The 7 RCM Questions
One of the cornerstones of Reliability Centered Maintenance (RCM) is seven questions that form the basis of the methodology. These questions guide the systematic analysis of assets and the determination of the most appropriate maintenance strategy:
1. What are the functions of the asset?
The first question seeks to understand the intended purpose of the equipment. What is it supposed to do, and what functions does it serve?
2. In what ways can the asset fail to fulfill its functions?
This question encourages the identification of all possible failure modes or ways in which the equipment can deviate from its intended functions.
3. What are the consequences of each failure?
RCM requires a thorough examination of the consequences of each identified failure mode. This includes considering safety, environmental, operational, and financial implications.
4. How can the failure be predicted or detected before it happens?
RCM promotes using predictive or detection tools and techniques to identify impending failures. This proactive approach is a departure from reactive maintenance strategies.
5. What are the consequences of not performing any maintenance?
This question explores the impact of doing nothing and not performing any maintenance. It helps in understanding the potential risks and costs of inaction.
6. What maintenance tasks can be performed to prevent or mitigate each failure?
RCM seeks to determine the most effective maintenance tasks that can prevent or mitigate each identified failure mode. This includes preventive, predictive, or other strategies.
7. What are the consequences of failure despite maintenance?
Even with maintenance actions in place, failures can still occur. This question assesses the consequences of a failure despite all preventive efforts, helping develop contingency plans.
In RCM, assessing the consequences of failure and the criticality of equipment are essential steps. Understanding the consequences, including safety, environmental, and operational impacts, helps in making informed decisions about maintenance. FMECA helps prioritize equipment based on its importance to the overall operation, ensuring that resources are allocated to the most essential assets.
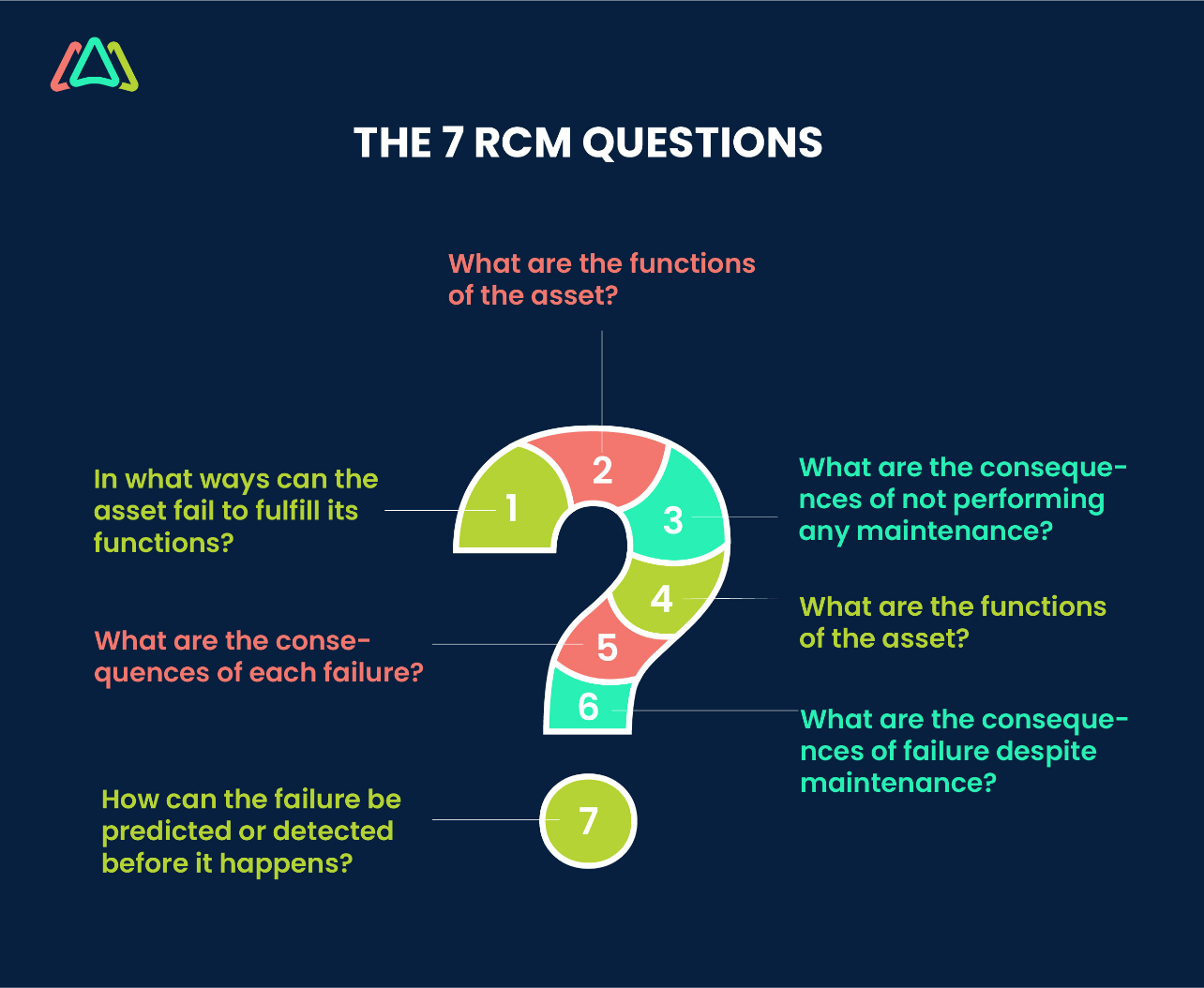