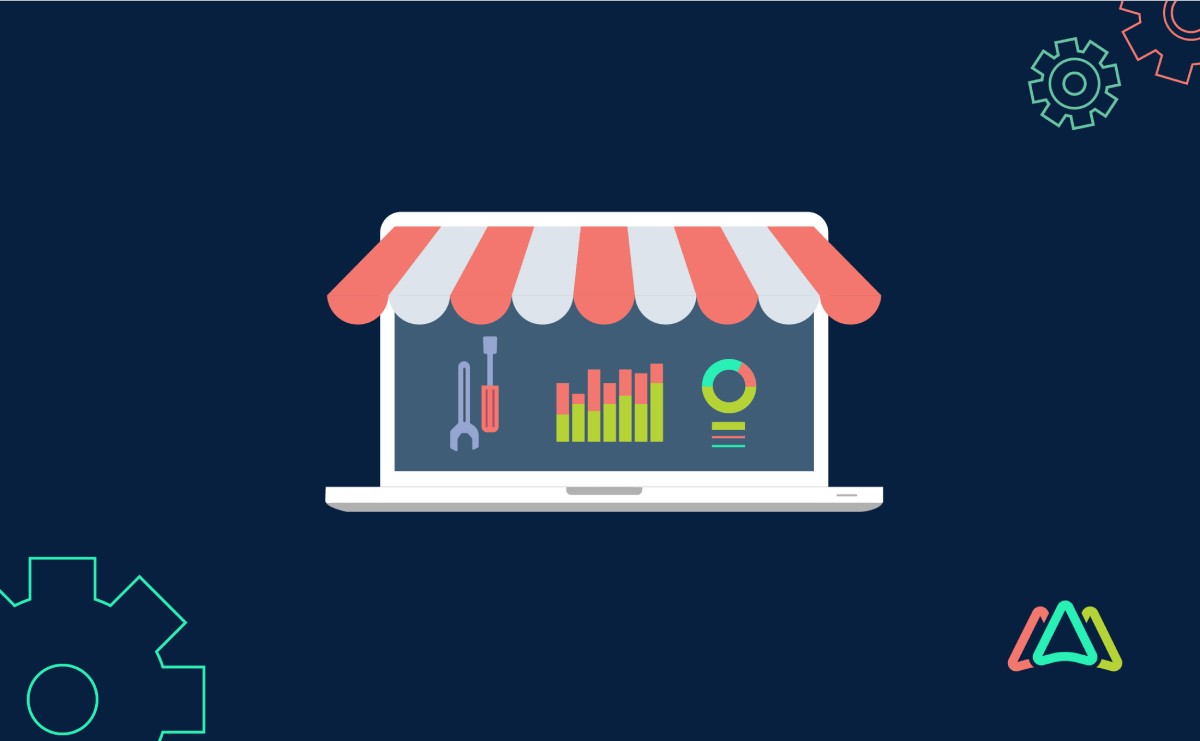
Step-by-Step Transition: Introducing CMMS to Small Businesses
For small businesses, where resources are often limited and every operational facet must be finely tuned, the adoption of CMMS software can be a game-changer. CMMS serves as a powerful platform to manage and monitor maintenance activities, asset life cycles, and work orders. It empowers businesses to move beyond the limitations of traditional, manual methods by digitizing, centralizing and automating maintenance processes. By transitioning to a CMMS software, small businesses can significantly improve their maintenance operations, leading to increased reliability, reduced downtime, and enhanced overall operational efficiency.
This article aims to guide small business owners through the step-by-step process of transitioning from traditional maintenance management methods, often reliant on spreadsheets, pen and paper, and manual tracking, to a more advanced and efficient CMMS software. Recognizing the unique challenges faced by small businesses, we will explore how adopting CMMS can revolutionize maintenance practices, providing a roadmap for a seamless and successful implementation.
Challenges in Traditional Maintenance Management
Traditional maintenance management methods often pose significant challenges that can impede growth and profitability. Identifying and addressing these challenges is essential for paving the way toward a more streamlined and efficient approach to maintenance. Here are some common hurdles faced by small businesses:
1. Reactive Maintenance
Small businesses frequently find themselves trapped in a cycle of reactive maintenance, addressing issues only when they arise. This approach leads to unplanned downtime, emergency repairs, and increased operational costs. When critical assets breakdown, businesses need to call in specialized vendors, or pay staff overtime to repair. Parts that required have to be rush ordered which adds to costs. Furthermore, every minute critical assets are not available, costs businesses money. The lack of a proactive strategy can hinder overall productivity, increase costs and strain resources.
2. Lack of Organization and Documentation
Manual maintenance management, relying on spreadsheets, pen and paper, using sticky notes, and other disparate “documentation systems”, results in disorganization. Critical maintenance data is scattered, making it challenging to access and analyze. This disorganization leads to inefficiencies, errors, and difficulties in tracking historical maintenance information.
3. Inefficient Resource Allocation
Without a centralized system for managing maintenance tasks, small businesses often struggle with allocating resources optimally. Manpower, equipment, and materials may be underutilized or overextended, leading to inefficiencies and avoidable costs.
Benefits of CMMS Software for SMBs
To address the challenges inherent in traditional maintenance management, small businesses can leverage the numerous benefits offered by a Computerized Maintenance Management System (CMMS).
1. Improved Asset Management
CMMS allows small businesses to gain precise control over their assets. From tracking equipment performance to scheduling preventive maintenance, CMMS ensures that assets are well-maintained and optimized for longevity. This leads to increased reliability, reduced downtime, and a longer lifespan for important business assets. A study by the Aberdeen Group found that organizations using CMMS software for preventive maintenance experienced a 32% improvement in equipment reliability. (Source: Aberdeen Group, "Enterprise Asset Management: A Comprehensive Approach," 2017)
Another study by the ARC Advisory Group found that organizations with CMMS software reported an average 10-15% increase in asset life expectancy. (Source: ARC Advisory Group, "Maintenance Management Systems for Process Industries," 2017)
2. Increased Maintenance Efficiency
The automation capabilities of CMMS streamline maintenance processes, reducing manual intervention and the likelihood of errors. By automating work orders, scheduling preventive maintenance, and managing inventory, small businesses can enhance their maintenance efficiency. This not only saves time but also ensures that tasks are completed with precision.
3. Cost Savings
One of the most compelling reasons for small businesses to adopt CMMS is the potential for significant cost savings. By minimizing unplanned downtime, reducing emergency repairs, and optimizing inventory levels, CMMS contributes to overall cost efficiency. Small businesses can allocate their financial resources more strategically, promoting sustainable growth. In its 2018 study, the U.S. Department of Energy found that preventive maintenance programs, when supported by CMMS, can lead to cost savings of up to 12-18% compared to reactive maintenance. (U.S. Department of Energy, "Effective Implementation of Planned Maintenance Practices," 2018)
4. Enhanced Data and Reporting
CMMS systems generate detailed reports and analytics, providing small businesses with valuable insights into their maintenance performance. This data-driven approach facilitates informed decision-making, enabling businesses to identify trends, predict maintenance needs, and continuously improve their operational processes.
Pre-Implementation Preparation
Small businesses with limited resources and small maintenance teams often face unique challenges in maintaining their operations efficiently. Many rely on rudimentary methods like spreadsheets and pen-and-paper systems to track and manage maintenance activities. As these businesses consider transitioning to a CMMS, having a structured approach and game plan is necessary.
1. Assess Current Maintenance Practices
1.1 Identify Pain Points
Small maintenance teams using manual methods often encounter specific pain points that hinder their effectiveness. These may include difficulties in tracking work orders, identifying equipment issues, or managing preventive maintenance schedules. Identifying these pain points is the first important step in understanding where improvements are needed.
Example: Are equipment breakdowns leading to unplanned downtime? Is there a challenge in coordinating maintenance tasks due to a lack of centralized information?
1.2 Evaluate Existing Processes
Evaluate the current maintenance processes. This involves understanding how work orders are created and tracked, how preventive maintenance tasks are scheduled, and how information is communicated within the team. Documenting these processes provides a clear picture of the existing workflow.
Example: Are work orders written on paper and manually assigned? Is there a standardized system for recording equipment maintenance history?
2. Establish Clear Objectives and Goals
2.1 Define Key Performance Indicators (KPIs)
Small businesses should establish measurable maintenance KPIs that align with their maintenance goals. These metrics can include reduced downtime, increased equipment reliability, faster response times to maintenance requests, and improved overall operational efficiency. Defining KPIs provides a benchmark for success.
Example: Decreasing unplanned downtime by 20%, improve response time to maintenance requests by 15%, and achieve 90% completion of preventive maintenance tasks.
2.2 Align with Business Objectives
Ensure that the objectives of implementing a CMMS align with the broader business goals. Whether it's reducing operational costs, improving customer satisfaction, or expanding operations, the integration of CMMS should contribute directly to the overall success of the business.
Example: If the business objective is to expand operations, the CMMS implementation should support this goal by ensuring efficient maintenance of existing equipment and minimizing disruptions.
Selecting the Right CMMS
The right CMMS can enhance efficiency, reduce downtime, and provide a more organized approach to maintenance operations.
1. Research Available CMMS Solutions
1.1 Cloud-Based vs. On-Premise
Small businesses should carefully consider whether a cloud-based or on-premise CMMS is more suitable for their operations. Cloud-based solutions offer accessibility from anywhere with an internet connection, while on-premise solutions provide greater control over data but may require more upfront infrastructure investment. Cloud-based solutions today are very secure, require no maintenance, are easy to deploy and have much lower upfront costs. On-prem might be better suited for businesses in specific industries like defense where they handle very sensitive data.
Example: A small business with a dispersed maintenance team might find a cloud-based CMMS more convenient, allowing technicians to access information on the go.
1.2 Scalability and Customization Options
Assess the scalability and customization features of potential CMMS solutions. Small businesses need a system that can grow with them and be tailored to their unique requirements. Look for systems that allow customization without overwhelming complexity.
Example: A small manufacturing business might need a CMMS that can adapt to changing production lines and equipment without requiring extensive reconfiguration.
1.3 User-Friendly Interface
Given the size of the maintenance team, a user-friendly interface is important for quick adoption and minimal training requirements. Look for a user-friendly CMMS software with an intuitive design that allows technicians, who may not be tech savvy, to navigate and utilize the system easily.
Example: A small business with a diverse team of maintenance technicians may benefit from a CMMS with a straightforward interface to ensure widespread usability.
2. Evaluate Costs
2.1 Upfront Costs
Small businesses often operate on tight budgets, so it's essential to consider upfront costs when selecting a CMMS. This includes software licensing fees, implementation costs, and any required hardware. Finding a solution that aligns with the budget is essential for a successful implementation.
Example: A small business with a fixed budget may prioritize a cloud-based CMMS with lower upfront costs over an on-premise solution requiring substantial initial investment. Many SaaS subscriptions offer monthly payments, and in some cases no long term contract.
2.2 Ongoing Maintenance and Support Fees
Beyond upfront costs, evaluate the ongoing maintenance and support fees associated with each CMMS option. Consider the level of support offered and the responsiveness of the provider, ensuring that the chosen system remains reliable and well-supported.
Example: A small business may prioritize a CMMS provider with responsive customer support and regular updates to address any issues that may arise.
2.3 Return on Investment (ROI)
If not obvious at first, conduct an ROI analysis to understand the long-term benefits of each CMMS option. Consider the potential savings in terms of reduced downtime, improved maintenance efficiency, and overall cost savings. Understanding the expected return on investment is essential for making an informed decision. CMMS providers can help you create the ROI case.
Example: If a small business estimates a 15% reduction in downtime and a 20% increase in maintenance efficiency with a particular CMMS, the ROI analysis can quantify the financial impact.
Building a Supportive Team
Implementing a CMMS in a small business with a small maintenance team is not just about introducing new technology; it's about fostering a collaborative and supportive environment to ensure a successful transition from manual methods.
1. Appoint a CMMS Implementation Team
1.1 Involve Key Stakeholders
Identify and involve key stakeholders from different departments to ensure diverse perspectives are considered. In a small business context, this may include maintenance technicians, IT personnel, and relevant decision-makers. The involvement of frontline workers is essential, as they can provide valuable insights into day-to-day operational needs.
Example: In a small manufacturing business, involving maintenance technicians, production managers, and IT specialists would ensure comprehensive input.
1.2 Assign Roles and Responsibilities
Clearly define roles and responsibilities within the CMMS implementation team. Assign individuals who are not only knowledgeable about maintenance processes but also possess the communication skills needed to facilitate a smooth transition. Ensure that each team member understands their specific contributions to the implementation process.
Example: Designate a team member to oversee data migration, another for user training, and a point of contact for ongoing support and issue resolution.
2. Conduct Training Programs
2.1 Train End Users
Small maintenance teams relying on manual methods may have varying levels of familiarity with digital tools. Implementing a training program is important to ensure that end users understand how to navigate and utilize the CMMS effectively. Training sessions should be tailored to the specific needs of the small business and the proficiency levels of the team members.
Example: Schedule web-conference training sessions with the CMMS provider demonstrating how to create and manage work orders, use preventive maintenance features, and leverage the reporting capabilities of the CMMS. Also get familiar with the providers online documentation (videos, knowledge base, webinars) and ticketing process.
2.2 Provide Continuous Support and Feedback
Recognize that the learning curve for a new system may require ongoing support. Establish a feedback loop to address any challenges or questions that arise during the initial stages of implementation. Encourage open communication and create channels for users to provide feedback, ensuring that the team feels supported throughout the transition.
Example: Set up regular check-ins or a dedicated support channel where team members can share their experiences, ask questions, and receive timely assistance.
By understanding the challenges of traditional maintenance management and embracing the benefits of CMMS, small businesses can position themselves for long-term success. The journey towards efficient, proactive maintenance begins with recognizing the need for change and leveraging technology to overcome the limitations of outdated practices.
TABLE OF CONTENTS
Keep Reading
Ever find yourself checking into a luxury hotel and expecting a relaxing stay, only to find a ...
11 Apr 2025
Organizations are witnessing swift changes in the business environment and confronting a ...
8 Apr 2025
Last month, news outlets and the entire internet was abuzz with the return of NASA astronauts ...
3 Apr 2025
What comes first - CMMS or predictive maintenance? If your answer is either, it is correct. ...
28 Mar 2025
Artificial intelligence (AI) talk has become commonplace. Today, engaging in business-focused ...
27 Mar 2025
Imagine a world where machines predict, diagnose, and fix their issues before they fail. This ...
25 Mar 2025
A facility maintenance plan is at the core of a facility’s operations. This organized ...
21 Mar 2025
Think of managing your maintenance operations like managing a championship sports team. Just ...
21 Mar 2025
The maintenance sector is battling a severe talent shortage that threatens to undermine ...
7 Mar 2025
Manufacturing maintenance is the backbone of industrial efficiency, ensuring machines run ...
5 Mar 2025
No one likes playing a guessing game when equipment breaks down. Yet, maintenance teams often ...
4 Mar 2025
The size of the preventive maintenance software market is discussed in millions of dollars, ...
4 Mar 2025
The organizational structure and corporate hierarchy vary from company to company. Large ...
28 Feb 2025
Maintenance procedures are essential for ensuring the longevity and reliability of machinery ...
21 Feb 2025
Sustainability is no longer just a buzzword; it's a critical component of corporate social ...
20 Feb 2025
A Computerized Maintenance Management System (CMMS) relies on accurate, well-organized data ...
18 Feb 2025
In an era where technology drives operational efficiency, Computerized Maintenance Management ...
14 Feb 2025
A Computerized Maintenance Management System (CMMS) is a key component of modern maintenance ...
13 Feb 2025
Introduction Maintenance management is the foundation of maintenance operations in industries ...
11 Feb 2025
Introduction A Computerized Maintenance Management System (CMMS) is software designed to help ...
7 Feb 2025