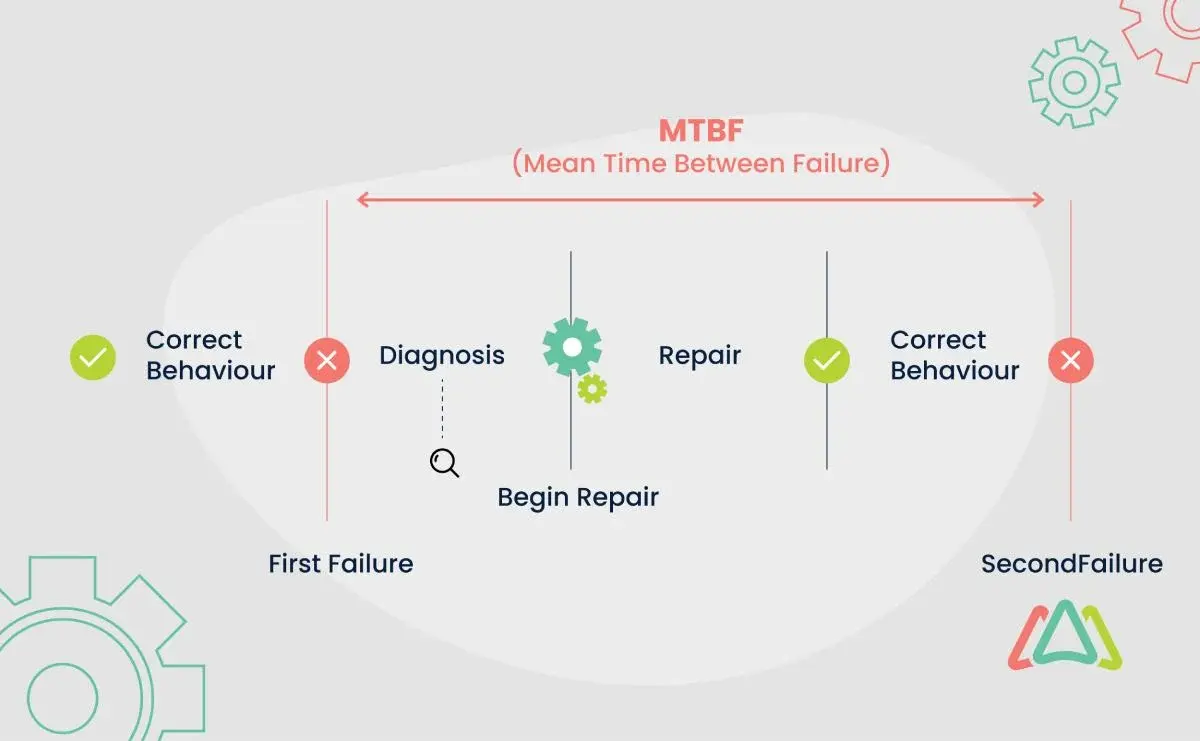
Mastering Mean Time Between Failures (MTBF) for Improved Equipment Reliability
Mean Time Between Failure (MTBF) Calculator
[Total Uptime (in hours) / # Number of breakdowns]
Our approach to managing work orders is radically different from other CMMS products in the market.
The maintenance team's primary objective is to ensure that equipment, machinery, and systems remain operational, contributing to overall productivity and minimizing costly downtime. For them to achieve this goal, it is important to grasp the concept of MTBF.
MTBF stands for Mean Time Between Failures. It is a reliability metric commonly used in engineering, manufacturing, and maintenance to predict the average time between failures of a system or component during operation. MTBF is typically measured in hours and provides an estimate of a system's reliability and expected performance.
MTBF measures equipment reliability. It shows how long one can reasonably expect a piece of equipment to operate without requiring maintenance or experiencing an unplanned failure. This metric plays an important role in helping maintenance professionals assess the health of their assets and make informed decisions about maintenance management strategies.
MTBF vs. MTTR
To comprehend the significance of MTBF, it's important to differentiate it from Mean Time to Repair (MTTR).
- MTBF represents the average time a piece of equipment can operate before experiencing a failure. It focuses on the reliability of the equipment itself and gauges how often it's likely to fail.
- MTTR, on the other hand, stands for Mean Time to Repair, and it measures the average time it takes to repair a piece of equipment after a failure has occurred. MTTR is more concerned with how quickly you can restore functionality once a breakdown happens.
Consider two machines with identical MTBF values, where one has a significantly shorter MTTR. The one with the shorter MTTR has less downtime when it fails, leading to higher availability. In essence, MTBF and MTTR work in tandem to manage and improve reliability.
How MTBF Fits into the Bigger Picture of Reliability
Reliability is not a one-dimensional concept; it’s multifaceted, where MTBF is an important piece of the puzzle. MTBF focuses on the proactive aspect of reliability by predicting the time between failures. When integrated into a broader reliability management strategy, MTBF helps in the following ways:
1. Assessing Equipment Health
MTBF provides a baseline for evaluating the health of the assets. If the MTBF is consistently high, it's an indicator that the equipment is reliable. However, a declining MTBF signifies underlying issues that need attention.
2. Optimizing Maintenance Strategies
Maintenance managers can tailor their maintenance strategies by knowing the MTBF assets. Equipment with high MTBF might benefit from less frequent, but more comprehensive maintenance, while equipment with lower MTBF may require more frequent checks.
3. Financial Planning
Understanding MTBF assists in financial planning. It allows organizations to allocate resources efficiently for maintenance activities and budget to reduce potential downtime.
4. Risk Mitigation
In industries where equipment failures can have severe consequences (e.g., healthcare or aerospace), MTBF helps identify and mitigate risks. Proactively addressing equipment with lower MTBF values reduces the chances of critical failures.
How is MTBF Calculated?
MTBF is calculated by dividing the total operational time by the number of failures to determine, on average, how long the equipment can operate before a failure occurs.
MTBF= Total operational time / Number of failures
A higher MTBF value indicates greater reliability, while a lower value suggests that the equipment is more prone to failures and requires closer attention in terms of maintenance.
Variables:
- Total Operational Time: It represents the total time the equipment was in operation during the assessment period. Any scheduled maintenance or downtime needs to be accounted for in the calculations.
- Number of Failures: Counting the number of failures is straightforward. It involves documenting every instance where the equipment or system experiences a breakdown or failure during the operational period.
Note that MTBF calculations can be tailored to specific types of equipment, components, or systems within the organization. For complex systems with multiple components, MTBF can be calculated for each component and aggregated to determine the overall system's MTBF.
Calculate MTBF for your maintenance operation:
Mean Time Between Failure (MTBF) Calculator
[Total Uptime (in hours) / # Number of breakdowns]
Our approach to managing work orders is radically different from other CMMS products in the market.
Data Collection for MTBF
The following are steps for gathering failure data, and utilizing historical records and maintenance logs to calculate MTBF effectively.
1. Gathering Failure Data
The calculation of MTBF requires precise information about the failures or breakdowns that have occurred during the operational period of the equipment or system in question. Here's how to gather this critical data:
- Failure Documentation: Whenever a failure occurs, ensure it is properly documented. This documentation should include details such as the date and time of the failure, the nature of the failure (e.g., mechanical, electrical, software-related), and any relevant notes on the circumstances surrounding the failure.
- Failure Severity: Categorize failures based on their severity. Some failures might result in partial downtime or reduced functionality, while others might cause complete equipment shutdown. Understanding the impact of each failure allows for a more nuanced analysis.
- Frequency of Data Collection: Regularly collect data on failures. The frequency of data collection depends on the nature of your operations. For critical equipment, real-time monitoring might be necessary, while less critical assets might require periodic data collection.
- Consistency: Ensure consistency in data collection processes. Use standardized forms or digital tools to record failure data. This consistency facilitates the reliability of your MTBF calculations over time.
2. Using Historical Records and Maintenance Logs
Historical records and maintenance logs are goldmines for information for calculating MTBF. Here's how to leverage these records effectively:
- Maintenance Logs: Maintenance logs contain a wealth of information about the maintenance activities performed on equipment. They include details such as maintenance dates, types of maintenance (preventive, corrective), parts replaced, and the duration of maintenance tasks. This information helps in distinguishing between planned downtime (maintenance) and unplanned downtime (failures).
- Equipment Usage Records: Utilize records that track the operational hours of equipment. These records can be electronic (sensors, counters) or manual (operator logs). They provide the total operational time required for MTBF calculations.
- Failure Histories: Historical records of past failures allow one to accurately count the number of failures that occurred during a specific operational period. Multiple failures within a short time frame should not be counted as a single event.
- Data Management Tools: Consider using dedicated a Computerized Maintenance Management Systems (CMMS) or Enterprise Asset Management (EAM) software. These systems help centralize and organize historical maintenance and failure data, making it readily accessible for MTBF analysis.
MTBF Calculation Examples - Walkthrough of MTBF Calculation for Different Maintenance Scenarios
1. Manufacturing Industry
Consider a manufacturing company that relies heavily on a robotic assembly line for its production. The company operates 24 hours a day, seven days a week. Over the course of a year, the assembly line experiences a total of 10 failures that necessitate unscheduled maintenance.
Data Collection:
- Total Operational Time: The assembly line operates continuously, resulting in a total operational time of 8,760 hours in a year.
- Number of Failures: Throughout the year, there were 10 instances where the assembly line experienced failures requiring immediate attention.
MTBF Calculation:
MTBF = Total operational time / Number of failures
MTBF = 8,760 hours / 10 failures
MTBF = 876 hours per failure
Interpreting the Results:
- The MTBF value of 876 hours per failure for the assembly line indicates that, on average, the assembly line can operate for approximately 876 hours before encountering a failure requiring maintenance.
- This MTBF value suggests that the assembly line has moderate reliability. Maintenance managers can use this information to plan maintenance activities, ensuring that they occur proactively and don’t disrupt production for extended periods.
2. Healthcare Facilities
In healthcare facilities, MRI machines are vital for patient diagnostics and consist of several critical components, including magnets, radiofrequency (RF) systems, gradient coils, and computer systems. To assess the reliability of the MRI system as a whole, Mean Time Between Failure (MTBF) for each of these components will have to be calculated and then aggregated.
Data Collection:
- Total Operational Time: The MRI machine operates for 16 hours a day, resulting in a total operational time of 5,840 hours in a year.
- Number of Failures for Each Component: Throughout the year, there were following instances of failure:
- Magnet: 1 failure
- RF System: 2 failures
- Gradient Coils: 1 failure
- Computer System: 1 failure
MTBF Calculation for Each Component:
MTBF = Total operational time / Number of failures
MTBF (Magnet) = 5,840 hours / 1 failure = 5,840 hours per failure
MTBF (RF System) = 5,840 hours / 2 failures = 2,920 hours per failure
MTBF (Gradient Coils) = 5,840 hours / 1 failure = 5,840 hours per failure
MTBF (Computer System) = 5,840 hours / 1 failure = 5,840 hours per failure
Aggregated MTBF for the MRI System:
Use the mean as it accounts for components with varying MTBF values:
MTBF (MRI Machine) = 4/(MTBF (Magnet) + MTBF (RF System) + MTBF (Gradient Coils) + MTBF (Computer System))
MTBF (MRI Machine) ≅ 1,951 hours per failure
Interpreting the Results:
The MRI system exhibits moderate reliability. With an aggregated MTBF of 1,951 hours, it can operate for an average of approximately 1,951 hours before experiencing a failure that requires maintenance. While this suggests a reasonably reliable system, it also implies that maintenance should be planned proactively to avoid unexpected downtime.
Role of MTBF in Maintenance Management
1. Scheduling Maintenance Based on MTBF Analysis
Preventive maintenance is all about performing scheduled maintenance tasks to prevent failures and downtime. MTBF analysis plays an important role in determining when preventive maintenance should occur:
- Time-Based Scheduling: For equipment with a relatively consistent MTBF, maintenance can be scheduled at intervals just before the expected MTBF. This minimizes the risk of failures and maximizes equipment uptime.
- Usage-Based Scheduling: For equipment with variable MTBF values due to varying operating conditions, usage-based scheduling can be employed. Maintenance is scheduled based on the number of operational hours, ensuring timely service when needed.
The proactive nature of preventive maintenance, informed by MTBF analysis, offers several advantages:
- Reduced Downtime: Preventive maintenance ensures that equipment is serviced before it reaches its failure point, reducing unscheduled downtime and minimizing disruptions to operations.
- Longer Asset Lifespan: Regular maintenance, guided by MTBF insights, extends the lifespan of equipment, reducing the need for premature replacements and cost savings.
- Improved Safety and Compliance: Preventive maintenance helps ensure that equipment complies with safety standards and regulatory requirements, mitigating risks associated with failures.
2. Optimizing Resource Allocation with MTBF Insights
Efficient resource allocation is the cornerstone of effective maintenance management. MTBF insights facilitate resource optimization by:
- Right-Sizing Maintenance Teams: Based on the expected frequency of failures (MTBF), maintenance teams can be staffed accordingly. Equipment with shorter MTBF values may require more frequent attention.
- Inventory Management: MTBF data helps decisions related to inventory management. Maintenance managers can stock spare parts and materials based on the likelihood of failures, minimizing storage costs while reducing wait times and expensive rush orders.
MTBF-driven resource allocation helps in:
- Minimizing Downtime: By allocating resources proactively based on MTBF, maintenance teams can perform maintenance during planned downtime, reducing the impact on overall operations.
- Budget Optimization: Efficient resource allocation guided by MTBF ensures that maintenance budgets are used effectively. Resources are allocated where they are needed most, preventing unnecessary expenditures such as overtime pay.
Overcoming Challenges in MTBF Analysis
MTBF’s effective application comes with its own set of challenges. The following are key challenges faced when analyzing MTBF and the ways to overcome them:
1. Overcoming Limitations in Data Collection
MTBF analysis heavily relies on historical data, making data collection an important but challenging piece. Some common hurdles include:
- Sparse Data: In cases where failures are infrequent, it can be challenging to gather sufficient data points for accurate MTBF calculations. To overcome this, consider extending data collection periods or pooling data from similar equipment.
- Incomplete Records: Maintenance logs may lack detailed information about failures, making it difficult to categorize them accurately. Regularly train maintenance personnel on the importance of thorough record-keeping to address this issue.
The accuracy of MTBF analysis depends on the quality of failure data:
- Misclassified Failures: Incorrectly identifying the root cause of failures can skew MTBF calculations. Ensure that failures are correctly categorized (e.g., distinguishing between software and hardware failures) to obtain accurate insights.
- Hidden Failures: Failures that go unnoticed or unreported can lead to low MTBF values. Implement robust reporting mechanisms and encourage personnel to report even minor issues.
2. Complex Systems
In complex environments where systems are interconnected, MTBF analysis becomes more intricate:
- Identifying Dependencies: Understand the dependencies between different components or subsystems within a complex system. An isolated MTBF calculation may not capture the ripple effects of failures on interconnected systems.
- Fault Propagation: Consider how a failure in one part of the system can propagate to other areas. Use fault tree analysis or similar techniques to model and analyze these scenarios.
To address complexities in interconnected systems:
- System-Level MTBF: Instead of analyzing individual components, calculate the MTBF at the system level, taking into account dependencies and fault propagation.
- Simulations: Use simulation tools to model the behavior of complex systems under various failure scenarios. This provides a more comprehensive view of system reliability.
Improving MTBF
Improving MTBF requires a multifaceted approach that spans various aspects of maintenance operations. The following are key strategies to improve MTBF:
1. Improving Equipment Reliability
Upgrading equipment and components can significantly improve MTBF:
- Advanced Technology: Consider replacing older equipment with newer models featuring advanced technology. Modern equipment often comes with enhanced reliability features, including more reliable components and parts, and manufacturing processes.
- Predictive Maintenance Capabilities: Look for equipment that includes predictive maintenance features, such as built-in sensors and diagnostics. These features can provide early warnings of potential failures, allowing for earlier intervention.
Redundancy can be a valuable strategy for ensuring continuous operation of critical assets:
- Redundant Systems: Design critical systems with redundancy, where backup components or systems can take over seamlessly in the event of a failure. This approach minimizes downtime and increases overall reliability.
- Failover Mechanisms: Implement automatic failover mechanisms that can switch to redundant systems without manual intervention. This reduces the Mean Time to Repair (MTTR) and helps maintain high MTBF values.
2. Maintenance Process Optimization
Efficient maintenance processes contribute to improved MTBF:
- Standardized Procedures: Develop standardized maintenance procedures and preventive maintenance checklists for equipment. This ensures consistency and reduces the risk of errors during maintenance tasks.
- Root Cause Analysis: Implement robust root cause analysis practices to determine why failures occur. Addressing underlying issues rather than just symptoms leads to higher MTBF values.
3. Data Analytics and Predictive Maintenance
Data analytics and artificial intelligence are powerful tools for predicting and preventing failures:
- Predictive Analytics: Implement predictive maintenance that helps analyze historical and real-time data to forecast when equipment is likely to fail. These models enable proactive maintenance planning. Use historical failure data to train machine learning models. These models can predict failures based on current conditions, allowing for preventive actions.
- Condition Monitoring: Use AI-driven condition monitoring techniques that continuously assess equipment health. Advanced algorithms can detect anomalies in equipment behavior, facilitating early intervention. Go beyond prediction by implementing prescriptive maintenance strategies. These strategies not only forecast failures but also recommend specific actions to prevent them.
Leveraging CMMS to Improve MTBF
CMMS software empowers maintenance teams with the tools and data needed to enhance Mean Time Between Failures (MTBF). Here are some ways organizations can leverage CMMS to improve MTBF:
1. Optimize Asset Lifespan
CMMS allows for historical tracking of asset maintenance history, enabling organizations to make informed decisions about equipment replacements or upgrades. This extends asset lifespan and improves MTBF.
Read our article to learn more about the best practices for effective asset lifecycle management.
2. Performance Analytics
A CMMS generates detailed reports on equipment performance, downtime, and maintenance activities. By analyzing this data, organizations can identify patterns, trends, and areas where MTBF can be improved.
3. Root Cause Analysis
When a failure occurs, a CMMS can aid in root cause analysis by providing a history of maintenance activities and equipment performance. Addressing root causes reduces the likelihood of recurring failures, thereby improving MTBF.
4. Condition-Based Maintenance
IoT-connected sensors continuously monitor equipment conditions. When deviations from normal behavior are detected, The CMMS triggers maintenance alerts, allowing for timely corrective action and improving MTBF.
5. Training Resources & Documentation
CMMS software can store training materials and resources for maintenance personnel. Well-trained teams are more effective at conducting preventive maintenance and addressing issues that could affect MTBF. CMMS software can also document maintenance procedures and best practices. This ensures consistency in maintenance activities, reducing the risk of errors that might lead to failures.
CMMS software is a versatile tool for improving MTBF. By centralizing asset management, enabling preventive maintenance, providing data analytics capabilities, optimizing inventory management, and integrating with IoT devices, it empowers organizations to enhance equipment reliability, reduce downtime, and ultimately boost operational efficiency. Investing in a CMMS system can have a significant impact on an organization's ability to achieve its maintenance and reliability goals.
TABLE OF CONTENTS
Keep Reading
Ever find yourself checking into a luxury hotel and expecting a relaxing stay, only to find a ...
11 Apr 2025
Organizations are witnessing swift changes in the business environment and confronting a ...
8 Apr 2025
Last month, news outlets and the entire internet was abuzz with the return of NASA astronauts ...
3 Apr 2025
What comes first - CMMS or predictive maintenance? If your answer is either, it is correct. ...
28 Mar 2025
Artificial intelligence (AI) talk has become commonplace. Today, engaging in business-focused ...
27 Mar 2025
Imagine a world where machines predict, diagnose, and fix their issues before they fail. This ...
25 Mar 2025
A facility maintenance plan is at the core of a facility’s operations. This organized ...
21 Mar 2025
Think of managing your maintenance operations like managing a championship sports team. Just ...
21 Mar 2025
The maintenance sector is battling a severe talent shortage that threatens to undermine ...
7 Mar 2025
Manufacturing maintenance is the backbone of industrial efficiency, ensuring machines run ...
5 Mar 2025
No one likes playing a guessing game when equipment breaks down. Yet, maintenance teams often ...
4 Mar 2025
The size of the preventive maintenance software market is discussed in millions of dollars, ...
4 Mar 2025
The organizational structure and corporate hierarchy vary from company to company. Large ...
28 Feb 2025
Maintenance procedures are essential for ensuring the longevity and reliability of machinery ...
21 Feb 2025
Sustainability is no longer just a buzzword; it's a critical component of corporate social ...
20 Feb 2025
A Computerized Maintenance Management System (CMMS) relies on accurate, well-organized data ...
18 Feb 2025
In an era where technology drives operational efficiency, Computerized Maintenance Management ...
14 Feb 2025
A Computerized Maintenance Management System (CMMS) is a key component of modern maintenance ...
13 Feb 2025
Introduction Maintenance management is the foundation of maintenance operations in industries ...
11 Feb 2025
Introduction A Computerized Maintenance Management System (CMMS) is software designed to help ...
7 Feb 2025