- CMMS
- Software
- Maintenance Management Software
Trusted by thousands of maintenance & facilities professionals
How much does Click Maint cost?
Try our Price Calculator to get an Instant Estimate for Your Use Case
PROFESSIONAL PLAN
$ 42 USD
PER USER PER MONTH
$ 35 USD
PER USER PER MONTH
Benefits of Maintenance Management Software
Asset Life
EXTEND equipment lifespan, and improve availability.
Downtime
REDUCE downtime, cut waste, and let production flow.
Compliance
ADHERE to local regulations, and create a safe workplace.
Costs
LOWER expenses with parts management and inventory control.
Productivity
IMPROVE people management, be organized, and get more done.
Performance
DRIVE gains with critical insights from tracking maintenance KPIs.
Experience Click Maint CMMS now
30-Day Free Trial
No Credit Card needed.
Instant access to all features & modules with an optional live walk-through with a Click Maint expert
Book a live Demo
In this 30-minute demo, see firsthand how our easy CMMS can streamline your operations, enhance productivity, and reduce downtime.
Click Maint Maintenance Management Software
Designed for Seamless Operations and Unparalleled Performance!
Work Order Management
- Create and assign work orders
- Associate work orders to assets, locations or both
- Assign due date, priority and category
- Add task checklist for SOPs
- Assign to technicians, teams or vendors
- Track labor, parts and other costs
- Attach images and important documents
- Email notifications on work order updates
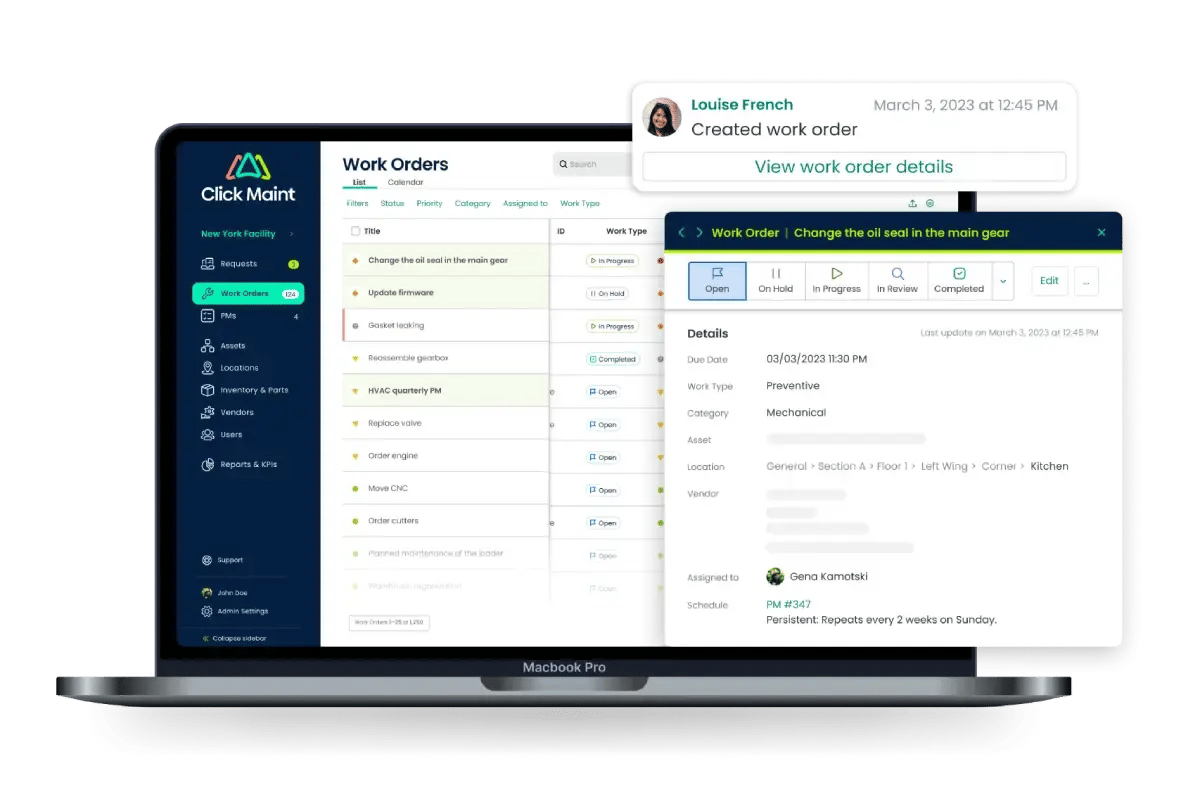
Preventive Maintenance
- Flexible scheduling (hourly, daily, monthly, etc..)
- Associate PMs to assets, locations or both
- Assign due date, priority and category
- Add task checklist for SOPs
- Assign to technicians, teams or vendors
- Track labor, parts and other costs
- Attach images and important documents
- Email notifications on PM updates
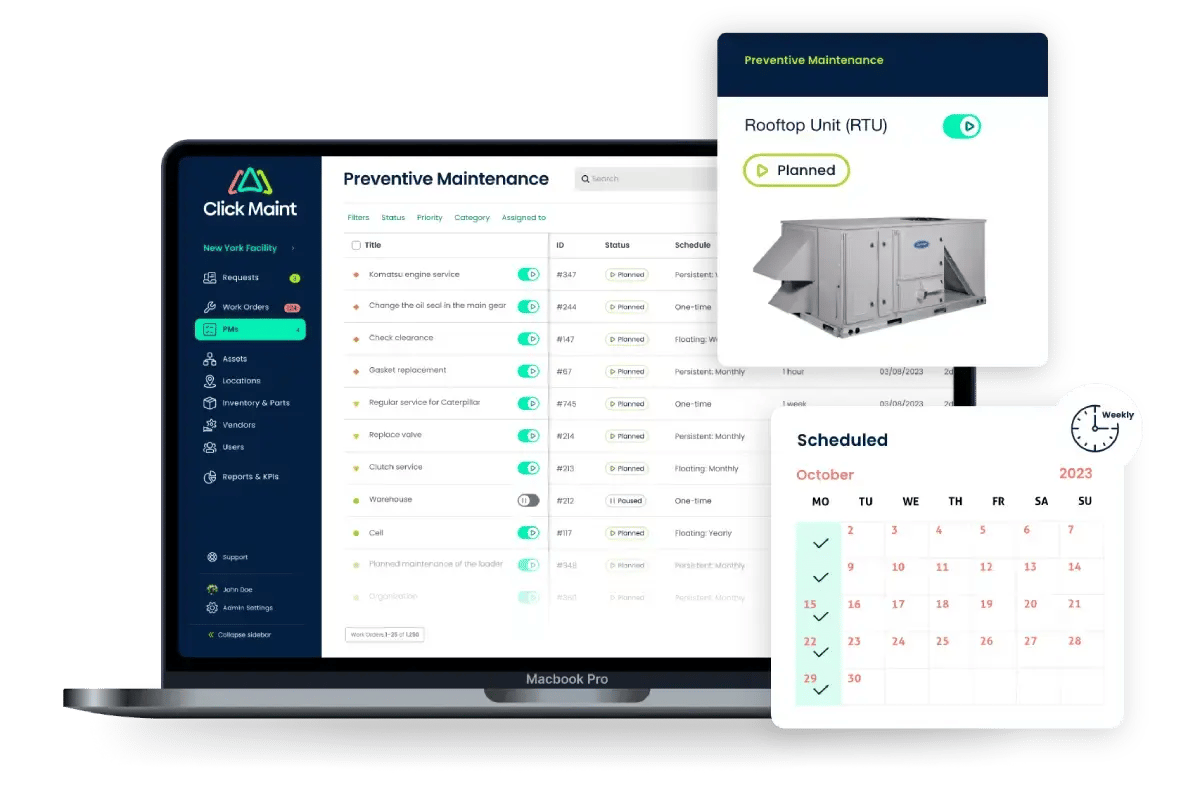
Asset Management
- Track all key assets that need to be maintained
- Monitor and report on asset downtime
- Create asset hierarchy (parent, child)
- Input key details (model, manufacturer, serial number, warranty, etc.)
- Generate QR codes
- Associate parts used
- Attach images and important documents
- Generate reports on maintenance history, costs, downtime, performance
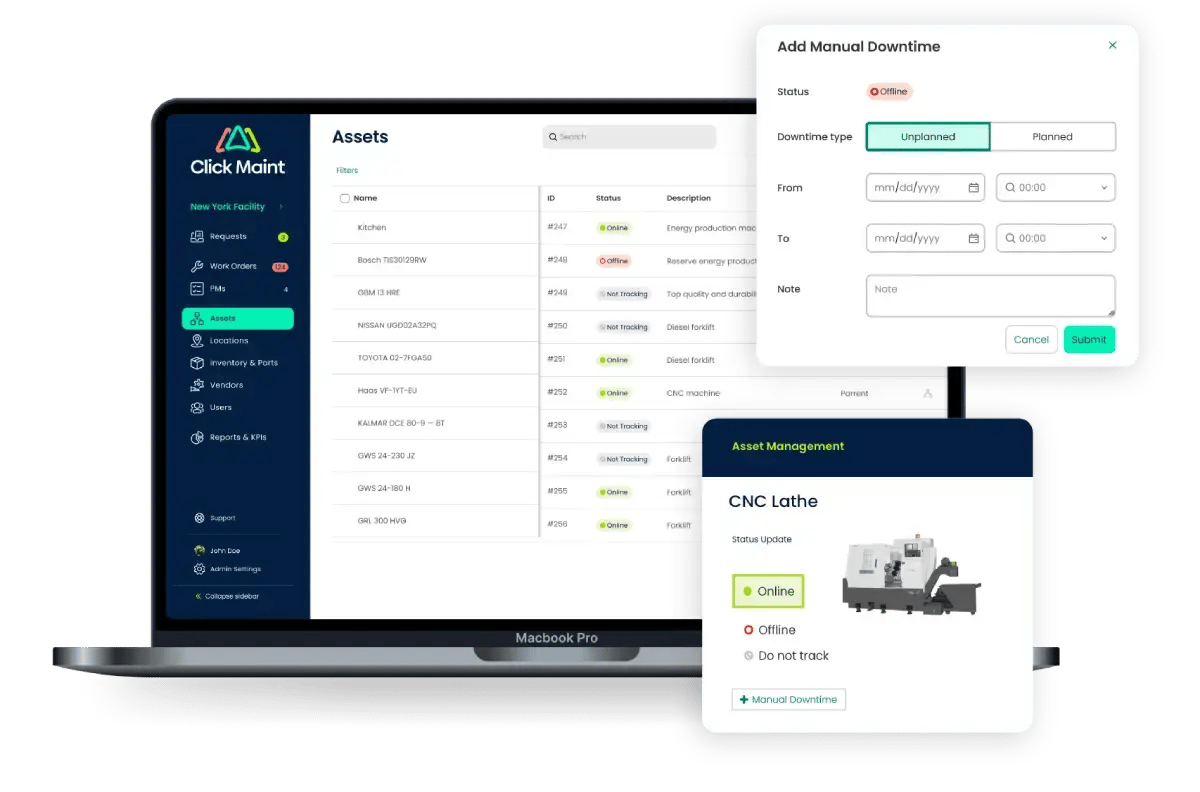
Parts and Inventory Management
- Track all key parts and materials used
- Monitor and report on inventory levels
- Associate parts with assets and work orders
- Input key details (supplier, cost, storage location, etc.)
- Generate QR codes
- Attach images and important documents
- Generate reports on parts used, costs, stock levels
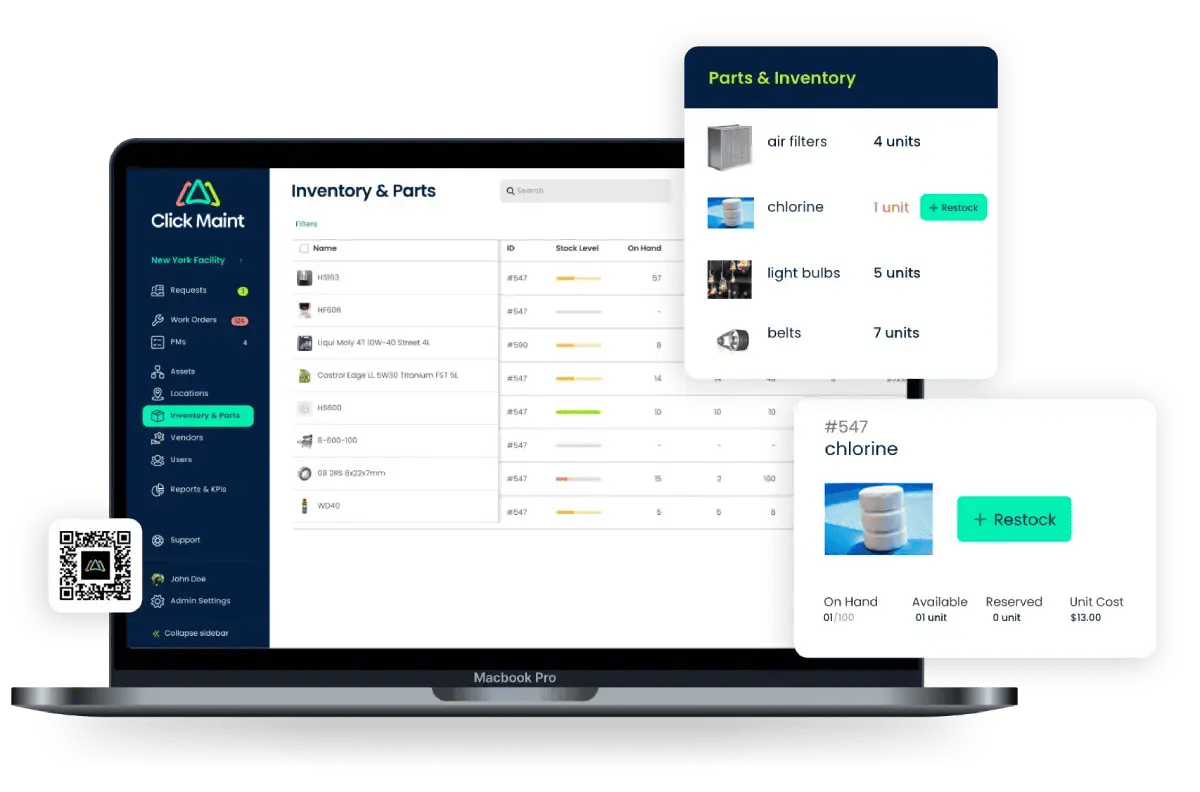
Mobile App
- Manage all work orders and requests in the field
- Create and edit all incoming work orders and preventive maintenance tasks
- Upload images and to work orders, requests and assets
- Scan QR codes for work orders, assets, locations, and parts
- Get real time notifications for work orders and maintenance requests
- Add and update assets and inventory on the go
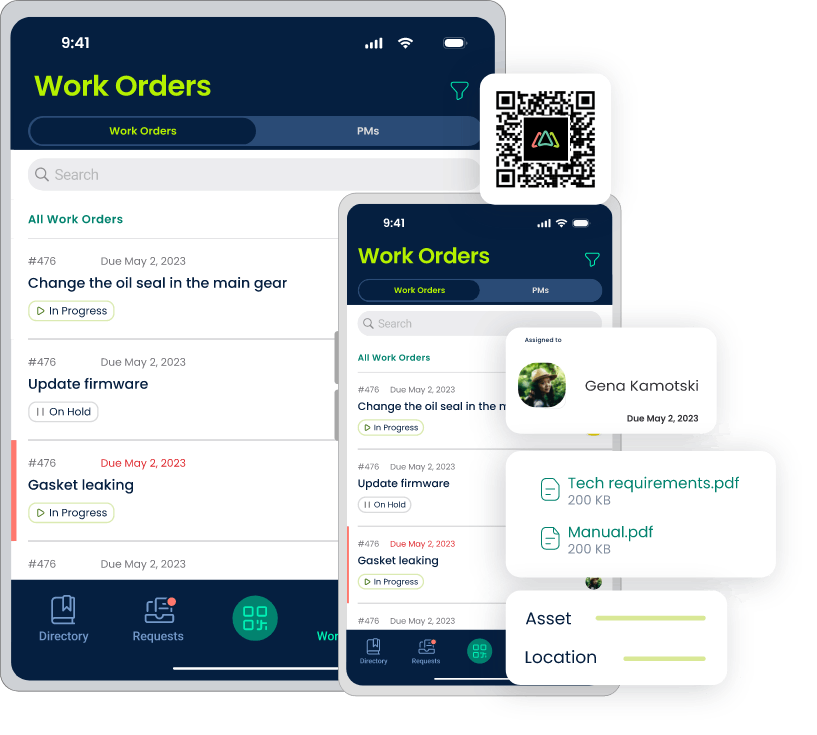
Mobile CMMS
For Maintenance Management on-the-go
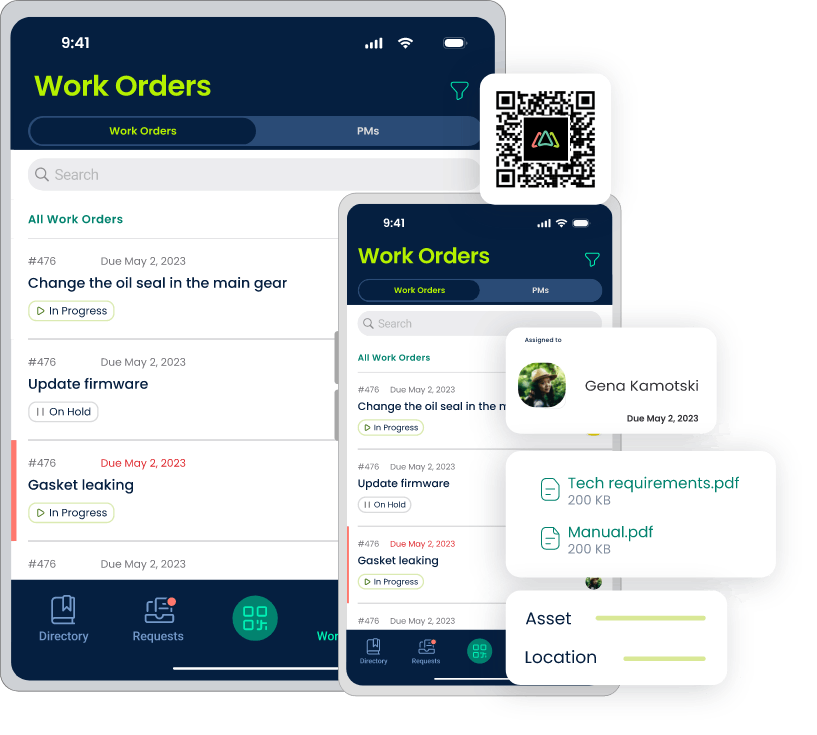
MOBILE ACCESS
Access the CMMS from anywhere, using mobile devices such as smartphones or tablets.
QR CODE SCANNING
Scan barcodes on assets, parts, and inventory using a mobile device's camera.
VOICE-TO-TEXT
Use voice commands to perform tasks, such as creating work orders or updating asset information.
REAL-TIME UPDATES
Receive real-time updates on work order status, asset history, and inventory levels.
COLLABORATION TOOLS
Communicate and collaborate with team members and external partners, such as contractors or suppliers.
ALERTS AND NOTIFICATIONS
Receive alerts and notifications for upcoming maintenance tasks, low inventory levels, or other important events.
IMAGE AND VIDEO ATTACHMENTS
Attach images and videos to work orders and asset records, providing additional context for technicians and managers.
See how affordable Click Maint CMMS is
ADDITIONAL CMMS SOFTWARE FEATURES
Work Order Management
Create, assign, and track work orders, allowing you to monitor progress and ensure fast response and completion times. (Add filters)
Work Order Management
Create, assign, and track work orders, allowing you to monitor progress and ensure fast response and completion times. (Add filters)
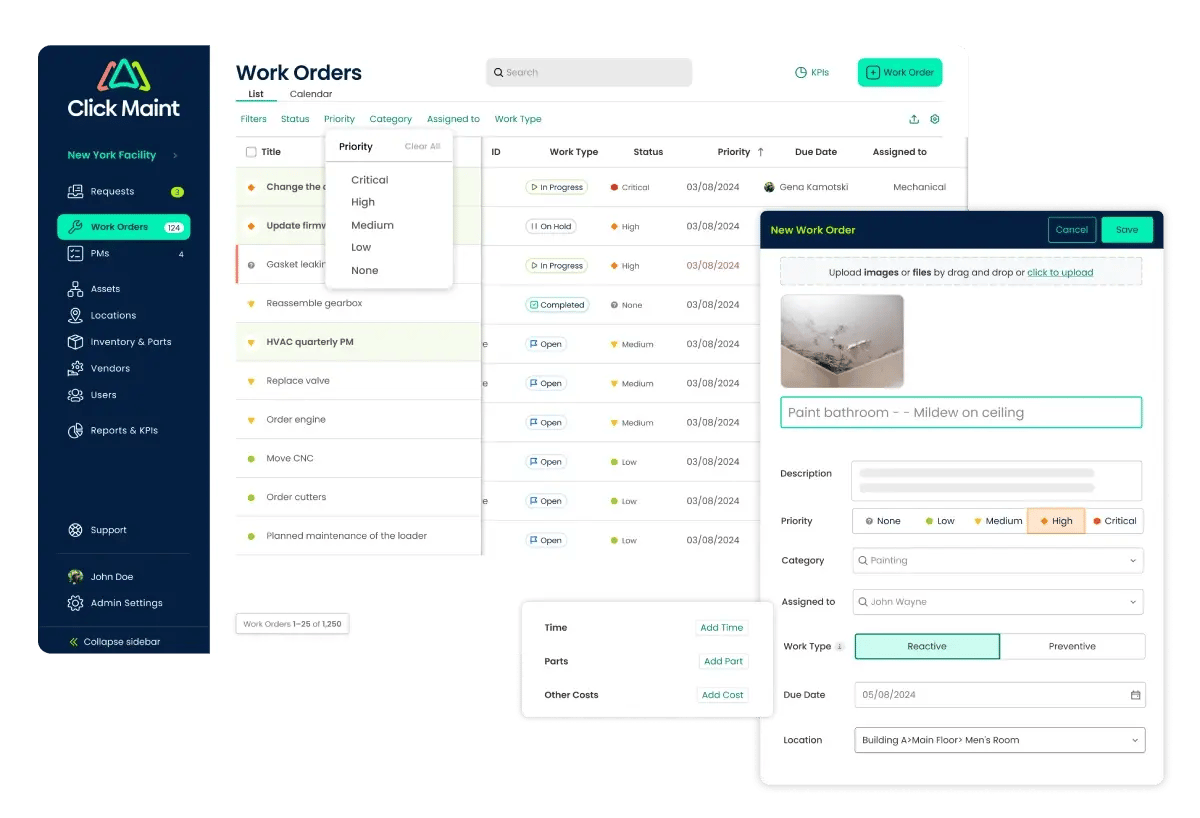
Not ready to Book a Demo yet?
Preventive Maintenance
Schedule routine maintenance and inspections to prevent equipment failures and unplanned downtime and extend the lifespan of assets.
Preventive Maintenance
Schedule routine maintenance and inspections to prevent equipment failures and unplanned downtime and extend the lifespan of assets.
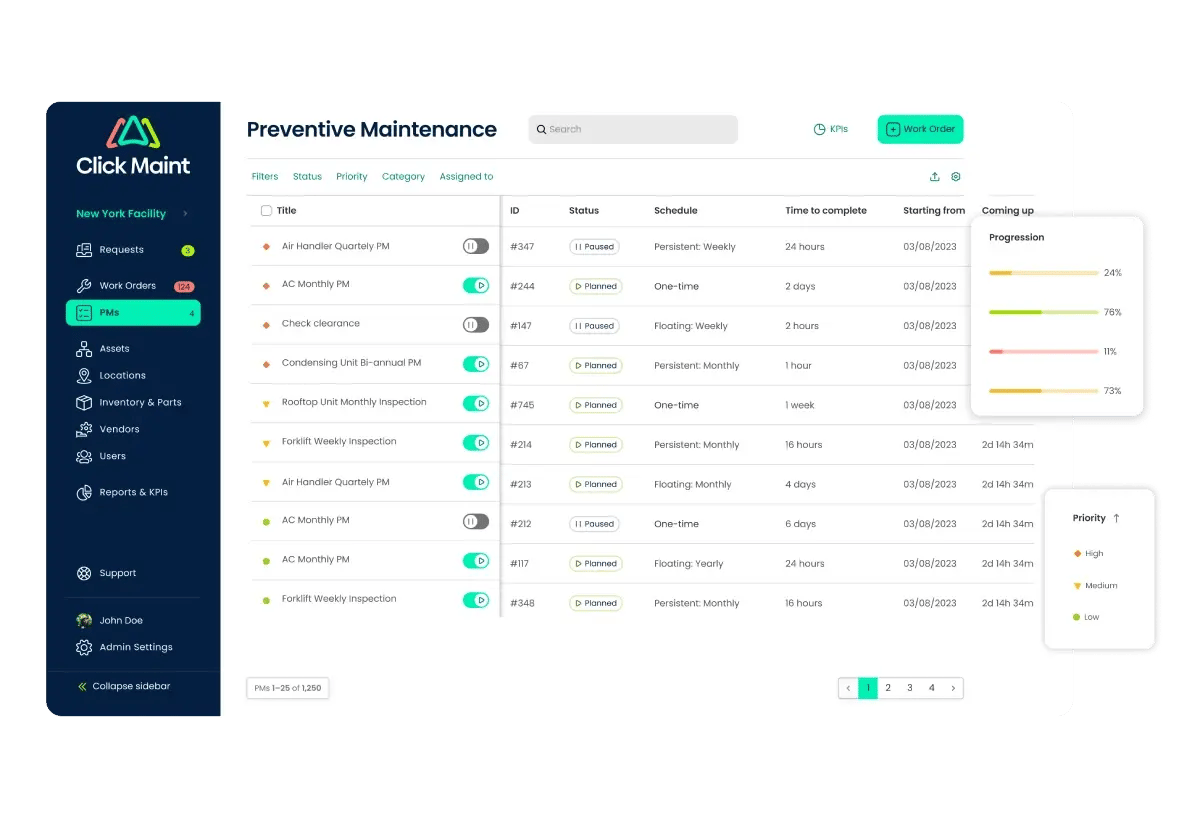
Not ready to Book a Demo yet?
Maintenance Scheduling
Plan and organize maintenance tasks, including preventive maintenance and inspections to reduce equipment downtime and improve efficiency, extend equipment life, and reduce repair costs.
Maintenance Scheduling
Plan and organize maintenance tasks, including preventive maintenance and inspections to reduce equipment downtime and improve efficiency, extend equipment life, and reduce repair costs.
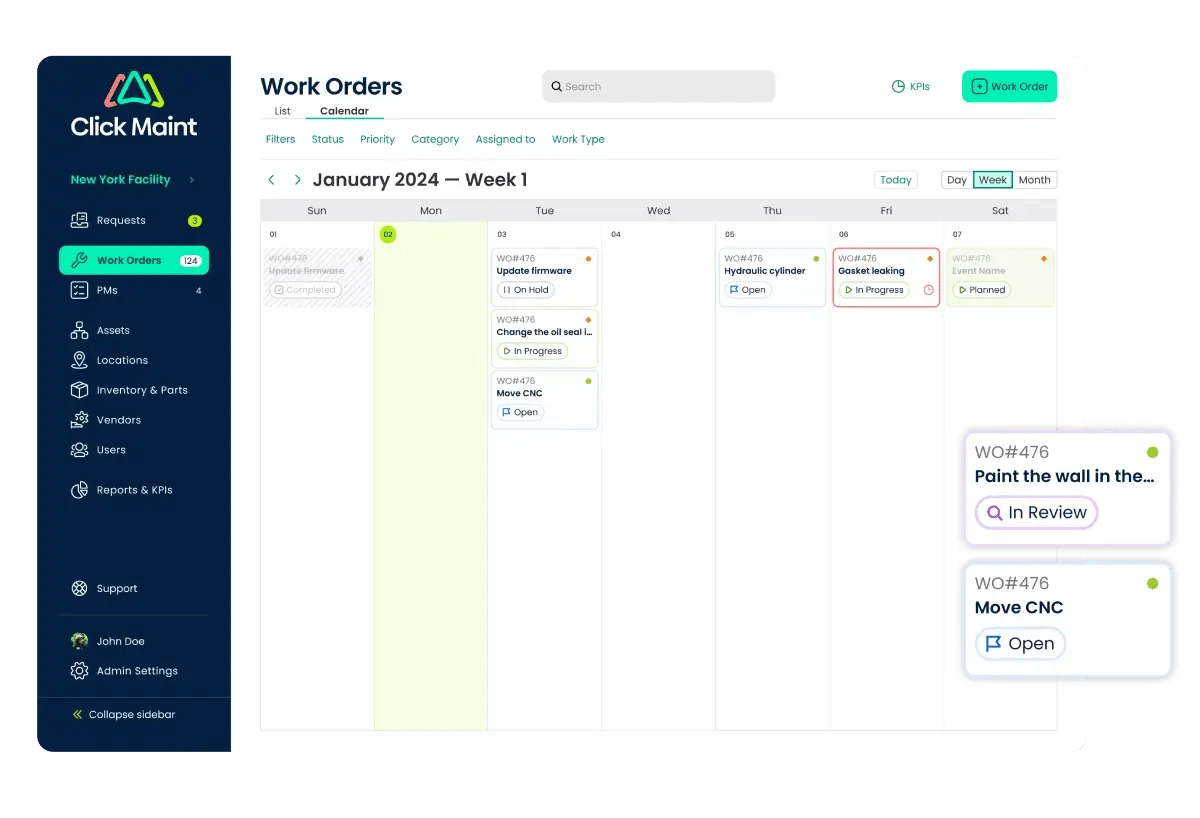
Not ready to Book a Demo yet?
Mobile Access
Equip maintenance teams with an easy-to-use mobile app that empowers users to manage work orders and tasks on the go. Users can scan QR codes, upload images, use voice to text, and more.
Mobile Access
Equip maintenance teams with an easy-to-use mobile app that empowers users to manage work orders and tasks on the go. Users can scan QR codes, upload images, use voice to text, and more.
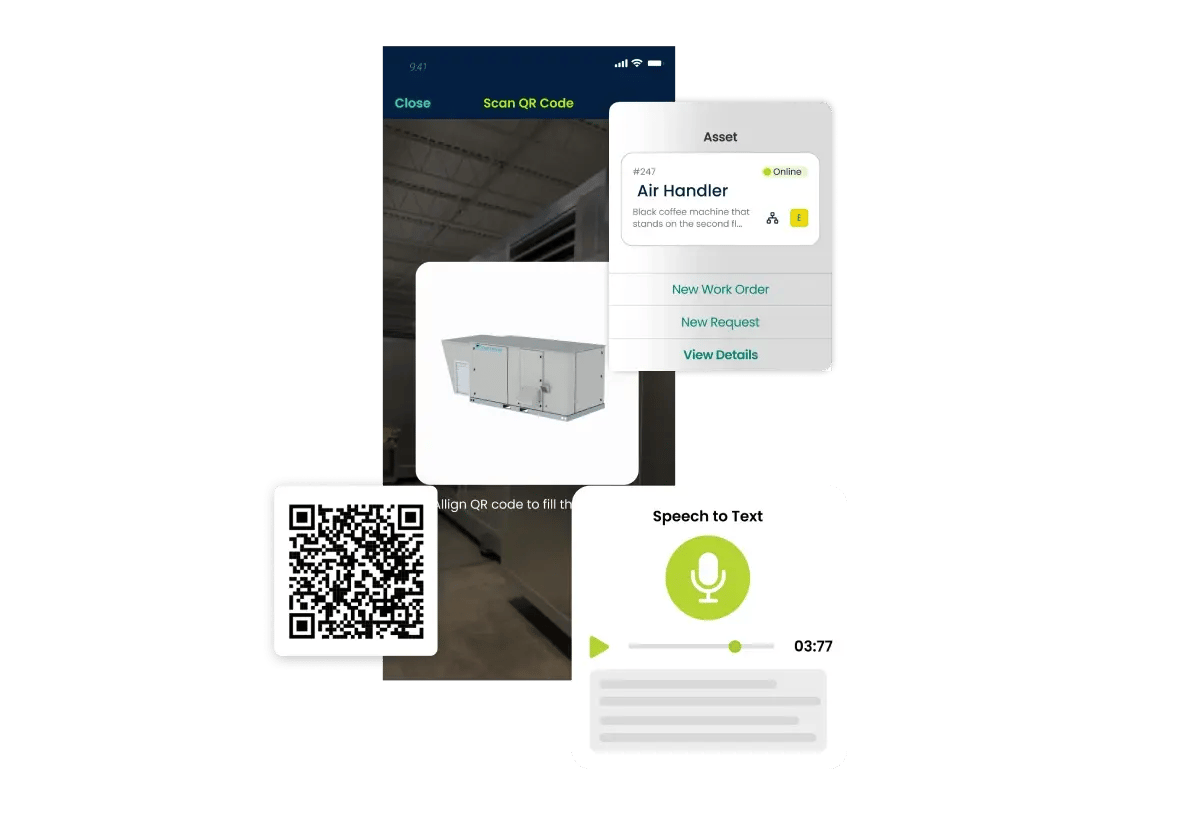
Not ready to Book a Demo yet?
Asset Tracking
Keep track of assets, including their location, condition, and maintenance history, to streamline maintenance planning and improve asset longevity.
Asset Tracking
Keep track of assets, including their location, condition, and maintenance history, to streamline maintenance planning and improve asset longevity.
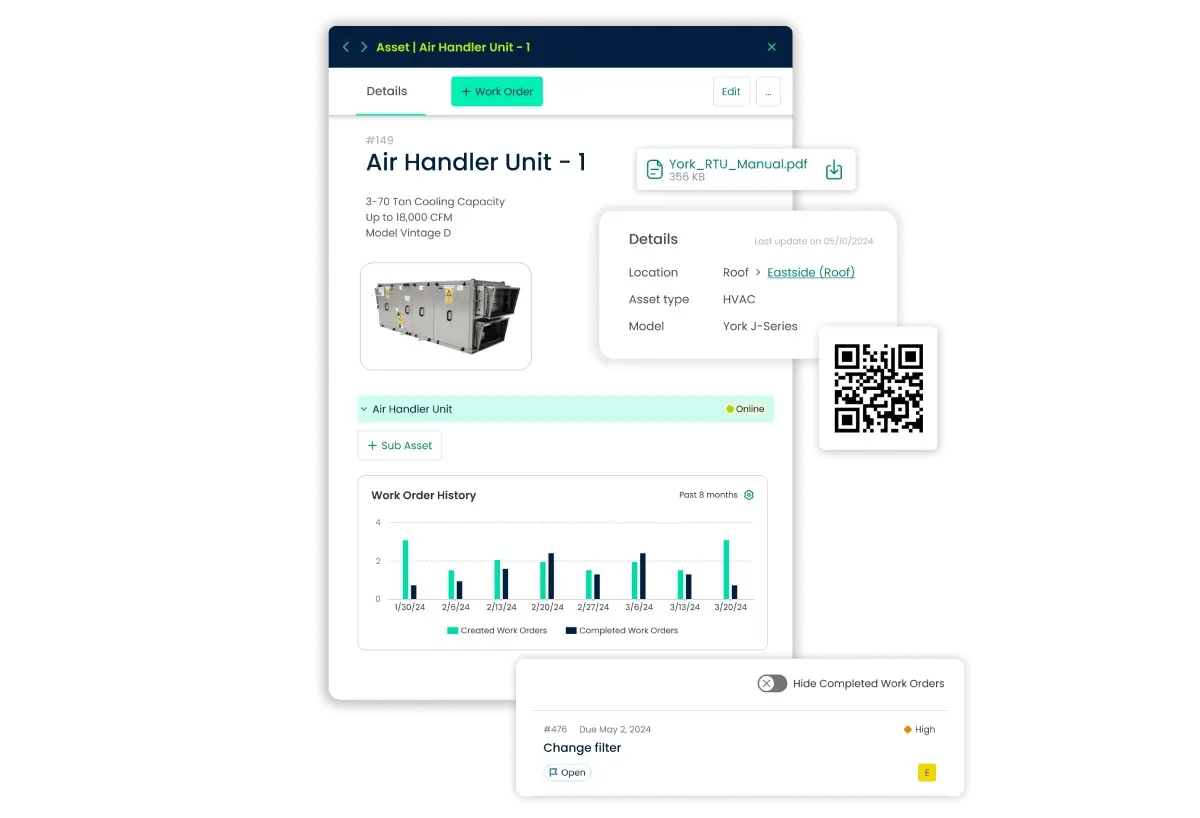
Not ready to Book a Demo yet?
Inventory Control and Management
Manage spare parts, materials, and maintenance supplies, ensuring you have the right items in stock when needed to reduce downtime and delays when completing work.
Inventory Control and Management
Manage spare parts, materials, and maintenance supplies, ensuring you have the right items in stock when needed to reduce downtime and delays when completing work.
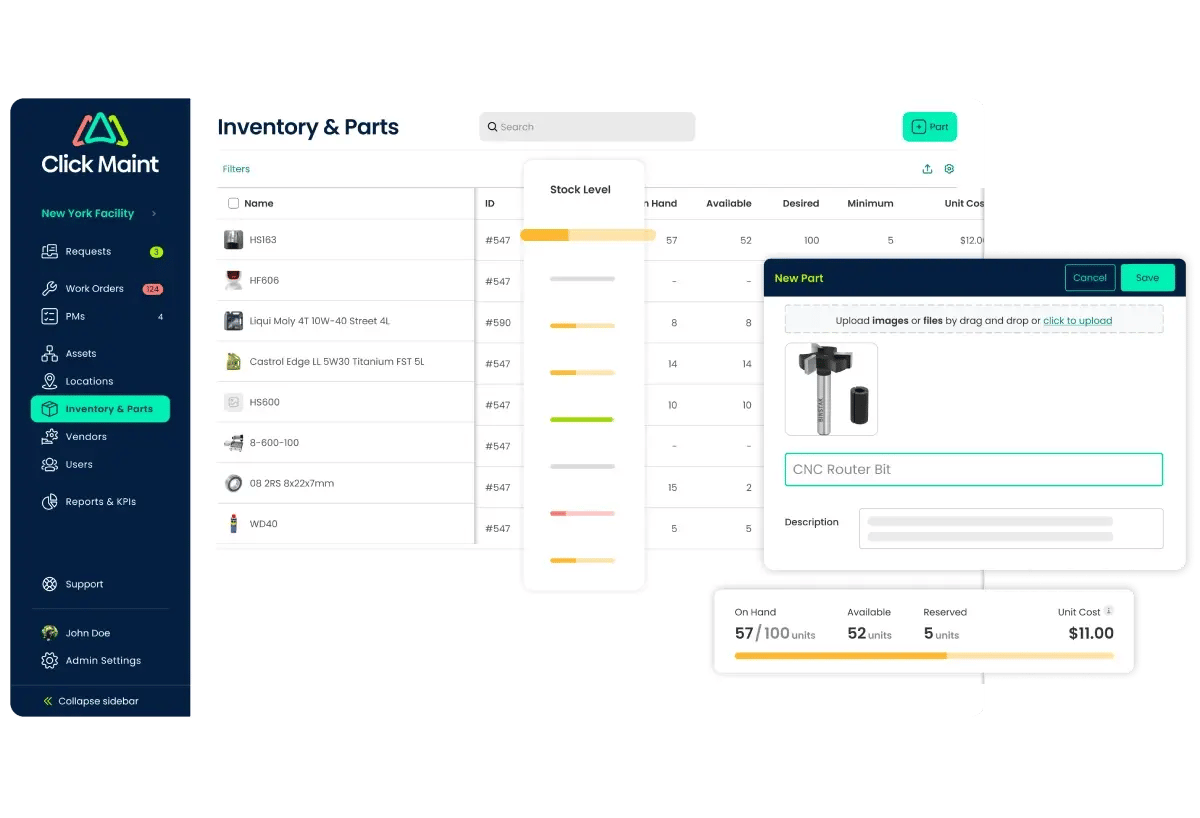
Not ready to Book a Demo yet?
Job Costing
Track and estimate costs for maintenance tasks and work orders, enabling effective budgeting and cost management.
Job Costing
Track and estimate costs for maintenance tasks and work orders, enabling effective budgeting and cost management.
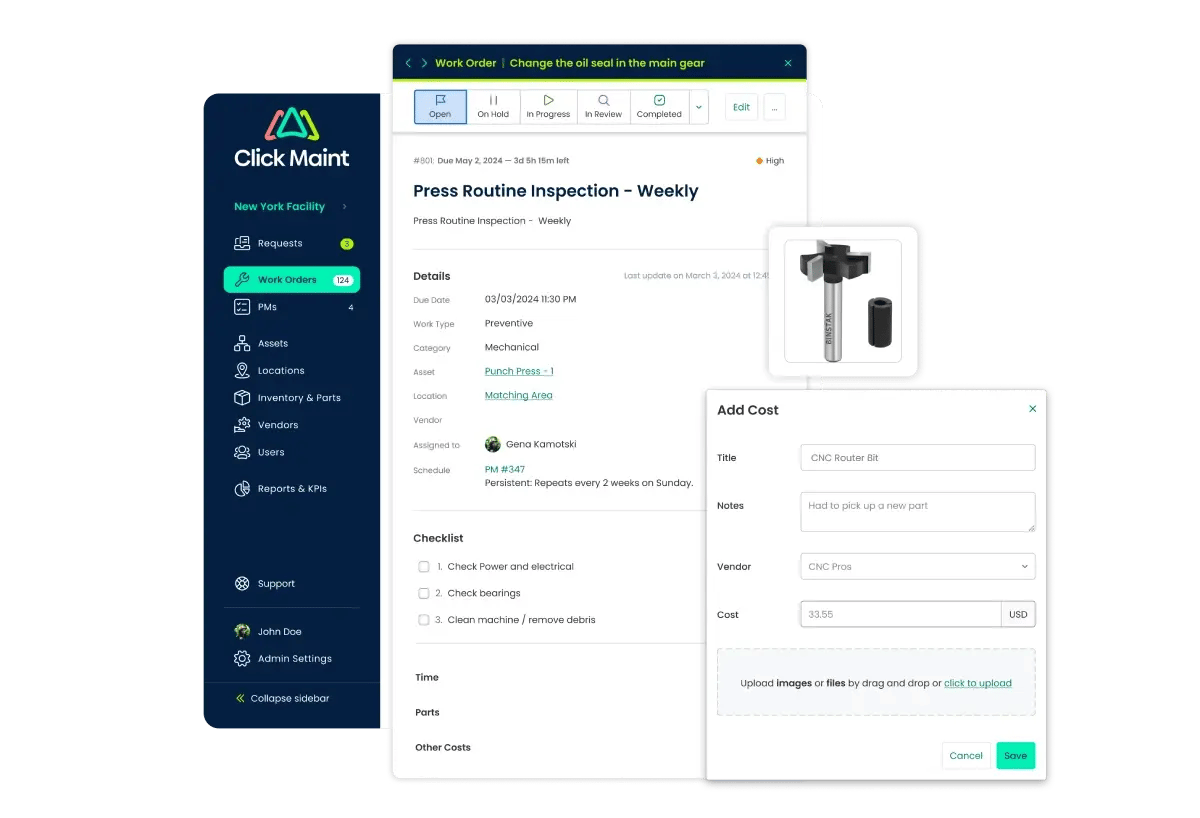
Not ready to Book a Demo yet?
Dispatch Management
Coordinate the assignment and dispatch of maintenance teams, optimizing maintenance scheduling and planning and response time for service requests.
Dispatch Management
Coordinate the assignment and dispatch of maintenance teams, optimizing maintenance scheduling and planning and response time for service requests.
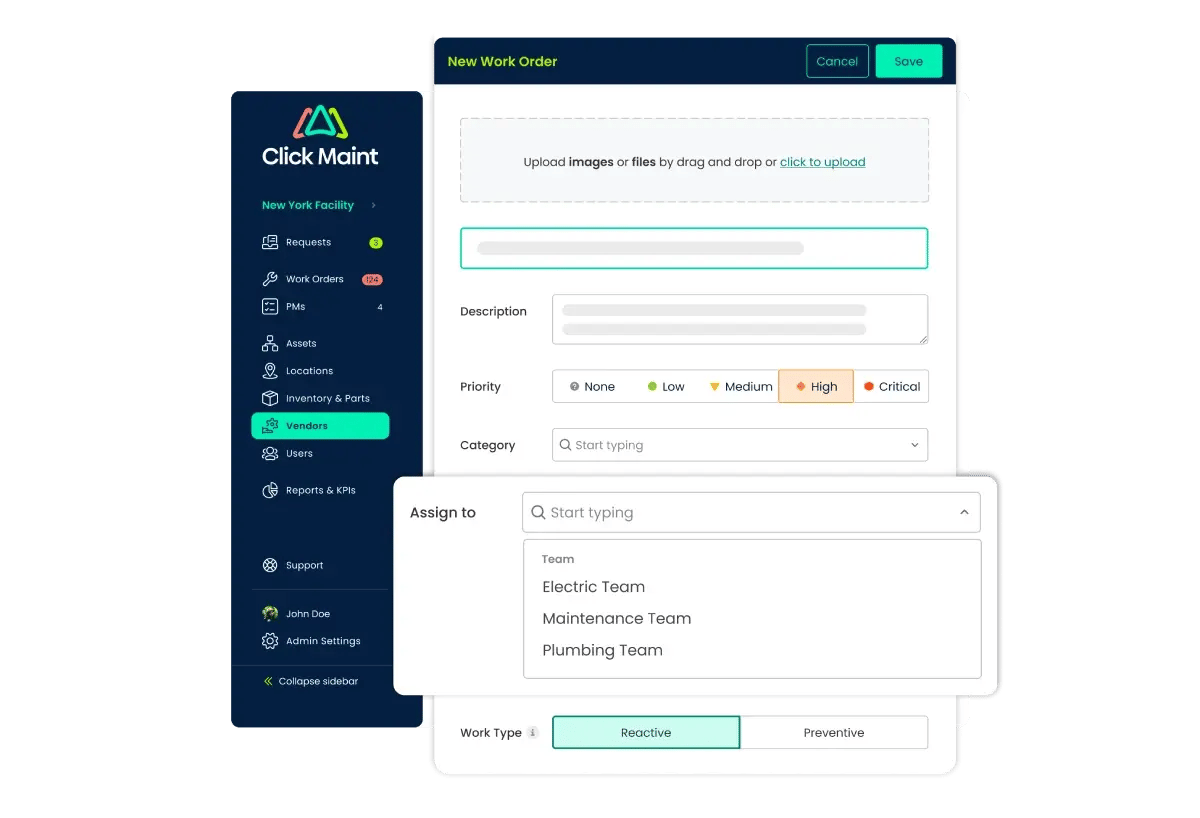
Not ready to Book a Demo yet?
Commercial and Residential Property Management
Manage maintenance tasks and work orders specific to commercial and residential buildings, ensuring building upkeep and high-quality service.
Commercial and Residential Property Management
Manage maintenance tasks and work orders specific to commercial and residential buildings, ensuring building upkeep and high-quality service.
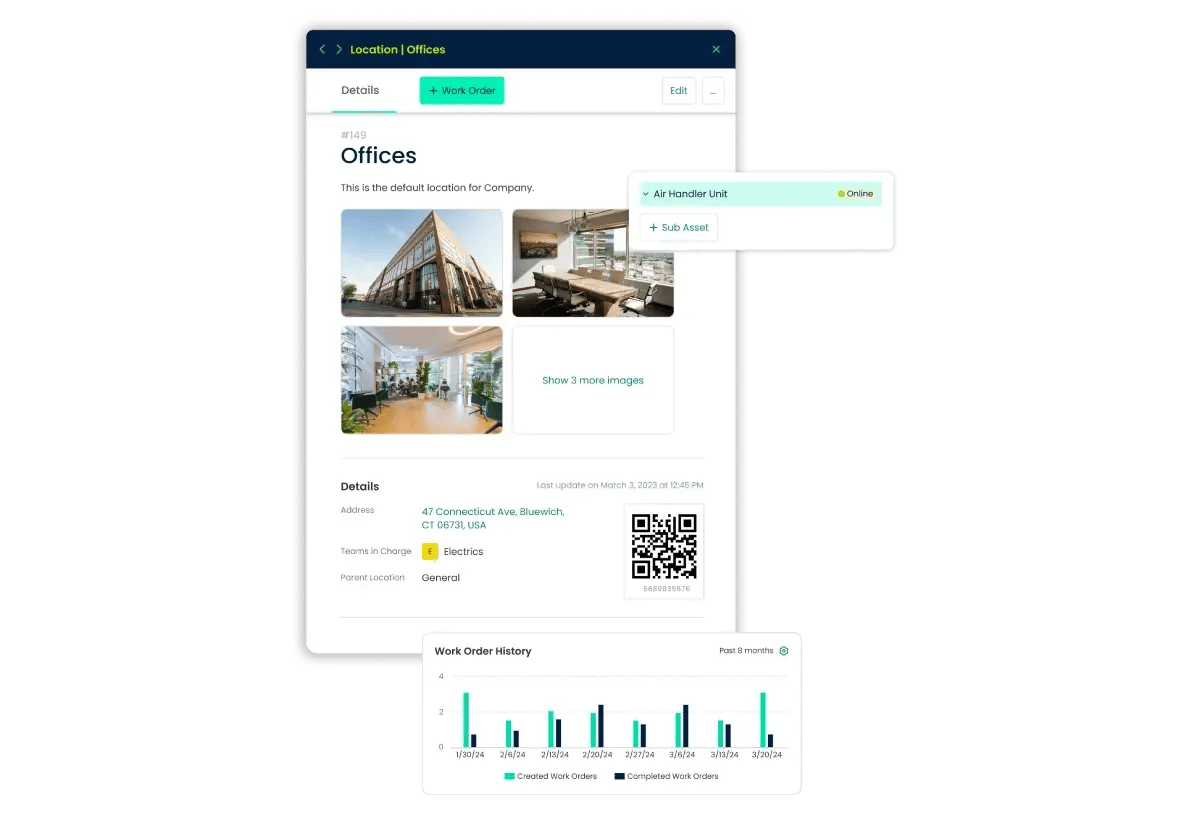
Not ready to Book a Demo yet?
Job Management
Oversee maintenance jobs from assignment to completion, ensuring tasks are completed on schedule and follow standard procedures.
Job Management
Oversee maintenance jobs from assignment to completion, ensuring tasks are completed on schedule and follow standard procedures.
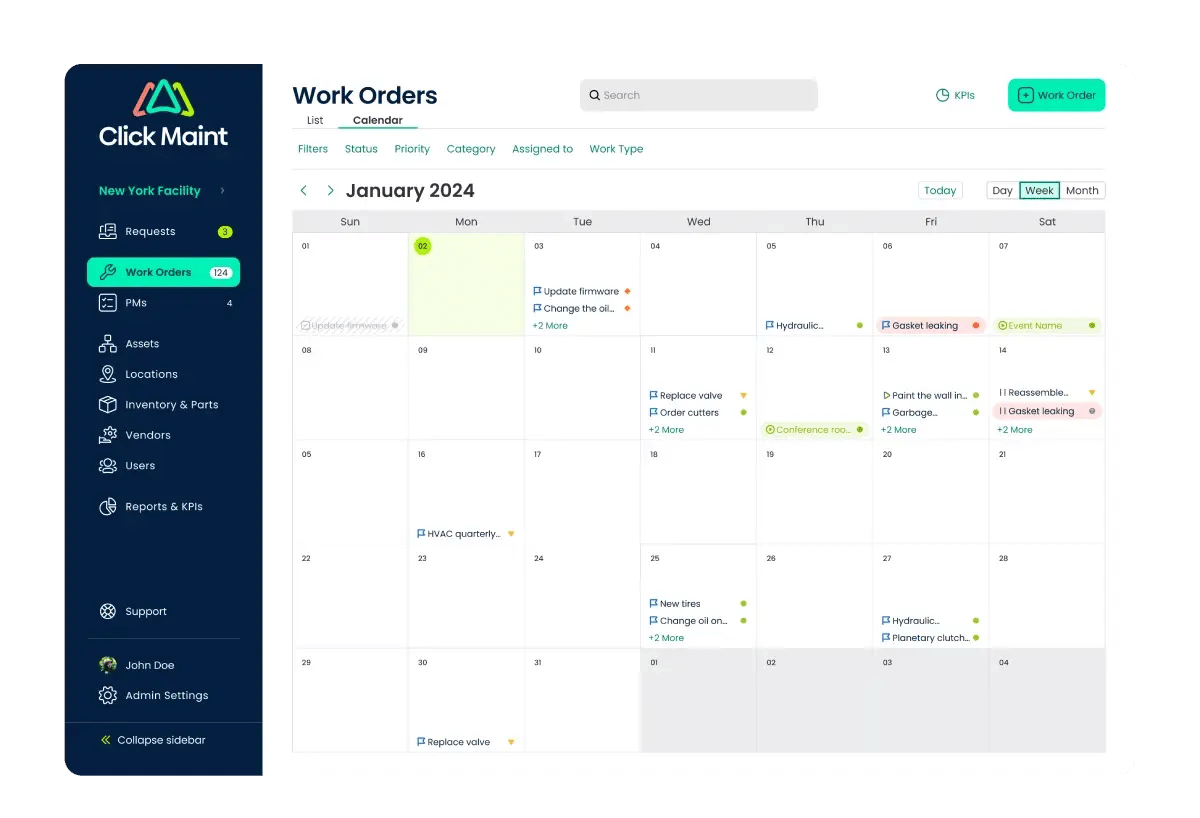
Not ready to Book a Demo yet?
Maintenance Analytics and Reporting
Generate reports and analyze maintenance data to identify trends, improve processes, and support data-driven decision-making.
Maintenance Analytics and Reporting
Generate reports and analyze maintenance data to identify trends, improve processes, and support data-driven decision-making.
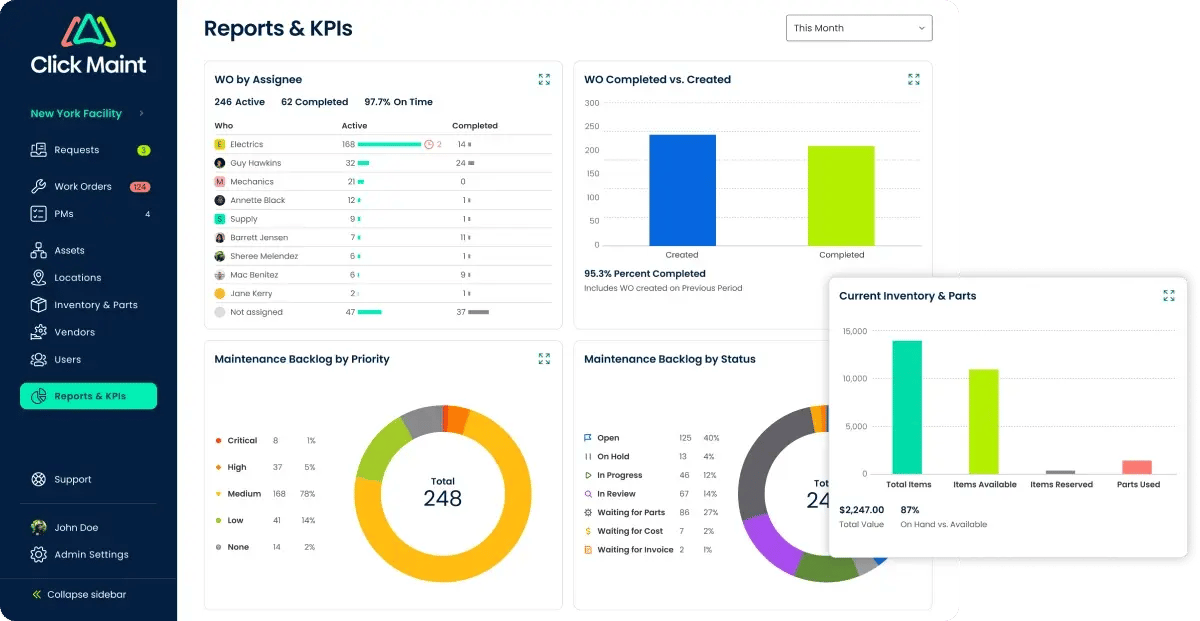
Not ready to Book a Demo yet?
Service History Tracking
Maintain detailed records of past maintenance activities, supporting audits, compliance, and future maintenance planning.
Service History Tracking
Maintain detailed records of past maintenance activities, supporting audits, compliance, and future maintenance planning.
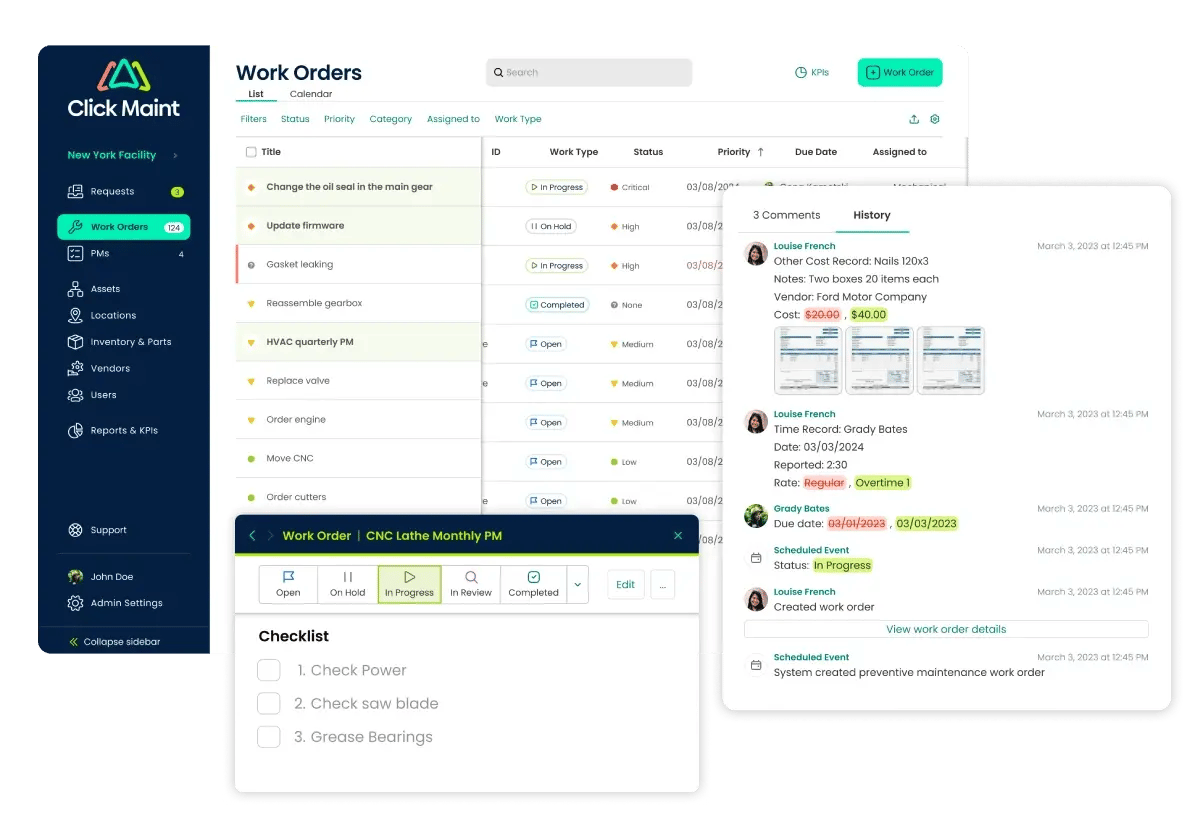
Not ready to Book a Demo yet?
Technician Management
Manage maintenance personnel, including task assignment, scheduling, skills tracking, performance, and labor cost and utilization.
Technician Management
Manage maintenance personnel, including task assignment, scheduling, skills tracking, performance, and labor cost and utilization.
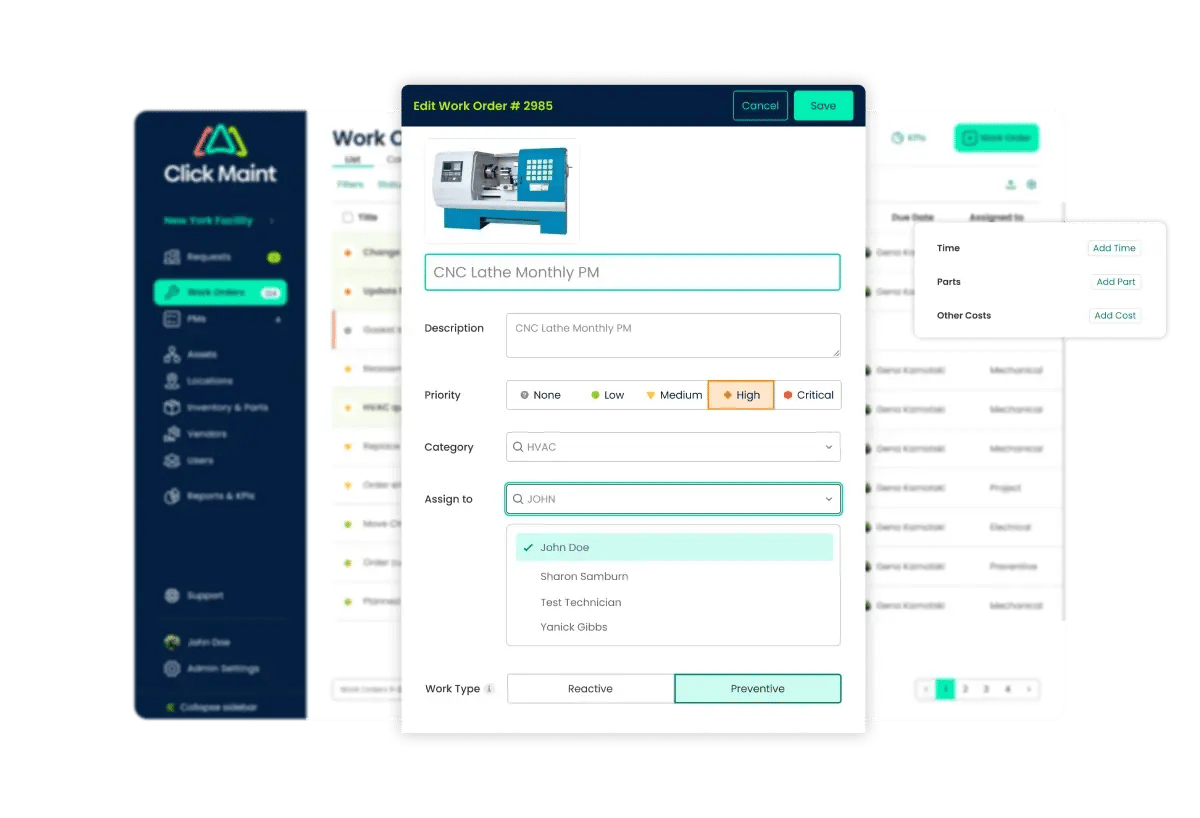
Not ready to Book a Demo yet?
Facility Management
Oversee all aspects of facility maintenance, including equipment management, incident response, and vendor relationships.
Facility Management
Oversee all aspects of facility maintenance, including equipment management, incident response, and vendor relationships.
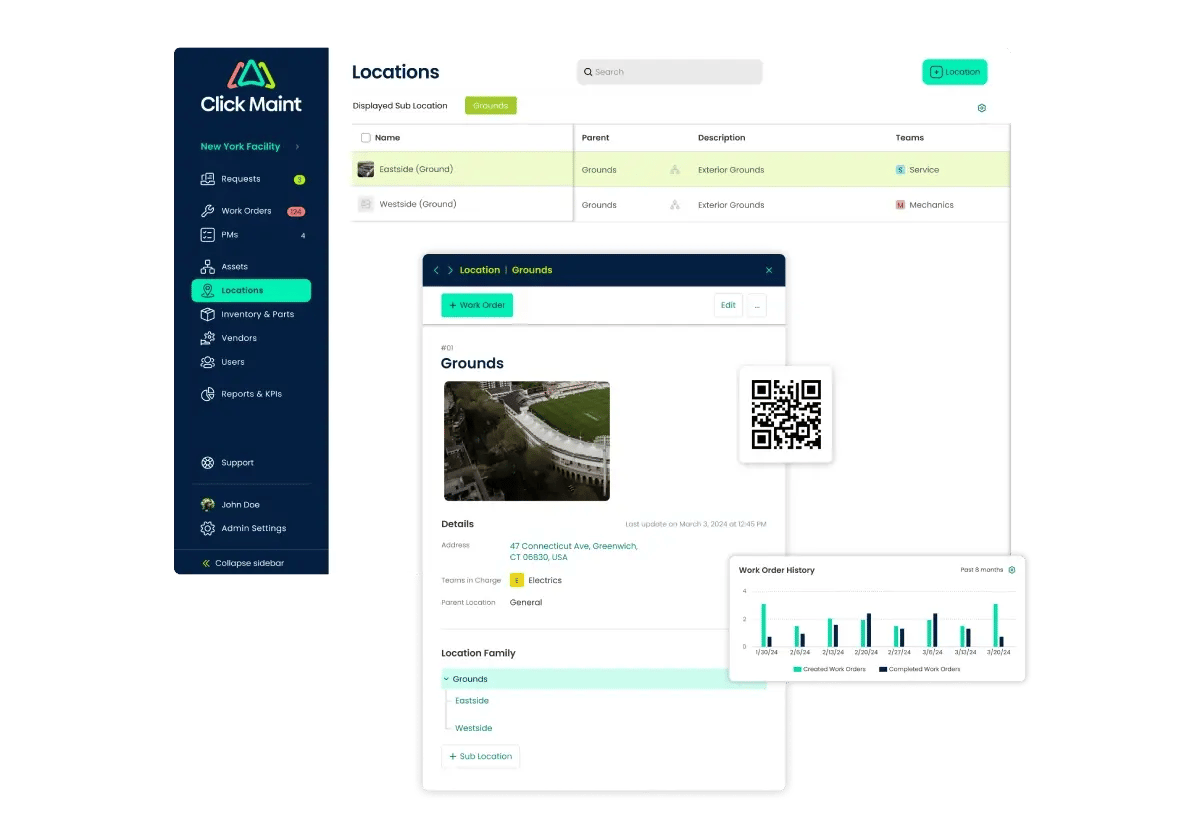
Not ready to Book a Demo yet?
Recurring Appointments
Automate the scheduling of recurring maintenance tasks, ensuring consistency and reduced manual effort.
Recurring Appointments
Automate the scheduling of recurring maintenance tasks, ensuring consistency and reduced manual effort.
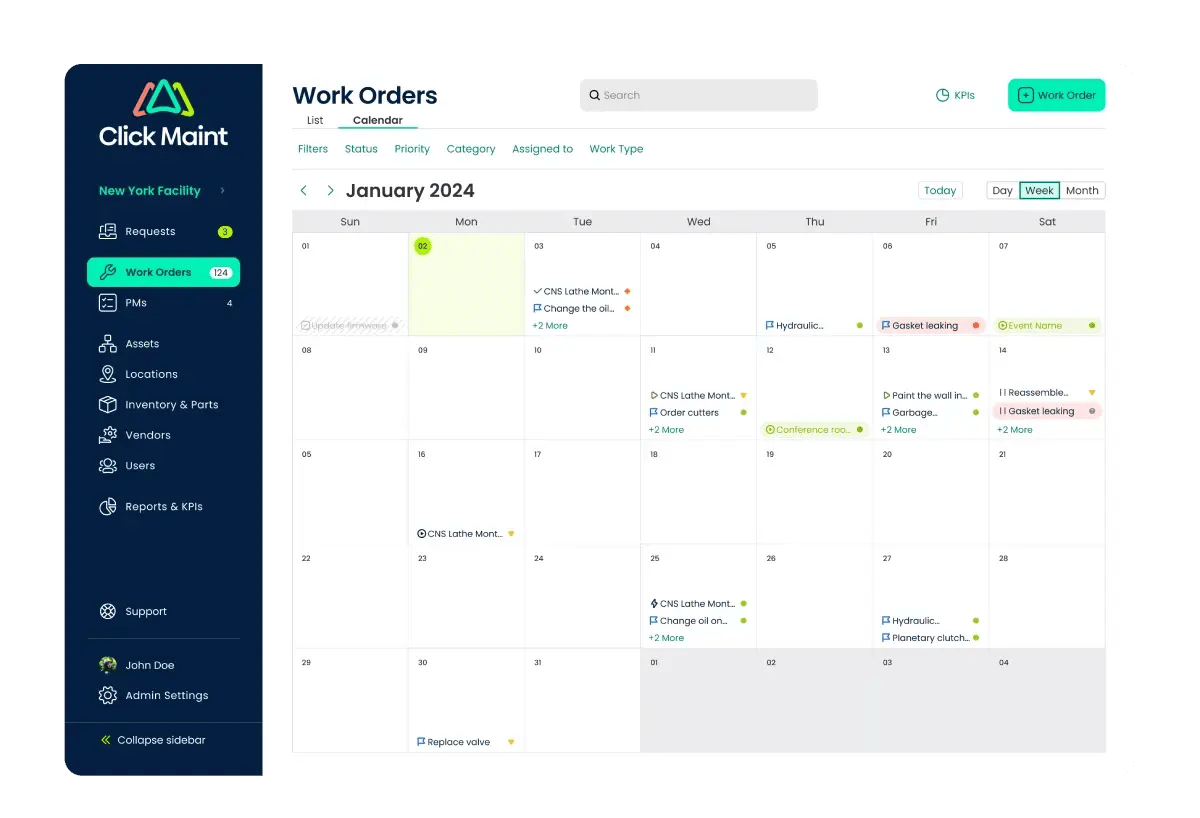
Not ready to Book a Demo yet?
Customer Support and Training (knowledge base)
Access support resources and training materials from our knowledge base and Youtube channel to help users get the most out of the CMMS software.
Customer Support and Training (knowledge base)
Access support resources and training materials from our knowledge base and Youtube channel to help users get the most out of the CMMS software.
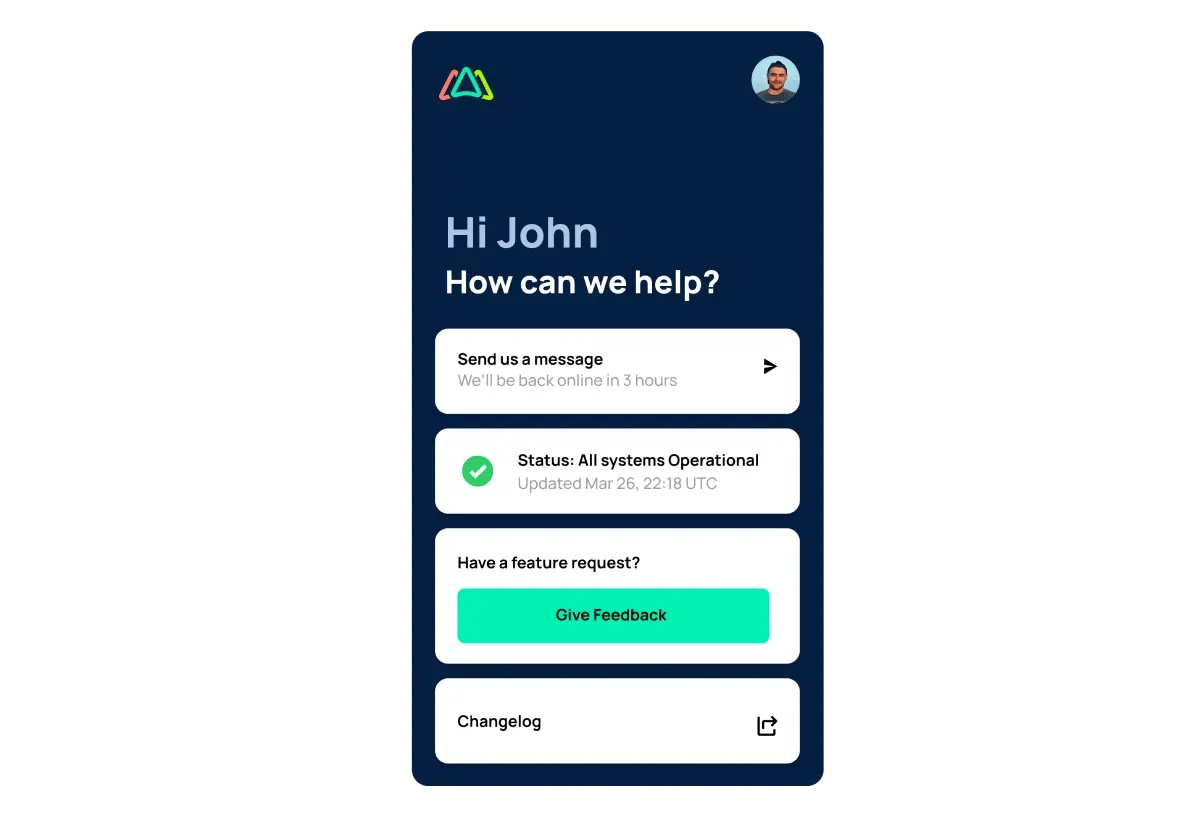
Not ready to Book a Demo yet?
To-Do List and Reminders
Use automated reminders and to-do lists to ensure maintenance tasks are completed on time and with consistency.
To-Do List and Reminders
Use automated reminders and to-do lists to ensure maintenance tasks are completed on time and with consistency.
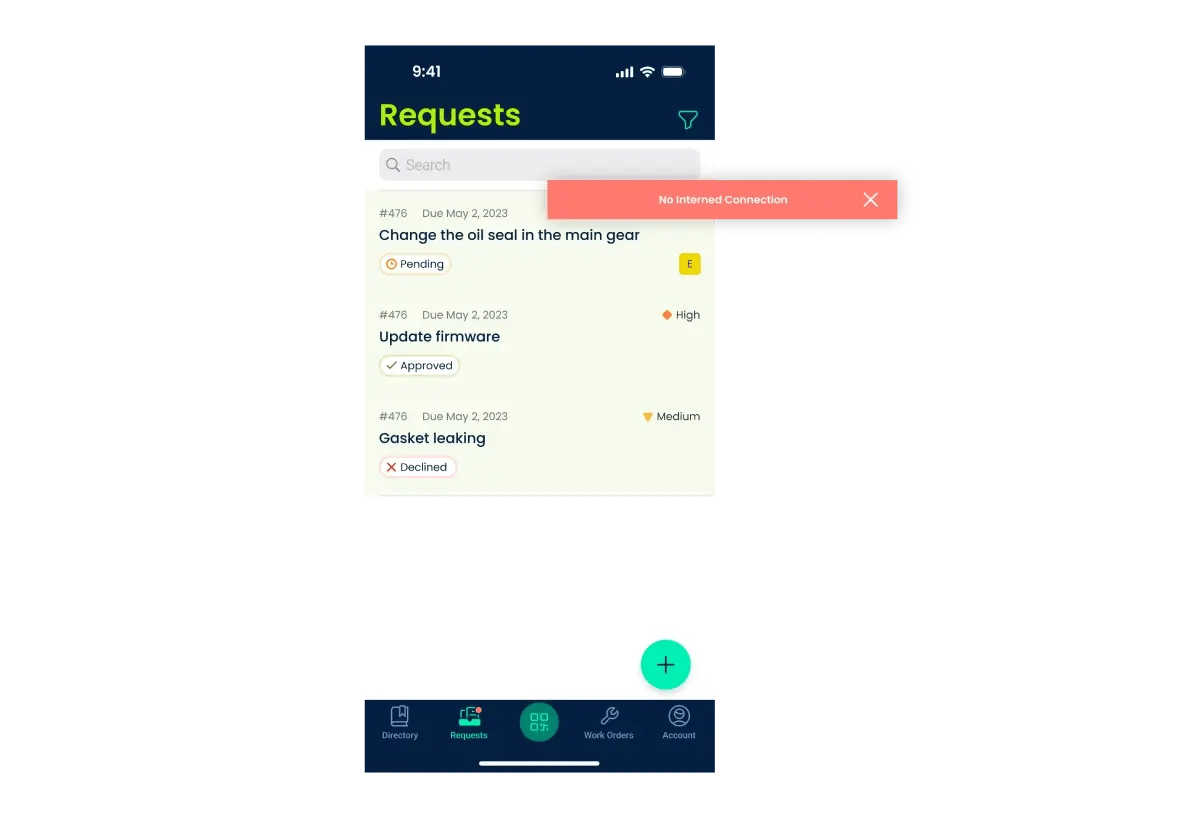
Not ready to Book a Demo yet?
Vendor Management
Coordinate with external vendors, managing service contracts and ensuring timely delivery of materials and services.
Vendor Management
Coordinate with external vendors, managing service contracts and ensuring timely delivery of materials and services.
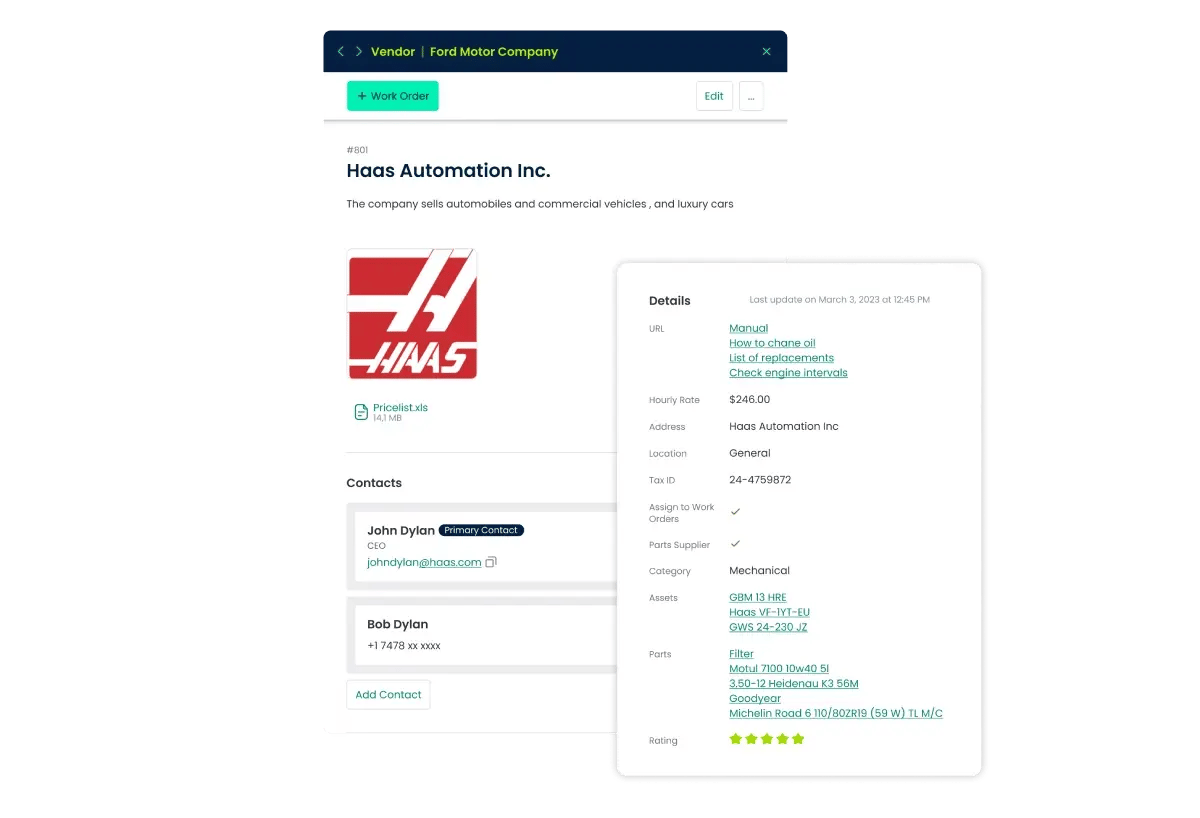
Not ready to Book a Demo yet?
User Permissions and Security
Define user roles and permissions to ensure data security and control access to sensitive information.
User Permissions and Security
Define user roles and permissions to ensure data security and control access to sensitive information.
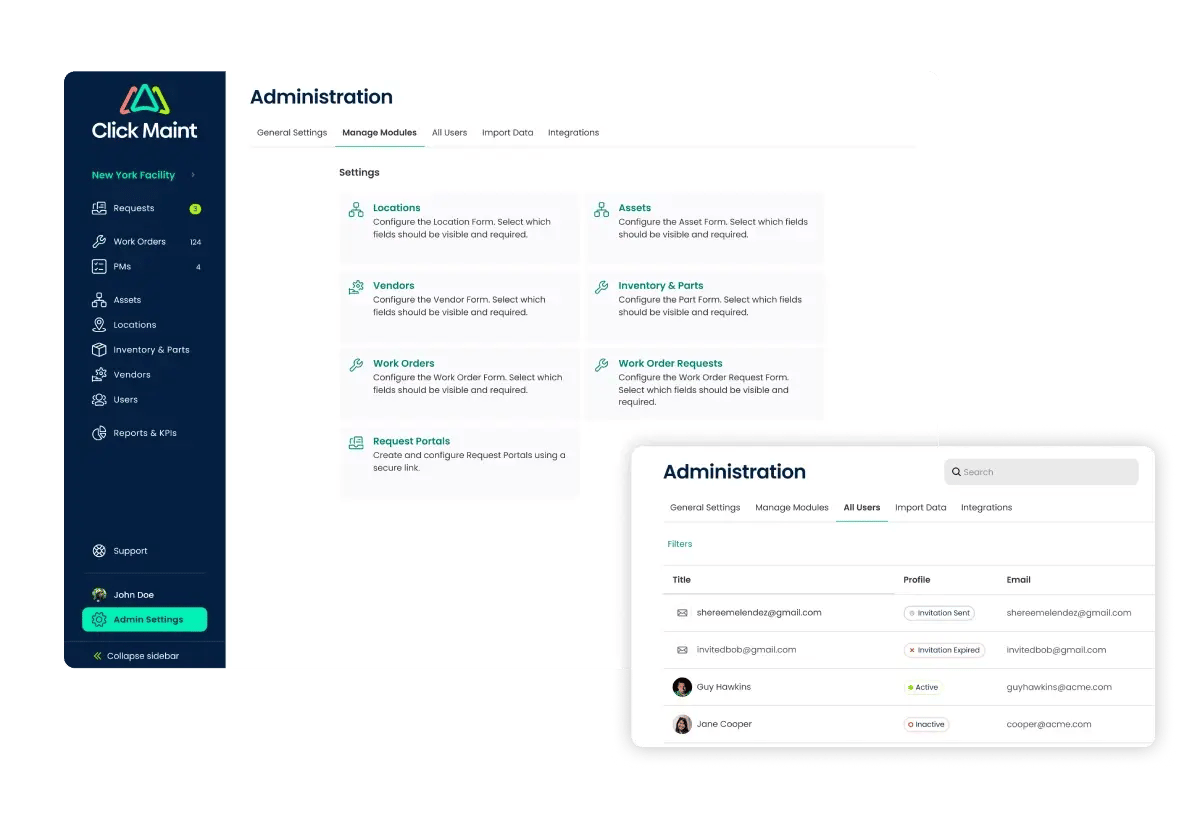
Not ready to Book a Demo yet?
Customizable Dashboards
Configure dashboards to display key performance indicators (KPIs) and other important metrics for quick insights.
Customizable Dashboards
Configure dashboards to display key performance indicators (KPIs) and other important metrics for quick insights.
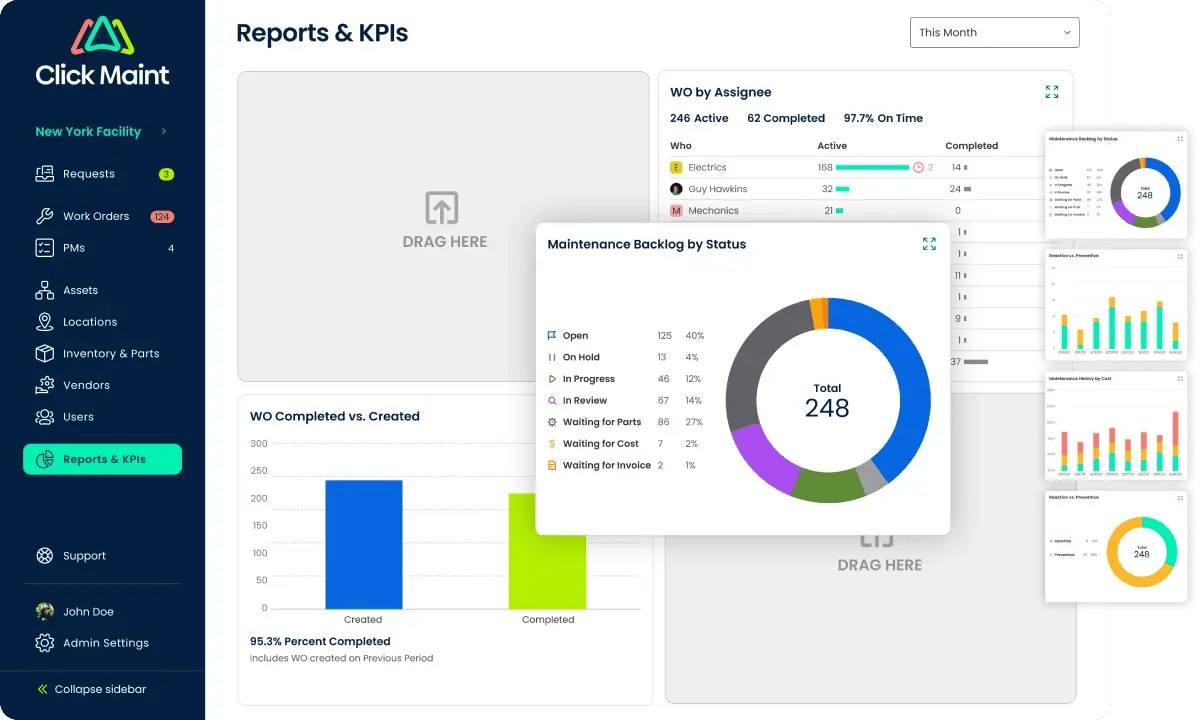
Not ready to Book a Demo yet?
Top 6 Maintenance Management Software Options
Disclaimer- The information provided in this feature comparison has been sourced from multiple review websites. We do not guarantee the accuracy or completeness of the information and advise the user to exercise discretion and make an informed decision while choosing a solution.
SOFTWARE COMPLETE WITH FEATURES TO ACCELERATE MAINTENANCE TEAMS
Functionality designed to optimize maintenance operations.
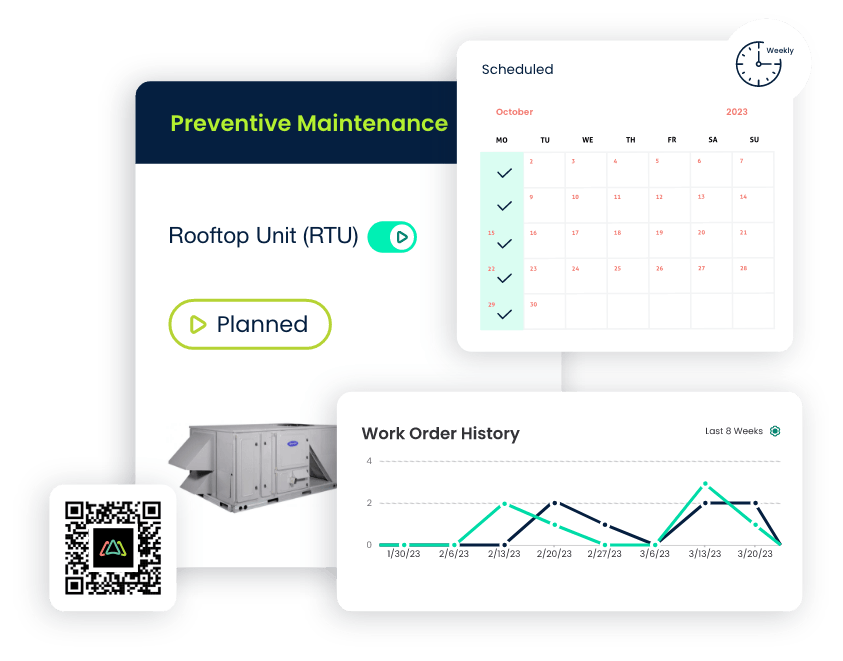
Preventive Maintenance
- Maximize Uptime, Minimize Disruptions
- Schedule maintenance tasks, proactively.
- Choose the type of preventive maintenance most suitable for your assets.
- Send timely alerts to technicians and managers.
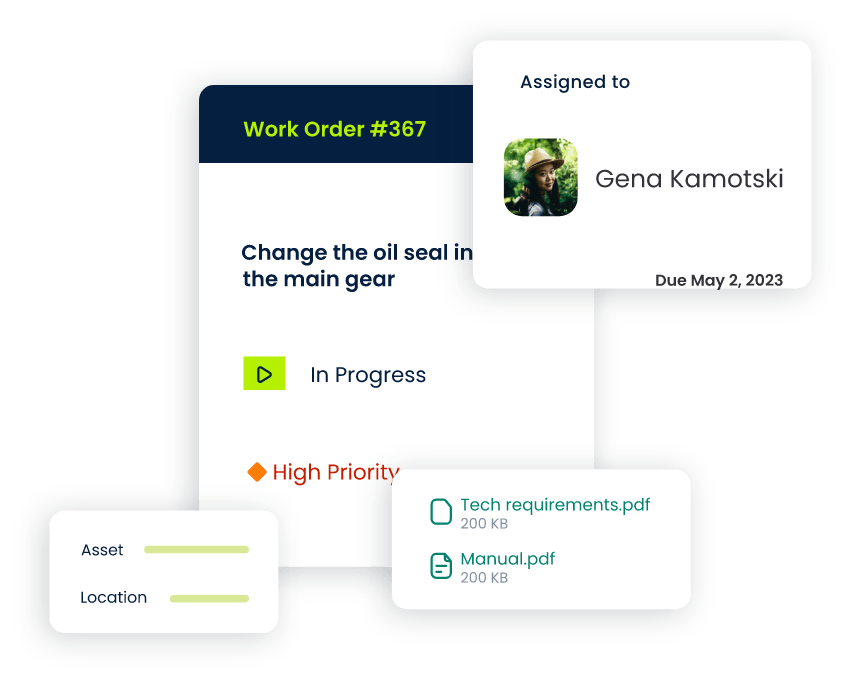
Work Order Management
- Maximize Response Time, Minimize Complexity
- Assign tasks and track progress in real-time.
- Streamline work order scheduling in a single platform.
- Allocate resources efficiently and reduce downtime.
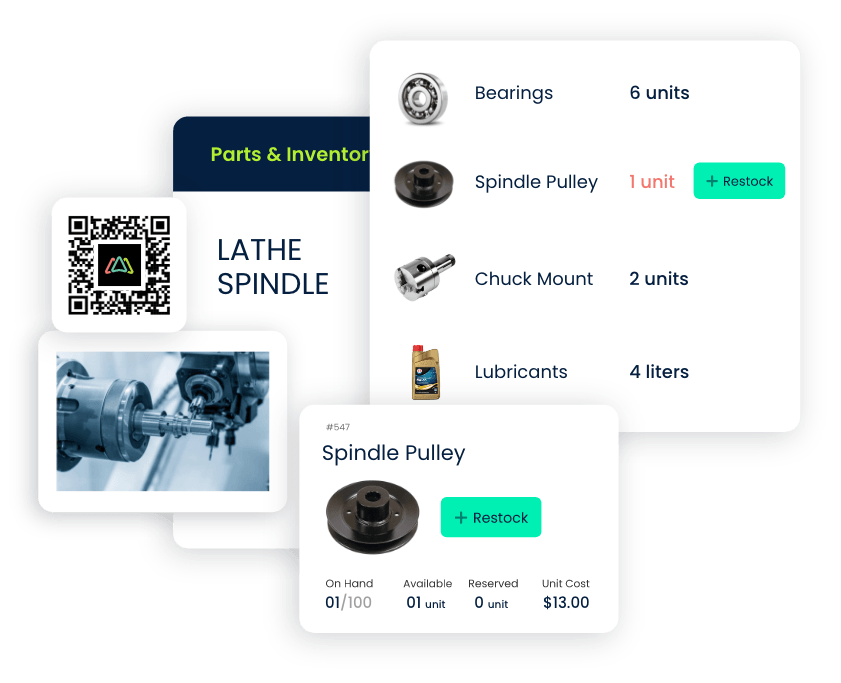
Inventory Management
- Maximize Stock Optimization, Minimize Inventory Costs
- Automate inventory tracking and restocking
- Improve inventory utilization and prevent stockouts and overstocking
- Set up automated reorder workflows and alerts for all stakeholders
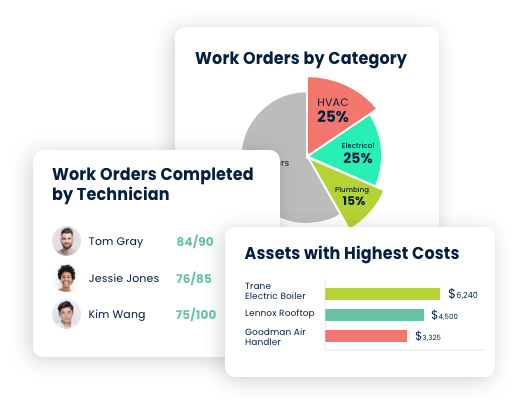
Maintenance Reporting
- Maximize Operational Efficiency, Minimize Data Overload
- Monitor equipment health of all your systems.
- Get accurate, real-time reports on asset performance and maintenance activities.
- Reduce downtime with data-driven decision-making.
Workflow Automation
Automatically assign tasks, send notifications, and trigger actions based on predefined rules, reducing manual effort and improving efficiency. Streamline maintenance activities and ensure timely completion.
Calendar View
Plan and schedule maintenance, inspections, and work orders with ease. Identify resource availability, overlapping schedules, and plan maintenance activities efficiently. Gain a holistic view of your schedule and avoid conflicts.
Complete Asset Registry
Maintain a centralized view of all your equipment and facilities. Capture detailed asset information, including specifications, maintenance history, warranties, and documentation. Easily search and track assets, ensuring effective maintenance planning and optimizing asset lifecycle.
Inventory & Work Order Tracking
Automate tracking of your maintenance activities, work orders, asset history, and maintenance schedules in one central location. Use it to quickly identify trends, anticipate potential issues, and analyze historical data to optimize resource allocation and improve overall maintenance efficiency.
Mobile App
Empower technicians to view and update work orders, perform inspections, access equipment information, and communicate with the team from their mobile devices. Enhance productivity and responsiveness with real-time access to critical maintenance data in the field.
Task Checklists
Create standardized checklists for routine maintenance tasks, inspections, or repairs. Technicians can follow step-by-step instructions, ensuring consistency and accuracy in their work. Track completion status and easily identify pending or overdue tasks.
Maintenance Management Software Implementation Best Practices
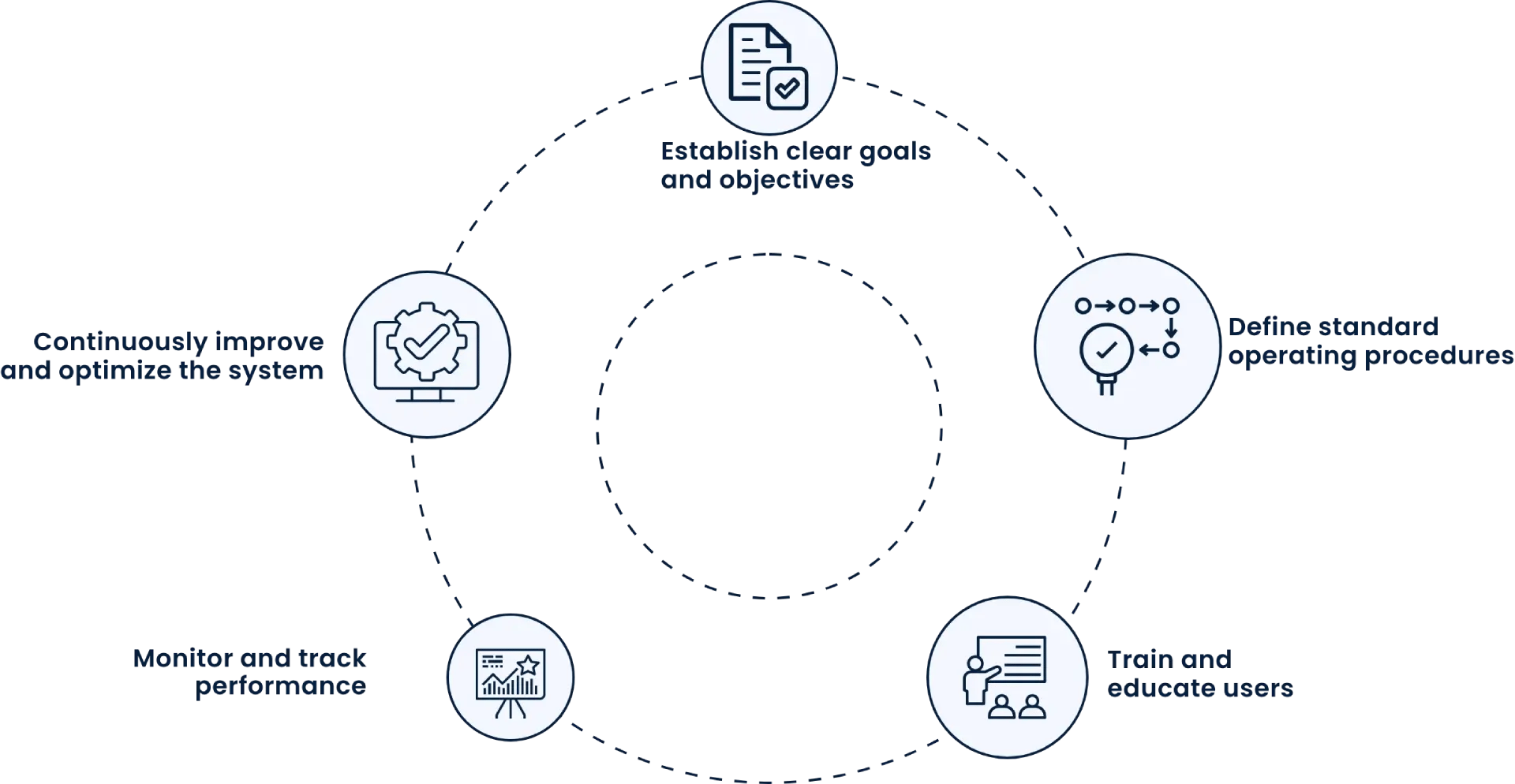
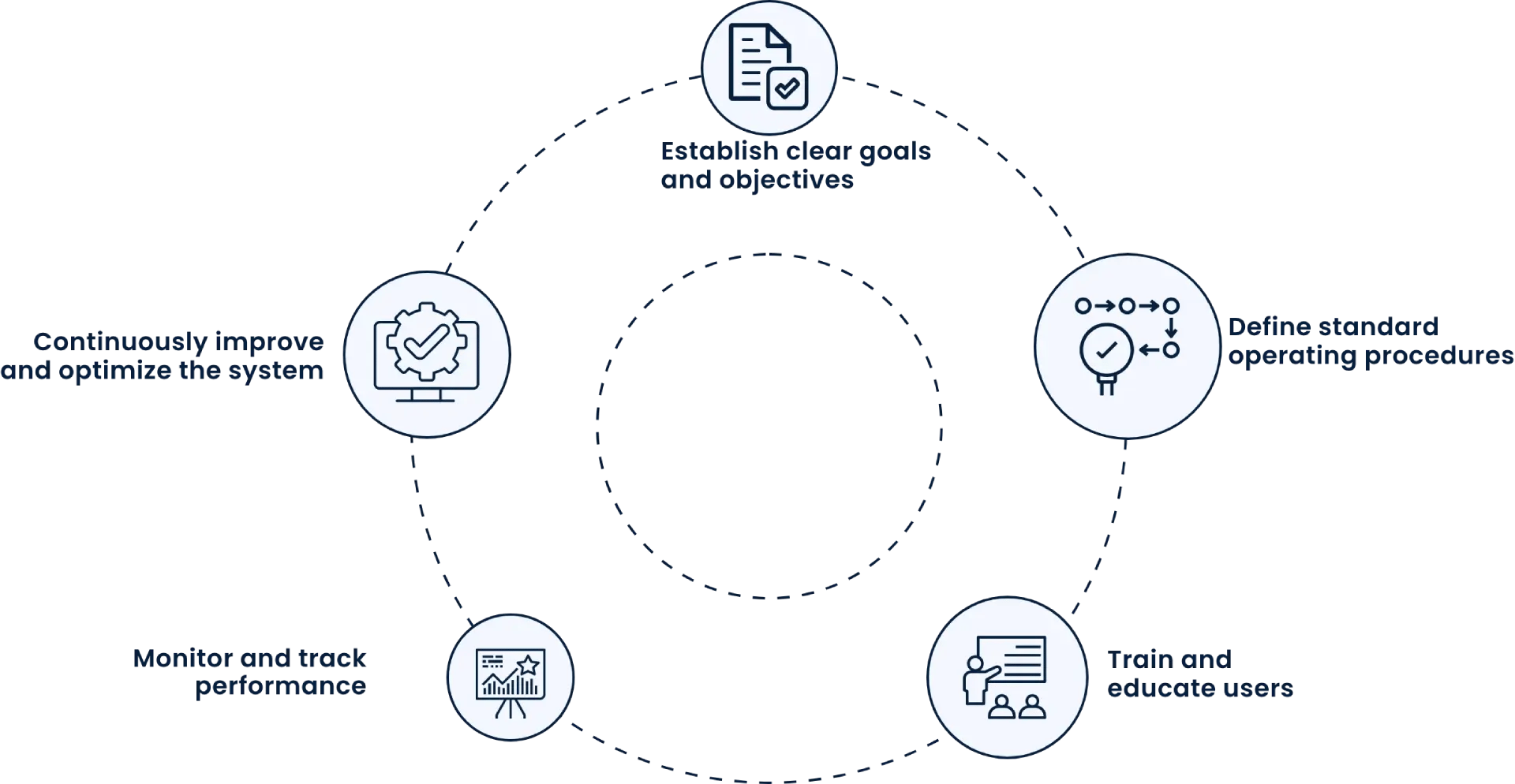
SIMPLE MAINTENANCE MANAGEMENT FOR EVERYONE
Leading buyer profiles across industries and champion personas (both buyers and users) know how to deliver with maintenance software.
Manufacturing
Maintenance software helps manufacturers optimize equipment uptime, reduce maintenance costs, and ensure compliance with safety regulations.
Healthcare
Healthcare facilities maintain critical medical equipment, ensuring patient safety and regulatory compliance while also reducing downtime and repair costs.
Transportation
Facilities managers maintain critical building systems, reducing downtime, and minimizing repair costs, while also ensuring compliance with safety regulations and extending the lifespan of assets.
Energy & Utilities
Energy companies manage their complex infrastructure and equipment, ensuring high levels of uptime, safety, and regulatory compliance.
Higher Education
Colleges and universities maintain their campus buildings and equipment, ensuring student safety, reducing downtime, and minimizing repair costs.
Hotels & Resorts
Maintenance software helps hotels and resorts maintain their properties, ensuring guest satisfaction and minimizing disruptions to operations.
Arenas & Stadiums
Maintenance software helps stadiums and arenas maintain their facilities and equipment, ensuring a positive guest experience, reducing downtime, and minimizing repair costs.
Retail & Restaurants
Maintenance software helps retailers and restaurant owners maintain their buildings and equipment, ensuring customer satisfaction, reducing downtime, and minimizing repair costs.
Religious Institutions & Non-Profits
Religious institutions and non- profit organizations maintain their facilities and equipment, ensuring a safe and welcoming environment, and minimizing repair costs.
Who uses a Maintenance Management Software?
Maintenance Supervisors
Maintenance supervisors streamline the maintenance process, schedule preventive maintenance activities, track maintenance history, and assign work orders. It also provides real-time insights into the maintenance performance and helps in resource allocation and planning.
Maintenance Technicians
Maintenance software helps technicians to view and manage work orders, update maintenance records, and track inventory and spare parts. It also provides access to equipment manuals, schematics, and other technical documents.
Asset Managers
Maintenance software helps asset managers to monitor the condition of assets, track the maintenance history, and plan for capital expenditures. It also provides insights into asset utilization, downtime, and performance, which helps in making informed decisions about asset replacement and maintenance.
Procurement Managers
Maintenance software helps procurement managers to track inventory and spare parts, manage vendors and contracts, and plan for procurement activities. It also provides real-time insights into inventory levels, which helps in making informed decisions about inventory management and procurement.
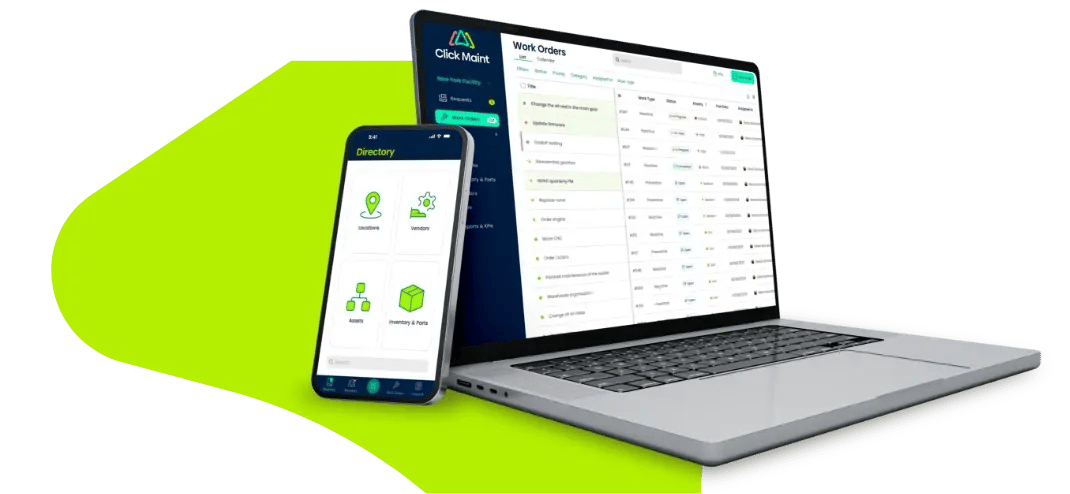
Optimize your maintenance operations with Maintenance Management Software
Maintenance Management Software
Everything you need to know
What is Maintenance Management Software?
Maintenance management software, often called a Computerized Maintenance Management System (CMMS), is software designed to help organizations manage their maintenance operations efficiently. It provides tools for tracking assets, scheduling maintenance, managing work orders, and monitoring inventory, ultimately reducing downtime and improving overall operational efficiency.
It is a type of computer program that helps organizations manage their maintenance operations more efficiently. The software can be used to track assets, schedule and assign maintenance tasks, monitor equipment and inventory, and generate reports.
It typically includes a range of features such as work order management, preventive maintenance scheduling, asset tracking, inventory management, and reporting. Some software may also offer advanced features such as predictive maintenance and mobile access.
The benefits of using maintenance management software include improved equipment uptime, increased efficiency and productivity, better asset utilization, reduced maintenance costs, and improved compliance with regulations and safety standards. It is commonly used in industries such as manufacturing, healthcare, transportation, and facilities management.
Key Features and Benefits:
Asset Tracking:
CMMS systems help organizations keep track of all their assets, including equipment, machinery, and building appliances.
Work Order Management:
They facilitate the creation, assignment, and tracking of work orders, ensuring that maintenance tasks are completed on time and efficiently.
Preventive Maintenance Scheduling:
CMMS allows for the scheduling of routine maintenance tasks to prevent failures and extend the lifespan of assets.
Inventory Management:
They help track spare parts and other materials needed for maintenance, ensuring that the right supplies are available when needed.
Real-time Tracking and Reporting:
CMMS systems often provide real-time visibility into maintenance activities, allowing for quick response to issues and improved decision-making.
Cost Reduction:
By optimizing maintenance processes, CMMS helps reduce downtime, extend asset lifespans, and minimize maintenance costs.
Different Types of Maintenance Management Software
There are several types of maintenance management software available in the market, each designed to meet the specific needs of different industries and organizations. Some of the common types of maintenance management software are:
Computerized Maintenance Management System (CMMS)
This is a software that is designed to manage and schedule maintenance tasks for equipment, facilities, and assets. CMMS software typically includes features such as work order management, asset tracking, inventory management, preventive maintenance scheduling, and reporting.
Enterprise Asset Management (EAM)
This is a more comprehensive software that not only manages maintenance tasks but also helps organizations optimize their asset lifecycle, from acquisition to disposal. EAM software typically includes features such as asset tracking, work order management, inventory management, preventive maintenance scheduling, procurement, and reporting.
Facility Management Software (FMS)
This software is designed to manage and maintain facilities, such as buildings and grounds. FMS software typically includes features such as space management, lease management, maintenance management, asset tracking, and reporting.
Field Service Management (FSM)
This software is designed for organizations that provide maintenance and repair services on- site, such as HVAC and plumbing services. FSM software typically includes features such as scheduling, dispatching, work order management, mobile access, and reporting.
Predictive Maintenance (PdM)
A predictive maintenance software uses data analytics and machine learning to predict when equipment is likely to fail, allowing organizations to perform maintenance before a breakdown occurs. PdM software typically includes features such as data analysis, predictive modeling, and reporting.
By integrating AI-powered predictive analytics with IoT sensors, modern maintenance software can monitor equipment conditions in real time, offering unprecedented insights into asset performance. This enables maintenance teams to shift from reactive or scheduled maintenance to truly predictive strategies, reducing unplanned downtime and extending the life of critical assets. IoT sensors collect real-time data on variables like temperature, vibration, and energy consumption, while AI analyzes this data to predict when maintenance should occur. These advancements help organizations avoid costly equipment failures and optimize maintenance schedules.
The Role of Mobile Access in Modern Maintenance Operations
Mobile accessibility is an essential feature of maintenance management software, especially for industries where fieldwork is prevalent. Maintenance teams can now access work orders, asset histories, and real-time data directly from mobile devices, allowing for quicker response times and improved task efficiency. Mobile apps often support offline functionality, enabling technicians to continue their work in remote locations without internet access. Furthermore, mobile integration promotes better communication across teams, providing real-time updates and photos directly from the field, ensuring that any issues or roadblocks are swiftly addressed. This capability can significantly improve productivity and reduce delays in industries such as utilities, field services, and manufacturing.
Challenges with Maintenance Software
While maintenance management software can bring many benefits to organizations, there are also several challenges that need to be considered. Some of the common challenges include:
Data accuracy and integrity
Maintenance software relies heavily on accurate and up-to-date data to function properly. If the data entered into the system is inaccurate or incomplete, it can lead to incorrect decisions being made or maintenance tasks being missed.
User adoption and training
Maintenance management software can be complex and require a significant investment of time and resources to implement. Ensuring that users are properly trained and adopt the software can be a challenge, and lack of adoption can undermine the effectiveness of the system.
Integration with existing systems
Many organizations already have multiple systems in place, such as ERP or asset management systems. Integrating the maintenance management software with these systems can be a challenge and require significant IT resources.
Customization and configuration
Every organization has unique maintenance management needs and workflows. Customizing and configuring the software to meet these needs can be time-consuming and require technical expertise.
Cost
In a big-ticket enterprise implementation context, maintenance software can be expensive to purchase, implement, and maintain. Organizations need to carefully evaluate the costs and benefits of implementing the software before making a decision. Cloud based software like Click Maint maintenance management software have solved this challenge to a large extent.
Security and privacy
Maintenance software often contains sensitive data about equipment, assets, and personnel. Ensuring that the software is secure and complies with privacy regulations can be a challenge, particularly for cloud-based solutions.
Recommended Reads
Here are some articles we recommend you also go through:
What is Maintenance management software?
How to find the right Maintenance Management Software?
What is Maintenance Management Software? Examples & Benefits