Maintenance Knowledge at Your Fingertips
Print or Download for Offline Access!
Maintenance Management
An Introduction to Maintenance Management
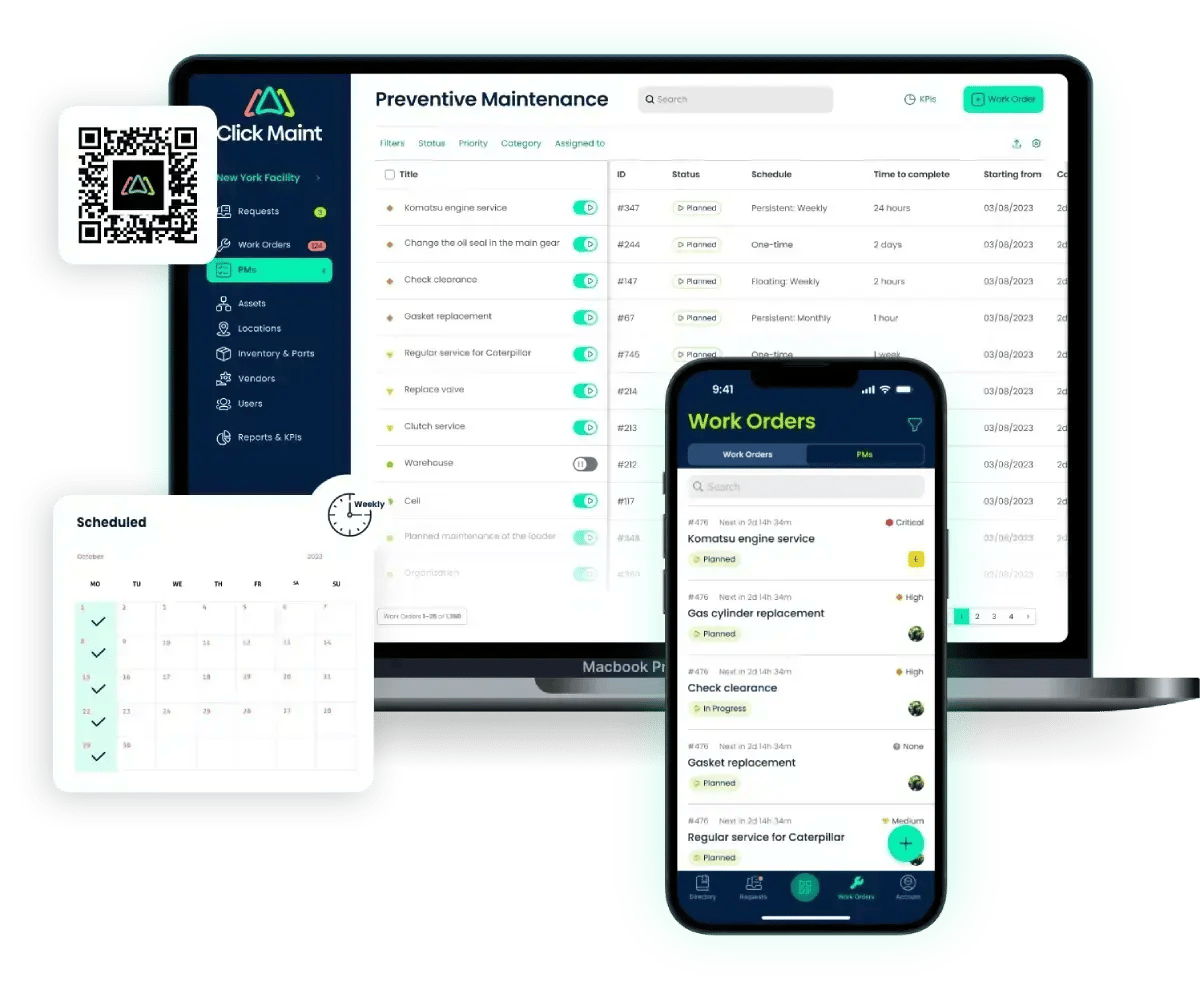
TABLE OF CONTENTS
WHAT IS MAINTENANCE MANAGEMENT?
A business has assets. These include people, machinery equipment, and goodwill. Maintenance management is the process of taking care of all of a company’s assets. It also ensures the efficiency necessary for a company to meet its business objectives. Maintenance management reduces the costs associated with equipment breakdown and downtime. Maintenance management plays a key role in keeping production flowing. Poor maintenance management interrupts business production workflow, hampering operations and negatively affecting a company’s bottomline. Good maintenance management practices result in increased margins and improved profitability.
Cutting edge maintenance management has made the shift from a pen-and-paper approach to digital tools. These tools range from spreadsheets to computerized maintenance management systems, called CMMS. A CMMS maps a company’s entire maintenance management process into a digitally formatted system. A CMMS centralizes all maintenance activities into one program capable of managing all aspects of company assets.
Maintenance management is a combination of strategy, people, process, and also, a CMMS. Since each business is unique; it is left to the company to decide what combination of functions suits it best. For companies embarking on an organization-wide digital transformation process, they may want to consider a system that offers preventive maintenance, breakdown maintenance, or predictive maintenance. These in turn, will impact the approach taken to maintenance management.
WHY IS MAINTENANCE MANAGEMENT A CRITICAL SUCCESS FACTOR IN BUSINESS?
CMMS’s benefits outweigh the costs of the system, installation and training many times over. It keeps production moving along like clockwork, improves reliability, prioritizes quality assurance, and sets the company on the path to long-term success. On the other hand, when effective maintenance management is not conducted routinely or efficiently, there can be serious consequences. Among other things, it can adversely impact production and equipment costs, and customer satisfaction. Maintenance management gaps can also lead to workplace hazards undermining workplace safety.
Maintenance management benefits
The tactical benefits of a systematic maintenance management process including the following:
Creating and sticking to a preventive maintenance plan has many benefits:
- Saves costs - direct and indirect - by reducing unplanned downtime.
- Increases equipment lifespan and efficiency.
- Improves workplace safety and adheres to local compliance requirements.
- Improves inventory management of materials and spare parts.
- Provides data and analytics for continuous improvement
See how affordable Click Maint CMMS is
Consequences of maintenance management neglect
Neglect adversely affects business operations and future prospects with serious consequences.
- Equipment failures and breakdowns can occur more frequently, leading to unplanned downtime and disruption to operations.
- This can result in decreased productivity, missed deadlines, and dissatisfied customers.
- Increases equipment lifespan and efficiency.
- The reliability and performance of assets deteriorate over time, reducing their lifespan and necessitating costly replacements or repairs.
- Neglecting maintenance can compromise the safety of employees, as malfunctioning equipment poses an increased risk of accidents and injuries.
- Maintenance management neglect can result in inefficient resource allocation, excessive downtime for repairs, and higher maintenance costs in the long run.
- Financial losses, damaged reputation, and a decline in overall organizational effectiveness.
A Deloitte study on “Predictive Maintenance and Smart Manufacturing” conducted a few years ago, claimed that unplanned downtime costs industrial manufacturers an estimated $50 billion each year. The same research also reported that poor maintenance strategies can reduce a plant’s overall productive capacity by 5% to 20%.
MAINTENANCE MANAGEMENT OBJECTIVES
Maintenance management objectives are crucial for organizations to ensure the efficient and effective utilization of resources and assets. Data plays a significant role in measuring and evaluating the performance of maintenance management activities. Without data and statistics, maintenance management will be unable to drive progress toward Key Performance Indicators (KPIs).
Equipment Reliability and Availability
This refers to how long your equipment is up and running, and ready for use. When your equipment is available more often, it means less downtime and increased productivity. When machines are down for hours, production is affected and the potential loss of customers may also be a concern.
Improving equipment uptime and availability is a critical goal of preventive maintenance as it reduces downtime and improves productivity.
Maintenance Cost Control
Another objective of maintenance management is to control maintenance costs while ensuring optimal asset performance. Statistics can assist in analyzing maintenance expenditures, such as labor, spare parts, and external contractor costs. Key metrics, such as Maintenance Cost as a Percentage of Asset Value or Maintenance Cost per Unit of Production, help organizations evaluate their maintenance spending efficiency. By tracking these statistics, organizations can identify cost-saving opportunities, optimize maintenance budgets, and make informed decisions regarding maintenance strategies and resource allocation.
Maintenance Backlog Reduction
Maintenance backlog refers to the accumulation of pending maintenance tasks or repairs. A high backlog can lead to unnecessary delays, increased downtime, and reduced equipment availability. Statistics can be used to measure the backlog, such as the total number of open work orders or the average time to complete a maintenance request. By tracking and analyzing these statistics, organizations can set targets for reducing the backlog and implementing proactive maintenance strategies to address pending tasks promptly. This improves operational efficiency, minimizes unplanned downtime, and enhances customer satisfaction.
Maintenance Performance Evaluation
Statistics are essential for evaluating the overall performance of the maintenance function. Key performance indicators (KPIs), such as Overall Equipment Effectiveness (OEE), Maintenance Cost per Unit of Production, or Maintenance Schedule Compliance, provide a quantitative measure of maintenance efficiency and effectiveness. By regularly monitoring these statistics, organizations can identify areas of improvement, benchmark performance against industry standards, and implement strategies to enhance maintenance performance. This leads to better resource utilization, increased asset reliability, and improved operational outcomes.
These objectives provide a roadmap for implementing proactive maintenance strategies, optimizing resource allocation, and achieving operational excellence.
Experience Click Maint CMMS now
30-Day Free Trial
No Credit Card needed.
Instant access to all features & modules with an optional live walk-through with a Click Maint expert
Book a live Demo
In this 30-minute demo, see firsthand how our easy CMMS can streamline your operations, enhance productivity, and reduce downtime.
TYPES OF MAINTENANCE MANAGEMENT
An organization’s approach to maintenance management is a function of its own unique business requirement. Thus, all maintenance management types aren’t the same. It depends on the manufacturing process, asset profile, asset age, equipment manufacturer PM schedules, and actual maintenance history. The following types of maintenance management are listed here.
Preventive Maintenance
Preventive maintenance involves regular inspections, servicing, and replacement of parts to prevent equipment failure. This type of maintenance is planned in advance, and is based on a predetermined schedule or the manufacturer’s recommended maintenance intervals.
Also called preventative maintenance, it involves performing routine tasks on a scheduled basis to prevent breakdowns and extend the lifespan of your equipment. Detecting potential issues before they escalate into major problems can result in cost-savings on repairs and replacements, minimize downtime, and enhance the dependability and productivity of operations.
As the term suggests, preventive maintenance’s focus is on prevention. It’s not about addressing problems once they arise or using a band-aid approach to keep operations going. This old-school and inefficient approach is referred to as “run to fail”. While there may be some short-term benefits with it, overall, this approach has been shown to be very costly and inefficient because unanticipated equipment failures slow down production and delay orders. Reactive maintenance or conducting repairs as needed always costs more because it is unplanned.
Predictive Maintenance
Predictive maintenance uses data analytics and condition monitoring techniques to predict when equipment failure is likely to occur. This allows maintenance teams to perform maintenance tasks before equipment fails, minimizing downtime and reducing the risk of catastrophic failures.
Corrective Maintenance or Reactive Maintenance
Corrective maintenance involves repairing or replacing equipment after it has failed. This type of maintenance is unplanned and can result in costly downtime. It is the maintenance type that is best to be avoided.
Reliability Centered Maintenance (RCM)
Reliability Centered Maintenance (RCM) is a systematic approach to maintenance management that focuses on optimizing the reliability and performance of assets. It involves analyzing the functions, failure modes, and consequences of equipment failures to develop proactive maintenance strategies. RCM aims to identify the most appropriate maintenance tasks, such as preventive or predictive maintenance, based on the criticality and impact of potential failures. The key principle of RCM is to determine the maintenance requirements that provide the best balance between cost, performance, and risk. RCM emphasizes a data-driven approach, analysis of historical performance data, and involvement of cross-functional teams to ensure a thorough understanding of equipment and its maintenance needs.
COMPONENTS OF MAINTENANCE MANAGEMENT
Independent of the approach an organization takes in maintenance management, the following two components are fundamental to any option.
Inventory Management
Inventory management involves managing an organization’s inventory of spare parts and other maintenance-related supplies. This can involve tracking inventory levels, reordering supplies, and managing costs.
Corrective Maintenance or Reactive Maintenance
Corrective maintenance involves repairing or replacing equipment after it has failed. This type of maintenance is unplanned and can result in costly downtime. It is the maintenance type that is best to be avoided.
Asset Management
Asset management involves tracking and managing an organization’s assets, including equipment, facilities, and other physical assets. This can involve tracking maintenance schedules, equipment history, and other relevant information.
Machine Learning
Machine learning in maintenance management is revolutionizing the way organizations approach equipment maintenance. By leveraging advanced algorithms and data analysis techniques, machine learning can identify patterns, anomalies, and trends in equipment data to make predictions and optimize maintenance practices. Machine learning models take information from historical data, sensor readings, and other relevant information to predict equipment failures, determine optimal maintenance schedules, and prioritize maintenance tasks. This proactive approach helps prevent unexpected breakdowns, reduce downtime, and minimize maintenance costs. Machine learning algorithms can also assist in optimizing inventory management by predicting spare part requirements and ensuring timely availability. By harnessing the power of machine learning, organizations can make data-driven decisions, improve maintenance efficiency, extend equipment lifespan, and enhance overall operational performance.
BEST PRACTICES FOR MAINTENANCE MANAGEMENT
A systems approach to maintenance management maximizes an organization’s chance to address downtime. Implementing maintenance management software is a good first step to enable maintenance management. But it is just one of the steps. The following are recommended maintenance management best practices:
Develop a Maintenance Plan
Develop a comprehensive maintenance plan that includes preventive, predictive, and corrective maintenance tasks. This plan should be based on the equipment manufacturer's recommendations, industry best practices, and the organization's specific needs.
Implement a Computerized Maintenance Management System (CMMS)
A CMMS is a software tool that can help organizations manage maintenance tasks, track equipment history, and automate many maintenance-related processes. Here is a detailed step-by-step guide to a CMMS implementation.
Train and Empower Maintenance Staff
Provide regular training to maintenance staff to ensure they have the skills and knowledge necessary to perform their jobs effectively. Empower them to make decisions and take ownership of maintenance tasks. The overall approach here is to help build a culture of improving maintenance management continuously.
Track and Analyze Maintenance Data
Track maintenance data, including equipment history, maintenance schedules, and costs. Use these data to identify trends and make informed decisions about maintenance activities.
Prioritize Maintenance Tasks
Prioritize maintenance tasks based on their impact on production, safety, and other critical factors. This can help ensure that the most important maintenance tasks are completed first.
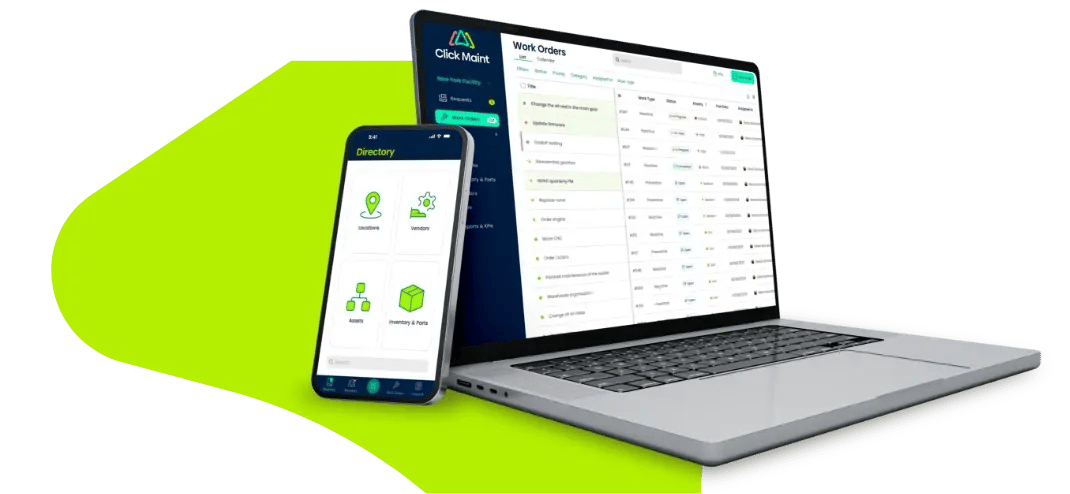
Optimize your maintenance operations with CMMS Software
FAQs
How does preventive maintenance differ from corrective maintenance?
Preventive maintenance involves scheduled inspections and maintenance tasks performed at regular intervals to prevent equipment failure. Corrective maintenance, on the other hand, involves repairing or replacing equipment after it has failed.
What tools or software are commonly used in maintenance management?
Commonly used tools and software in maintenance management include Computerized Maintenance Management Systems (CMMS), Enterprise Asset Management (EAM) systems, and Condition Monitoring tools.
How can I prioritize and schedule maintenance tasks effectively?
Prioritize maintenance tasks based on criticality, impact on production, safety concerns, and equipment importance. Utilize tools such as a maintenance backlog list, job planning, and scheduling to optimize task prioritization and scheduling.
How can maintenance management contribute to improving overall equipment reliability?
By implementing proactive maintenance strategies, conducting regular inspections, performing preventive maintenance tasks, and analyzing equipment performance data, maintenance management can identify potential issues, address them before they lead to failures, and improve overall equipment reliability.
How can maintenance pros ensure proper documentation and record-keeping of maintenance activities?
Maintain detailed records of maintenance tasks, including work orders, equipment history, maintenance logs, and any modifications or repairs performed. Utilize digital systems or software to streamline documentation processes.
How can maintenance personnel stay updated on new maintenance techniques and industry standards?
Stay updated by attending industry conferences, participating in training programs, subscribing to relevant publications, and networking with other maintenance professionals. Online forums and industry associations can also provide valuable resources and information.