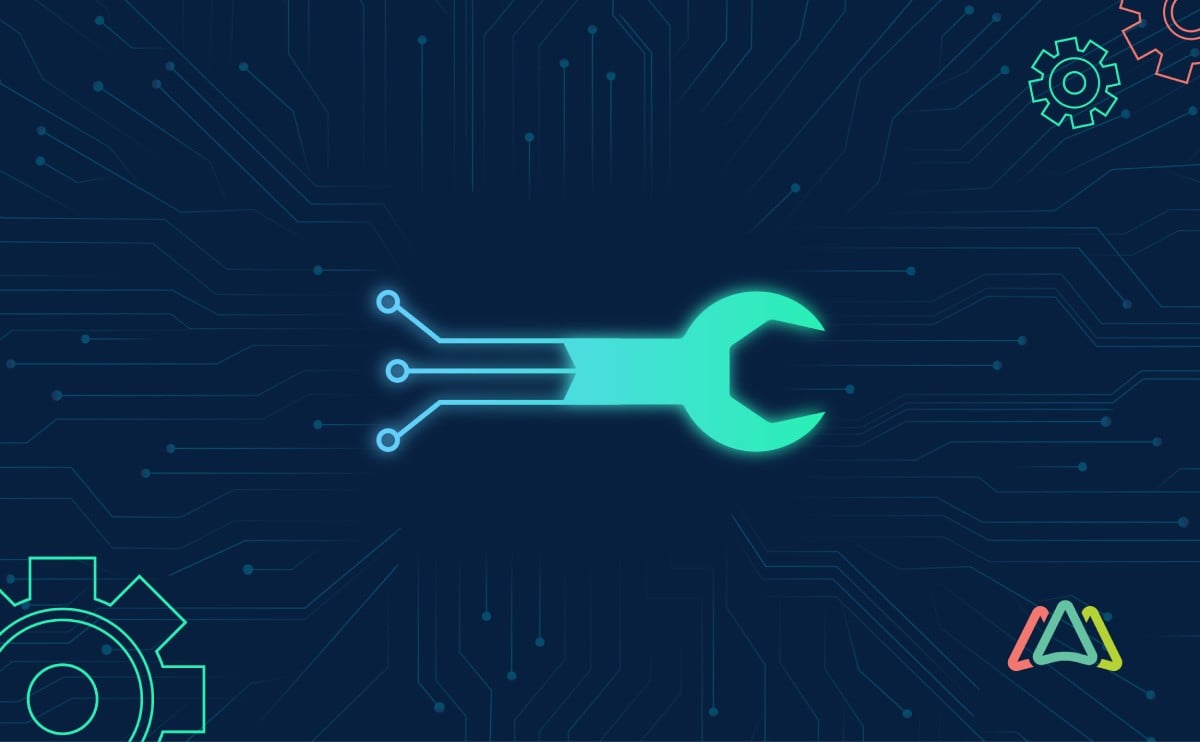
Smart Maintenance and How It Helps Businesses?
The term smart maintenance has recently been making its rounds in industry, media, and colleges. But what does it mean? By definition, smart maintenance refers to all technical and organizational measures aimed at using digital tools to make maintenance and servicing more efficient and contribute to greater value creation for the company. It does this by using extensive amounts of maintenance data to achieve this goal. Through digitalization of maintenance management and using CMMS, IoT, predictive analytics, machine learning, and Industry 4.0 methods, a smart maintenance strategy is able to generate a continuous flow of data. Smart maintenance drives insights from the data inputted into its system to direct accurate decision-making. Continuously evolving and learning algorithms are at the center of smart maintenance, making it a cutting edge approach.
By leveraging smart maintenance, manufacturers can streamline their maintenance processes, improve asset uptime, reduce downtime, cut costs, and boost their bottom line. Whether you have a small business or a large-scale industrial enterprise, incorporating smart maintenance into your maintenance strategy can help you stay ahead of the curve and remain competitive in today's fast-paced market.
What is Smart Maintenance?
Coping with unexpected equipment breakdowns is a common frustration for businesses because they disrupt daily routines. They can also lead to costly repairs and replacements. Improved processes, continuous improvement, and software; have addressed some of these problems. Smart maintenance takes the solution to the next level.
Smart maintenance is an advanced approach to predictive and preventive maintenance that takes advantage of the latest technologies like AI, machine learning, sensors, and automation. It provides proactive insight into the condition of equipment to identify potential issues before they become costly problems. By leveraging data analytics and intelligent systems, smart maintenance helps businesses reduce downtime while improving efficiency and safety. Smart maintenance can also help organizations achieve better asset utilization, extend asset life cycles, expect future needs for repairs or replacement parts, improve energy usage management and maximize resources.
Smart maintenance solutions are revolutionizing the way we approach repairs and upkeep - from monitoring the performance of HVAC systems to detecting leaks and malfunctions in industrial equipment. From predictive maintenance to prescriptive maintenance, there are a variety of maintenance approaches available to fit every need. Predictive maintenance uses sensors and data analysis to predict when equipment may fail before it occurs. Preventive maintenance aims to prevent failures by performing regular maintenance and inspections, while prescriptive maintenance goes even further by providing step-by-step instructions on how to resolve an issue.
Smart maintenance also has the benefit of accelerating automation in maintenance no longer necessitating manual checks and labor-intensive maintenance. Automated maintenance saves time, reduces costly errors, and ensures that equipment and machinery are running at optimal levels, minimizing downtime. Furthermore, it increases the lifespan of equipment and machinery, lowers energy costs, and helps to prevent accidents.
Enable Smart Maintenance with Technology
Smart maintenance exists because of technology and feeds off it. The technology will include but is not limited to:
- CMMS (Computerized Maintenance Management System): This system automates the maintenance process and enables businesses to track information like work orders, preventive maintenance schedules, inventory levels, and more, in one centralized location.
- IoT (Internet of Things): IoT technology enables remote monitoring of equipment performance by gathering data from sensors connected to machines. With this data, companies can identify issues before they become serious problems.
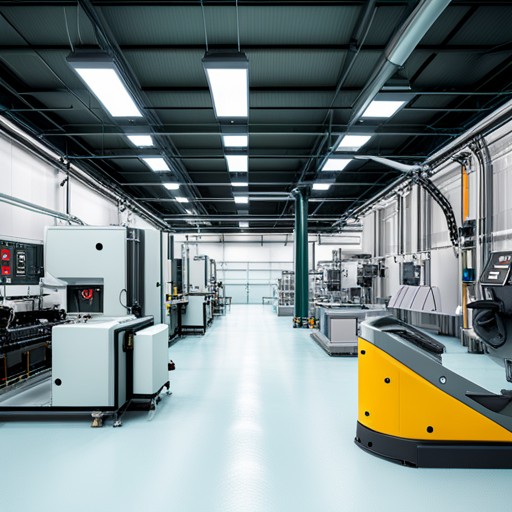
- Predictive Analytics: Predictive analytics utilizes machine learning algorithms to analyze large amounts of data and make predictions on future trends or patterns that may affect the condition or health of machinery.
- Machine Learning & AI: Machine learning and artificial intelligence are being used in smart maintenance solutions to detect anomalies in operations or equipment conditions as well as analyze massive amounts of ever-changing product performance data for better insight into decision-making processes.
- Industry 4.0 Methods: These methods incorporate augmented reality technologies such as virtual reality headsets which allow technicians to visualize objects so they can track difficult tasks without needing physical access. Additionally, these methods include automation technologies such as robotic arms which help reduce labor costs while accelerating production processes for improved cost savings through greater efficiency gains.
How Smart Maintenance Helps Businesses?
Smart maintenance is a relatively new concept, but it has been gaining traction as more businesses recognize its potential to reduce costs and improve efficiency. The idea of using machine learning, automation, and advanced analytics to monitor the condition of equipment originated in the early 2000s when Japanese companies began experimenting with predictive maintenance technologies. Today, smart maintenance systems are used by organizations across industries from manufacturing to healthcare for their ability to optimize operations and enhance safety protocols.
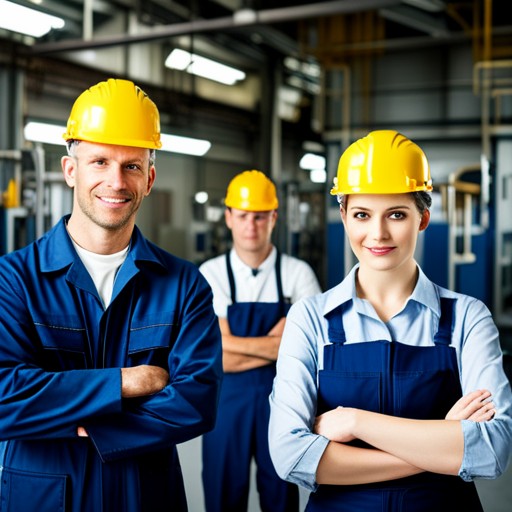
Improved Efficiency and Productivity
Smart maintenance offers a range of advantages that can help businesses increase efficiency and productivity. By automating routine maintenance tasks, such as monitoring asset performance or scheduling preventive maintenance activities, smart maintenance systems free up resources to focus on more pressing issues. Smart maintenance also helps reduce labor costs and energy consumption by optimizing equipment operations and minimizing downtime. Finally, by providing predictive analytics for potential failure points, smart maintenance helps organizations plan and avoid costly disruptions.
Case studies have shown that businesses using smart maintenance systems can experience a significant reduction in operational costs and an increase in productivity. For example, one healthcare provider utilized sensors to monitor the temperature of its equipment and was able to reduce energy costs by 10%. Another manufacturing company saw a 40% decrease in downtime thanks to predictive maintenance.
Reduced Operating Costs and Risk
Smart maintenance helps businesses reduce operating costs and risks in several ways. First, it enables organizations to identify potential failure points before they occur. This allows quick and urgent corrective action. This reduces the amount of time and money spent on repairs and can help minimize downtime. Additionally, smart maintenance systems provide predictive analytics to help businesses anticipate future needs and plan for potential contingencies. This can prevent costly disasters such as equipment failure or production delays. Finally, smart maintenance helps organizations optimize their resource utilization and allocation by providing real-time data that allows them to better manage energy usage and extend asset life cycles.
One of the biggest benefits of using smart maintenance is its ability to reduce operational costs and risks. According to research from PwC, investing in smart maintenance systems can result in savings of up to 30%, with some businesses finding even higher cost reductions. Additionally, the reduction in risks associated with equipment failure or delays can help organizations reduce long-term liability costs and in so doing, they benefit from increased market share.
Improved Quality Control
Smart maintenance provides a significant boost to quality control operations by helping businesses identify and address any potential issues before they become costly production problems. With advanced analytics and predictive maintenance, smart maintenance systems can detect trends and patterns in equipment performance that may indicate an imminent issue. This allows organizations to take corrective action early on, reducing the risk of costly production delays or equipment failures. Additionally, by providing real-time data and automated maintenance reports, smart maintenance systems help organizations stay up-to-date on asset performance and maintain higher levels of quality control.
Studies show that businesses utilizing smart maintenance can achieve significant improvements in quality control. For example, one food manufacturing company reported a 40% reduction in product waste and a 20% improvement in product quality after implementing smart maintenance systems. Another automobile manufacturer saw a 5-10% increase in overall product quality after investing in predictive analytics for its production line.
Implement Smart Maintenance
Fortunately, the smart maintenance implementation process is straightforward and can be tailored to an organization's individual needs. As a starting point, businesses should assess their current systems and processes to determine what areas need improvement. From there, a plan can be created outlining the objectives and requirements for implementing a smart maintenance system. The plan should keep pace with changing technological developments in maintenance. For example, tools such as maintenance hardware that include vibration analysis equipment or a thermal imaging camera, can help detect problems before they become major issues. In combination with predictive maintenance software, real-time analysis of data can be performed to spot patterns and ensure timely repairs. Once the plan is in place, it should be communicated to all employees who will be affected by the change. To ensure successful implementation, businesses should consider partnering with companies that specialize in smart maintenance systems. These organizations can provide tailored solutions based on an organization's specific needs and goals. Additionally, an experienced team can provide valuable guidance and advice during the implementation process. Finally, proper training and onboarding for all employees are essential prerequisite steps before launching any new system.
Increase Stakeholder Value
Businesses exist to grow stakeholder value. Increasing stakeholder value is what successful businesses always strive toward. It will build a reputation in the eyes of shareholders, customers, and other stakeholders. Smart maintenance can play an important role in helping businesses achieve this goal. Increased quality due to smart maintenance will improve customer experience and build customer loyalty. Operating efficiency and cost reductions will help increase mindshare. Smart maintenance will also promote a culture of safety thereby instilling employee loyalty. Over time, smart maintenance will help businesses build brand recognition within the marketplace.
TABLE OF CONTENTS
Keep Reading
Ever find yourself checking into a luxury hotel and expecting a relaxing stay, only to find a ...
11 Apr 2025
Organizations are witnessing swift changes in the business environment and confronting a ...
8 Apr 2025
Last month, news outlets and the entire internet was abuzz with the return of NASA astronauts ...
3 Apr 2025
What comes first - CMMS or predictive maintenance? If your answer is either, it is correct. ...
28 Mar 2025
Artificial intelligence (AI) talk has become commonplace. Today, engaging in business-focused ...
27 Mar 2025
Imagine a world where machines predict, diagnose, and fix their issues before they fail. This ...
25 Mar 2025
A facility maintenance plan is at the core of a facility’s operations. This organized ...
21 Mar 2025
Think of managing your maintenance operations like managing a championship sports team. Just ...
21 Mar 2025
The maintenance sector is battling a severe talent shortage that threatens to undermine ...
7 Mar 2025
Manufacturing maintenance is the backbone of industrial efficiency, ensuring machines run ...
5 Mar 2025
No one likes playing a guessing game when equipment breaks down. Yet, maintenance teams often ...
4 Mar 2025
The size of the preventive maintenance software market is discussed in millions of dollars, ...
4 Mar 2025
The organizational structure and corporate hierarchy vary from company to company. Large ...
28 Feb 2025
Maintenance procedures are essential for ensuring the longevity and reliability of machinery ...
21 Feb 2025
Sustainability is no longer just a buzzword; it's a critical component of corporate social ...
20 Feb 2025
A Computerized Maintenance Management System (CMMS) relies on accurate, well-organized data ...
18 Feb 2025
In an era where technology drives operational efficiency, Computerized Maintenance Management ...
14 Feb 2025
A Computerized Maintenance Management System (CMMS) is a key component of modern maintenance ...
13 Feb 2025
Introduction Maintenance management is the foundation of maintenance operations in industries ...
11 Feb 2025
Introduction A Computerized Maintenance Management System (CMMS) is software designed to help ...
7 Feb 2025