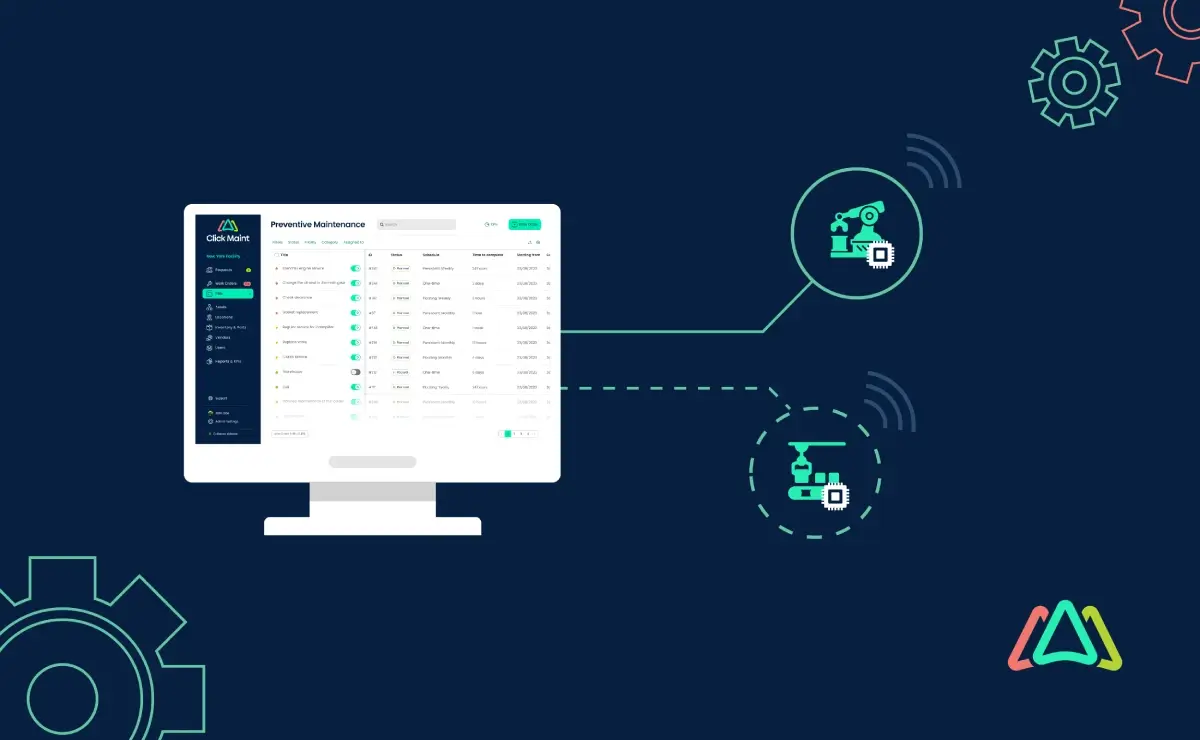
How Accurate Data Collection Drives Smarter Maintenance Decisions
In the world of maintenance management, data reigns supreme.
Did you know that organizations with data-driven maintenance strategies or predictive maintenance strategies experience 30%-50% less machine downtime?
Your ability to make smart decisions hinges on the accuracy of the information at your fingertips. As maintenance professionals, you're tasked with keeping operations running smoothly, keeping costs under control, and performing equipment optimally. To achieve these goals, you need reliable, up-to-date data to guide your choices.
From asset performance metrics to work order history, every piece of information contributes to your overall maintenance strategy. However, collecting and managing this data effectively can be challenging.
Enter Computerized Maintenance Management Systems (CMMS), your maintenance tool for collecting, organizing, and analyzing critical maintenance data. By leveraging a CMMS, you can transform raw data into actionable insights, driving smarter maintenance decisions and ultimately boosting your organization's bottom line.
This article explores how accurate data collection drives smarter maintenance decisions and how Computerized Maintenance Management Systems (CMMS) can be your ally in this endeavor.
The Importance of Accurate Data Collection in Maintenance Management
Accurate data collection is a fundamental component of effective maintenance management. By gathering precise information on asset performance, maintenance history, and work orders, you can make informed decisions that optimize operations. Reliable data enables predictive maintenance strategies, efficient resource allocation, and improved budgeting reducing costly downtime and extending equipment lifespan.
Without it, you risk increased downtime, higher costs, and equipment failures. Implementing standardized data collection practices ensures consistency across teams, ultimately driving smarter maintenance decisions and enhancing overall operational efficiency.
1.1. Role of Data in Maintenance
Integrating CMMS software automates work orders and scheduling, streamlining maintenance workflows and providing valuable insights for strategic planning and operational improvements.
Inaccurate maintenance data often results in increased equipment downtime, as improper scheduling and resource allocation can delay critical repairs.
This ripple effect translates to higher operational costs and potential equipment failures, jeopardizing both productivity and safety. Data decay further compounds these issues, eroding the reliability of maintenance decisions over time.
By leveraging comprehensive asset performance data, maintenance history, and work order information, organizations can make informed decisions that drive operational efficiency and minimize disruptions.
1.2. Types of Data in Maintenance Management
In maintenance management, various types of data play important roles.
Asset Performance Metrics
Maintenance managers rely on various data types to make informed decisions. Asset performance data includes metrics like uptime, efficiency, and output quality. This critical information helps identify underperforming assets and optimize maintenance schedules.
Asset performance metrics provide key insights into equipment efficiency and reliability. This data helps establish operational benchmarks, prevent breakdowns, and optimize maintenance operations.
Financial and Operational Data
Detailed financial data is essential for budget management and cost control. Operational data, including work orders, inventory levels, and maintenance history, contributes to overall strategy formulation. Centralizing this information enables more effective resource allocation and smart maintenance.
Maintenance History
Detailed maintenance records track past repairs, replacements, and servicing. This historical data enables trend analysis and informs future maintenance planning.
Work Orders and Inventory Levels
Work order data captures task details, while inventory data tracks spare part availability.
Together, they support efficient resource allocation and prevent maintenance delays.
1.3. Impact on Decision-Making
Accurate data enables predictive maintenance, reducing maintenance costs by 25-30%.
Enhanced Predictive Maintenance
Accurate data collection enables smarter decision-making in maintenance management by enhancing predictive capabilities. With reliable data, maintenance teams can identify potential equipment failures before they occur, reducing downtime and costs.
Improved Resource Allocation
Data-driven insights allow for better resource allocation, ensuring that maintenance efforts are focused where they're most needed. This optimization leads to increased efficiency and cost-effectiveness in maintenance operations.
Challenges in Accurate Data Collection
Poor data quality can have far-reaching impacts. It often leads to suboptimal maintenance scheduling, inventory mismanagement, and incorrect failure diagnostics. These issues can result in increased downtime, higher costs, and equipment failures, ultimately compromising overall maintenance efficiency.
2.1. Common Issues in Data Collection
Manual data entry remains a significant challenge in maintenance management. Studies show human error rates in manual data entry as high as 1-5% for complex data, leading to costly mistakes and potentially impacting decision making.
In fact, Gartner estimates poor data quality costs businesses an average of $15 million annually. These errors can result in incorrect work orders, misdiagnosed equipment failures, and inefficient resource allocation, ultimately compromising maintenance effectiveness and increasing operational costs.
Manual data entry often leads to errors, with studies showing up to 88% of spreadsheets contain mistakes.
Inconsistent Data Repercussions
Inconsistent data entry practices can significantly impact maintenance management efficiency. Different teams or shifts may use varying abbreviations, spellings, and formats, leading to confusion and errors.
This lack of standardization can result in inaccurate reporting, ineffective resource allocation, and missed maintenance opportunities. Implementing a CMMS with standardized data entry guidelines and validation checks can help ensure consistency and improve overall data quality across your organization.
Data Silos and Quality Concerns
Data silos are isolated repositories of information controlled by individual departments, often incompatible with other data sources in the organization. These silos typically arise from decentralized IT strategies and organizational structures where different units operate independently. The consequences of this can be significant, including incomplete data sets, inconsistent reporting, and reduced collaboration between teams. To break down these barriers, companies should implement centralized data management systems and foster a culture of data sharing.
2.2. Consequences of Inaccurate Data
Poor data quality can have far-reaching impacts. It often leads to suboptimal maintenance scheduling, inventory mismanagement, and incorrect failure diagnostics. These issues can result in increased downtime, higher costs, and equipment failures, ultimately compromising overall maintenance efficiency.
Operational Inefficiencies
Inaccurate data can lead to decreased wrench time, incomplete work tasks, and inefficient use of specialized skills. This results in operational inefficiencies that can significantly impact maintenance productivity and increase downtime.
Increased Maintenance Costs
Poor data quality often leads to obsolete part catalogs and missing spare parts, which negatively impacts preventative maintenance. These issues can substantially increase maintenance costs and equipment failures, highlighting the importance of smart maintenance decisions based on accurate data collection.
Poor Decision-Making
Inaccurate data negatively impacts maintenance strategies, resulting in increased equipment downtime and higher repair costs. Misguided resource allocation can stem from unreliable information, causing inefficiencies in workforce deployment and inventory management.
Compromised Safety and Compliance
Faulty data may obscure potential safety hazards, putting workers at risk. It can also lead to non-compliance with regulatory requirements, exposing organizations to legal and financial repercussions. Accurate data is a key component for maintaining a safe work environment and adhering to industry standards.
Additionally, faulty data can lead to incorrect failure diagnostics, potentially causing repeated equipment failures and escalating maintenance costs.
2.3. The Need for Standardization
Standardizing data collection practices is vital for maintaining accuracy and reliability in maintenance management. By establishing uniform formats and procedures, you ensure consistency across teams and shifts, reducing discrepancies and errors.
Standardization facilitates easier data analysis, comparison, and integration with other systems. It also streamlines training processes and improves overall efficiency.
Implementing standardized methods eliminates discrepancies, reduces errors, and makes it easier to analyze and report. Moreover, it enables more accurate trend identification and forecasting, ultimately leading to better-informed maintenance decisions and improved overall operational efficiency.
This includes using consistent terminology, data entry formats, and collection methods across your organization. By establishing standardized protocols for data entry, asset tagging, and reporting, you can streamline reporting, improve resource planning, and enhance communication among teams.
How a CMMS Enables Accurate Data Collection
A Computerized Maintenance Management System (CMMS) revolutionizes data collection in maintenance operations.
3.1. Automation of Data Entry
CMMS software significantly reduces human error by automating data capture and entry processes. Integrating with loT devices facilitates real-time data collection directly from equipment sensors and connected devices.
This automation not only improves accuracy but also saves time, allowing maintenance teams to focus on analysis and decision-making rather than manual data input. By eliminating manual input, CMMS reduces typos, omissions, and other common data entry mistakes that can lead to costly maintenance errors and provides up-to-the-minute insights.
This real-time data empowers maintenance teams to make informed decisions quickly, optimizing equipment uptime and efficiency.
The result is a more efficient, reliable maintenance operation driven by precise, up-to-date information.
3.2. Centralized Data Repository
A CMMS serves as a unified platform for all maintenance-related information, creating a single source of truth. This centralization eliminates data silos, reduces inconsistencies, and improves data accessibility. By housing all data in one location, maintenance teams can quickly access, retrieve, and analyze critical historical records, track asset performance, and generate comprehensive reports leading to more efficient operations and better resource allocation.
The centralized repository also facilitates seamless collaboration among team members, enhancing overall maintenance effectiveness.
This streamlined approach enhances decision-making processes, leading to more efficient maintenance operations and improved overall asset management.
Real-Time Data Collection
Real-time data updates in CMMS provide a significant advantage for maintenance decision-making. By offering instant access to the latest information, managers can respond swiftly to emerging issues, optimizing resource allocation and minimizing downtime. This immediacy enables proactive maintenance strategies, allowing teams to address potential problems before they escalate.
Additionally, real-time updates facilitate better coordination among staff, ensuring everyone works with the most current information available.
3.3. Real-Time Data Updates
Real-time data availability in CMMS systems promotes effective maintenance decision-making. By providing up-to-the-minute information on asset performance, work order status, and inventory levels, managers can respond swiftly to emerging issues.
This immediate access enables proactive maintenance, reducing downtime and optimizing resource allocation.
CMMS features like mobile apps and loT integration further enhance real-time capabilities, allowing technicians to input data on the go and get real-time data on equipment and machine conditions.
Mobile apps allow technicians to input data on the go, instantly syncing with the central system. IoT integration enables continuous monitoring of equipment performance, triggering immediate alerts for anomalies or failures.
Automated work order generation responds to real-time data, ensuring timely maintenance. These features empower teams to make swift, informed decisions, minimizing downtime and optimizing asset performance.
3.4. Enhanced Reporting and Analytics
CMMS provides powerful tools for data analysis, enabling maintenance teams to identify trends, track performance, and implement predictive maintenance strategies. With customizable dashboards and real-time KPI tracking, managers can make data-driven decisions quickly. Advanced reporting features allow for in-depth analysis of asset performance, maintenance costs, and resource utilization, helping organizations optimize their maintenance operations and reduce downtime.
CMMS software offers powerful analytical tools that transform raw maintenance data into actionable insights. These platforms provide customizable dashboards and reports, enabling teams to identify equipment performance trends, track key metrics, and predict potential failures.
CMMS software offers powerful analytical tools that transform raw maintenance data into actionable insights. By leveraging advanced machine learning algorithms, these systems can identify recurring issues, track key performance indicators, optimize schedules, and forecast potential equipment failures.
This enables maintenance teams to make data-driven decisions, optimize resource allocation, and implement proactive maintenance strategies, ultimately reducing downtime and extending asset life cycles.
CMMS software offers a wealth of reporting capabilities, enabling maintenance teams to visualize key performance indicators (KPIs) and trends. Common reports include equipment downtime analysis, work order completion rates, and maintenance cost breakdowns.
Many CMMS platforms feature customizable dashboards, allowing users to track metrics like mean time between failures (MTBF) and overall equipment effectiveness (OEE) at a glance.
Best Practices for Leveraging a CMMS for Accurate Data Collection
Training and Integration
Implementing comprehensive staff training on CMMS usage is essential to ensure consistent data entry. Integrating CMMS with other systems like ERP and loT devices for seamless data flow and regularly auditing data quality, and setting up automated alerts within the CMMS will help maintain accuracy.
Continuous Improvement
Foster a culture of ongoing refinement in your maintenance team. Regularly review and update data collection processes, encouraging feedback and adapting to evolving needs.
This proactive approach helps optimize CMMS utilization and enhances overall maintenance efficiency.
4.1. Training and Onboarding
Effective CMMS implementation hinges on comprehensive staff training. Proper training is crucial for maximizing the benefits of your CMMS investment. Well-trained staff can leverage the system's full potential, ensuring accurate data collection and optimal maintenance decisions.
Strategies for Ensuring Consistent Use of CMMS by Team Members
- Establish clear protocols.
- Develop standardized procedures for CMMS usage across departments.
- Create step-by-step guides for common tasks like work order creation and asset updates.
- Implement a consistent naming convention for assets and maintenance activities to ensure uniformity.
Regular Training and Refresher Courses
Conduct periodic training sessions to keep staff up-to-date on CMMS features and best practices. Offer both group workshops and one-on-one coaching to address individual needs. Consider creating short video tutorials for quick reference. Establish a strong relationship with your CMMS provider and lean on their customer success team to keep users up to date on software updates, new features, support resources, and additional training when needed.
Incentivize Adoption
Recognize and reward employees who consistently use the CMMS effectively.
Integrate CMMS usage into performance evaluations to underscore its importance.
Highlight success stories where accurate data entry led to improved maintenance outcomes.
Consider designating "CMMS champions" to provide ongoing support and reinforce best practices. By investing in thorough training, you'll maximize CMMS adoption, improve data accuracy, and ultimately drive smarter maintenance decisions.
4.2. Regular Data Audits
Implementing routine checks is crucial for maintaining data accuracy and integrity in your CMMS.
- Establish a schedule for systematic reviews of your maintenance data, focusing on key metrics and high-priority assets.
- Utilize automated alerts within your CMMS to flag potential discrepancies, anomalies or missing information in real-time.
This proactive approach helps identify and rectify issues promptly, ensuring your maintenance decisions are always based on reliable, up-to-date data and rectify issues before they impact decision-making processes.
- Consider implementing a tiered audit system with daily quick checks, weekly reviews, and monthly comprehensive audits.
- Implement data validation rules to catch errors at the point of entry, reducing the likelihood of inaccurate information making its way into your system.
- Consider conducting periodic spot checks or random sampling of work orders and asset records to verify their accuracy.
By consistently monitoring and verifying your data, you'll build a solid foundation for informed decision-making and optimize your maintenance strategies. This approach ensures ongoing data quality while balancing resource allocation. Additionally, team members from different departments should be involved in the audit process to gain diverse perspectives and foster a culture of data responsibility across the organization.
Configuring Automated Alerts
- Set up your CMMS to send notifications for critical events like equipment failures or maintenance due dates.
- Customize alert thresholds and recipients to ensure timely responses.
- Utilize email, SMS, or in-app notifications to reach team members effectively.
4.3. Integration with Other Systems
Seamlessly integrating your CMMS with ERP, IoT devices, and other management systems unlocks powerful synergies and creates a powerful ecosystem for seamless data flow. This interconnectivity enables real-time data flow across platforms, enhancing decision-making capabilities. By breaking down data silos, you'll gain a holistic view of your maintenance operations. Careful planning and execution are crucial for smooth integration, ensuring compatibility and data integrity across systems.
- By connecting with ERP systems, you'll synchronize financial data, streamlining budgeting and cost tracking for maintenance activities.
- IoT integration enables real-time equipment monitoring, facilitating predictive maintenance and reducing downtime.
- Linking with inventory management systems ensures accurate parts availability, preventing delays in repairs.
Ultimately, integration drives efficiency, cuts costs, and improves overall maintenance performance by leveraging the strengths of each connected system.
Steps to Ensure Smooth Integration
- Plan and prepare
Begin by mapping out your existing systems and data flows. Identify key integration points and potential challenges.
Establish clear objectives for the integration process and set realistic timelines.
- Choose the right integration method
Select an appropriate integration method based on your CMMS and other systems. Options may include API connections, middleware solutions, or custom integrations.
Consider factors like data volume, frequency of updates, and security requirements.
- Test thoroughly and implement gradually
Conduct rigorous testing in a controlled environment before full implementation. Start with a pilot program to identify and address any issues. Gradually roll out the integration across your organization, providing support and training as needed.
Benefits of Integration
- Real-time data synchronization across platforms.
- Elimination of data silos and manual data transfer.
- Improved accuracy and consistency of maintenance information
Flowchart for Smooth Integration
- Identify integration points and data requirements
- Ensure compatibility of systems and data formats
- Implement secure API connections
- Conduct thorough testing and validation
- Provide training on integrated workflows
By leveraging system integration, you'll unlock the full potential of your CMMS and drive smarter maintenance decisions.
4.4. Continuous Improvement and Feedback Loop
Implementing a CMMS is not a one-time event but an ongoing process of refinement. Regularly review and update your data collection processes to ensure they remain effective and aligned with your maintenance goals.
Embracing a Culture of Refinement
Encourage your team to provide feedback on the system's usability and suggest improvements. This collaborative approach fosters a culture of continuous improvement within your maintenance department. Implementing a robust feedback loop is crucial for maintaining data accuracy and enhancing CMMS effectiveness. Regularly review and update your data collection processes, encouraging team members to report inconsistencies or suggest improvements. Establish key performance indicators (KPIs) to measure data quality and CMMS usage. Foster a culture of continuous improvement by recognizing and rewarding team members who contribute to data accuracy and system optimization.
Importance of Regular Review and Updating Data Collection Processes
Regular review and updating of data collection processes is crucial for maintaining the accuracy and relevance of your maintenance data. By consistently evaluating your current practices, you can identify areas for improvement and adapt to changing needs.
This ongoing refinement ensures that your CMMS remains a valuable tool for decision-making.
Implement a schedule for periodic audits of your data collection methods involving key stakeholders from different departments. Encourage regular brainstorming sessions to identify areas for enhancement in data collection processes. Implement a rewards system for innovative ideas that lead to more accurate data or streamlined workflows.
Use these reviews to:
- Assess the quality and completeness of collected data.
- Identify bottlenecks or inefficiencies in the collection process.
- Update data fields or categories to reflect evolving maintenance requirements.
Incorporate feedback from end-users to enhance usability and adoption. By fostering a culture of continuous improvement, you'll maximize the value of your CMMS and drive smarter maintenance decisions.
Implement Feedback Loops
Establish channels for ongoing communication between maintenance staff and management. Regularly solicit feedback on the CMMS's effectiveness and ease of use. Use this input to refine data collection methods, update training materials, and optimize the system's interface. Remember, your team's hands-on experience is invaluable for driving continuous improvement in maintenance operations.
Conclusion
In conclusion, accurate data collection is a key component of effective maintenance management. By leveraging a robust CMMS solution, you can overcome common data challenges and drive smarter decision-making across your organization. Implementing best practices for data collection and management is an ongoing process. Regularly audit your data, invest in proper training, and foster a culture of continuous improvement. As you refine your data collection strategies, you'll unlock new insights that lead to increased efficiency, reduced downtime, and optimized resource allocation. Embrace the power of accurate data, and watch as your maintenance operations transform, delivering tangible benefits to your bottom line and overall operational excellence.
TABLE OF CONTENTS
Keep Reading
Ever find yourself checking into a luxury hotel and expecting a relaxing stay, only to find a ...
11 Apr 2025
Organizations are witnessing swift changes in the business environment and confronting a ...
8 Apr 2025
Last month, news outlets and the entire internet was abuzz with the return of NASA astronauts ...
3 Apr 2025
What comes first - CMMS or predictive maintenance? If your answer is either, it is correct. ...
28 Mar 2025
Artificial intelligence (AI) talk has become commonplace. Today, engaging in business-focused ...
27 Mar 2025
Imagine a world where machines predict, diagnose, and fix their issues before they fail. This ...
25 Mar 2025
A facility maintenance plan is at the core of a facility’s operations. This organized ...
21 Mar 2025
Think of managing your maintenance operations like managing a championship sports team. Just ...
21 Mar 2025
The maintenance sector is battling a severe talent shortage that threatens to undermine ...
7 Mar 2025
Manufacturing maintenance is the backbone of industrial efficiency, ensuring machines run ...
5 Mar 2025
No one likes playing a guessing game when equipment breaks down. Yet, maintenance teams often ...
4 Mar 2025
The size of the preventive maintenance software market is discussed in millions of dollars, ...
4 Mar 2025
The organizational structure and corporate hierarchy vary from company to company. Large ...
28 Feb 2025
Maintenance procedures are essential for ensuring the longevity and reliability of machinery ...
21 Feb 2025
Sustainability is no longer just a buzzword; it's a critical component of corporate social ...
20 Feb 2025
A Computerized Maintenance Management System (CMMS) relies on accurate, well-organized data ...
18 Feb 2025
In an era where technology drives operational efficiency, Computerized Maintenance Management ...
14 Feb 2025
A Computerized Maintenance Management System (CMMS) is a key component of modern maintenance ...
13 Feb 2025
Introduction Maintenance management is the foundation of maintenance operations in industries ...
11 Feb 2025
Introduction A Computerized Maintenance Management System (CMMS) is software designed to help ...
7 Feb 2025