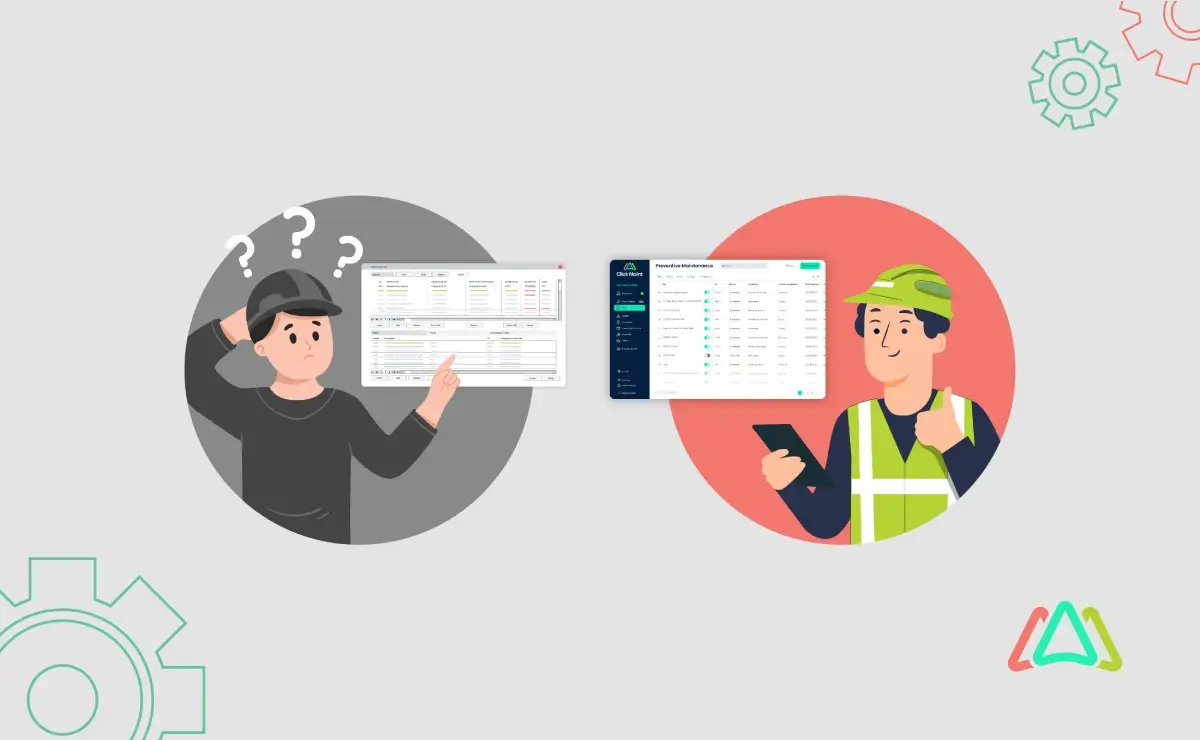
How can Businesses Make the Most of Their CMMS?
In today's competitive business environment, maintaining operational efficiency is important. At the heart of this endeavor lies the Computerized Maintenance Management Systems (CMMS), software solutions designed to streamline maintenance operations. CMMS empowers businesses to efficiently manage assets, schedule maintenance tasks, and track maintenance activities, all within a single platform. Preventive maintenance is an important element in facilities management, serving as an approach to equipment upkeep.
However, despite the vast potential CMMS offers, a prevalent issue persists: many businesses fail to fully capitalize on the features at their disposal. This underutilization limits their ability to obtain the full benefits of the CMMS, leading to inefficiencies, missed opportunities for cost savings, and decreased overall productivity. In this article, we’ll explore the reasons behind this challenge and suggest ways to help businesses obtain maximum value from their CMMS investment.
Why Businesses Fail to Take Full Advantage of CMMS Features
1. Lack of Awareness about Available Features
One of the primary challenges hindering effective CMMS utilization is the lack of awareness regarding its full features. While businesses invest in CMMS software to streamline maintenance operations, many users often remain unaware of its extensive capabilities. This lack of awareness leads to underutilization, with businesses missing out on opportunities to optimize their maintenance processes and achieve greater efficiency. Without a comprehensive understanding of the available features, organizations may resort to manual methods or supplementary software for tasks that could be easily handled within the CMMS platform.
There are many reasons why CMMS users are not fully aware of all the capabilities and features of the software. Often, the employee who was involved in the evaluation, purchase, and implementation of CMMS left the company. Many times, when people exit an organization, transitioning their duties and knowledge to their successor isn’t complete. Similarly, people come and go and switch roles, and the core group of users that were initially involved in the CMMS implementation are no longer with the organization. Sometimes, it’s just a matter of training. Some businesses don’t see the value in comprehensive training and adopt the learn-as-you-go approach. In many cases, lack of awareness of CMMS features is due to users not keeping updated on new features and software updates. With software as a service (SaaS) subscriptions, the CMMS provider will release new updates monthly or quarterly. They usually provide webinars and email notifications on new features, but it’s up to the users to take the initiative to register for the release, update webinars and read their emails. Ultimately, users should stay connected with the CMMS provider's customer success and account manager to stay current on new features.
2. Misconceptions about Preventive Maintenance
Misconceptions about preventive maintenance can also hinder effective CMMS utilization. Some businesses perceive preventive maintenance as an unnecessary expense to their operations, leading them to lean on reactive maintenance instead, which deals with problems after they arise. However, the reactive approach often results in higher costs, increased downtime, and compromised asset reliability in the long run.
3. Inadequate Understanding of CMMS Capabilities
One of the primary reasons why businesses often fall short in harnessing the full potential of CMMS software is the inadequate understanding of its capabilities and insufficient training. Despite investing in advanced CMMS systems, many organizations fail to grasp the breadth and depth of features offered by these solutions. CMMS software goes beyond mere maintenance scheduling; it encompasses preventive maintenance, asset management, inventory control, and analytics tools, among others. Also, insufficient training stands as a significant barrier to effective CMMS utilization. Many businesses invest in CMMS systems but fail to provide adequate training to their staff, resulting in inefficient usage. Without proper training, users may struggle to navigate the software interface, interpret data, or utilize advanced features effectively. Consequently, frustration and resistance to change may arise, leading to underutilization or abandonment of the system altogether.
However, due to limited awareness or training, users may only utilize basic functionalities, leaving key features unused. This lack of understanding prevents businesses from leveraging CMMS software to its full potential, resulting in missed opportunities for optimizing maintenance processes, enhancing asset reliability, and reducing operational costs.
4. Failure to Assess and Align the CMMS with Business Goals and Processes
Another common challenge that hinders effective CMMS utilization is the failure to align the software with business goals and processes. Implementing a CMMS system without considering the unique requirements and workflows of the organization can lead to inefficiencies and resistance from users. For instance, if the CMMS software does not integrate seamlessly with existing business systems or fails to accommodate specific maintenance procedures, users may perceive it as irrelevant or a waste of time for their daily tasks.
To maximize the value of CMMS software, businesses must ensure that it is tailored to their operational needs and objectives. This entails conducting a thorough assessment of existing maintenance processes, identifying areas for improvement, and configuring the CMMS system accordingly. By aligning CMMS functionalities with business goals, organizations can streamline maintenance operations, enhance productivity, and achieve better outcomes in terms of asset performance and facility management.
5. Resistance to Change
Resistance to change is a significant barrier to the successful adoption and utilization of CMMS software within organizations. Implementing new technology solutions often disrupts established routines and requires users to adapt to new workflows and procedures. This resistance can stem from various factors, including fear of the unknown, reluctance to abandon familiar methods, or concerns about job security.
In conclusion, businesses must address these key challenges to unlock the full potential of CMMS software and realize its benefits in terms of preventive maintenance, facility management, and overall operational efficiency. By enhancing understanding, alignment, and acceptance of CMMS within the organization, businesses can reap the benefits of their CMMS investment.
Recommendations for Getting Better Value from CMMS
1. Invest in comprehensive training for users
To maximize the value derived from CMMS software, businesses should prioritize CMMS training for users. Proper training ensures that employees are proficient in navigating the software, utilizing its features effectively, and understanding how it aligns with their roles and responsibilities. By investing in training, businesses can enhance user competency, boost confidence in utilizing CMMS functionalities, and minimize errors or inefficiencies in maintenance operations.
2. Conduct regular assessments of CMMS utilization and performance
Regular assessments of CMMS utilization and performance are essential for identifying areas of improvement and optimizing system functionality. By analyzing usage metrics, maintenance data, and user feedback, businesses can pinpoint challenges, address training gaps, and implement enhancements to streamline workflows and enhance productivity. Continuous evaluation allows businesses to adapt CMMS strategies to evolving needs and ensure ongoing alignment with business objectives.
Check out our blog on Challenges Faced by Maintenance Leaders and How to Overcome Them
3. Encourage collaboration between maintenance teams and other departments
Effective collaboration between maintenance teams and other departments is required for leveraging CMMS software to its fullest potential. By encouraging cross-functional communication and cooperation, businesses can break down problems and facilitate seamless information sharing and workflow integration. Collaboration enables proactive problem-solving, enhances decision-making processes, and promotes an effective approach to facility management, ultimately leading to improved operational efficiency and asset performance.
4. Leverage advanced features for preventive maintenance scheduling and asset management
To enhance preventive maintenance practices and asset lifecycle management, businesses should leverage advanced features offered by CMMS software. These features may include predictive maintenance analytics, IoT integration, and mobile accessibility for real-time monitoring and diagnostics. By harnessing advanced functionalities, businesses can optimize maintenance schedules, identify potential issues before they escalate, and prolong the lifespan of critical assets, thus minimizing downtime and reducing repair costs.
5. Stay updated on software updates and enhancements
Staying aware of software updates and enhancements is compulsory for ensuring that businesses derive maximum value from their CMMS investment. Regularly updating the software enables businesses to access new features, security patches, and performance improvements, thereby enhancing system functionality and user experience. By staying proactive in software maintenance, businesses can mitigate risks, stay ahead of technological advancements, and maintain optimal system performance.
6. Overcoming resistance to change
Overcoming resistance to change requires leadership, effective communication, and stakeholder engagement. To gain the support and buy-in of employees at all levels, business leaders must clearly communicate the advantages of implementing CMMS software, such as increased productivity, decreased downtime, and cost effectiveness. Providing adequate training, offering ongoing support, and promoting a culture of collaboration and innovation can help mitigate resistance and facilitate the successful integration of CMMS into the organization's maintenance practices.
7. Encourage a culture of continuous improvement and innovation
Lastly, businesses should encourage a culture of continuous improvement and innovation to drive CMMS utilization and optimize maintenance practices. Encouraging employees to explore new techniques, share best practices, and propose innovative solutions cultivates a dynamic and adaptive workforce. By embracing a culture of continuous learning and innovation, businesses can adapt to changing market dynamics, anticipate future challenges, and remain competitive in the evolving landscape of facility management systems and preventive maintenance.
Conclusion
CMMS software serves as a powerful tool for streamlining preventive maintenance, optimizing facility management, and enhancing operational efficiency. By harnessing its full potential, businesses can achieve significant cost savings, minimize downtime, and prolong the lifespan of critical assets. It's essential for organizations to recognize the immense value that CMMS systems offer and prioritize efforts to extract maximum benefits from these solutions.
In this article, we've explored the common challenges hindering businesses from fully leveraging CMMS software, including lack of awareness about available features, misconceptions about preventive maintenance, inadequate understanding of its capabilities, failure to align with business goals, and resistance to change. We've also provided recommendations for overcoming these challenges and maximizing the value derived from CMMS systems.
It is essential that organizations understand the specific challenges that are unique to their businesses models and market, helping them attune intuitively to their needs and requirements.
Businesses should take steps to optimize CMMS utilization within their organizations. This includes investing in comprehensive training for users, conducting regular assessments of system performance, nurturing collaboration between maintenance teams and other departments, leveraging advanced features for preventive maintenance scheduling and asset management, staying updated on software updates and enhancements, and promoting a culture of continuous improvement and innovation.
Before getting started, here are our recommendations to select the right CMMS software for your business. Once you have selected the one that fits your needs, you can follow our insights to overcome common challenges and unlock the full potential of your CMMS software and drive sustainable business growth. It's time to seize the opportunity to enhance preventive maintenance practices, elevate facility management processes, and realize tangible benefits through effective CMMS utilization.
TABLE OF CONTENTS
Keep Reading
Ever find yourself checking into a luxury hotel and expecting a relaxing stay, only to find a ...
11 Apr 2025
Organizations are witnessing swift changes in the business environment and confronting a ...
8 Apr 2025
Last month, news outlets and the entire internet was abuzz with the return of NASA astronauts ...
3 Apr 2025
What comes first - CMMS or predictive maintenance? If your answer is either, it is correct. ...
28 Mar 2025
Artificial intelligence (AI) talk has become commonplace. Today, engaging in business-focused ...
27 Mar 2025
Imagine a world where machines predict, diagnose, and fix their issues before they fail. This ...
25 Mar 2025
A facility maintenance plan is at the core of a facility’s operations. This organized ...
21 Mar 2025
Think of managing your maintenance operations like managing a championship sports team. Just ...
21 Mar 2025
The maintenance sector is battling a severe talent shortage that threatens to undermine ...
7 Mar 2025
Manufacturing maintenance is the backbone of industrial efficiency, ensuring machines run ...
5 Mar 2025
No one likes playing a guessing game when equipment breaks down. Yet, maintenance teams often ...
4 Mar 2025
The size of the preventive maintenance software market is discussed in millions of dollars, ...
4 Mar 2025
The organizational structure and corporate hierarchy vary from company to company. Large ...
28 Feb 2025
Maintenance procedures are essential for ensuring the longevity and reliability of machinery ...
21 Feb 2025
Sustainability is no longer just a buzzword; it's a critical component of corporate social ...
20 Feb 2025
A Computerized Maintenance Management System (CMMS) relies on accurate, well-organized data ...
18 Feb 2025
In an era where technology drives operational efficiency, Computerized Maintenance Management ...
14 Feb 2025
A Computerized Maintenance Management System (CMMS) is a key component of modern maintenance ...
13 Feb 2025
Introduction Maintenance management is the foundation of maintenance operations in industries ...
11 Feb 2025
Introduction A Computerized Maintenance Management System (CMMS) is software designed to help ...
7 Feb 2025