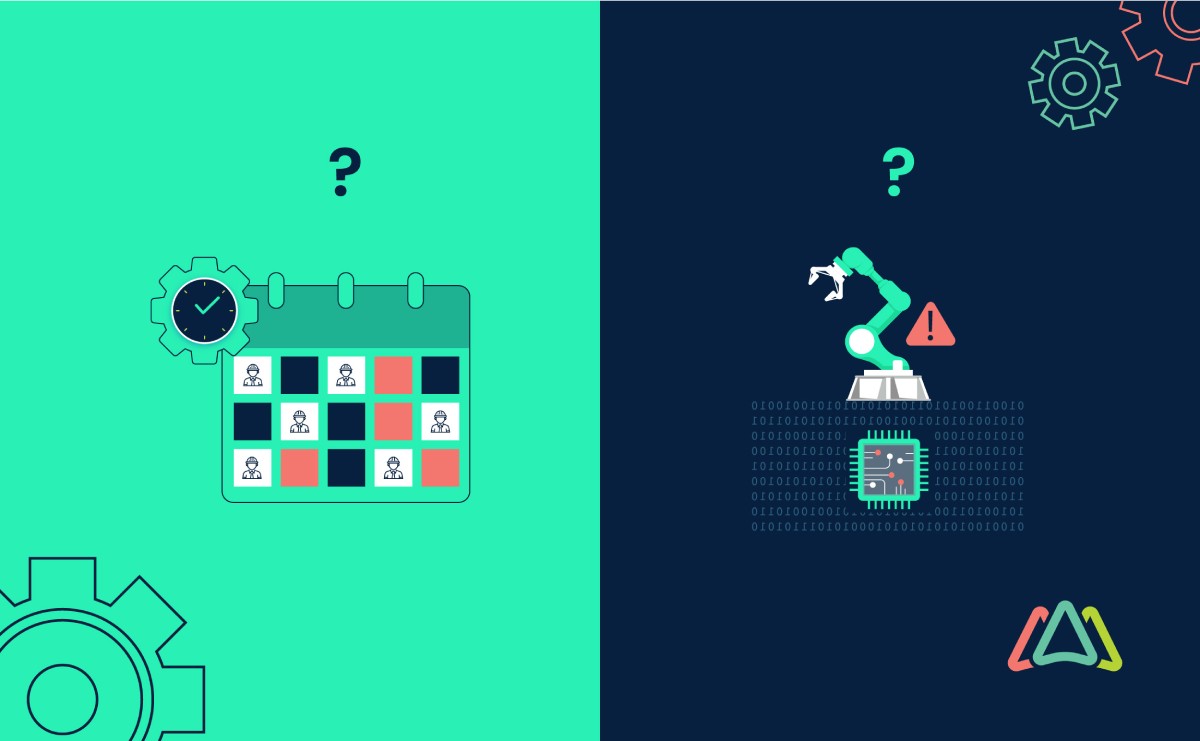
Preventive and Predictive Maintenance: Choosing the Best Maintenance Strategy
Maintenance is much more than just fixing or replacing what's broken; it is an essential business component that significantly impacts a company's operational efficiency, safety, and financial performance.
There are many approaches to determining a company’s maintenance management strategy; this article focuses on 2 common and effective strategies – Preventive Maintenance and Predictive Maintenance.
Preventive Maintenance refers to routine maintenance and inspections conducted to prevent equipment failures before they actually occur. Predictive Maintenance (PdM), however, involves continuously monitoring equipment performance to predict when maintenance might be required, thereby minimizing the risk of unexpected equipment breakdowns. PdM is a more recent strategy that has gained traction with maintenance professionals and managers. According to the State of Industrial Maintenance Report, about 41% of the businesses surveyed have integrated predictive maintenance and analytical tools into their operations to monitor their critical assets and proactively schedule maintenance tasks.
Choosing the right maintenance approach isn't just about keeping machines running; it's about optimizing processes, increasing efficiency, and maximizing profitability. A well-chosen and executed approach reduces downtime, prevents catastrophic failures, increases equipment life expectancy, and lowers maintenance costs.
What is Preventive Maintenance?
Preventive Maintenance involves planned maintenance tasks aimed at the prevention of breakdowns and failures. The primary goal is to prevent the failure of equipment before it occurs. It is designed to improve equipment reliability by through regular upkeep and maintenance of assets and replacing worn components before they actually fail.
At its core, Preventive Maintenance entails taking a proactive approach to managing equipment. It is a calendar-based or usage-based strategy, meaning maintenance is performed on a predetermined schedule (daily, weekly, monthly, etc.) or based on specific usage metrics (run-time hrs., mileage, etc.).
Preventive Maintenance involves regular inspections and routine work, similar to going for medical check-ups to catch potential health issues before they become serious. It involves tasks such as cleaning, lubrication, adjustments, repairs, and parts replacements that are performed regularly to help prevent sudden equipment breakdowns.
The key characteristic of Preventive Maintenance is its proactive nature. Instead of waiting for equipment to fail, the goal is to maintain it regularly so that it doesn't fail in the first place. In essence, it is a risk-averse strategy that prioritizes consistency and reliability. One of the key advantages of adopting a preventive maintenance strategy is that maintenance is planned. This simplifies resource planning where a reactive approach requires having people staffed ready to deal with incidents as they come. Repairs can be costly and interrupt production.
What is Predictive Maintenance?
Predictive Maintenance uses condition-monitoring to track the performance and condition of equipment. It detects possible defects and abnormalities allowing maintenance techs to address them before they result in failure. This approach is more targeted compared to preventive maintenance, as it seeks to detect or predict when maintenance should be performed instead of on a routine schedule.
Predictive Maintenance is a strategy that’s further along with respect to being proactive. Rather than following a set schedule or usage metrics for maintenance activities, PdM relies on the actual condition of the equipment to determine what needs to be done.
This approach is based on condition-monitoring data. It uses various monitoring technologies like sensors to track equipment performance and predict future failures. Measures include vibration analysis, infrared thermography, oil analysis among others that allow technicians and operators to spot abnormalities that point to potential issues in the future.
Predictive Maintenance is inherently data-driven. It leverages advanced technology and machine learning algorithms to analyze data and predict equipment failures before they happen. This approach enables businesses to act only when maintenance is actually necessary, saving time and resources when compared with preventive maintenance.
5 Key Differences between Preventive and Predictive Maintenance
1. Maintenance Planning and Scheduling
Preventive maintenance relies on predetermined schedules or usage metrics. Schedules are time-based (daily, weekly, monthly, seasonally, etc.), while PMs based on usage metrics trigger maintenance tasks from meter readings (run-time hrs., mileage, etc.) Maintenance activities are set regardless of the condition of the equipment, meaning maintenance occurs at regular intervals or after a certain amount of use.
In contrast, with PdM, maintenance activities are based on the actual condition of the equipment, determined by continuous monitoring and analysis of equipment data via sensors. Maintenance is performed only when indicators show that equipment performance is decreasing or that failure is imminent.
2. Maintenance Execution
Preventive maintenance follows a "better safe than sorry" approach where routine checks and replacements are conducted to avoid potential failures. This strategy involves regular routine maintenance tasks and planned downtime to perform the work.
Predictive maintenance, on the other hand, is a "just-in-time" approach where condition-monitoring technologies identify when parts or equipment are nearing failure, and maintenance activities only occur when needed. This approach aims to minimize downtime by performing maintenance as required, not on a set schedule. Maintenance tasks are performed when the asset data indicates a potential failure or when machine learning algorithms forecast an impending issue.
3. Role of Technology and Data
Preventive maintenance doesn’t require advanced technology. It might involve manual inspections and basic tools to perform maintenance tasks. Some businesses with a small amount of assets can get away with a spreadsheet, Outlook and even paper and pen. As the number of assets, work orders and the criticality of the assets increase, organizations implement preventive maintenance software which streamlines processes, automates alerts, enhances data accuracy, and delivers accurate reports on preventive maintenance performance.
Implementing a predictive maintenance strategy requires more advanced technology. It uses condition-monitoring tools like IoT sensors and machine learning to gather data which is integrated with a computerized maintenance management system (CMMS) or enterprise asset management (EAM) application. Software applications, integration through APIs and sensors are commonplace with predictive maintenance.
4. Risk Management
Both preventive and predictive maintenance strategies aim to mitigate the risk of unexpected equipment failure, but they differ in how they accomplish this.
Preventive maintenance reduces risk by regularly maintaining equipment and replacing parts to avoid sudden failures.
Predictive maintenance attempts to mitigate risk by continuously monitoring equipment performance and predicting future failures, allowing for timely maintenance only when required. Predictive maintenance at times offers better risk reduction, as it allows for more precise targeting of maintenance activities based on actual equipment condition.
5. Flexibility and Adaptability
Compared to predictive maintenance, preventive maintenance is less adaptable to changing equipment conditions. It follows predefined schedules and intervals, which may not account for sudden changes or variations in equipment performance.
Predictive maintenance is adaptable to real-time equipment variations. By continuously monitoring equipment and analyzing data, users can respond and adapt to changing conditions, adjusting maintenance activities accordingly.
Understanding these key differences between preventive and predictive maintenance helps businesses make informed decisions about the most suitable approach for their specific equipment, budget, and maintenance goals.
Benefits and Drawbacks of Preventive and Predictive Maintenance
Both approaches have advantages and limitations. Understanding the pros and cons in the context of the organization’s available resources and industry requirements is important when evaluating which strategy is best for your business.
Preventive Maintenance |
Predictive Maintenance |
Benefits |
|
Reduced Downtime: Regular maintenance helps avoid unexpected equipment failure and reduces unplanned downtime. |
Reduced Downtime: Predictive maintenance like preventive maintenance reduces unplanned downtime and equipment failure. It also reduces planned downtime, because maintenance tasks are only performed when assets require it. |
Cost-Effective: Preventive maintenance can be implemented at a lower cost as it does not require advanced technologies. |
Long-term Cost Savings: Despite the initial investment in technology, predictive maintenance can lead to significant savings in the long run due to optimized maintenance tasks, less scheduled downtime and reduced equipment failure. |
Prolonged Equipment Lifespan: By addressing asset wear and tear, preventive maintenance extends equipment life. |
Optimized Maintenance Tasks: Since maintenance is conducted based on actual equipment conditions, predictive maintenance helps avoid unnecessary tasks, optimizing resources. |
Ease of Planning: With pre-set schedules, planning for preventive maintenance is typically straightforward and predictable. |
|
Drawbacks |
|
Potential Over-Maintenance: Since preventive maintenance follows a set schedule, there is a risk of conducting unnecessary maintenance on equipment that is functioning well. Companies should consider using preventive maintenance on critical assets and exclude non-critical ones. |
High Initial Investment: Setting up a predictive maintenance system requires investment in technology and training, which may be substantial. Experts and consultants are often involved in implementations. |
Inefficiency: Preventive maintenance can be inefficient, especially when maintaining equipment that does not need any attention, thereby wasting resources. |
Complex Implementation: Implementing predictive maintenance requires a clear understanding of the data collected and the ability to interpret it accurately, making it more complex than preventive maintenance. Expertise is required. |
Unpredictable Failures: Even with a thorough preventive maintenance plan, unexpected failures can still occur. |
Dependency on Technology: Since predictive maintenance relies heavily on advanced technology, any tech-related issues could disrupt operations. |
10 Key Considerations for Choosing the Best Maintenance Strategy for Businesses
The following factors should be considered when evaluating preventive and predictive maintenance strategies. The decision on which strategy to adopt comes with costs and impacts employees and business operations as a whole.
1. Size and Scale of Operations
For businesses with a limited number of machines or assets, a preventive maintenance strategy may be sufficient and more cost-effective. However, larger operations with numerous high-value assets may benefit from a predictive maintenance strategy, which can optimize maintenance activities and extend equipment life, resulting in substantial savings over time.
2. Industry and Regulatory Standards
Take into account industry-specific regulations and standards that may dictate the maintenance approach to follow. Industries such as aviation or nuclear power, where equipment failures can have catastrophic consequences, often prioritize preventive maintenance.
For instance in the aviation industry, Federal Aviation Administration (FAA) oversees civil aviation in the United States and establishes regulatory standards for maintenance practices through various documents, including the Code of Federal Regulations (CFRs).
CFR Part 43 outlines the requirements for maintenance, preventive maintenance, and alterations of aircraft, engines, and other aviation components. It mandates that aircraft operators and maintenance providers adhere to specific maintenance intervals and tasks prescribed by the manufacturer or FAA-approved maintenance program.
Similarly, in the United States, Nuclear Regulatory Commission (NRC) is responsible for regulating the nuclear power industry and establishing standards for safety and maintenance.
Regulation 10 CFR Part 50 pertains to the operation and maintenance of nuclear power plants. Section 50.65 addresses the requirements for maintenance and the establishment of maintenance rule programs. It emphasizes the need for a systematic and integrated approach to maintenance, including preventive maintenance, to ensure plant safety and reliability.
These are examples of industry-specific regulations and standards in the United States. Other countries may have their own corresponding regulatory bodies and standards and it is important to consult the relevant regulatory authorities and standards applicable to the specific region for comprehensive information on preventive or predictive maintenance requirements.
Both preventive maintenance and predictive maintenance are important practices for ensuring safe and reliable operations in the above mentioned industries. While preventive maintenance is typically mandated by industry and regulatory standards, predictive maintenance is considered an advanced and beneficial approach.
3. Technology and Available Resources
Assess the availability of advanced technology and necessary resources for implementing predictive maintenance. Predictive maintenance relies on technologies like IoT sensors and data analysis software, as well as skilled personnel to interpret the data. If these resources are not readily available or if costs are prohibitive, preventive maintenance might be a more feasible option.
4. Organizational Goals and Objectives
Align your maintenance strategy with the organization’s short and long-term business goals and objectives. If the focus is on minimizing short-term costs and you operate in a relatively low-risk environment, preventive maintenance might be the better option. However, if the goal is to optimize operations, maximize uptime, and optimize long term efficiencies, investing in predictive maintenance may be the right strategic move.
5. Cost-Benefit Analysis
Perform a cost-benefit analysis to evaluate the financial implications of each maintenance approach. While preventive maintenance requires a smaller initial investment, predictive maintenance has the potential to offer larger long-term savings and efficiency gains. Weighing the costs against the anticipated benefits can help determine which approach makes the most financial sense for the organization.
6. Impact on Business Continuity and Sustainability
Assess the potential impact of each maintenance approach on your organization's continuity and sustainability. A well-chosen approach can minimize downtime, enhance safety measures, and promote sustainable practices by extending the lifespan of equipment and optimizing resource utilization. By choosing maintenance strategies that prioritize continuity and sustainability, businesses can ensure smooth operations, reduce disruptions, and minimize their environmental footprint.
7. Skill and Availability of Expertise
Evaluate the availability of skilled maintenance professionals and experts who can effectively implement and manage your chosen maintenance strategy. Predictive maintenance requires expertise in data analysis and interpretation, while preventive maintenance may require skilled technicians for regular inspections and maintenance tasks. Assessing the availability of qualified personnel can help determine the feasibility and effectiveness of each approach.
8. Scalability and Flexibility
Assess the scalability and flexibility of each maintenance strategy to accommodate future growth and organizational changes. Predictive maintenance, with its data-driven approach, can be more adaptable to evolving equipment conditions, allowing for proactive adjustments to maintenance plans. Preventive maintenance, although less flexible, can still be effective if implemented with scalability in mind, allowing for adjustments based on equipment additions or changes in operational requirements.
9. Data Availability and Quality
Consider the availability and quality of data necessary for predictive maintenance. Accurate and reliable data are crucial for the success of predictive maintenance strategies. If the organization lacks robust data collection processes or data quality is a concern, preventive maintenance may be a more practical choice until data-related challenges are addressed.
10. Risk Management
Assess the level of risk associated with equipment failures in the industry and the potential consequences for the organization. Predictive maintenance, with its focus on early detection and prevention, helps mitigate risks and avoid costly breakdowns. On the other hand, preventive maintenance can provide a sense of reassurance and compliance with maintenance schedules, minimizing the risk of equipment failures due to neglect or oversight.
Hybrid Maintenance Strategy
When it comes to maintenance, it is never “one or the other”. Organizations can adopt hybrid maintenance strategies that leverage both preventive and predictive maintenance approaches to achieve optimal results. Here's how it can be beneficial:
- Critical Equipment: For critical equipment that is vital to business operations or poses significant risks in case of failure, businesses can implement predictive maintenance. This involves continuous monitoring, data analysis, and early detection of potential failures. By proactively addressing issues before they escalate, businesses can minimize downtime, reduce costly repairs, and ensure maximum uptime.
- Less Critical Equipment: For equipment with lower criticality or predictable failure patterns, businesses can utilize preventive maintenance. This involves scheduled maintenance tasks and regular inspections to prevent failures that maximize equipment reliability. By following established maintenance intervals, businesses can maintain the equipment's operational efficiency, extend its lifespan, and reduce the likelihood of unexpected breakdowns.
By combining these approaches, businesses can optimize their maintenance efforts, allocate resources efficiently, minimize downtime, and prioritize maintenance activities based on criticality and risk.
Preventive and predictive maintenance strategies serve different purposes and come with their unique set of advantages and disadvantages. Preventive maintenance, with its scheduled checks and balances, is a cost-effective solution for small businesses or those with less complex equipment. Predictive maintenance, on the other hand, though it requires a higher initial investment, provides substantial long-term benefits, particularly for larger businesses with more complex and high-value assets.
The choice between these two approaches should be driven by a clear understanding of the organization’s needs, resources, and long-term goals. The ultimate aim is to enhance operational efficiency, reduce downtime, and achieve a higher return on investment.
TABLE OF CONTENTS
Keep Reading
Ever find yourself checking into a luxury hotel and expecting a relaxing stay, only to find a ...
11 Apr 2025
Organizations are witnessing swift changes in the business environment and confronting a ...
8 Apr 2025
Last month, news outlets and the entire internet was abuzz with the return of NASA astronauts ...
3 Apr 2025
What comes first - CMMS or predictive maintenance? If your answer is either, it is correct. ...
28 Mar 2025
Artificial intelligence (AI) talk has become commonplace. Today, engaging in business-focused ...
27 Mar 2025
Imagine a world where machines predict, diagnose, and fix their issues before they fail. This ...
25 Mar 2025
A facility maintenance plan is at the core of a facility’s operations. This organized ...
21 Mar 2025
Think of managing your maintenance operations like managing a championship sports team. Just ...
21 Mar 2025
The maintenance sector is battling a severe talent shortage that threatens to undermine ...
7 Mar 2025
Manufacturing maintenance is the backbone of industrial efficiency, ensuring machines run ...
5 Mar 2025
No one likes playing a guessing game when equipment breaks down. Yet, maintenance teams often ...
4 Mar 2025
The size of the preventive maintenance software market is discussed in millions of dollars, ...
4 Mar 2025
The organizational structure and corporate hierarchy vary from company to company. Large ...
28 Feb 2025
Maintenance procedures are essential for ensuring the longevity and reliability of machinery ...
21 Feb 2025
Sustainability is no longer just a buzzword; it's a critical component of corporate social ...
20 Feb 2025
A Computerized Maintenance Management System (CMMS) relies on accurate, well-organized data ...
18 Feb 2025
In an era where technology drives operational efficiency, Computerized Maintenance Management ...
14 Feb 2025
A Computerized Maintenance Management System (CMMS) is a key component of modern maintenance ...
13 Feb 2025
Introduction Maintenance management is the foundation of maintenance operations in industries ...
11 Feb 2025
Introduction A Computerized Maintenance Management System (CMMS) is software designed to help ...
7 Feb 2025