Maintenance Knowledge at Your Fingertips
Print or Download for Offline Access!
Work Orders
Knowing What Needs to be Done and When
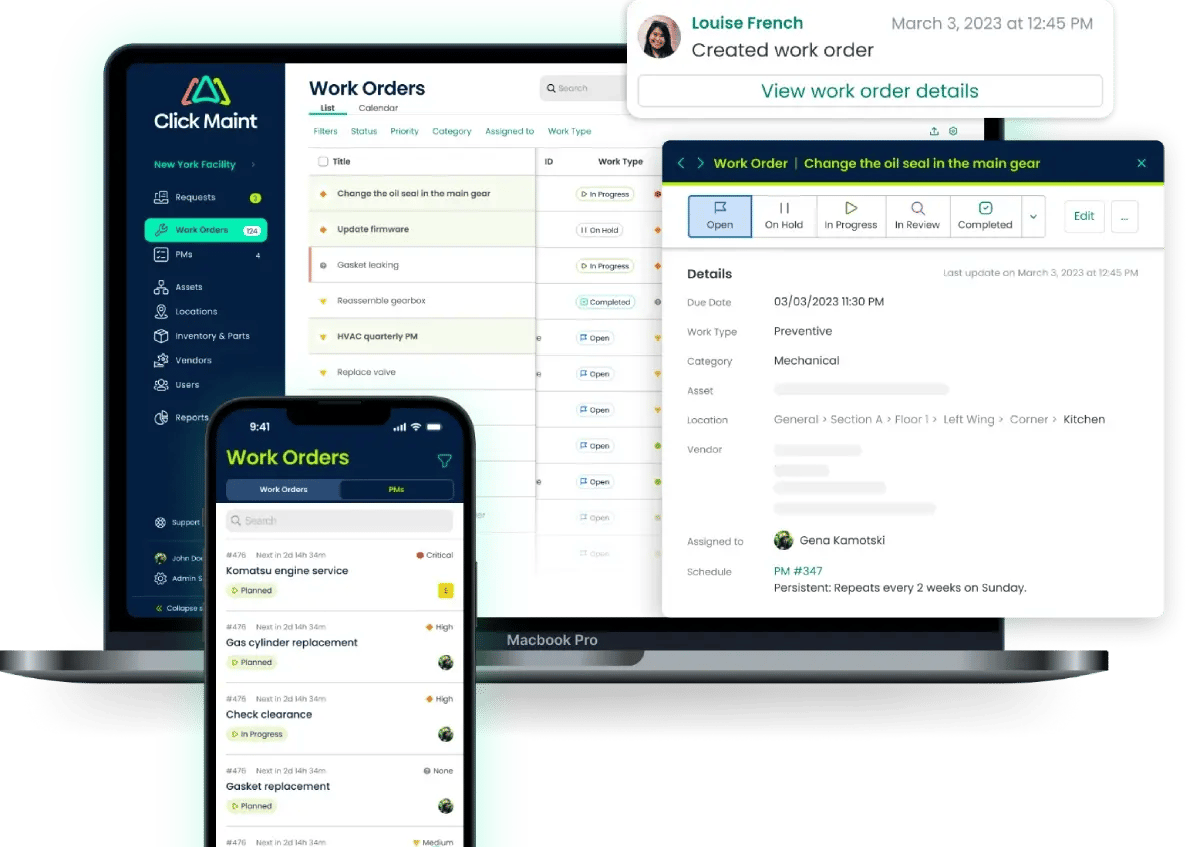
TABLE OF CONTENTS
- What is a Work Order?
- Importance of Work Orders
- 1. Maintenance and Facilities Management
- 2. Compliance and Documentation
- Objectives of a Work Order
- 1. Clarity and Communication
- 2. Resource Management
- 3. Time Management
- 4. Accountability and Performance Tracking
- 5. Cost Control
- Types of Work Orders
- 1. Maintenance Work Orders
- 2. Service Work Orders
- Components of a Work Order
- 1. Work Order Number and Title
- 2. Requester Information
- 3. Description of Work to be Completed
- 4. Assigned Personnel and Responsibilities
- 5. Resources and Materials Required
- 6. Timeline and Due Dates
- 7. Cost Estimation and Budget Allocation
- 8. Priority and Approval Process
- Work Order Lifecycle
- PHASE: 1 Work Order Initiation
- PHASE: 2 Work Order Planning and Scheduling
- PHASE: 3 Work Order Execution
- PHASE: 4 Work Order Completion and Closure
- Using a CMMS to Manage Work Orders
- 1. Standardizing Work Order Processes
- 2. Establishing Clear Communication Channels
- 3. Implementing Preventive Maintenance Strategies
- 4. Tracking and Analyzing Work Order Data
- 5. Continuous Improvement and Feedback
- 10 Tips for Smart Work Order Prioritization and Organization
- 1. Collect and Evaluate Work Order Information
- 2. Categorize Work Orders
- 3. Implement a Priority System
- 4. Consider Resources and Skill Requirements
- 5. Utilize a CMMS for Work Order Management
- 6. Plan and Schedule Maintenance Activities
- 7. Group Similar Tasks for Efficiency
- 8. Consider Geographical Proximity
- 9. Communicate and Collaborate
- 10. Monitor Progress and Adjust Priorities
- How is a Work Request Different from a Work Order?
What is a Work Order?
A work order is a document or request that serves as the foundation for managing and executing specific tasks, projects, or maintenance activities within an organization. It outlines details such as the nature of the work, required resources and materials, due dates and timelines, responsible personnel, and associated costs. Work orders act as a communication tool between different departments, teams and external contractors or vendors.
Work orders can take various forms, from paper-based documents to digital entries in a work order management software. Regardless of the format, they share the common goal of facilitating the smooth and systematic completion of work across diverse industries.
IMPORTANCE OF WORK ORDERS
Work orders play an important role in improving operational efficiency and productivity in maintenance management. Their importance can be observed in the following ways:
1. Maintenance and Facilities Management
In industries like manufacturing, healthcare, hospitality, education and property management, work orders are instrumental in scheduling and coordinating maintenance tasks. These may include equipment repairs, facility upkeep, or infrastructure improvements. Work orders ensure that assets are well-maintained, minimizing equipment downtime and prolonging their lifespan.
2. Compliance and Documentation
Work orders serve as records, documenting the work performed, any changes made, and compliance with safety regulations and industry standards. They are invaluable during audits and help organizations maintain a transparent and work environment with accountability.
See how affordable Click Maint CMMS is
OBJECTIVES OF A WORK ORDER
1. Clarity and Communication
The primary objective of a work order is to provide clear and concise instructions regarding the work to be performed. It ensures that everyone involved understands their roles and responsibilities, reducing the chances of any misunderstanding or miscommunication resulting in errors when work is performed.
2. Resource Management
Work orders help optimize resource allocation by specifying the materials, parts, tools, and personnel required for a particular task or project. This ensures that resources are available and utilized efficiently, reducing waste and unnecessary expenses.
3. Time Management
By defining timelines and due dates, work orders facilitate effective time management. They enable prioritization of tasks, prevent delays, and ensure that projects are completed on schedule.
4. Accountability and Performance Tracking
Work orders establish accountability for the successful completion of assigned tasks. They are instruments that enable managers to evaluate individual and team performance, aiding in continuous improvement and employee development.
5. Cost Control
Work orders include cost estimates and budgets, allowing organizations to monitor expenses associated with specific tasks or projects. Costs can be charged against accounts or GL codes. This helps in maintaining financial discipline and avoiding cost overruns.
Experience Click Maint CMMS now
30-Day Free Trial
No Credit Card needed.
Instant access to all features & modules with an optional live walk-through with a Click Maint expert
Book a live Demo
In this 30-minute demo, see firsthand how our easy CMMS can streamline your operations, enhance productivity, and reduce downtime.
TYPES OF WORK ORDERS
1. Maintenance Work Orders
Maintenance work orders are formal documents that pertain to the upkeep, repair, or inspection of assets within an organization. They serve as important tools for facility and equipment management, ensuring that necessary maintenance tasks are executed in a structured and timely manner. Maintenance work orders detail the scope of work, required resources, and any safety considerations, documenting and streamlining the maintenance process.
The primary purpose of maintenance work orders is to preserve the functionality, reliability, and longevity of assets, preventing breakdowns, defects, or safety hazards. Whether it's a piece of machinery on a production line or the physical infrastructure of a building, maintenance work orders play a vital role in ensuring that assets remain in optimal working condition.
Common Maintenance Work Order Examples
1. Equipment Maintenance Work Orders
These work orders involve the regular inspection, repair, and servicing of machinery and equipment used in manufacturing, production, or industrial processes. Examples include CNC machines, pumps, conveyors, and HVAC systems. Properly maintained equipment leads to increased productivity, reduced downtime, and improved product quality.
2. Facilities Maintenance Work Orders
Facilities maintenance work orders focus on the upkeep of buildings, offices, and other physical structures. This category includes tasks such as plumbing repairs, electrical maintenance, painting, and general building maintenance. Proper facilities maintenance ensures a safe and comfortable environment for employees and visitors.
2. Service Work Orders
Service work orders are used in service-oriented industries to manage and deliver a wide range of services to clients or customers. Whether it's technical support, repairs, installations, or on-site assistance, service work orders help provide prompt and high-quality services while maintaining a structured workflow.
The purpose of service work orders is to streamline service delivery, ensuring that the necessary tasks are completed efficiently and quickly with customer satisfaction as the primary objective. These work orders contain important information, such as the client's request, service details, assigned personnel, required resources, and timelines. Service work orders act as a roadmap for service providers, guiding them through the entire service process to achieve client satisfaction and operational excellence.
Different Types of Service Work Orders
1. Repair Service Work Orders
These work orders address clients' requests for fixing or restoring a malfunctioning product, equipment, or system. Repair service work orders detail the issue, required replacement parts, and the expertise needed to rectify the problem efficiently.
2. Installation Service Work Orders
For new equipment or systems, installation service work orders provide a step-by-step guide for setting up and integrating the equipment or product into the client's environment. They include details on assembly, configuration, and testing to ensure successful installation.
3. On-site Support Service Work Orders
On-site support work orders are issued when clients require assistance at their location. It may involve technical troubleshooting, training sessions, or hands-on help from service technicians.
4. Preventive Maintenance Service Work Orders
Similar to maintenance work orders, preventive maintenance service work orders focus on scheduled inspections and proactive maintenance to prevent future issues and extend the life of the equipment or system.
Best Practices for Handling Service Work Orders
- Prompt Response: Respond to service requests promptly to show clients that their concerns are being addressed and prevent any issues from escalating.
- Clear Communication: Maintain clear and consistent communication with clients throughout the service process, providing updates on progress and any changes in the timeline or scope.
- Streamlined Workflow: Implement a streamlined workflow for service work orders, from creation to execution to ensure efficiency and minimize delays.
- Real-time Tracking: Utilize digital systems to track service work orders in real-time, allowing supervisors to monitor progress, assign tasks, and address any bottlenecks promptly.
- Service Technician Training: Ensure that service technicians are well-trained and equipped with the necessary skills and knowledge to deliver high-quality service.
- Customer Feedback and Follow-up: Gather customer feedback after the service is completed and follow-up to ensure client satisfaction and address any further needs or concerns. A great way to collect feedback is through customer surveys.
- Knowledge Base and Documentation: Maintain a comprehensive knowledge base and documentation for common service issues, resolutions, and best practices, aiding in faster issue resolution and consistency.
Components of a Work Order
Maintenance operations and management rely heavily on well-structured and comprehensive work orders to ensure the efficient and effective completion of maintenance tasks. A comprehensive work order includes valuable information that guides maintenance teams, helps allocate resources and tracks progress throughout the maintenance process.
1. Work Order Number and Title
The work order number is a unique identifier assigned to each maintenance request, enabling easy tracking and reference. It helps maintenance managers and technicians quickly locate and prioritize work orders. The title should be concise and descriptive, summarizing the nature of the maintenance task or service required.
Example:
Work Order Number: #0001
Title: HVAC System Inspection and Repair
2. Requester Information
This section includes details about the person or department that initiated the maintenance request. It’s important to have the requester details including name, email address, phone number and location so that service technicians can contact the requester if and when needed.
Example:
Requester Name: David Green
Requester Department: Facilities Management
3. Description of Work to be Completed
The description of work order outlines the scope of the maintenance task or repair. It should be detailed and specific, describing the issue and required maintenance clearly. Including additional details like photos, drawings, or schematics can aid the maintenance team in understanding the problem.
Example:
Description: The HVAC system in the main office building is emitting strange noises and failing to maintain a consistent temperature. An inspection and repair are required to identify and rectify the issue.
4. Assigned Personnel and Responsibilities
This section lists the names or job titles of the maintenance personnel assigned to the work order. It also defines their specific responsibilities and tasks. Clarity regarding roles ensures accountability and prevents confusion during the maintenance process.
Example:
Assigned Personnel and Responsibilities
- Technician 1: James Dean; Conduct HVAC system inspection and diagnostics.
- Technician 2: Phil Johnson; Perform necessary repairs and component replacements.
5. Resources and Materials Required
In this section, all the resources, tools, parts and other materials needed to complete the maintenance work are listed (also referred to as Bill of Materials (BOM). This includes spare parts, equipment, and any specialized tools required for the task.
Example:
Resources and Materials:
- Replacement fan motor
- HVAC diagnostic equipment
- Hand tools (wrenches, screwdrivers, etc.)
6. Timeline and Due Dates
The timeline sets the expected start and end dates for the maintenance task. Clear due dates help prioritize tasks and ensure that maintenance is completed within a reasonable timeframe. It is important to consider the urgency of the maintenance issue when setting timelines.
Example:
Start Date: 2023-07-25
Due Date: 2023-07-28
7. Cost Estimation and Budget Allocation
This section provides an estimated cost for the maintenance task, including labor, materials, and any additional expenses. Budget allocation ensures that the necessary funds are available to carry out the maintenance work.
Example:
Cost Estimation: $1,500
Budget Allocation: Approved
8. Priority and Approval Process
The priority level indicates the urgency or criticality of the maintenance task. It helps maintenance managers allocate resources based on the importance of the work order. The approval process details the necessary steps for obtaining authorization before starting the work order.
Example:
Priority: High
Approval Process: Work order requires approval from the Facilities Manager before proceeding.
WORK ORDER LIFECYCLE
PHASE 1 : Work Order Initiation
The work order life cycle begins with work order initiation, where maintenance requests are submitted and assessed before being converted into work orders. This phase ensures that maintenance tasks are identified, prioritized, and approved in a systematic manner. It allows managers to assess if the work is actually necessary and identify duplicates before work is assigned. The following are key steps involved in work order initiation:
1.1 Request Submission
The work order process starts with the submission of maintenance requests. These requests can come from various sources, including employees, occupants, or automated monitoring systems that detect equipment issues. Requests can be submitted through different channels, such as maintenance request forms, emails, helpdesk software, or facility management systems.
1.2 Initial Assessment and Prioritization
After receiving maintenance requests, the maintenance team conducts an initial assessment to understand the nature and urgency of each issue. The requests are then prioritized based on factors like safety concerns, impact on operations, and the potential for equipment damage or failure. Urgent or critical issues are given higher priority and addressed promptly.
1.3 Work Order Approval Process
Once the initial assessment and prioritization are completed, maintenance work orders that require approval are routed through an approval process. The approval process involves obtaining authorization from relevant stakeholders, such as facility and maintenance managers or department heads. This step ensures that the maintenance tasks align with organizational goals and budgets before proceeding.
Example:
Upon receiving a maintenance request for a malfunctioning air conditioning unit in an office building, the maintenance team conducts a preliminary assessment of the issue's severity. If the issue poses a significant risk to occupant comfort or can lead to further damage to the HVAC system, the work order is prioritized as "High." The work order then goes through an approval process, where the Facilities Manager reviews and authorizes the work order before the maintenance team begins repairs.
PHASE: 2 Work Order Planning and Scheduling
Once the work order is approved, it moves into the planning and scheduling phase. This phase involves creating a detailed plan to execute the maintenance task efficiently and effectively. Key steps in this phase include:
2.1 Resource Allocation and Availability
The maintenance team identifies the required resources, including people, tools, materials, and equipment needed to complete the maintenance task. They also ensure that these resources are available.
2.2 Work Sequencing and Dependencies
The maintenance team arranges the tasks in the most logical and efficient order to minimize downtime and avoid disruptions to ongoing operations. They also identify any dependencies between tasks to ensure smooth workflow.
2.3 Assign a Realistic Timeline
A realistic timeline is established for each task, considering the complexity of the maintenance work, the availability of resources and any constraints. The timeline is communicated to all involved parties to set clear expectations.
Example:
For the approved HVAC repair work order, the maintenance team allocates two technicians with the necessary HVAC diagnostic equipment and replacement parts. They plan the work to begin on the next available date and estimate that the repairs will be completed within three days.
PHASE: 3 Work Order Execution
The execution phase is where the actual maintenance work takes place. It involves carrying out the tasks as per the planned schedule, closely adhering to safety protocols and quality standards. Key steps in this phase include:
3.1 Communicating Work Details to Assigned Personnel
The maintenance team communicates the work order details, including the scope, tasks, and safety considerations to the assigned personnel. This ensures that everyone is aware of their responsibilities and follows proper procedures.
3.2 Tracking Progress and Updates
Throughout the execution phase, the maintenance team tracks the progress of each task and updates the work order status. Real-time updates are necessary for effective communication and to address any unexpected challenges promptly.
3.3 Handling Change Requests
In cases where unforeseen issues arise or the scope of work needs adjustment, change requests may be required. The maintenance team evaluates change requests and updates the work order accordingly, ensuring that all changes are documented.
Example:
During the execution phase, the HVAC technicians begin the repairs following the planned sequence. As they dismantle the faulty unit, they discover additional damage that requires a part replacement not initially accounted for in the work order. The maintenance team submits a change request to the facilities manager for approval, and upon receiving authorization, they proceed with the necessary repairs.
PHASE: 4 Work Order Completion and Closure
The final phase of the work order life cycle involves the completion and closure of the maintenance task. This stage ensures that all work is satisfactorily executed and documented for future reference, record keeping and reporting. Key steps in this phase include:
4.1 Final Inspection and Quality Control
The maintenance team conducts a final inspection to verify that all maintenance tasks are completed according to the specifications and quality standards. They test the repaired equipment to ensure it functions as intended.
4.2 Obtain Client or Requester’s Approval
In some cases, particularly for external clients or tenants, obtaining approval and sign-off from the requester are necessary to confirm that the maintenance work meets their satisfaction.
4.3 Documentation and Archiving
The maintenance team records all relevant data, including work performed, materials used, costs incurred, and any observations during the maintenance process. This information is archived for future reference, reporting and compliance purposes.
Example:
Upon completing the HVAC repairs, the maintenance team performs a final inspection to confirm that the system is functioning correctly and that the issue is resolved. The requester and the facilities manager approve the work order after reviewing the inspection report. The maintenance team then archives the work order documentation for record-keeping.
USING A CMMS TO MANAGE WORK ORDERS
1. Standardizing Work Order Processes
Standardizing work order processes helps maintain consistency and efficiency in maintenance operations. A Computerized Maintenance Management System (CMMS) is a great tool for work order management by providing a centralized platform for creating, managing, and tracking work orders. Here is how a CMMS improves standardization:
1.1 Work Order Creation
A CMMS offers customizable work order templates, ensuring that each work order contains information such as task details, assigned personnel and due dates, following a standardized format.
1.2 Approval Workflow
With a CMMS, the approval process becomes streamlined and automated. Authorized personnel can easily review and approve work orders directly from the system, eliminating delays caused by manual approvals.
1.3 Task Execution Guidelines
A CMMS allows maintenance teams to attach detailed work instructions, documents, or images to work orders, ensuring that technicians have clear guidelines for executing tasks.
1.4 Reporting and Documentation
The CMMS automatically generates comprehensive reports, documenting work order history, maintenance activities, and performance metrics, facilitating standardized documentation.
2. Establishing Clear Communication Channels
Effective communication is critical for effective work order management. A CMMS improves communication by providing a centralized platform for all stakeholders to interact and share information. Here is how a CMMS helps improve communication:
2.1 Centralized Communication Platform
A CMMS serves as a centralized hub for communication, allowing maintenance teams, supervisors, and requesters to exchange messages, updates, and notifications in real-time. Role-based Notifications: A CMMS can send automated notifications to relevant personnel based on their roles, ensuring that everyone receives timely updates on work order statuses and changes.
2.2 Feedback
CMMS software comes with built-in feedback mechanisms like work order rating systems or comment sections, enabling maintenance technicians and clients to provide input and suggestions.
2.3 Transparent Reporting
Through customizable dashboards and reports, a CMMS provides stakeholders with real-time insights into work order progress, facilitating transparent reporting.
3. Implementing Preventive Maintenance Strategies
Preventive maintenance is made more efficient with the support of a CMMS, as it helps schedule, plan, and manage preventive tasks effortlessly. Here is how a CMMS helps with the implementation of preventive maintenance strategies:
3.1 Scheduling Maintenance
A CMMS enables the creation of preventive maintenance schedules based on equipment specifications and performance data, ensuring that maintenance and upkeep are being performed according to manufacturer guidelines.
3.2 Condition-based Monitoring
Integrating condition monitoring sensors with a CMMS allows for real-time data collection, triggering maintenance work orders when equipment parameters deviate from acceptable ranges.
3.3 Data-driven Decision Making
CMMS analytics and reporting capabilities help maintenance teams analyze historical data to make data-driven decisions and optimize preventive maintenance plans.
3.4 Proactive Asset Management
A CMMS stores comprehensive asset information, including maintenance history, warranties, bill of materials (BOM) and O&M manuals streamlining asset tracking and facilitating asset management.
4. Tracking and Analyzing Work Order Data
A CMMS significantly improves the ability to track, analyze, and learn from work order data, providing valuable insights for continuous improvement. The following are ways a CMMS improves data tracking and analysis:
4.1 Key Performance Indicators (KPIs)
A CMMS automatically calculates and generates KPIs, such as MTTR and MTBF, allowing maintenance teams to monitor performance and identify areas for improvement.
4.2 Historical Data Analysis
CMMS data analytics tools enable in-depth historical data analysis, helping detect recurring issues, patterns and trends for proactive maintenance planning.
4.3 Root Cause Analysis
With work order history readily available in a CMMS, performing root cause analysis becomes possible, aiding in identifying and resolving the underlying reasons for failures.
4.4 Predictive Analytics
CMMS predictive maintenance capabilities use advanced algorithms to forecast maintenance needs, optimizing resource allocation and preventing unplanned downtime.
5. Continuous Improvement and Feedback
A CMMS facilitates a culture of continuous improvement by providing platforms for feedback and knowledge-sharing among maintenance teams. Here are some ways a CMMS enables continuous improvement efforts:
5.1 Regular Team Meetings
CMMS reporting features enable data sharing during team meetings, helping maintenance teams collaborate, analyze performance, and strategize improvements.
5.2 Feedback Surveys
CMMS-integrated survey tools allow organizations to gather feedback from maintenance technicians, clients, and requesters, gathering valuable insights for process refinement.
5.3 Training and Skill Development
Some CMMS software can track training and certification records, ensuring that maintenance teams are adequately trained and up-to-date with relevant skills.
5.4 Continuous Learning
CMMS knowledge bases and forums facilitate knowledge-sharing among maintenance teams, promoting a culture of continuous learning and growth.
10 Tips for Smart Work Order Prioritization and Organization
Prioritizing and organizing work orders is important for efficient maintenance operations and effective resource allocation. By implementing a systematic approach, maintenance teams can ensure that critical tasks are addressed promptly, downtime is minimized, and resources are optimally utilized. Here are key steps to prioritize and organize work orders effectively:
Collect and Evaluate Work Order Information
Gather all incoming work orders, including maintenance requests, inspections, and preventive maintenance tasks. Assess each work order's urgency, importance, and impact on operations. Consider factors such as safety risks, equipment criticality, and client or customer requirements.
Categorize Work Orders
Categorize work orders based on their nature, criticality or type. Common categories may include emergency repairs, preventive maintenance, routine inspections, or general maintenance tasks. Work orders can also be categorized according to the nature of the work; groundskeeping, HVAC, electrical, plumbing, machining, etc. This classification helps in grouping similar tasks for efficient handling and reporting.
Implement a Priority System
Develop a priority system to rank work orders based on their criticality and urgency. Common priority levels include:
- High Priority: Tasks that pose safety risks, impact production, or have significant operational consequences. These tasks require immediate attention and resolution.
- Medium Priority: Important tasks that need to be addressed promptly but may not have an immediate impact on safety or production.
- Low Priority: Tasks that are essential but can be scheduled and executed without urgency.
Consider Resources and Skill Requirements
Assess the availability of resources, including skilled technicians, tools, equipment, and spare parts when prioritizing work orders. High-priority tasks may require specialized expertise or additional resources to complete them.
Utilize a CMMS for Work Order Management
A CMMS provides a centralized platform to manage work orders, allows for easy assigning, sorting and filtering based on priority levels, and facilitates real-time tracking of work order status and future reporting.
Plan and Schedule Maintenance Activities
Create a maintenance schedule based on the priority of work orders, available resources, and equipment downtime windows. Efficient scheduling ensures that critical tasks are addressed promptly, while less urgent tasks are appropriately timed to avoid unnecessary disruptions.
Group Similar Tasks for Efficiency
Organize work orders with similar requirements or locations together. Grouping similar tasks allows maintenance teams to streamline their activities, minimize travel time, and optimize resource allocation.
Consider Geographical Proximity
If maintenance operations involve multiple locations or facilities, consider geographical proximity when planning work orders. Scheduling tasks in nearby locations together can save time and travel expenses.
Communicate and Collaborate
Maintain clear and open communication with maintenance teams, supervisors, and stakeholders. Regularly update all involved parties about the status of work orders, schedule changes and resource availability.
Monitor Progress and Adjust Priorities
Continuously monitor work order progress and adjust priorities as needed. Unexpected emergencies, equipment failures or changes in operational requirements may require changing the priority of tasks.
How is a Work Request Different from a Work Order?
Work orders and work requests serve distinct purposes in maintenance operations. Work orders are formal directives that outline detailed instructions and guidelines for specific maintenance tasks. A work request, on the other hand, is a less formal communication initiated by individuals or departments within an organization to inform the maintenance team of a maintenance need or issue. Work requests serve as a means for employees or occupants to report malfunctions, facility problems, or other maintenance requirements that require attention. Work requests become work orders once they are approved by a facility or maintenance manager.
Key Characteristics of Work Requests:
- Informal and General: Work requests are less structured than work orders providing general information about the issue or maintenance requirement.
- Initiated by Requesters: Work requests are initiated by employees, tenants, or occupants who notice a maintenance-related concern and wish to have it addressed by the maintenance team.
- Evaluation and Prioritization: Upon receiving work requests, the maintenance team evaluates and prioritizes them based on their urgency and impact on operations before approving and converting them into formal work orders.
- Initial Assessment: Maintenance teams may conduct an initial assessment of the reported issue to determine the appropriate course of action and resource allocation.
Work order management is a critical component for maintaining organizations’ facilities and assets. Contact us to learn about how Click Maint CMMS can help your organization streamline its work order management process.
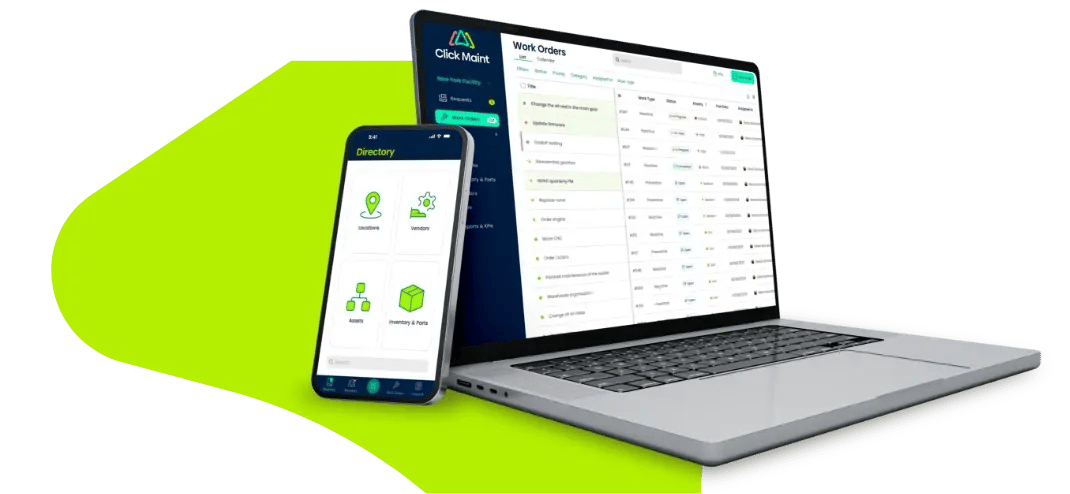