, equipment, and facilities in optimal working condition.
SIGNIFICANCE OF INVENTORY MANAGEMENT
Minimizing Downtime
Inventory management helps prevent unplanned downtime by ensuring that critical spare parts are on hand when needed. This reduces the impact of unexpected equipment failures on production and services.
Cost Control
Properly managed inventory prevents overstocking and understocking, thus optimizing working capital. This leads to cost savings by reducing carrying costs and avoiding expensive rush orders.
Efficient Repairs and Maintenance
Maintenance professionals rely on a well-organized inventory system to quickly locate the right parts, tools, and materials for repairs and preventive maintenance tasks. This efficiency translates to faster turnaround times and improved equipment availability.
Improved Productivity
Inventory management allows maintenance teams to focus on core tasks rather than spending time searching for parts, managing shortages, and waiting for deliveries.
See how affordable Click Maint CMMS is
TYPES OF MAINTENANCE INVENTORY
- Vital for equipment operation
- Can cause significant downtime if unavailable
- Often expensive or with long lead times
- Minimizes equipment downtime
- Reduces production losses
- Ensures operational reliability
High
Long
Controlled environment, if necessary
Infrequent
Strong relationships often important
Risk of obsolescence
Predictive maintenance tools
- Prioritization: Identify and prioritize critical spare parts based on impact
- Safety Stock: Maintain safety stock levels
- Supplier Agreements: Establish agreements with suppliers for rapid delivery
- Predictive Maintenance: Implement predictive maintenance techniques
- Regularly consumed during maintenance and operations
- Not critical but essential for smooth operations
- Supports day-to-day maintenance activities
- improves efficiency and productivity
Low to Moderate
Short to Moderate
Dry, cool storage for some items
Frequent
Vendor relationships beneficial
Lower risk
Inventory tracking software
- Reorder Points: Set reorder points for consumables
- Usage Tracking: Implement systems to track usage
- Vendor Relationships: Maintain strong relationships with consumable suppliers
- Bulk Purchasing: Consider bulk purchasing for cost-effectiveness
- Uniquely associated with specific machinery or equipment
- May not be used elsewhere within the organization
- Enables rapid repairs and maintenance for specialized equipment
- Reduces downtime for critical machinery
Varies by item
Varies by item
Close proximity to associated machinery
As needed
Equipment-specific suppliers
Equipment-specific risk
Asset management software
- Documentation: Maintain detailed documentation specifying equipment association
- Inventory Location: Store close to associated machinery
- Scheduled Maintenance: Plan maintenance activities to coincide with availability
- Supports maintenance, repair, and operational activities
- Improves safety and efficiency
- Ensures a safe and efficient working environment for maintenance personnel
- Supports routine maintenance and repairs
Moderate
Moderate to Long
Dry, secure storage
Regularly
Vendor relationships essential
Lower risk
CMMS (Computerized Maintenance Management System)
- Categorization: Categorize MRO items based on function
- Regular Audits: Conduct regular audits of MRO inventory
- Vendor Relationships: Establish relationships with reliable MRO suppliers
- Inventory Visibility: Implement systems to track MRO usage and reorder points
- Vital for equipment operation
- Can cause significant downtime if unavailable
- Often expensive or with long lead times
- Minimizes equipment downtime
- Reduces production losses
- Ensures operational reliability
High
Long
Controlled environment, if necessary
Infrequent
Strong relationships often important
Risk of obsolescence
Predictive maintenance tools
- Prioritization: Identify and prioritize critical spare parts based on impact
- Safety Stock: Maintain safety stock levels
- Supplier Agreements: Establish agreements with suppliers for rapid delivery
- Predictive Maintenance: Implement predictive maintenance techniques
- Regularly consumed during maintenance and operations
- Not critical but essential for smooth operations
- Supports day-to-day maintenance activities
- improves efficiency and productivity
Low to Moderate
Short to Moderate
Dry, cool storage for some items
Frequent
Vendor relationships beneficial
Lower risk
Inventory tracking software
- Reorder Points: Set reorder points for consumables
- Usage Tracking: Implement systems to track usage
- Vendor Relationships: Maintain strong relationships with consumable suppliers
- Bulk Purchasing: Consider bulk purchasing for cost-effectiveness
- Uniquely associated with specific machinery or equipment
- May not be used elsewhere within the organization
- Enables rapid repairs and maintenance for specialized equipment
- Reduces downtime for critical machinery
Varies by item
Varies by item
Close proximity to associated machinery
As needed
Equipment-specific suppliers
Equipment-specific risk
Asset management software
- Documentation: Maintain detailed documentation specifying equipment association
- Inventory Location: Store close to associated machinery
- Scheduled Maintenance: Plan maintenance activities to coincide with availability
- Supports maintenance, repair, and operational activities
- Improves safety and efficiency
- Ensures a safe and efficient working environment for maintenance personnel
- Supports routine maintenance and repairs
Moderate
Moderate to Long
Dry, secure storage
Regularly
Vendor relationships essential
Lower risk
CMMS (Computerized Maintenance Management System)
- Categorization: Categorize MRO items based on function
- Regular Audits: Conduct regular audits of MRO inventory
- Vendor Relationships: Establish relationships with reliable MRO suppliers
- Inventory Visibility: Implement systems to track MRO usage and reorder points
MAINTENANCE STRATEGIES THAT BENEFIT FROM EFFECTIVE INVENTORY MANAGEMENT
Effective inventory management strategies are essential for optimizing maintenance operations.
1. Preventive Maintenance
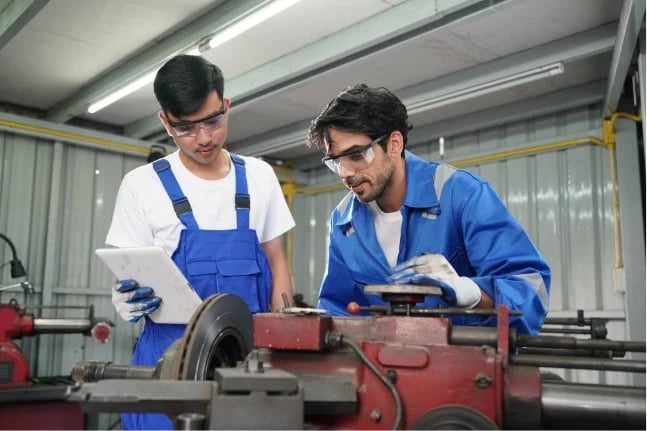
Preventive maintenance involves scheduled inspections and servicing to prevent equipment failures. When integrated with inventory control, it improves maintenance efficiency and cost-effectiveness:
- Scheduled Maintenance: Preventive maintenance schedules are known in advance, allowing for precise planning of inventory needs. Spare parts and materials can be procured and stocked in anticipation of upcoming maintenance tasks.
- Standardization: Standardize documenting and tracking spare parts and materials used in preventive maintenance procedures whenever possible. This simplifies inventory management by reducing the number of unique items in stock.
- Inventory Audits: Conduct regular audits to ensure that inventory aligns with preventive maintenance schedules. Identify and address discrepancies promptly to avoid delays in scheduled maintenance activities.
- Supplier Relationships: Develop strong relationships with suppliers to ensure fast deliveries of materials needed for preventive maintenance and repairs. Suppliers can be informed of maintenance schedules to streamline procurement.
- Asset Tracking: Implement asset tracking systems to monitor the usage and condition of spare parts and materials. This data helps with inventory replenishment decisions and prevents overstocking and understocking.
2. Predictive Maintenance

Predictive maintenance is a proactive approach that uses data and technology to predict when equipment or machinery is likely to fail, allowing maintenance to be performed just in time. This strategy has a significant impact on inventory management:
- Reduced Spare Parts Consumption: Predictive maintenance reduces the frequency of unscheduled breakdowns. With fewer emergency repairs, the consumption of critical spare parts decreases. Inventory turnover improves, and capital tied up in spare parts is reduced.
- Optimized Inventory Levels: As maintenance becomes more predictable, inventory levels can be optimized. Rather than stockpiling excess spare parts for unforeseen failures, inventory can be maintained at levels aligned with actual usage patterns.
- Cost Savings: Lower consumption and optimized inventory levels result in cost savings. Maintenance departments can allocate budgets more efficiently, investing in critical spare parts strategically rather than haphazardly.
3. Condition-Based Monitoring
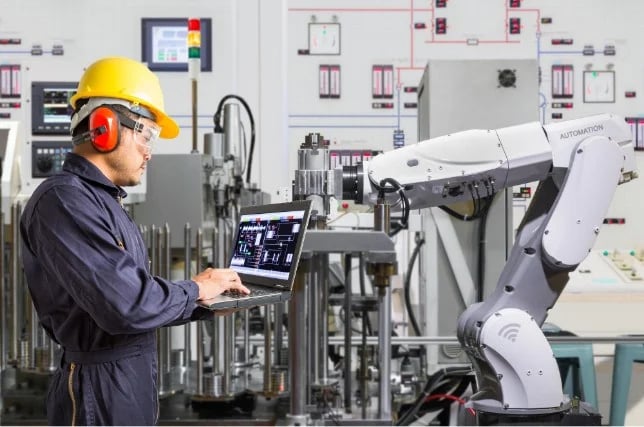
Condition-based monitoring (CBM) is a maintenance strategy that involves continuous monitoring of equipment and machinery to assess their performance and health in real-time. This data-driven approach can significantly impact inventory management:
- Data-Driven Inventory Replenishment: CBM provides real-time insights into the condition of critical equipment. When certain parameters or indicators reach predetermined thresholds, it triggers maintenance actions. This data can also signal the need for spare parts replenishment, ensuring that items are only ordered when they are needed.
- Reduced Stockouts: By relying on condition data to trigger reorder points, maintenance teams can avoid stockouts of critical spare parts. When a component shows signs of impending failure, a replacement part can be ordered immediately, reducing the risk of unplanned downtime.
- Optimized Inventory Investment: CBM allows maintenance managers to allocate resources more efficiently. Capital tied up in excess spare parts can be redirected to other critical areas of maintenance, improving overall financial performance.
4. Just-in-Time (JIT) Inventory for Maintenance
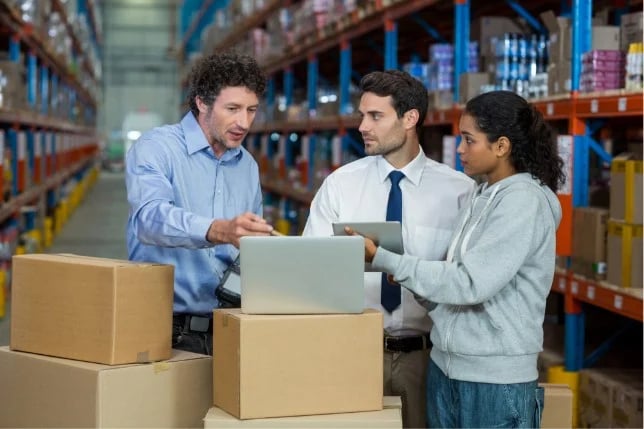
Just-in-Time (JIT) inventory management is a strategy that aims to minimize inventory levels while ensuring that the right parts and materials are available exactly when they are needed. While JIT is often associated with manufacturing, its principles can be adapted to maintenance operations:
- Demand-Driven Procurement: JIT in maintenance means procuring spare parts and materials based on actual demand rather than speculative stocking. Maintenance professionals closely monitor equipment conditions and order parts only when there is a need, thus reducing excess inventory.
- Reduced Lead Times: JIT encourages efficient supplier relationships and fast deliveries. Maintenance departments collaborate closely with suppliers to ensure rapid response times when parts are required. This reduces the need for excessive safety stock.
- Inventory Tracking: Implementing systems for real-time inventory tracking and management is essential for JIT in maintenance. This ensures that parts are ordered precisely when they are needed and not earlier, preventing overstocking.
Experience Click Maint CMMS now
30-Day Free Trial
No Credit Card needed.
Instant access to all features & modules with an optional live walk-through with a Click Maint expert
Book a live Demo
In this 30-minute demo, see firsthand how our easy CMMS can streamline your operations, enhance productivity, and reduce downtime.
INVENTORY OPTIMIZATION TECHNIQUES
1. ABC Analysis
ABC analysis is a widely used inventory management technique that categorizes items into three categories—A, B, and C—based on their importance and usage.
- Category A (High Priority): These items are critical for maintenance and have a high impact on operations if they are unavailable. Examples include critical spare parts for essential equipment and machinery. Maintenance professionals must closely monitor and ensure adequate stock levels for Category A items.
- Category B (Moderate Priority): Items in this category are important but do not have the same criticality as Category A items. They may include parts required for less critical equipment and machinery. Maintenance managers should maintain a reasonable stock level of Category B items without overstocking.
- Category C (Low Priority): These items have the lowest priority and may include consumables of less critical materials. Inventory levels for Category C items can be kept to a minimum, with orders placed on an as-needed basis.
Setting Priorities Based on Criticality:
ABC analysis helps maintenance professionals set priorities and allocate resources efficiently:
- Stocking Strategies: Criticality assessments based on ABC analysis guide stocking strategies. Category A items may have higher safety stock levels to prevent stockouts, while Category C items can have minimal stocking.
- Procurement Strategies: Category A items often require strong supplier relationships to ensure quick deliveries with reduced lead times. Maintenance managers can negotiate favorable terms and agreements with suppliers for these critical items.
- Budget Allocation: Maintenance budgets can be allocated more effectively when guided by ABC analysis. A larger portion of the budget can be dedicated to Category A items, ensuring that critical equipment remains operational.
- Resource Allocation: Maintenance teams can allocate their resources, including time and labor, based on the priority of items. Category A items may receive more attention and proactive maintenance efforts.
2. Economic Order Quantity (EOQ)
Economic Order Quantity (EOQ) is a fundamental inventory optimization formula that calculates the ideal order quantity to minimize total inventory costs. In the context of maintenance, EOQ is a valuable tool for determining the optimal quantity of maintenance supplies to order. Here's how EOQ is calculated:
EOQ Formula: EOQ = √ (2 DS / H)
Where:
EOQ = Economic Order Quantity
D = Annual demand (the quantity of items used annually)
S = Ordering cost per order (cost to place and receive an order)
H = Holding cost per unit per year (cost to store and maintain one unit for a year)
For maintenance professionals, this formula can be applied to determine the most cost-effective order quantities for supplies, such as consumables, lubricants, or non-critical spare parts. By calculating the EOQ, maintenance managers can:
- Minimize Ordering Costs: EOQ helps identify the order quantity that minimizes the expense of placing and receiving orders. Ordering fewer times in larger quantities can lead to cost savings.
- Reduce Holding Costs: By optimizing inventory levels, maintenance departments can reduce the costs associated with storing and maintaining items in inventory.
- Improve Availability: EOQ ensures that items are ordered in quantities that match actual demand, reducing the risk of stockouts and improving availability when needed.
EOQ for Critical Spares vs. Non-Critical Spares:
EOQ calculations can be tailored to distinguish between critical spares and non-critical spares:
- Critical Spares: These are items essential for maintaining critical equipment and machinery. For critical spares, maintenance managers may prioritize higher EOQ quantities to ensure their immediate availability in case of breakdowns. The emphasis is on minimizing downtime.
- Non-Critical Spares: Non-critical spares are items needed for less essential equipment or routine maintenance tasks. EOQ calculations for non-critical spares may result in smaller order quantities, reducing the capital tied up in inventory.
By differentiating between critical and non-critical spares in EOQ calculations, maintenance managers strike a balance between ensuring the availability of vital parts and components, and optimizing inventory costs. This approach aligns inventory management with maintenance priorities.
3. Two-Bin System
The Two-Bin System aligns with the principles of lean inventory management by promoting efficient use of resources and preventing stockouts. It involves dividing inventory into two bins or containers, each serving a specific purpose:
- Active Bin: The active bin contains items currently in use or immediately accessible for maintenance tasks. When items in this bin are consumed, it serves as a visual signal to reorder or replenish those items.
- Reserve Bin: The reserve bin holds surplus or backup inventory. It acts as a buffer to ensure that essential supplies or spare parts are always available when needed.
Implementing the Two-Bin System in maintenance operations involves the following steps:
- Identification of Critical Items: Determine which items are essential for maintenance tasks, such as consumables, frequently used tools, or commonly replaced parts.
- Setting Bin Sizes: Decide on the appropriate sizes for the active and reserve bins. The active bin should be small enough to encourage frequent replenishment and large enough to meet immediate needs.
- Replenishment Process: When the active bin is emptied or reaches a predefined minimum level, it triggers the replenishment process. This can include generating a purchase order or requesting items from a central storeroom.
- Regular Audits: Conduct regular audits to ensure that the reserve bin remains properly stocked. Adjust the reorder quantities based on usage patterns and demand fluctuations.
Benefits in Reducing Stock Outages:
The Two-Bin System offers several benefits in reducing stockouts and enhancing maintenance operations:
- It’s Visual: The active bin's visual emptiness serves as a clear signal for replenishment. Maintenance teams can quickly identify when items are running low, reducing the risk of stockouts.
- Reduction in Downtime: With a reserve bin in place, maintenance personnel can access backup supplies immediately, avoiding downtime due to stockouts.
- Simplified Reordering: Replenishment is straightforward, as it's triggered by visual cues. This simplicity ensures that essential items are consistently available.
- Space Optimization: The system is space-efficient, as it encourages the careful allocation of space for active and reserve bins, reducing the need for excessive storage.
- Efficient Resource Allocation: Maintenance managers can allocate their time and resources more efficiently, knowing that essential supplies are readily accessible.
INVENTORY TRACKING AND CONTROL SYSTEMS
Effective inventory tracking and control systems are essential for maintenance operations, ensuring that the right items are available when needed.
CMMS (Computerized Maintenance Management System)
A Computerized Maintenance Management System (CMMS) streamlines maintenance operations, including inventory management.
Key benefits of CMMS in the context of inventory control include:
- Centralized Data: CMMS centralizes data related to maintenance activities, including inventory. It provides a single platform for tracking inventory levels, reorder points, usage history, and supplier information.
- Automated Alerts: CMMS can be configured to send automated alerts when inventory levels reach reorder points (minimum quantities) or when items need replacement. This proactive approach minimizes stockouts and downtime.
- Data Analytics: CMMS generates valuable data and analytics on inventory usage, enabling maintenance managers to make informed decisions about stocking levels, item prioritization, and budget allocation.
- Integration: Many CMMS solutions can integrate with procurement systems, enabling seamless order placement and reducing manual data entry.
- Real-time Updates: CMMS provides real-time updates on inventory levels, allowing maintenance professionals to make decisions based on the latest information.
- Automated Work Orders: When inventory items are used in maintenance tasks, CMMS can automatically generate purchase orders for replenishment, ensuring that items are replaced promptly.
- Usage Tracking: CMMS tracks item usage history, helping maintenance managers identify trends and adjust stocking levels accordingly.
- Cost Control: Integration with financial systems allows for precise cost tracking related to inventory management, helping to optimize budgets. Some CMMS platforms offer flexible accounting methodologies for managing inventory cost; FIFO, LIFO or Average Cost.
2. RFID and IoT Solutions
Radio-Frequency Identification (RFID) and Internet of Things (IoT) technologies offer real-time visibility into inventory. In maintenance, these technologies provide benefits such as:
- Real-time Tracking: RFID tags and IoT sensors continuously track the location and status of inventory items, reducing the risk of loss or misplacement.
- Automated Data Collection: RFID and IoT solutions automatically collect data on item usage, providing accurate records for maintenance history and inventory audits.
- Predictive Maintenance: IoT sensors can monitor the condition of critical spare parts, triggering maintenance actions when abnormalities are detected.
3. Barcoding and QR Code Scanning Systems
Barcoding and QR Code scanning systems simplify maintenance inventory management:
- Efficient Data Entry: Barcodes and QR codes on inventory items can be scanned for quick and accurate data entry, reducing manual errors.
- Inventory Audits: Regular barcode and QR code scans facilitate inventory audits and reconciliation, ensuring data accuracy.
- Order Picking: Barcodes and QR codes on bins or shelves help maintenance staff locate and pick items efficiently.
BEST PRACTICES FOR INVENTORY MANAGEMENT IN MAINTENANCE DEPARTMENTS
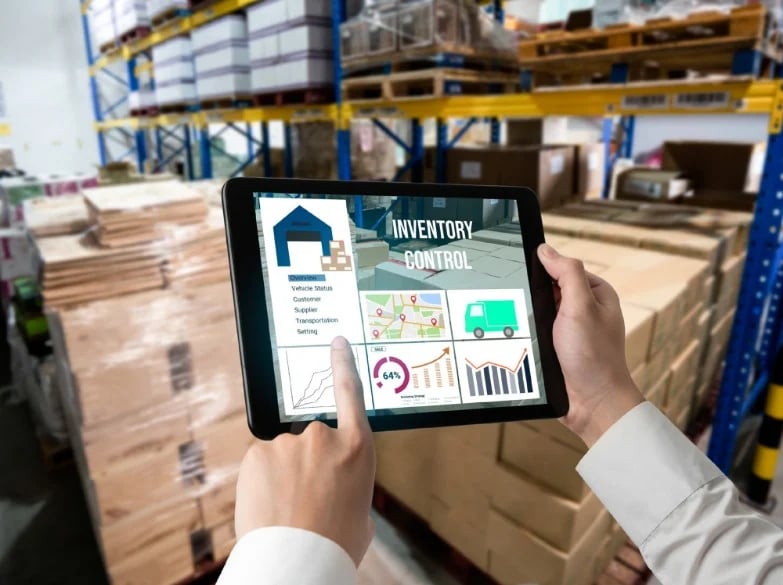
1. Demand Forecasting for Maintenance
Demand forecasting is important for maintaining optimal inventory levels in maintenance operations:
- Historical Data Analysis: Utilize historical maintenance data to identify usage patterns and trends. This provides valuable insights into which items are frequently used and when.
- Maintenance Scheduling: Coordinate maintenance schedules with inventory requirements. Forecasting can help ensure that the necessary parts and materials are available when maintenance activities are planned.
- Collaboration: Engage maintenance teams in the forecasting process. Those on the front lines often have valuable insights into which items are critical and in what quantities.
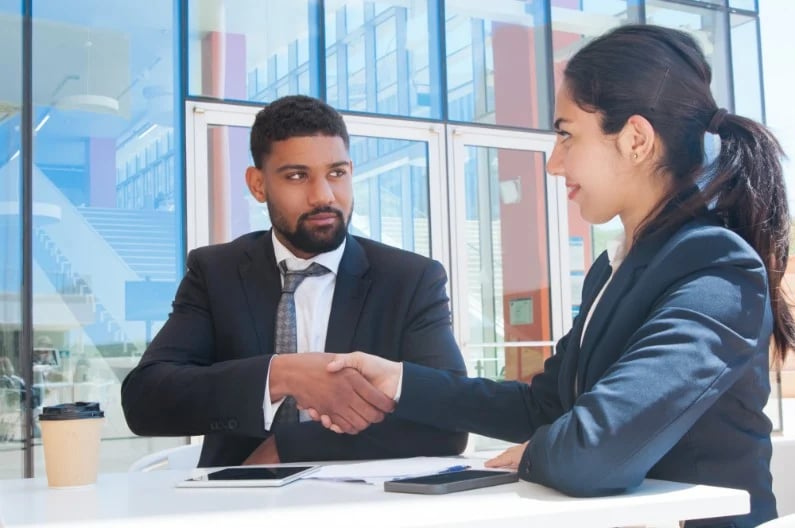
2. Vendor and Supplier Relationship Management
Effective vendor and supplier relationships are essential for timely procurement and inventory management:
- Supplier Partnerships: Build strong partnerships with reliable suppliers. Collaborate on lead times, pricing, and order flexibility to ensure timely deliveries.
- Communication: Maintain open communication with suppliers. Provide forecasts and updates on inventory needs, especially for critical items.
- Alternative Suppliers: Have backup suppliers or sources for critical parts to reduce the risk of supply chain disruptions.
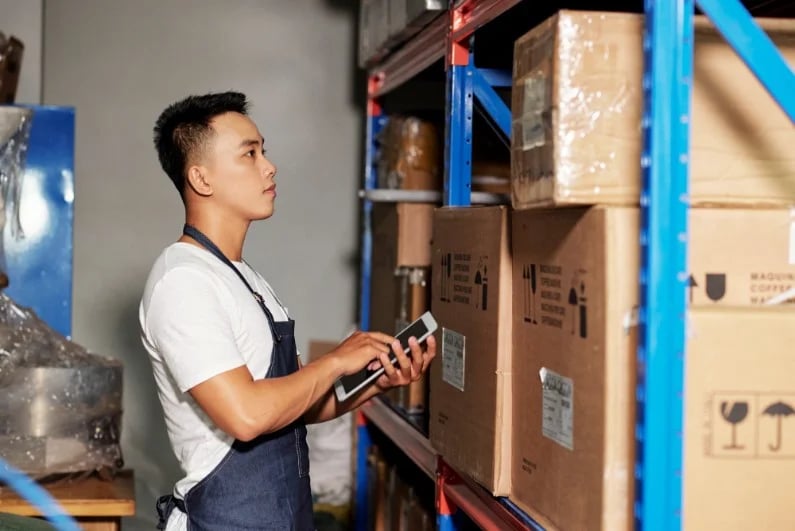
3. Maintenance Storeroom Organization
Organizing the maintenance storeroom is fundamental to efficient inventory management:
- Proper Labeling: Clearly label items, shelves, and bins for easy identification. Use barcoding, QR codes or RFID if possible.
- Logical Layout: Organize items logically based on usage frequency, criticality, or equipment association. This speeds up locating parts and inventory items when needed.
- Safety Measures: Ensure that safety protocols are in place for hazardous materials and that items are stored in compliance with regulations.
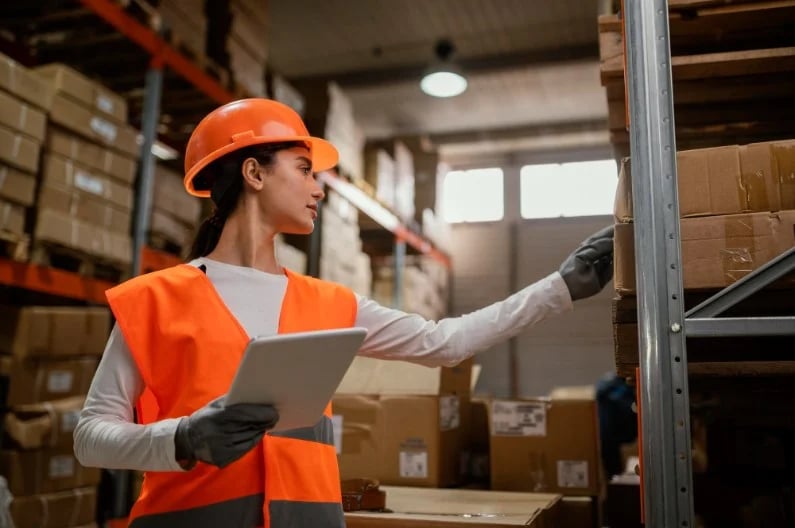
4. Inventory Audits and Cycle Counts
Regular inventory audits and cycle counts maintain inventory accuracy:
- Scheduled Audits: Conduct scheduled audits to verify inventory levels. This helps identify discrepancies and address them promptly.
- Cycle Counts: Implement cycle counting, which involves counting a subset of items regularly. This ongoing process ensures that inventory records remain accurate and prevents theft.
- Root Cause Analysis: When discrepancies are identified, perform root cause analysis to understand why they occurred and implement corrective actions.
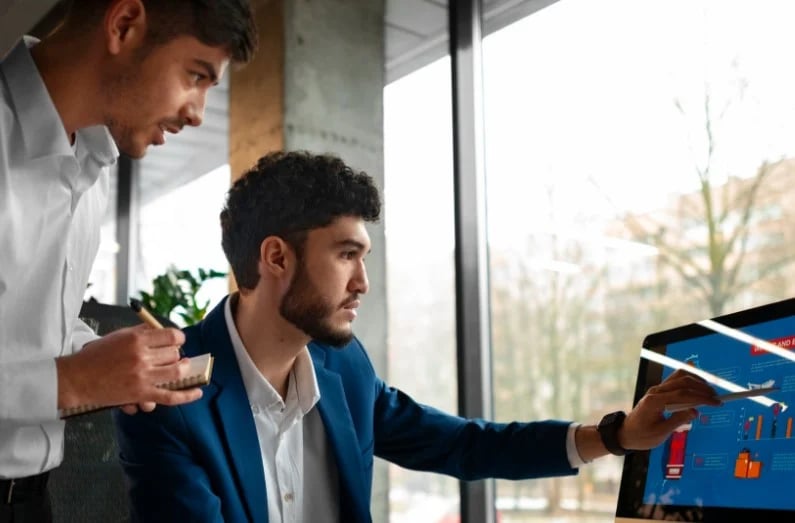
5. Standardization and Rationalization of Parts
Standardization and rationalization of parts simplify inventory management:
- Item Reduction: Review inventory to identify duplicate or seldom-used items. Eliminate or consolidate them to reduce stocking complexity.
- Standardized Parts: Whenever possible, standardize on certain parts across equipment or machinery. This reduces the number of unique items in inventory.
- Cross-Training: Cross-train maintenance staff on the use of standardized parts. This ensures that team members can work on a wider range of equipment without the need for specialized parts. Moreover, implementing standardization for Bill of Materials (BOM) ensures that for every asset, there is a consistent and well-documented list of parts required for maintenance. This not only simplifies inventory management but also streamlines maintenance procedures, improves equipment reliability, and facilitates quicker response to maintenance needs
CHALLENGES IN MAINTENANCE INVENTORY MANAGEMENT
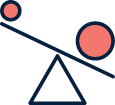
Balancing Stock Levels
Balancing stock levels is a delicate task in maintenance inventory management:
- Overstocking: Maintaining excess inventory ties up capital, increases storage costs, and may lead to items becoming obsolete before use.
- Understocking: Insufficient inventory can result in stockouts, which disrupt maintenance operations, cause downtime, and lead to emergency orders with higher costs.
- Optimization: Finding the right balance between overstocking and understocking is a continuous challenge. It requires accurate demand forecasting, data analysis, and regular inventory reviews.
Spare Parts Obsolescence
Spare parts obsolescence is a significant concern:
- Changing Equipment: Equipment upgrades or replacements can render some spare parts obsolete.
- Expiration Dates: Some consumables and chemicals have a limited shelf life, and if not used, they become obsolete.
- Capital Tied Up: Obsolete parts represent capital tied up in unusable inventory.
- Disposal Costs: Disposing of obsolete parts can incur additional costs.
Managing spare parts obsolescence involves regularly reviewing inventory, updating item statuses, and implementing proper disposal processes.
Budget Constraints
Budget constraints often limit maintenance inventory management efforts:
- Competing Priorities: Maintenance budgets are finite and must cover various needs, including labor, equipment, and materials.
- Cost-Effective Decisions: Maintenance managers must make cost-effective decisions about which items to stock and in what quantities.
- Trade-offs: Budget constraints may require trade-offs between preventive maintenance and reactive maintenance, impacting inventory needs.
To address budget constraints, maintenance managers should prioritize critical items and focus on efficient inventory management techniques.
Data Accuracy and Integration
Data accuracy and integration are vital for effective inventory management:
- Manual Errors: Manual data entry can lead to inaccuracies, affecting reorder points and inventory levels.
- Integration: Ensuring that inventory data seamlessly integrates with other systems, such as CMMS or procurement, can be challenging and often requires internal IT experts, consultants and assistance from software providers.
- Data Visibility: Lack of real-time data visibility can lead to delayed decision-making.
Maintenance professionals need reliable systems and processes to maintain accurate inventory data and integrate it into broader maintenance operations.
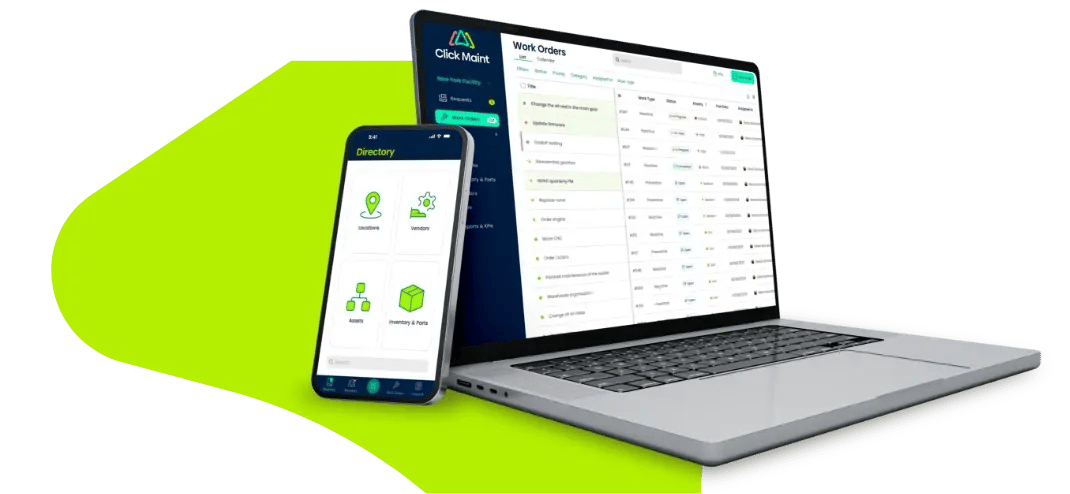
Optimize your maintenance operations with CMMS Software
FUTURE TRENDS IN INVENTORY MANAGEMENT
3D Printing for Spare Parts
3D printing offers huge potential for improving spare parts management:
- On-Demand Production: Maintenance teams can manufacture spare parts on-site, reducing the need for extensive inventory storage.
- Obsolete Parts: 3D printing enables the reproduction of obsolete parts that are no longer available through traditional suppliers.
- Customization: Parts can be tailored to specific needs, improving equipment performance and longevity.
- Reduced Lead Times: Rapid prototyping and production significantly reduce lead times for obtaining critical spare parts.
Augmented Reality (AR) for Inventory Management Training
Augmented Reality (AR) is enhancing maintenance inventory training and on-the-job support:
- Training Simulations: AR allows maintenance personnel to train in realistic scenarios without the risk of damaging equipment.
- Inventory Navigation: AR overlays digital information on real-world environments, aiding in inventory location and selection.
- Remote Expertise: Maintenance professionals can access real-time support from experts who can guide them using AR interfaces.
- Reduced Downtime: AR-enabled training and troubleshooting can reduce the time required to address maintenance issues.