React and Restore: A Comprehensive Guide to Reactive Maintenance
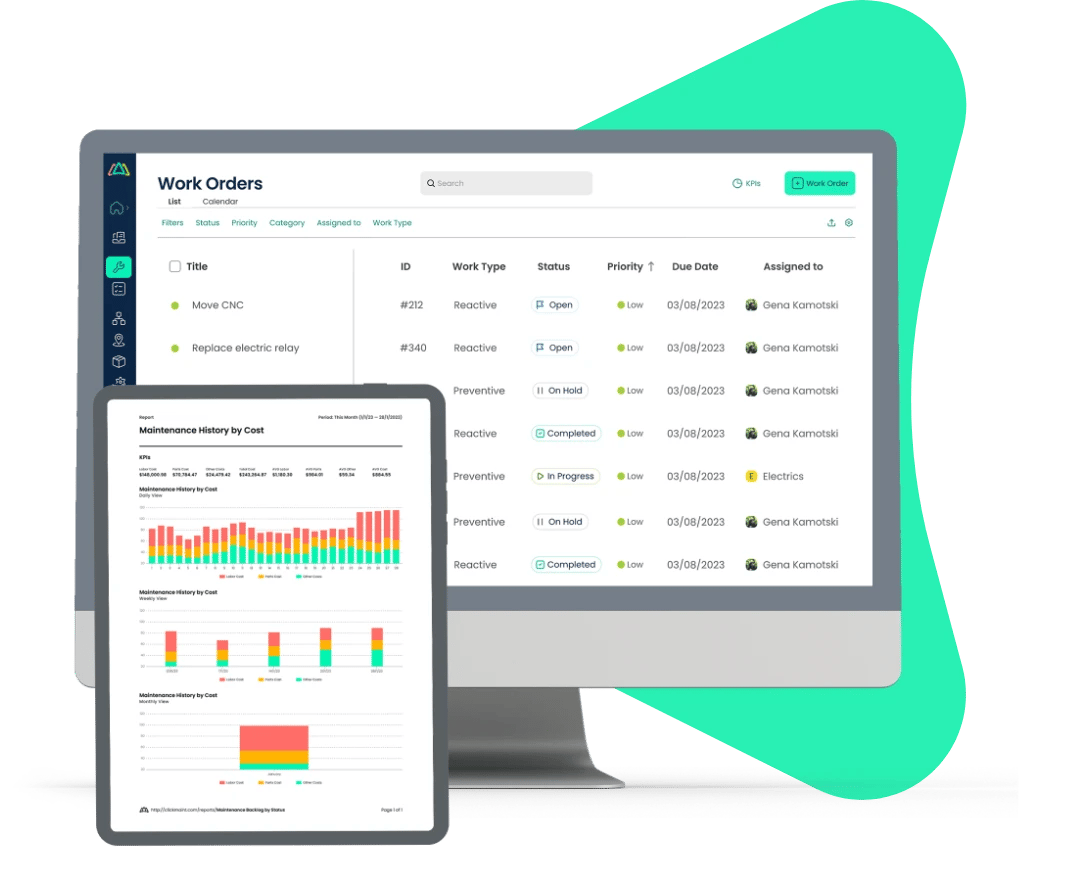
TABLE OF CONTENTS
Reactive Maintenance, often referred to as "breakdown maintenance" or "run-to-failure," is a maintenance strategy that involves addressing equipment issues and conducting repairs only when failures occur. Unlike preventive maintenance, which is based on scheduled inspections and proactive upkeep, reactive maintenance responds to unexpected breakdowns, malfunctions, or emergencies. The focus, in the case of reactive maintenance, is on addressing the immediate problems as they arise, with the primary goal of restoring functionality and minimizing downtime.
In industries where equipment downtime directly impacts production schedules, revenue, and overall efficiency, reactive maintenance helps minimize the negative impact on productivity by swiftly restoring operations to normalcy. Furthermore, reactive maintenance can be particularly relevant in situations where the root causes of potential failures are challenging to identify through routine inspections alone. The ability to respond rapidly to unexpected issues is a hallmark of an effective reactive maintenance strategy, making it an indispensable component of a comprehensive maintenance approach.
Types of Reactive Maintenance
Based on the nature and urgency of equipment issues, these are the distinct types of reactive maintenance that organizations can deploy:
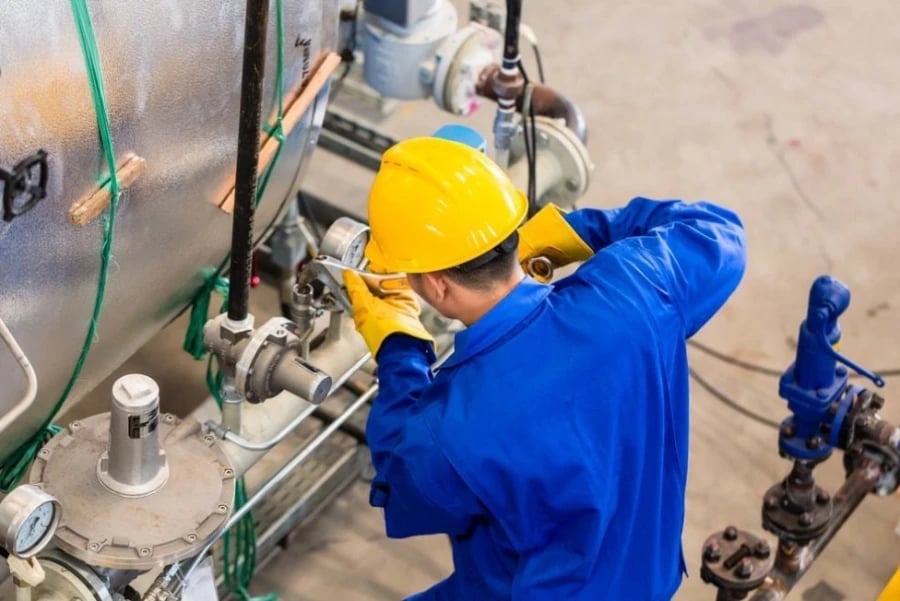
Breakdown Maintenance
Breakdown maintenance, also known as "fix it when it breaks," is the most straightforward type of reactive maintenance. This approach involves addressing equipment failures as they occur, with the primary focus on restoring functionality quickly. Organizations employing breakdown maintenance operate under the assumption that unexpected failures are inevitable, and their response is geared towards minimizing downtime.
Key Characteristics:
- Reactive response to equipment failures.
- Minimal or no pre-planned maintenance activities.
- Immediate attention to restore the system to operational status.
Best Suited For:
- Equipment with low maintenance requirements.
- Situations where downtime has minimal impact on operations.
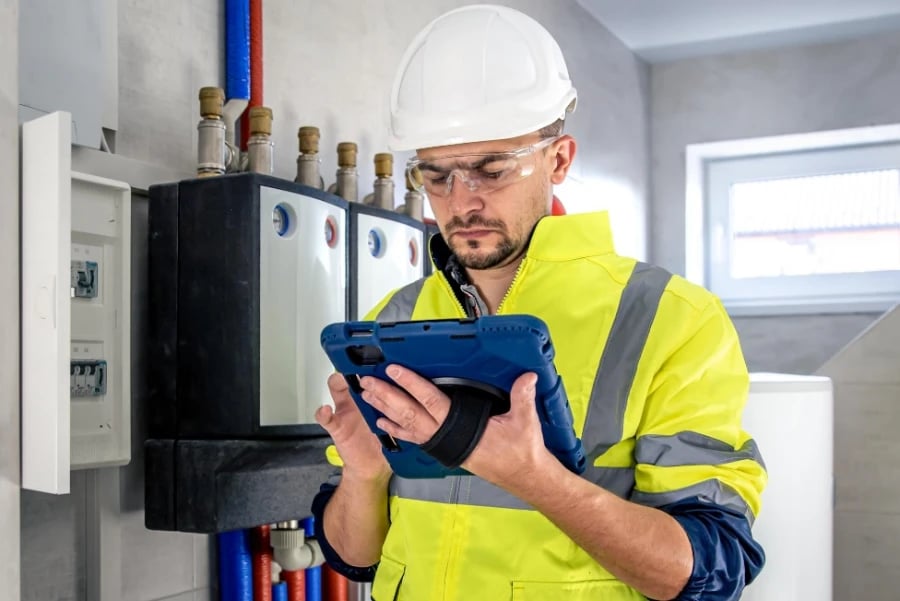
Corrective Maintenance
Corrective maintenance is a broader category that encompasses a planned, reactive response to identified issues. Unlike breakdown maintenance, corrective maintenance involves recognizing potential problems through routine inspections or monitoring and then scheduling maintenance activities to address those issues. It is a proactive yet reactive approach aimed at preventing complete breakdowns.
Key Characteristics:
- Identification of issues through inspections or monitoring.
- Scheduled maintenance activities in response to identified problems.
- Balancing proactive and reactive elements for comprehensive maintenance.
Best Suited For:
- Equipment with known failure patterns.
- Situations where a balance between preventive and reactive maintenance is required.
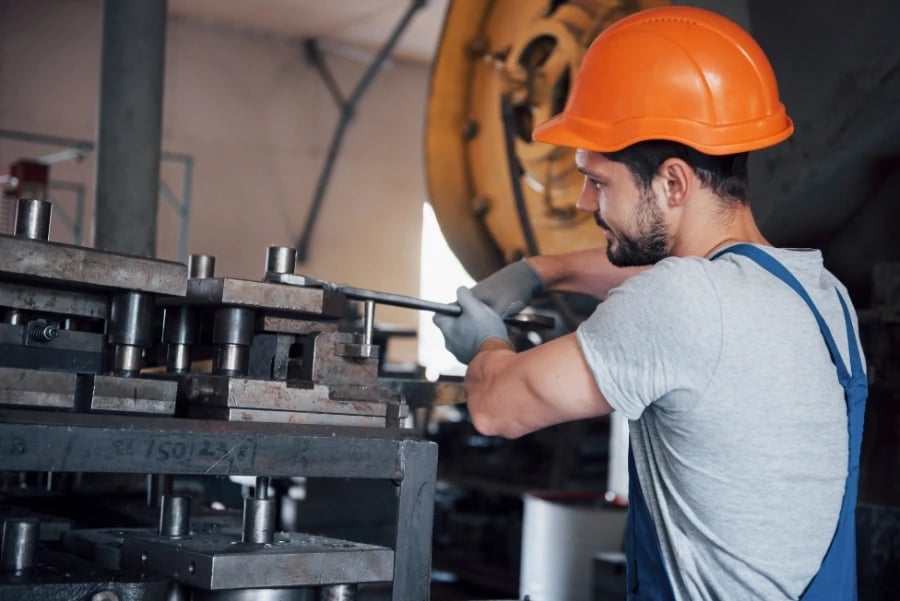
Emergency Maintenance
Emergency maintenance is the most urgent and critical type of reactive maintenance, necessitated by unforeseen events that pose an immediate threat to operations, safety, or the environment. This type of maintenance requires an immediate response to prevent catastrophic consequences. Emergency maintenance is often reserved for situations where a failure could result in severe consequences, and swift action is essential.
Key Characteristics:
- Immediate response to critical failures.
- Addressing issues that pose an imminent threat.
- Prioritizing safety and preventing severe operational disruptions.
Best Suited For:
- High-risk equipment or systems.
- Situations where delay in maintenance could lead to safety hazards.
Understanding the nuances of these reactive maintenance types allows organizations to tailor their approaches based on the criticality of the equipment, the impact of potential failures, and the available resources for maintenance activities.
Common Scenarios Requiring Reactive Maintenance
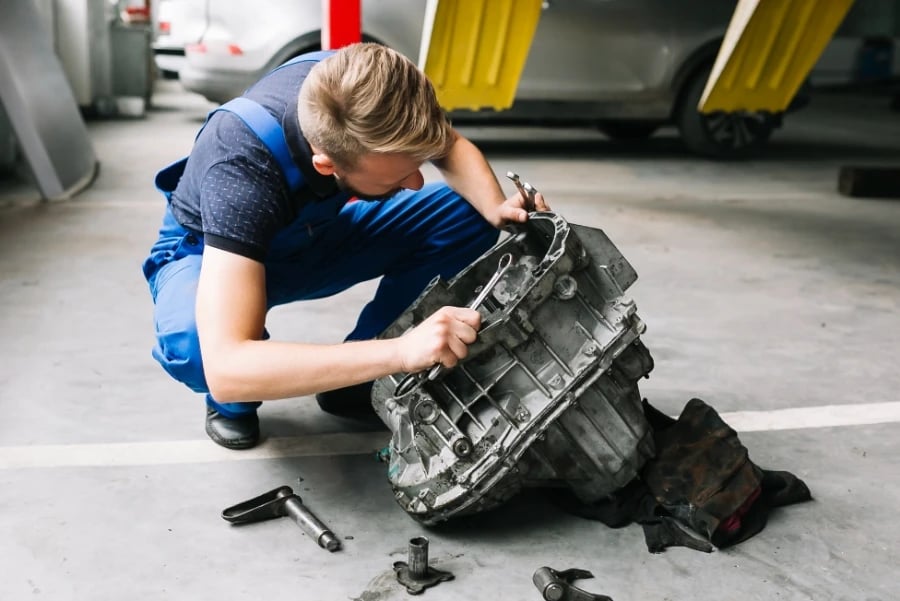
Equipment Breakdowns
Equipment breakdowns are perhaps the most common scenario requiring reactive maintenance. Despite regular preventive measures, machinery and systems can unexpectedly fail due to wear and tear, component malfunctions, or unforeseen issues. In these instances, reactive maintenance becomes essential to swiftly diagnose and address the root cause, facilitating the prompt restoration of operational capabilities.
Key Characteristics:
- Sudden cessation of equipment functionality.
- Occurs despite routine maintenance efforts.
- Requires immediate attention to resume normal operations.
Mitigation Strategies:
- Rapid response protocols.
- Proactive monitoring to identify signs of impending breakdowns.
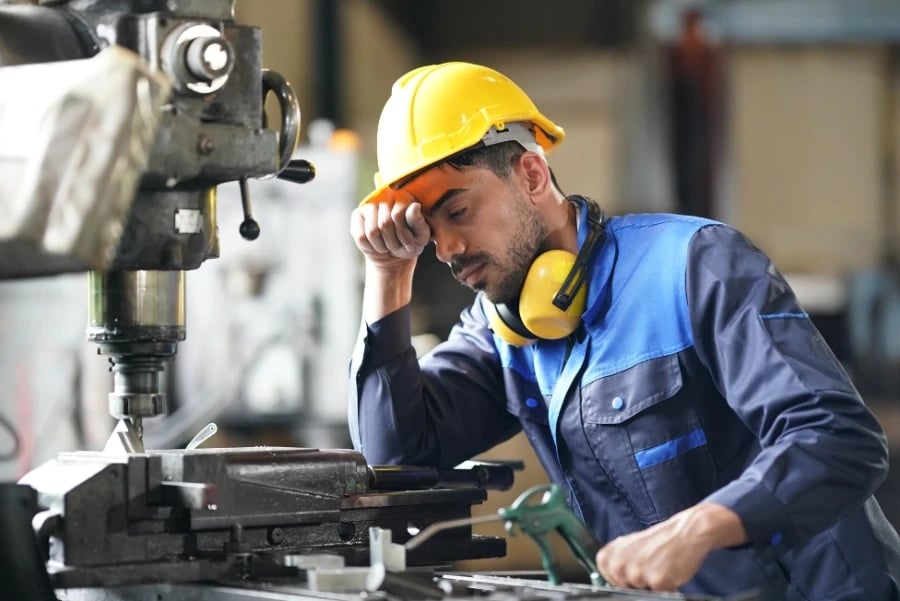
Unexpected Failures
Beyond routine wear and tear, unexpected failures can occur due to factors such as manufacturing defects, design flaws, or environmental influences. Reactive maintenance is instrumental in responding to these unforeseen events, providing organizations with the agility to address issues that may not be predictable through regular inspections alone.
Key Characteristics:
- Failures not anticipated in regular maintenance schedules.
- Occurrence linked to external factors or design issues.
- Necessitates prompt diagnosis and resolution.
Mitigation Strategies:
- Enhanced monitoring and data analysis.
- Collaboration with equipment manufacturers for defect identification.
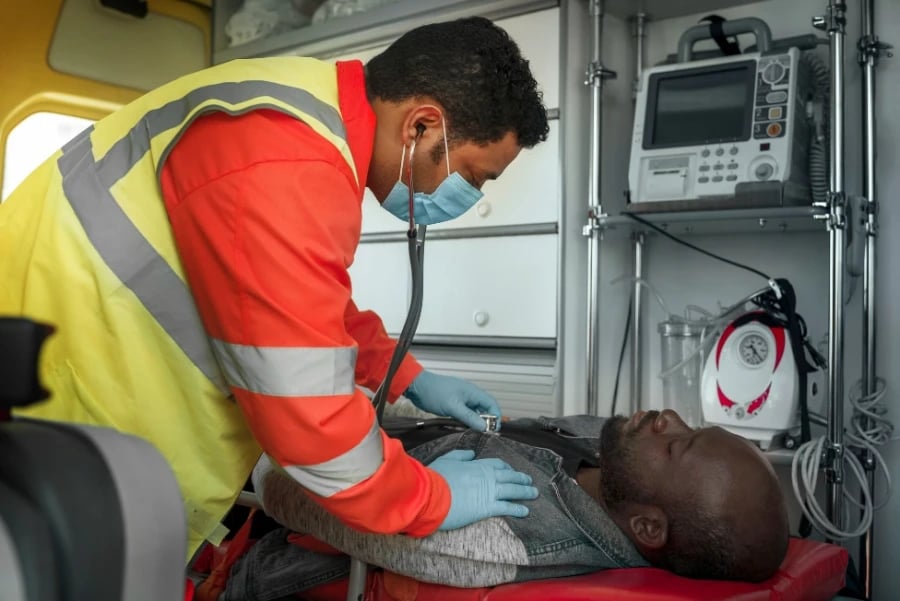
Emergency Situations
Certain scenarios demand an immediate and decisive response to prevent severe consequences. Emergency situations, such as system malfunctions posing safety hazards or environmental risks, require a specialized form of reactive maintenance. In these critical moments, the focus is on containing the situation, minimizing damage, and safeguarding personnel and assets.
Key Characteristics:
- Imminent threats to safety, environment, or operations.
- Demand for immediate intervention to prevent escalation.
- Unpredictable events requiring specialized expertise.
Mitigation Strategies:
- Emergency response plans and protocols.
- Continuous training for personnel on handling critical situations.
The Cost of Reactive Maintenance
Maintenance strategies are intrinsically tied to financial considerations, and understanding the costs associated with reactive maintenance is important for organizations seeking to strike a balance between operational efficiency and fiscal responsibility.
Immediate Costs of Reactive Maintenance
Direct Repair Expenses
The immediate costs of reactive maintenance primarily revolve around the direct expenses incurred in repairing or replacing faulty equipment. This includes the cost of spare parts, labor, and any external services required for a swift resolution. Since reactive maintenance is triggered by unexpected breakdowns, these costs are often urgent and can escalate if not addressed promptly.
Downtime-Related Costs
Perhaps the most significant immediate cost is the impact of downtime on operations. When equipment fails unexpectedly, there is a direct correlation with lost production time, reduced output, and potential disruptions in supply chains. Downtime-related costs encompass not only the direct financial impact but also potential reputational damage and strained customer relationships.
Emergency Response Expenses
Responding to unexpected failures often requires an emergency response, leading to additional expenses. This may involve overtime payments for maintenance personnel, expedited shipping costs for critical spare parts, or any other expenditures necessary to expedite the resolution process. These costs contribute to the overall financial impact of reactive maintenance.
Long-Term Financial Implications
Cumulative Repair Costs
Over time, the cumulative costs of repeatedly repairing equipment in a reactive manner can surpass the expenses associated with preventive maintenance. Chronic issues that are not addressed comprehensively may lead to a cycle of breakdowns, resulting in a higher overall expenditure on repairs.
Equipment Lifecycle
Reactive maintenance can potentially shorten the lifespan of equipment. The lack of regular, proactive care may contribute to accelerated wear and tear, leading to more frequent replacements. This long-term financial implication involves the capital investment required for acquiring new equipment.
Operational Efficiency and Productivity
Prolonged downtime and operational disruptions impact overall efficiency and productivity. While the immediate costs are evident, the long-term financial implications extend to reduced revenue generation, missed business opportunities, and increased operational inefficiencies.
Risk of Catastrophic Failures
Failing to address underlying issues in a proactive manner increases the risk of catastrophic failures. These failures can result in significant financial losses, potential safety hazards, and damage to assets beyond repair.
Though reactive maintenance provides a quick and often cost-effective solution in the short term, organizations must carefully assess the long-term financial implications. Striking a balance between reactive and preventive maintenance can be pivotal in optimizing costs while ensuring operational resilience.
Learn more about the financial implications of preventive maintenance vs. reactive maintenance.
Advantages of Reactive Maintenance
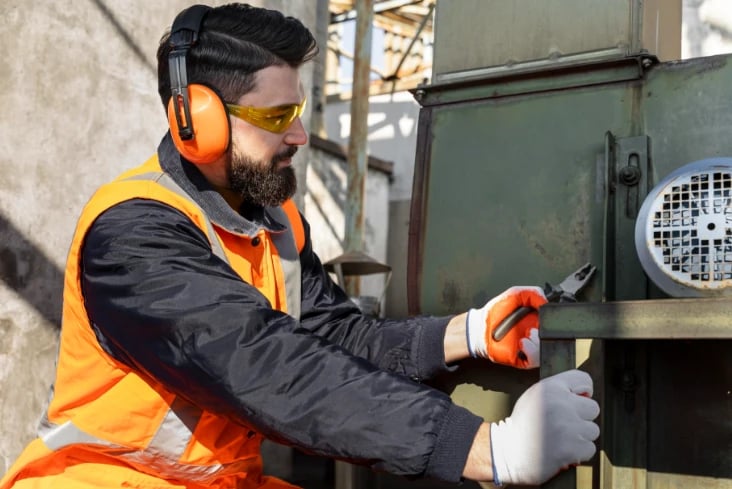
Flexibility in Response
Addressing Issues as They Arise
One of the primary advantages of reactive maintenance is its inherent flexibility in responding to issues as they arise. This strategy allows organizations to tackle problems immediately when they become apparent, preventing potential escalation. The ability to address issues in real-time aligns well with the unpredictable nature of certain equipment failures or malfunctions.
Handling Urgent Situations Promptly
Reactive maintenance excels in situations that demand urgent attention. In cases where immediate intervention is critical to prevent further damage or safety hazards, the flexibility of reactive maintenance ensures a prompt and focused response. This can be particularly beneficial in industries where downtime poses severe consequences.
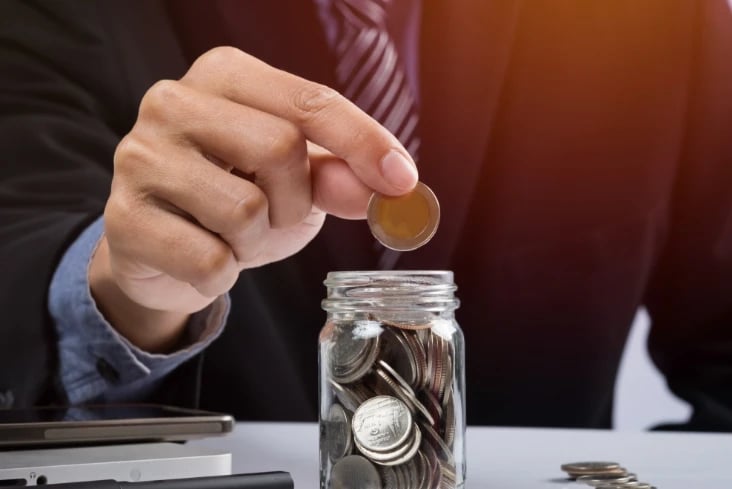
Initial Cost Savings
Lower Upfront Expenses Compared to Preventive Maintenance
Reactive maintenance is often associated with lower upfront expenses compared to preventive maintenance. Since there are no scheduled inspections or routine tasks, organizations can save on the initial costs associated with planning and executing preventive measures. This cost-effectiveness is particularly appealing for businesses operating in environments where equipment failures are sporadic.
Alleviating Budget Constraints in the Short Term
The lower immediate costs of reactive maintenance can be advantageous in situations where budget constraints are a significant consideration. Organizations facing financial limitations may find that reactive maintenance allows them to allocate resources based on immediate needs, providing a short-term solution without placing a heavy burden on budgets.
While these advantages highlight the merits of reactive maintenance in specific contexts, it's essential for organizations to balance these benefits with the potential drawbacks. The responsive nature of reactive maintenance may be suitable for certain equipment or situations, but a comprehensive maintenance strategy often involves integrating preventive measures to ensure long-term operational resilience.
Disadvantages of Reactive Maintenance
Increased Downtime
Impact on Productivity and Operations
One of the most significant disadvantages of reactive maintenance is the potential for increased downtime. When equipment failures are addressed reactively, the time required for diagnosis, repair, and system restoration can lead to operational disruptions. This downtime directly impacts productivity, affecting production schedules, delivery timelines, and overall operational efficiency.
Consequences for Overall Efficiency
Prolonged downtime resulting from reactive maintenance has cascading effects on overall efficiency. Inefficient operations can lead to missed business opportunities, strained customer relationships, and diminished competitiveness in the market. The consequences extend beyond immediate financial losses to broader implications for the organization's standing within its industry.
Higher Repair Costs
Escalation of Repair Expenses Over Time
While reactive maintenance may offer immediate cost savings, the long-term repair costs can escalate over time. Addressing issues only when they become critical may lead to more extensive damage, requiring more resources and costly components for repairs. This escalation can result in a higher cumulative expenditure on maintenance compared to preventive strategies.
Analysis of Potential Cost Spirals
Reactive maintenance can initiate a cost spiral, especially when chronic issues are not adequately addressed. The repetitive cycle of breakdowns, repairs, and subsequent failures can create a pattern of escalating costs. This cost spiral not only affects the organization's financial health but also raises concerns about the sustainability of relying solely on reactive maintenance.
Unpredictability
Lack of Control Over Maintenance Schedules
Reactive maintenance lacks a predefined schedule, making it challenging to control maintenance activities. The unpredictable nature of equipment failures means that organizations cannot plan maintenance activities in advance. This unpredictability can lead to disruptions in operations, making it difficult to allocate resources effectively.
Challenges in Planning and Resource Allocation
The absence of a structured maintenance schedule poses challenges in planning and resource allocation. Organizations may struggle to efficiently deploy personnel, tools, and spare parts, leading to delays in addressing issues. This lack of control can hinder overall maintenance efficiency and effectiveness.
Best Practices for Implementing Reactive Maintenance
The following best practices outline key elements for organizations to consider when implementing reactive maintenance protocols:
1. Developing a Streamlined Response System
Establishing a rapid response system is paramount for effective reactive maintenance. This involves creating standardized protocols and procedures that clearly define the steps to be taken when an issue is identified. The system should outline how to report problems, initiate work orders, and deploy personnel swiftly. By streamlining these processes, organizations can ensure a coordinated and efficient response to unexpected events.
2. Training Personnel for Quick and Effective Interventions
Personnel training plays an important role in the success of reactive maintenance. Ensuring that maintenance teams are well-versed in rapid response protocols, equipment troubleshooting, and effective problem-solving is essential. Training programs should emphasize the importance of quick interventions, safe practices, and the use of technology to streamline the resolution process. Well-trained personnel can significantly contribute to minimizing downtime and optimizing the effectiveness of reactive maintenance efforts.
Using a CMMS to Streamline Reactive Maintenance Workflows
Leveraging a CMMS for reactive maintenance workflows brings numerous advantages, from efficient work order management to data-driven decision-making. As organizations continue to embrace digital transformation in their maintenance practices, the integration of CMMS becomes a strategic imperative for optimizing reactive maintenance processes.
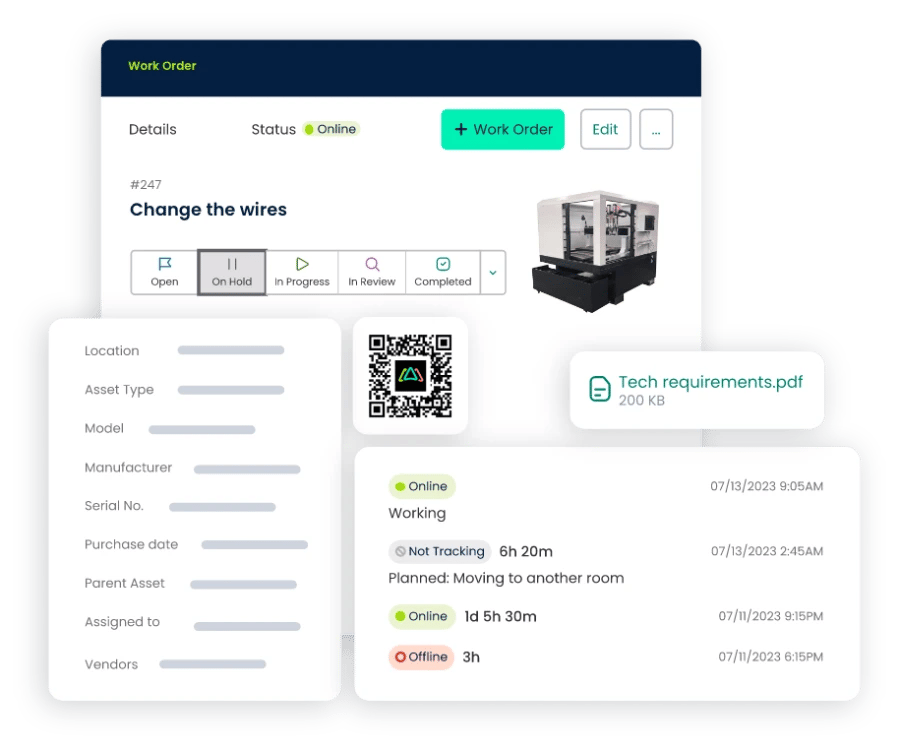
Efficient Work Order Management
CMMS platforms enable organizations to create, track, and manage work orders seamlessly. In the context of reactive maintenance, this functionality is invaluable. When an issue arises, maintenance personnel can swiftly generate a work order through the CMMS, detailing the problem, required tasks, and any necessary documentation. This expedites the initiation of maintenance activities.
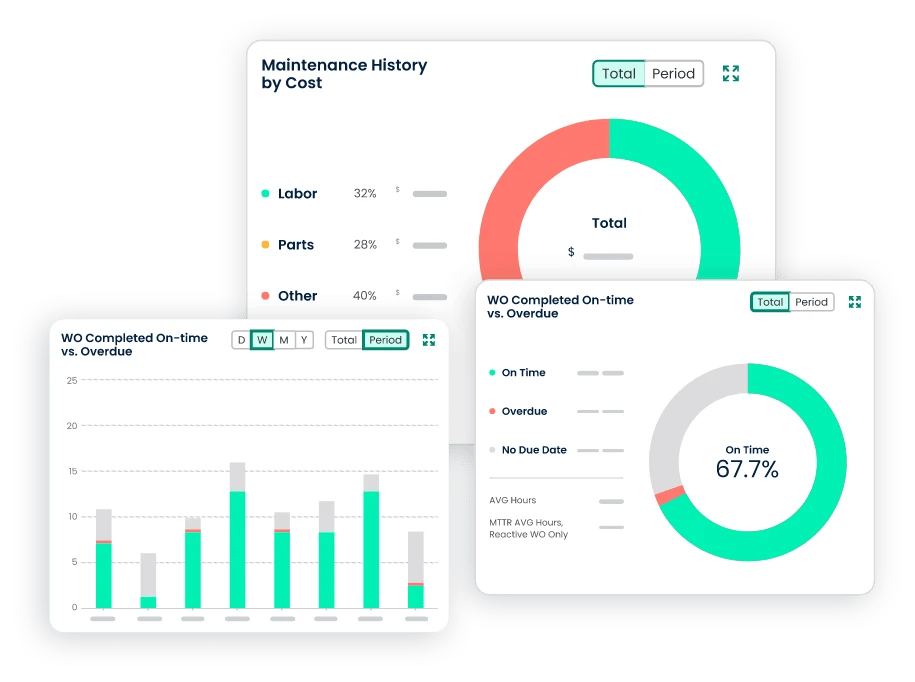
Real-Time Asset Tracking
A CMMS provides real-time visibility into the status and location of assets. For reactive maintenance, this means that teams can quickly identify the specific equipment or machinery in need of attention. The ability to track assets in real-time enhances the efficiency of response times, allowing maintenance personnel to pinpoint the exact location of the issue and take immediate action.
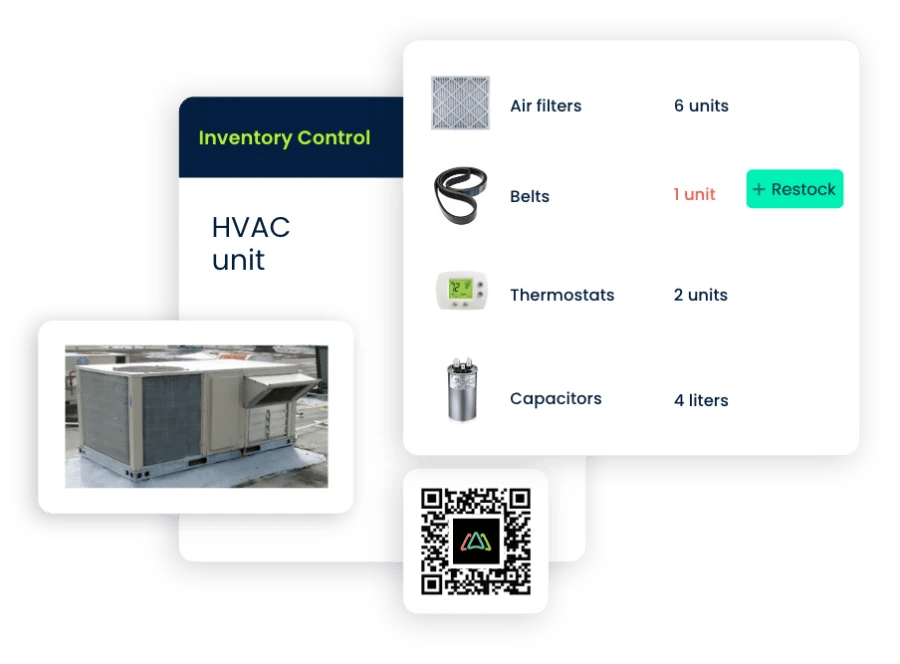
Inventory Management and Parts Tracking
Reactive maintenance often involves the need for spare parts or replacement components. A CMMS with inventory management capabilities ensures that organizations maintain optimal stock levels and can quickly identify and procure necessary parts. This minimizes delays in the repair process and enhances the overall efficiency of reactive maintenance workflows.
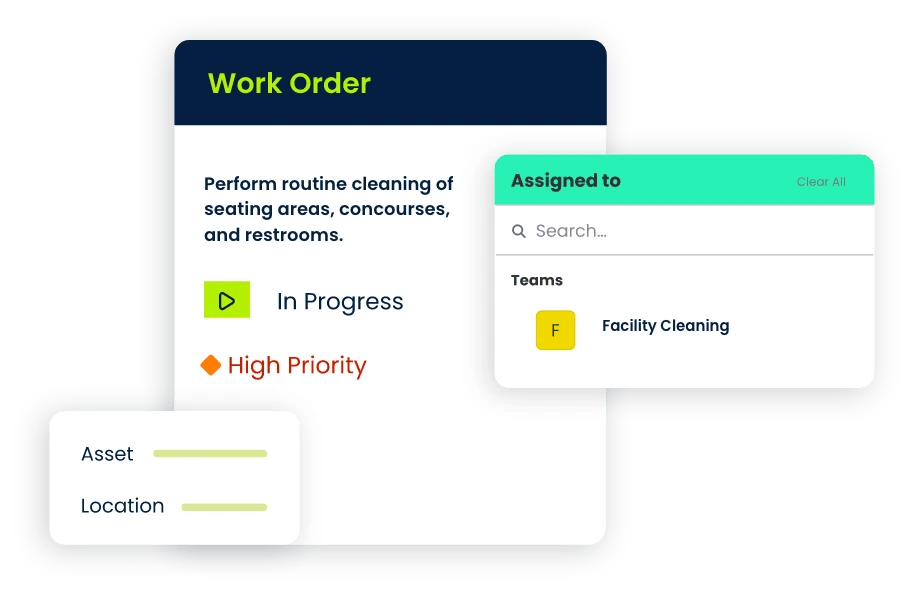
Prioritization and Resource Allocation
CMMS platforms enable organizations to prioritize maintenance tasks based on factors such as criticality and urgency. In the context of reactive maintenance, this functionality is invaluable for ensuring that the most pressing issues receive immediate attention. Furthermore, CMMS tools facilitate effective resource allocation, ensuring that the right personnel and equipment are deployed promptly.
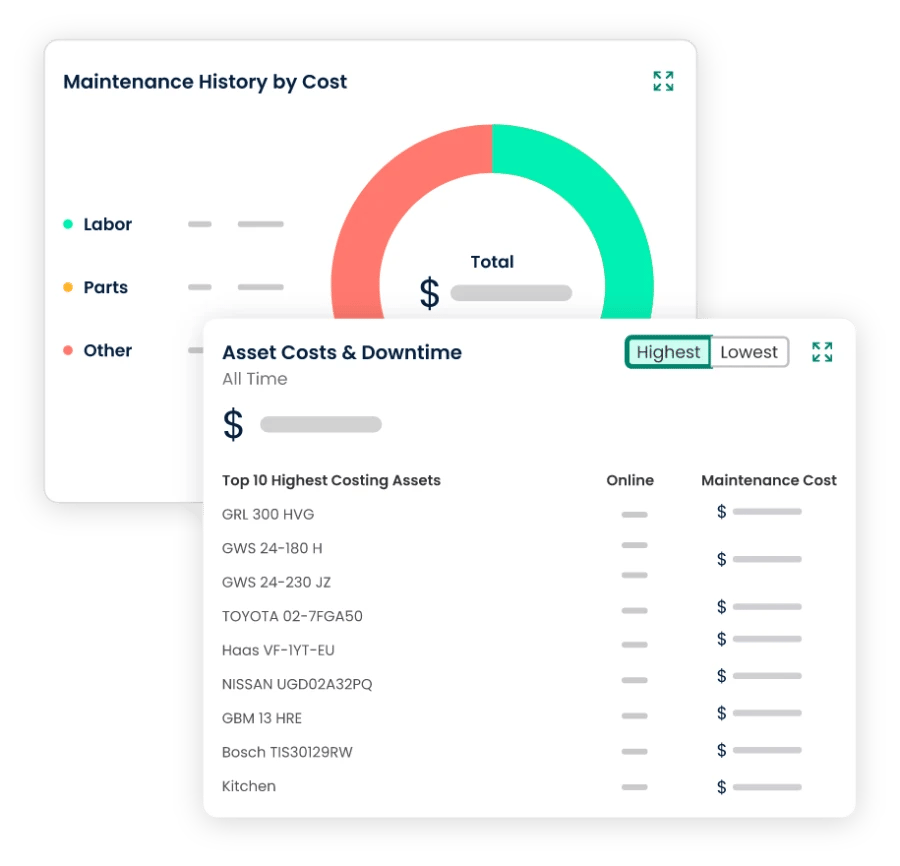
Historical Data Analysis
A key advantage of using a CMMS for reactive maintenance is the ability to analyze historical maintenance data. By reviewing past incidents and resolutions, organizations can identify patterns, root causes, and potential areas for improvement. This data-driven approach enhances decision-making and allows for the continuous refinement of reactive maintenance strategies.
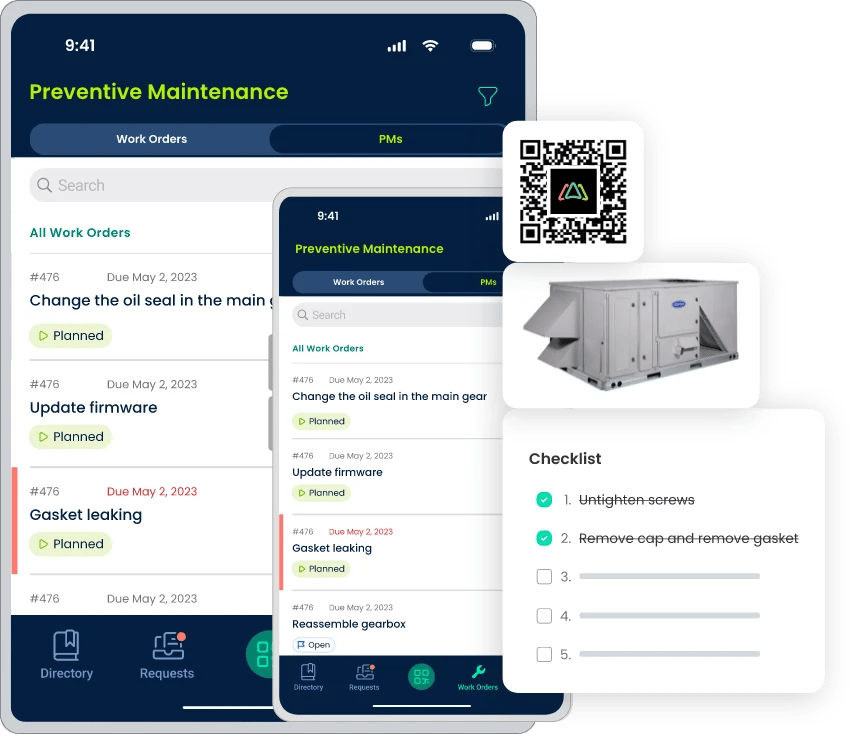
Mobile Accessibility for On-the-Go Management
CMMS platforms often offer mobile applications, empowering maintenance teams to manage workflows on the go. This is particularly beneficial for reactive maintenance scenarios where immediate response is important. Maintenance personnel can receive and update work orders, access asset information, and communicate in real-time, irrespective of their physical location.
Alternative Maintenance Strategies to Consider
In addition to reactive maintenance, organizations have the option to explore alternative strategies that focus on preventing issues before they occur or predicting potential failures.
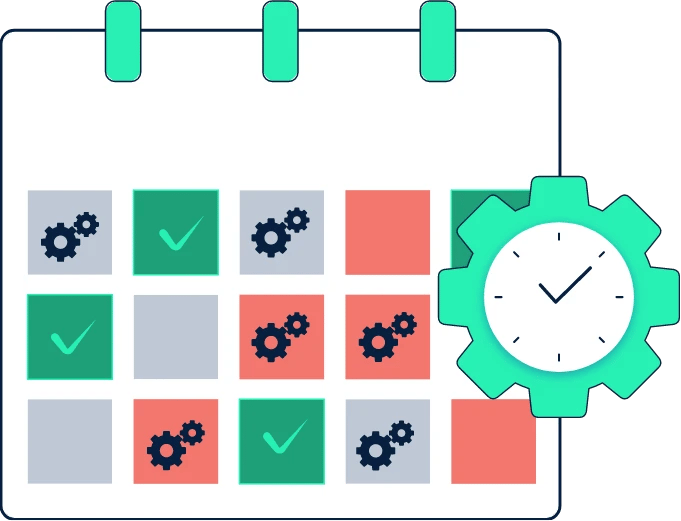
Preventive Maintenance
Proactive Measures to Avoid Breakdowns
Preventive maintenance is a proactive strategy that revolves around scheduled inspections and routine tasks aimed at avoiding unexpected breakdowns. Instead of waiting for equipment to fail, organizations systematically perform maintenance activities to identify and address potential issues before they escalate. This approach is particularly effective for equipment with known failure patterns or components that wear out predictably over time.
Scheduled Inspections and Routine Tasks
The cornerstone of preventive maintenance is the implementation of scheduled inspections and routine tasks. These may include regular equipment checks, lubrication, cleaning, and component replacements at specified intervals. By adhering to a predetermined maintenance schedule, organizations can extend the lifespan of equipment, improve reliability, and minimize the likelihood of sudden breakdowns.
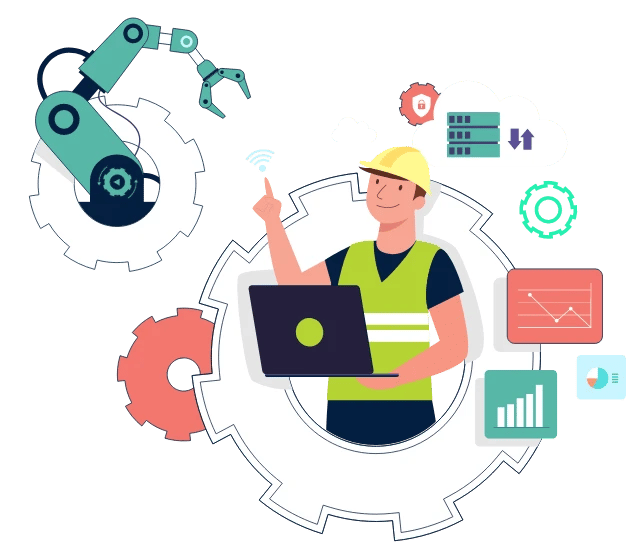
Predictive Maintenance
Utilizing Data and Analytics for Predictive Insights
Predictive maintenance leverages data and analytics to anticipate when equipment failures are likely to occur. By monitoring the performance and condition of assets in real time, organizations can collect data on factors such as vibration, temperature, and usage patterns. Advanced analytics and machine learning algorithms then analyze this data to identify patterns indicative of potential issues.
Anticipating Issues Before They Occur
The primary goal of predictive maintenance is to anticipate issues before they lead to equipment failure. By detecting subtle changes in asset conditions, organizations can schedule maintenance activities precisely when needed, optimizing resource allocation and minimizing downtime. This approach is particularly advantageous for critical assets where unplanned downtime can have significant repercussions.
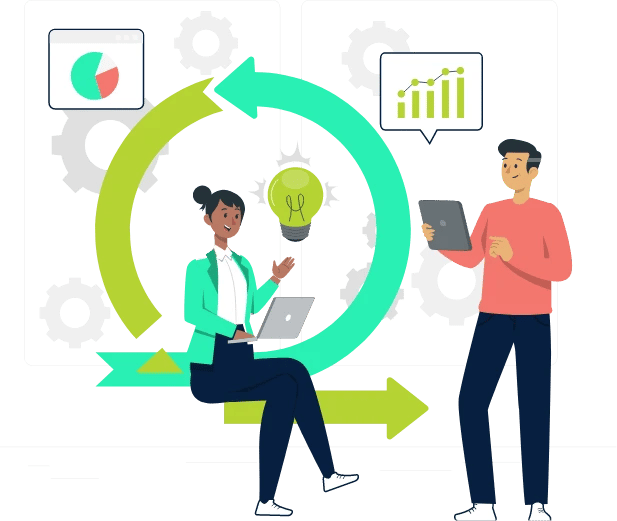
Choosing the Right Strategy
Selecting the best maintenance strategy depends on factors such as the nature of the equipment, operational requirements, and the organization's goals. While reactive maintenance is effective in addressing immediate issues, preventive and predictive maintenance offer a more proactive approach that can lead to long-term cost savings and improved operational efficiency.
Integrating a combination of these strategies, known as a hybrid or condition-based maintenance approach, allows organizations to strike the right balance. The goal is to optimize maintenance efforts by leveraging the strengths of each strategy based on the specific characteristics and criticality of the assets in question.
When is Reactive Maintenance Optimal?
Reactive maintenance is most appropriate in scenarios where the immediate response to unexpected issues is important. Identifying situations conducive to reactive maintenance involves recognizing the nature of the equipment, the likelihood of sudden failures, and the criticality of the assets to the overall operation. Equipment with low maintenance requirements, where failures are infrequent and predictable, is well-suited for a reactive approach.
Considering Factors Like Equipment Criticality and Operational Impact
The criticality of equipment and the potential impact of failures on overall operations play a pivotal role in determining the appropriateness of reactive maintenance. Critical assets that, if they fail, could lead to substantial downtime, safety hazards, or significant operational disruptions may warrant a more proactive maintenance strategy. On the other hand, less critical equipment with minimal impact on operations may be suitable for reactive maintenance, especially if the costs of preventive measures outweigh the benefits.
When Reactive Maintenance Makes Sense:
- Low Criticality, High Predictability: In situations where equipment failures are infrequent, easily identifiable, and have minimal impact on operations, reactive maintenance can be a cost-effective and practical approach.
- Limited Resources: Organizations with constraints on budget and personnel may find reactive maintenance more feasible, particularly when preventive measures are resource-intensive.
- Equipment with Low Maintenance Requirements: Assets that naturally have low maintenance requirements and exhibit predictable failure patterns may be well-suited for a reactive maintenance strategy.
Considerations for Integration
While reactive maintenance has its place, it is essential to integrate it strategically within an overall maintenance plan. Combining reactive maintenance with preventive and predictive strategies ensures a well-rounded approach that addresses immediate issues while proactively managing long-term asset health. Organizations should continuously evaluate the performance of their maintenance strategies and adjust the balance based on evolving operational needs.
Integration with Overall Maintenance Strategy
To achieve a holistic and effective maintenance strategy, organizations often find success in integrating both reactive and preventive approaches. Striking the right balance between these two methodologies is important for optimal results. This section explores the synergies of combining reactive and preventive maintenance and emphasizes the importance of creating a comprehensive maintenance plan.
Finding the Right Balance for Optimal Results
Critical assets or those prone to unpredictable failures may benefit from a proactive preventive approach, complemented by reactive strategies for swift response when issues arise. Less critical equipment with predictable failure patterns may be better suited for a more reactive-centric approach.
Creating a Comprehensive Maintenance Plan
A comprehensive maintenance plan encompasses both reactive and preventive elements, ensuring a well-rounded approach to asset management. Key components of such a plan include:
- Risk Assessment: Identifying critical assets and assessing the potential impact of failures on operations helps prioritize where preventive measures are most important.
- Scheduled Maintenance: Establishing routine inspections, lubrication, and other preventive tasks to address potential issues before they lead to failures.
- Rapid Response Protocols: Developing streamlined response systems for reactive maintenance, focusing on quick interventions and minimizing downtime.
Benefits of Integration
- Operational Resilience: Combining reactive and preventive strategies enhances overall operational resilience. Preventive measures mitigate the risk of unexpected failures, while reactive approaches provide swift responses when issues occur.
- Cost Optimization: Integrating both strategies allows organizations to optimize costs. Proactive preventive measures can reduce the frequency of reactive interventions, minimizing long-term repair expenses.
- Asset Longevity: Preventive maintenance contributes to extending the lifespan of assets by addressing potential issues before they escalate. Reactive maintenance complements this by swiftly resolving unforeseen challenges to avoid further damage.
Continuous Improvement
A successful integration of reactive and preventive maintenance is an ongoing process that requires continuous evaluation and improvement. Organizations should regularly review the performance of their maintenance plan, adjust the balance based on evolving needs, and leverage data-driven insights for optimization.