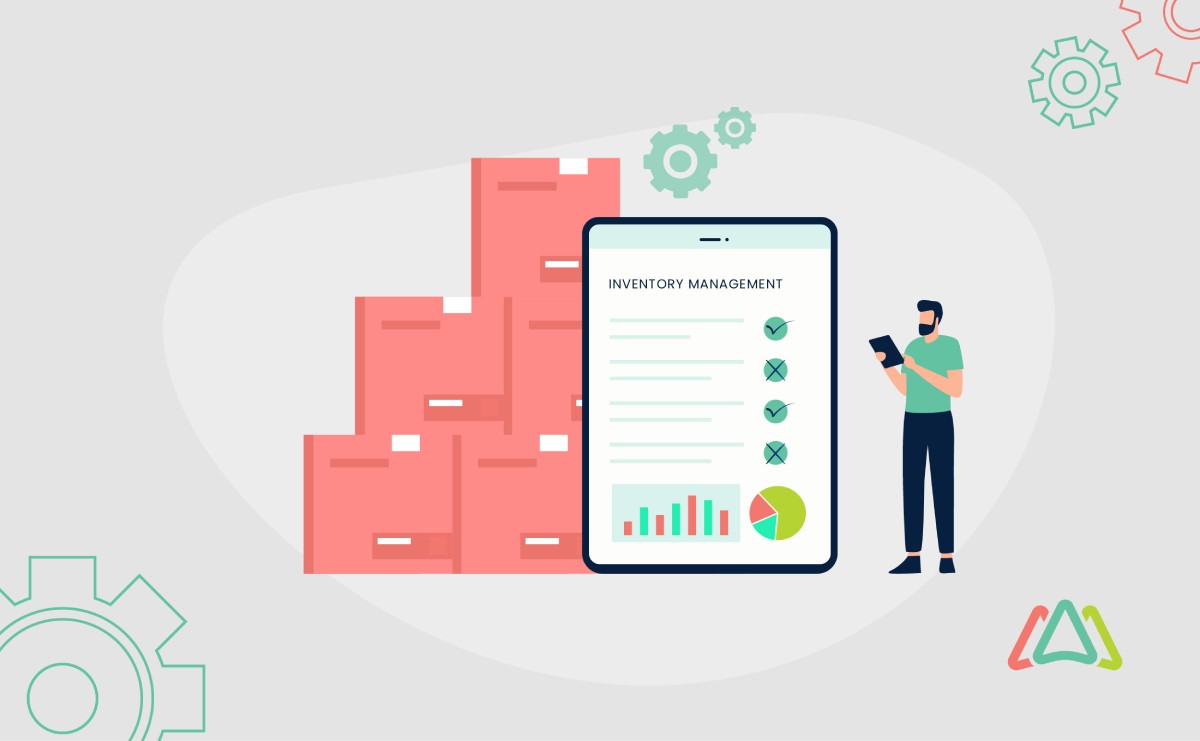
The Role of a CMMS in Improving Inventory Management KPIs
Maintaining optimal inventory levels, minimizing stock outages, and reducing carrying costs are key objectives for businesses across various industries. To achieve these goals, organizations rely on inventory management key performance indicators (KPIs) to assess and monitor their inventory performance. However, manual or outdated inventory management systems can present challenges in accurately tracking and managing inventory, leading to inefficiencies and interrupted maintenance operations.
This is where a CMMS can add significant value. A Computerized Maintenance Management System (CMMS) has features that provide a centralized platform for inventory management. In addition to tracking and scheduling maintenance activities like work orders and preventive maintenance tasks, modern CMMS solutions have evolved to encompass broader functionalities, including inventory management of spare parts and other consumables.
A CMMS acts as a central hub where organizations can consolidate and manage inventory-related data. It serves as a repository for inventory records, such as part descriptions, part numbers, supplier information, pricing, and stock levels. By utilizing the inventory management features within a CMMS, organizations can streamline their maintenance processes and eliminate the need for separate software applications or paper and spreadsheets.
Benefits of a CMMS for Centralizing Inventory Management & Improving KPIs
A CMMS offers significant benefits when it comes to improving Inventory KPIs in maintenance management. The following are some significant advantages that a CMMS brings to inventory management:
1. Real-time Visibility into Inventory Levels
With a CMMS in place, maintenance teams have access to real-time information about inventory levels. Common CMMS inventory management features such as QR code scanning to pull up part details, cycle count tracking and scheduling, min and max quantity thresholds, and reorder points give users instant insights into the state of their inventory. This allows them to monitor stock levels accurately, ensuring that they always have the necessary spare parts and materials available for maintenance. Real-time visibility eliminates guesswork and provides a clear understanding of stock availability, enabling proactive inventory management.
2. Accurate Stock Tracking and Monitoring
CMMS software provides robust inventory tracking capabilities. Each inventory item can be assigned a unique identifier and stored in a centralized database, allowing maintenance teams to track and monitor stock accurately. By having precise visibility into stock movements, including receipt, usage, and disposal, organizations can ensure accurate inventory counts, reduce the risk of inventory discrepancies, and manage costs and budgets better.
3. Streamlined Procurement Processes
CMMS software streamlines the procurement process by automating purchasing tasks. When inventory levels reach predetermined thresholds, the system can automatically notify maintenance and parts managers to restock items that are needed. Some CMMS platforms include a purchase order module that creates PO’s and sends them directly to suppliers. Additionally, for organizations using an external purchase order system, the CMMS can be integrated using its API. This automation eliminates manual intervention and minimizes the chances of stockouts, costly rush orders, and equipment downtime.
4. Data-driven Decision Making
CMMS software collects and analyzes maintenance data, including inventory usage, equipment downtime, and historical maintenance records. By leveraging this data, maintenance managers can make informed decisions regarding inventory management. They can identify patterns and trends, forecast demand accurately, and adjust inventory levels accordingly. Data-driven decision making ensures that inventory is optimized based on actual maintenance needs, reducing carrying costs and ensuring necessary parts are available with the right quantity.
Improving Stock Availability with CMMS
A CMMS offers significant benefits in improving stock availability by providing centralized inventory management and enabling automatic inventory replenishment.
1. Centralized Inventory Management
1.1 Consolidation of inventory data in one system
A CMMS allows organizations to consolidate spare parts inventory data into a single cloud-based system. This consolidation brings together information such as stock levels, item descriptions, suppliers, and locations, providing a real-time comprehensive view of the spare parts inventory landscape. Centralized inventory management ensures accurate and up-to-date inventory information, facilitating efficient spare parts tracking and availability.
For example, manufacturing plants use CMMS software to manage their inventory ensuring that spare parts are readily available. According to some reports, equipment downtime for one hour can be as high as $260,000. For businesses that rely on production machinery that needs to be online as much as possible, having access to replacement parts is critical. Long lead times waiting for parts can have disastrous effects on the bottom line for many businesses in manufacturing. CMMS software is a tool that assists maintenance managers with making sure parts are available, streamlining ordering processes and shortening lead times.
1.2 Easy access to inventory information for maintenance teams
A CMMS empowers maintenance teams with easy access to critical inventory information. For instance, technicians can quickly check stock levels, view item specifications, and identify availability through the software with a mobile device. This accessibility streamlines inventory retrieval and helps avoid delays in maintenance activities. By having instant access to inventory data, maintenance teams can plan effectively and ensure that the required stock is readily available.
A hospital can adopt a CMMS to improve spare parts stock availability for medical equipment maintenance. By centralizing inventory data in the CMMS, the hospital gains visibility into stock levels, specifications, and suppliers. Maintenance teams can easily access this information to identify and retrieve the necessary spare parts for medical equipment repairs. The CMMS facilitates streamlined spare parts management, minimizing equipment downtime, optimizing spare parts utilization, and lowering lead time for orders.
2. Automatic Inventory Replenishment
2.1 Setting up reorder points and safety stock levels
By utilizing a CMMS, organizations can establish reorder points and safety stock levels for inventory items. For example, an airline maintenance department can set up reorder points for critical spare parts used in aircraft maintenance. Once the inventory level falls below the reorder point, the CMMS automatically triggers alerts to restock the item. Some CMMS systems allow users to generate purchase orders directly to suppliers. This proactive approach ensures that stock is replenished in a timely manner, reducing the risk of stockouts.
2.2 Automating purchase orders and restocking processes
Many CMMS enable the automation of purchase orders and restocking processes. These applications not only alert users when parts and materials are low, and need to be reordered, CMMS systems can start the purchase order process and complete it entirely. PO capabilities vary between software providers, but most involve a user submitting a request, which is reviewed and approved or rejected). If the request is approved, a purchase order is generated and sent directly to the supplier. Some advanced CMMS platforms allow vendors to engage directly with the PO through a secured link which keeps all activities within the software, from start to finish. Orders can be checked, received and inventory stock levels care adjusted. For organizations with a purchase order system already in place, the CMMS can be integrated through its API. For large ERP or accounting systems, some CMMS will have a pre-built out of the box connector, reducing the effort of building a custom integration..
Optimizing Inventory Turnover with CMMS
Inventory turnover is an important metric in maintenance management as it indicates how efficiently inventory is being utilized and replenished. A CMMS offers several advantages in optimizing inventory turnover, resulting in improved operational efficiency and reduced carrying costs.
1. Streamlined Maintenance Workflows
1.1 Efficient work order management
A CMMS streamlines work order management processes, ensuring that maintenance tasks are executed promptly and efficiently. Work orders generated within the CMMS can include specific inventory requirements, enabling maintenance technicians to access necessary parts or materials directly from the system. This streamlined workflow reduces delays caused by manual inventory retrieval and due to searching for parts and materials that are associated with the work order. This contributes to optimizing inventory turnover. For example, in a healthcare facility, a CMMS can generate work orders for equipment maintenance, listing the required spare parts and consumables, their availability and location, ensuring that technicians can quickly access and utilize the necessary inventory.
1.2 Timely completion of maintenance tasks
A CMMS facilitates efficient scheduling, assignment, and tracking of maintenance tasks. By providing visibility into task statuses and timelines, the system ensures that maintenance activities are completed on time. This helps prevent unnecessary downtime and ensures that inventory is utilized optimally. For instance, in the energy sector, a CMMS can schedule routine maintenance for turbines, allowing maintenance teams to replace worn-out components before they cause breakdowns. This proactive approach reduces downtime and maximizes inventory turnover by minimizing the need for emergency last minute orders.
2. Reduced Equipment Downtime and Improved Maintenance Efficiency
2.1 Impact on inventory turnover and carrying costs
By using a CMMS to streamline maintenance processes and reduce equipment downtime, organizations can significantly improve inventory turnover. When maintenance tasks are completed efficiently, equipment uptime increases, minimizing the need for excess inventory to cover extended downtime periods. This optimization of inventory turnover directly impacts carrying costs by reducing the amount of inventory held in stock. For example, in the manufacturing industry, a CMMS manages preventive maintenance scheduling, ensuring that equipment is serviced at regular intervals, minimizing unplanned breakdowns, and optimizing inventory turnover.
Minimizing Carrying Costs with a CMMS
A CMMS offers valuable capabilities to optimize spare parts inventory and reduce associated costs. Let's explore these benefits in the context of maintenance management, focusing on accurate demand forecasting and just-in-time inventory management:
1. Accurate demand forecasting
1.1 Historical data analysis
By utilizing a CMMS, maintenance teams can analyze historical maintenance data, including past work orders, equipment breakdowns, and spare parts usage. This data provides insights into demand patterns, identifying the frequency and quantity of spare parts required for maintenance assignments. For example, by analyzing historical data, a maintenance manager at a manufacturing plant can identify the specific spare parts that are frequently needed for maintenance tasks on critical production machinery.
1.2 Predictive maintenance insights
A CMMS integrated with predictive maintenance technologies, such as IoT sensors or machine learning algorithms, allows for real-time monitoring of equipment health and performance. By collecting data on equipment conditions, organizations can proactively identify potential failures and maintenance needs. This data-driven approach enables more accurate demand forecasting for spare parts. For instance, a CMMS integrated with condition monitoring sensors for an HVAC system can provide insights into the health of critical components, such as filters and motors, ensuring that the inventory is stocked based on predicted maintenance requirements.
2. Just-in-time inventory management
2.1 Optimizing reorder points and safety stock levels
With a CMMS, organizations can set optimal reorder points and safety stock levels for spare parts inventory. By considering lead times, equipment criticality, and maintenance schedules, organizations can determine the appropriate reorder points to trigger restocking. Safety stock levels provide a buffer to account for unexpected demand variations or lead time fluctuations. For instance, a facility management company can set reorder points (minimum qty. thresholds) for commonly used spare parts based on historical consumption data, ensuring that inventory is replenished just in time to meet maintenance demands.
2.2 Reducing excess inventory and associated costs
By implementing just-in-time inventory practices through a CMMS, organizations can minimize excess inventory of spare parts. Maintaining a lean inventory reduces carrying costs associated with storage, obsolescence, and capital tied up in excess stock. For example, a maintenance department in a power plant can leverage a CMMS to optimize spare parts inventory for turbines. By accurately forecasting maintenance needs and adjusting reorder points, the department can reduce excess inventory levels, ultimately minimizing carrying costs.
CMMS for Seamless Inventory Management
An effective CMMS implementation for inventory management not only enables seamless work order management but also drives improvements in inventory management KPIs. By optimizing inventory levels, improving stock availability, and reducing carrying costs, organizations can improve operational efficiency, reduce downtime, and achieve cost savings. Embracing a CMMS empowers organizations to take control of their inventory management processes, leading to improved maintenance outcomes and overall operational success.
TABLE OF CONTENTS
- Benefits of a CMMS for Centralizing Inventory Management & Improving KPIs
- 1. Real-time Visibility into Inventory Levels
- 2. Accurate Stock Tracking and Monitoring
- 3. Streamlined Procurement Processes
- 4. Data-driven Decision Making
- Improving Stock Availability with CMMS
- 1. Centralized Inventory Management
- 2. Automatic Inventory Replenishment
- Optimizing Inventory Turnover with CMMS
- 1. Streamlined Maintenance Workflows
- 2. Reduced Equipment Downtime and Improved Maintenance Efficiency
- Minimizing Carrying Costs with a CMMS
- 1. Accurate demand forecasting
- 2. Just-in-time inventory management
- CMMS for Seamless Inventory Management
Keep Reading
Introduction Maintenance management is the foundation of maintenance operations in industries ...
11 Feb 2025
Introduction A Computerized Maintenance Management System (CMMS) is software designed to help ...
7 Feb 2025
Ever find yourself checking into a luxury hotel and expecting a relaxing stay, only to find a ...
11 Apr 2025
Organizations are witnessing swift changes in the business environment and confronting a ...
8 Apr 2025
Last month, news outlets and the entire internet was abuzz with the return of NASA astronauts ...
3 Apr 2025
What comes first - CMMS or predictive maintenance? If your answer is either, it is correct. ...
28 Mar 2025
Artificial intelligence (AI) talk has become commonplace. Today, engaging in business-focused ...
27 Mar 2025
Imagine a world where machines predict, diagnose, and fix their issues before they fail. This ...
25 Mar 2025
A facility maintenance plan is at the core of a facility’s operations. This organized ...
21 Mar 2025
Think of managing your maintenance operations like managing a championship sports team. Just ...
21 Mar 2025
The maintenance sector is battling a severe talent shortage that threatens to undermine ...
7 Mar 2025
Manufacturing maintenance is the backbone of industrial efficiency, ensuring machines run ...
5 Mar 2025
No one likes playing a guessing game when equipment breaks down. Yet, maintenance teams often ...
4 Mar 2025
The size of the preventive maintenance software market is discussed in millions of dollars, ...
4 Mar 2025
The organizational structure and corporate hierarchy vary from company to company. Large ...
28 Feb 2025
Maintenance procedures are essential for ensuring the longevity and reliability of machinery ...
21 Feb 2025
Sustainability is no longer just a buzzword; it's a critical component of corporate social ...
20 Feb 2025
A Computerized Maintenance Management System (CMMS) relies on accurate, well-organized data ...
18 Feb 2025
In an era where technology drives operational efficiency, Computerized Maintenance Management ...
14 Feb 2025
A Computerized Maintenance Management System (CMMS) is a key component of modern maintenance ...
13 Feb 2025
Introduction Maintenance management is the foundation of maintenance operations in industries ...
11 Feb 2025
Introduction A Computerized Maintenance Management System (CMMS) is software designed to help ...
7 Feb 2025
Ever find yourself checking into a luxury hotel and expecting a relaxing stay, only to find a ...
11 Apr 2025
Organizations are witnessing swift changes in the business environment and confronting a ...
8 Apr 2025
Last month, news outlets and the entire internet was abuzz with the return of NASA astronauts ...
3 Apr 2025
What comes first - CMMS or predictive maintenance? If your answer is either, it is correct. ...
28 Mar 2025
Artificial intelligence (AI) talk has become commonplace. Today, engaging in business-focused ...
27 Mar 2025
Imagine a world where machines predict, diagnose, and fix their issues before they fail. This ...
25 Mar 2025
A facility maintenance plan is at the core of a facility’s operations. This organized ...
21 Mar 2025
Think of managing your maintenance operations like managing a championship sports team. Just ...
21 Mar 2025
The maintenance sector is battling a severe talent shortage that threatens to undermine ...
7 Mar 2025
Manufacturing maintenance is the backbone of industrial efficiency, ensuring machines run ...
5 Mar 2025
No one likes playing a guessing game when equipment breaks down. Yet, maintenance teams often ...
4 Mar 2025
The size of the preventive maintenance software market is discussed in millions of dollars, ...
4 Mar 2025
The organizational structure and corporate hierarchy vary from company to company. Large ...
28 Feb 2025
Maintenance procedures are essential for ensuring the longevity and reliability of machinery ...
21 Feb 2025
Sustainability is no longer just a buzzword; it's a critical component of corporate social ...
20 Feb 2025
A Computerized Maintenance Management System (CMMS) relies on accurate, well-organized data ...
18 Feb 2025
In an era where technology drives operational efficiency, Computerized Maintenance Management ...
14 Feb 2025
A Computerized Maintenance Management System (CMMS) is a key component of modern maintenance ...
13 Feb 2025
Introduction Maintenance management is the foundation of maintenance operations in industries ...
11 Feb 2025
Introduction A Computerized Maintenance Management System (CMMS) is software designed to help ...
7 Feb 2025