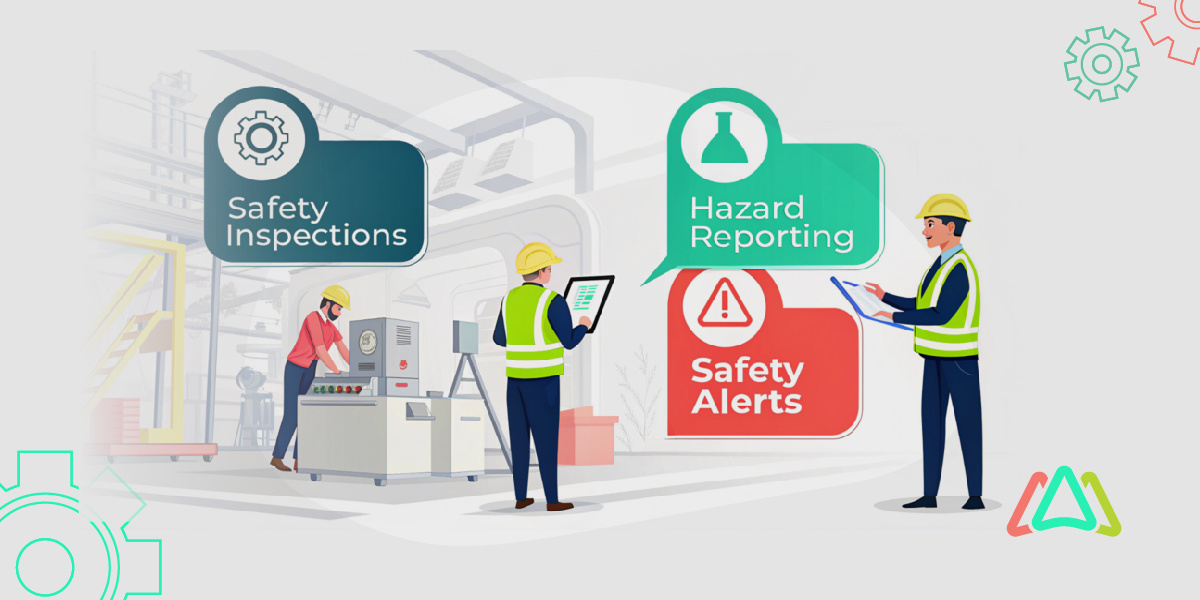
How a CMMS Ensures Workplace Safety and Compliance in Manufacturing
In manufacturing, workplace accidents and non-compliance can have severe consequences. To break this down, the National Safety Council reported a total cost of $167 billion for work injuries across industries in 2022, encompassing wage and productivity losses, medical expenses, and administrative costs. Manufacturing, as one of the higher-risk industries, contributes significantly to these numbers. This highlights the pressing need for manufacturers to prioritize safety and compliance to mitigate risks and avoid costly repercussions.
Also, manufacturers struggle with navigating complex regulations, passing frequent audits, and maintaining a safe work environment. Managing maintenance schedules, safety inspections, and regulatory documentation can be overwhelming, and failure to do so results in costly penalties and safety hazards.
CMMS software is a key tool for ensuring workplace safety and compliance in manufacturing. It offers a powerful solution by automating maintenance tasks, tracking safety inspections, and organizing compliance documents. It simplifies staying on top of regulatory requirements, reducing risks, and improving efficiency. This article will explore how CMMS enhances safety, ensures compliance, and streamlines operations, providing manufacturers with a reliable tool to safeguard their workforce and assets.
What is Workplace Safety?
Workplace safety refers to the practices and measures taken to prevent accidents and injuries while ensuring a safe working environment. This includes ensuring safe equipment operation, proper machine maintenance, ergonomic workplace design, and employee safety training. Proactive safety measures, such as conducting regular safety audits, implementing emergency response plans, and providing personal protective equipment (PPE), are key to minimizing the risk of workplace accidents and maintaining a healthy workforce.
Compliance in Manufacturing
Compliance in manufacturing means adhering to industry-specific regulations and standards set by governing bodies. Key organizations like OSHA (Occupational Safety and Health Administration), ISO (International Organization for Standardization), and EPA (Environmental Protection Agency) establish regulations that guide workplace safety, environmental protection, and operational procedures. Manufacturers must comply with standards related to equipment safety, worker training, environmental impact, and more to ensure both the safety of their employees and the legality of their operations.
The Cost of Non-Compliance
Non-compliance can lead to significant penalties, including substantial fines, legal action, and even shutdowns. Beyond financial costs, reputational damage can tarnish a company’s image, ruining customers’ trust and impacting future business opportunities. Operational disruptions, such as forced downtime or increased insurance premiums due to safety violations, can also hurt a company’s bottom line. These costs emphasize the importance of maintaining rigorous safety and compliance practices in manufacturing.
The Role of CMMS in Ensuring Workplace Safety
Workplace safety is a top priority in manufacturing, where hazardous conditions and complex machinery can pose significant risks. CMMS software plays a vital role in creating a safer work environment. Here are the key roles CMMS plays in ensuring workplace safety:
Preventive Maintenance and Equipment Reliability
Regular equipment checks are critical in preventing malfunctions that could lead to accidents or operational disruptions. In a manufacturing environment, even a small breakdown can result in hazardous situations for workers and costly downtime. CMMS (Computerized Maintenance Management System) helps mitigate this risk by automating preventive maintenance. By tracking equipment usage and performance, CMMS ensures that maintenance tasks are performed on time, reducing the likelihood of unexpected failures.
Safety Inspections and Audits
Safety inspections are a vital part of maintaining a safe workplace, ensuring compliance with regulations, and identifying potential hazards. CMMS simplifies the process of scheduling and tracking these inspections. It allows manufacturers to set recurring inspection reminders and track completion in real time, ensuring no task is overlooked. Additionally, CMMS enables the digital documentation of inspection outcomes, making it easy to store and retrieve records during audits. This centralized documentation helps manufacturers stay organized and prepared for any regulatory scrutiny, improving both safety and compliance efforts.
Hazard Identification and Risk Mitigation
Timely identification and resolution of safety hazards are essential for preventing accidents. CMMS allows manufacturers to log safety hazards as soon as they are identified, whether they are equipment-related, environmental, or procedural. By using the system to assign corrective actions and track their resolution, manufacturers can address risks before they lead to incidents. Furthermore, CMMS sends real-time notifications and alerts to relevant personnel, ensuring that hazards are addressed immediately. This helps create a proactive safety culture where potential risks are managed efficiently, reducing the likelihood of workplace accidents.
How to Ensure Workplace Safety with CMMS
Ensuring workplace safety in manufacturing is a continuous process that requires a combination of proactive measures, regular monitoring, and quick response to potential hazards. A CMMS provides manufacturers with the tools to streamline these safety efforts. Here’s how CMMS helps ensure a safer work environment:
Automating Preventive Maintenance
Regular maintenance of equipment is key to preventing breakdowns that could lead to accidents. A CMMS automates maintenance schedules, ensuring that machines are inspected, lubricated, and repaired before issues arise. This proactive approach minimizes the likelihood of equipment failures, reducing the risk of workplace injuries caused by malfunctioning machinery.
Tracking Safety Inspections
A CMMS enables easy scheduling and tracking of safety inspections, ensuring that all areas of the facility are regularly checked for hazards. The system allows for digital records of inspections, making it simple to monitor compliance and ensure no inspection is overlooked.
Real-Time Hazard Reporting
CMMS platforms allow employees to log safety hazards in real time quickly. These reports are instantly shared with the maintenance or safety team, who can take immediate action to address the risks. This quick response reduces the chances of incidents or accidents occurring due to unaddressed hazards.
Safety Alerts and Notifications
The system can send real-time alerts when critical safety tasks are due or if a potential safety issue is detected. These notifications keep safety protocols on track and ensure timely action is taken to prevent accidents.
The Role of CMMS in Maintaining Compliance
Regulatory compliance is essential in manufacturing, where strict standards and documentation requirements can be challenging to manage. A CMMS plays a vital role in simplifying compliance processes. The following are ways CMMS supports maintaining compliance:
Regulatory Documentation Management
Maintaining accurate and up-to-date regulatory documentation is important for ensuring compliance in manufacturing. CMMS streamlines this process by storing and organizing essential documents such as permits, certifications, inspection reports, and maintenance records. By digitizing these documents within the system, manufacturers can easily retrieve them during audits, reducing the risk of non-compliance due to missing or misplaced paperwork.
Training and Certifications
Tracking worker certifications and training records is vital for compliance with industry regulations. CMMS helps manufacturers monitor and manage employee qualifications by storing training records, certification details, and renewal deadlines. Automated reminders are sent to notify supervisors and employees of upcoming training or certification expirations, ensuring that workers remain compliant with safety and regulatory standards. This reduces the risk of penalties for non-compliance and ensures that employees are always qualified to perform their jobs safely and effective.
Compliance Reporting
CMMS simplifies the creation of detailed compliance reports, saving time and reducing the risk of errors. With minimal effort, manufacturers can generate reports that track compliance with safety regulations, environmental standards, and operational procedures. Customizable dashboards allow managers to monitor key compliance performance indicators (KPIs) in real-time, providing a clear overview of the organization’s compliance status. These insights help identify potential compliance gaps and ensure timely corrective actions, keeping the manufacturing operations in line with regulatory requirements and avoiding costly violations.
How to Maintain Compliance with CMMS
In the highly regulated manufacturing industry, maintaining compliance with various safety standards and regulations is important to avoid penalties, legal issues, and reputational damage. A CMMS simplifies the process of staying compliant and helps ensure that all regulations are met efficiently. Here’s how CMMS supports compliance in manufacturing:
Centralized Regulatory Documentation
Keeping track of essential compliance documents like permits, certifications, and inspection reports can be challenging. A CMMS stores all compliance-related documentation in one centralized location, ensuring that records are easily accessible during audits or inspections. Digitizing these documents reduces the risk of lost or misplaced paperwork and ensures that everything is up-to-date.
Automated Compliance Task Management
A CMMS automates scheduling for compliance-related tasks such as safety audits, inspections, and certification renewals. This ensures that all deadlines are met, preventing missed or late tasks that could lead to non-compliance.
Audit-Ready Reporting
CMMS platforms generate detailed, customizable reports that are ready for audits. These reports can track compliance metrics, including maintenance schedules, inspection histories, and safety performance. With automated report generation, manufacturers can quickly provide proof of compliance, saving time and reducing the stress of audits.
Tracking Employee Certifications and Training
Ensuring that all workers are properly trained and certified is essential for maintaining compliance. CMMS tracks employee certifications, training records, and renewal dates. Automated reminders for upcoming certifications or training refreshers ensure that employees stay compliant with industry standards and regulations.
Real-Time Compliance Monitoring
With CMMS software, manufacturers can monitor compliance in real-time. The system tracks all maintenance activities, inspections, and tasks related to regulatory requirements, helping managers stay on top of compliance in an ongoing manner.
Conclusion
In summary, a CMMS is a powerful tool for improving workplace safety, ensuring regulatory compliance, and enhancing operational efficiency in manufacturing. By automating preventive maintenance, tracking safety inspections, and managing compliance documents, CMMS helps reduce risks, streamline operations, and ensure that manufacturers meet the required standards. Additionally, the ability to generate detailed compliance reports and track training records further supports a company’s efforts to maintain a safe and compliant workplace.
TABLE OF CONTENTS
Keep Reading
Ever find yourself checking into a luxury hotel and expecting a relaxing stay, only to find a ...
11 Apr 2025
Organizations are witnessing swift changes in the business environment and confronting a ...
8 Apr 2025
Last month, news outlets and the entire internet was abuzz with the return of NASA astronauts ...
3 Apr 2025
What comes first - CMMS or predictive maintenance? If your answer is either, it is correct. ...
28 Mar 2025
Artificial intelligence (AI) talk has become commonplace. Today, engaging in business-focused ...
27 Mar 2025
Imagine a world where machines predict, diagnose, and fix their issues before they fail. This ...
25 Mar 2025
A facility maintenance plan is at the core of a facility’s operations. This organized ...
21 Mar 2025
Think of managing your maintenance operations like managing a championship sports team. Just ...
21 Mar 2025
The maintenance sector is battling a severe talent shortage that threatens to undermine ...
7 Mar 2025
Manufacturing maintenance is the backbone of industrial efficiency, ensuring machines run ...
5 Mar 2025
No one likes playing a guessing game when equipment breaks down. Yet, maintenance teams often ...
4 Mar 2025
The size of the preventive maintenance software market is discussed in millions of dollars, ...
4 Mar 2025
The organizational structure and corporate hierarchy vary from company to company. Large ...
28 Feb 2025
Maintenance procedures are essential for ensuring the longevity and reliability of machinery ...
21 Feb 2025
Sustainability is no longer just a buzzword; it's a critical component of corporate social ...
20 Feb 2025
A Computerized Maintenance Management System (CMMS) relies on accurate, well-organized data ...
18 Feb 2025
In an era where technology drives operational efficiency, Computerized Maintenance Management ...
14 Feb 2025
A Computerized Maintenance Management System (CMMS) is a key component of modern maintenance ...
13 Feb 2025
Introduction Maintenance management is the foundation of maintenance operations in industries ...
11 Feb 2025
Introduction A Computerized Maintenance Management System (CMMS) is software designed to help ...
7 Feb 2025