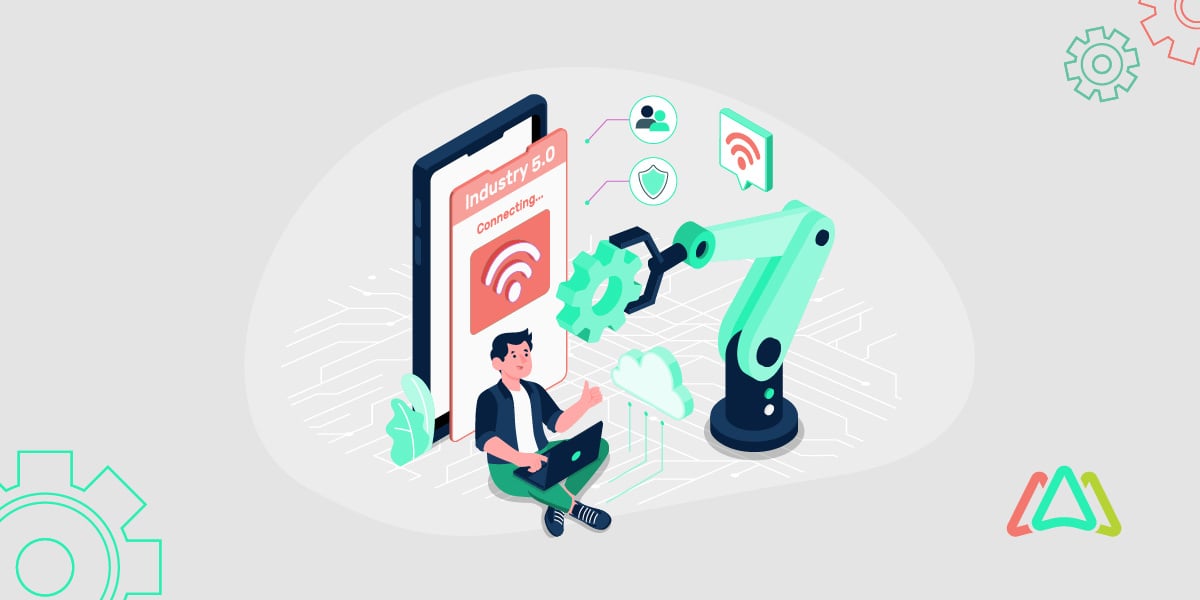
The Future of Autonomous Maintenance Systems
Imagine a world where machines predict, diagnose, and fix their issues before they fail. This will be the promise of Autonomous Maintenance Systems, a leap beyond traditional maintenance.
Industries started with reactive or preventive maintenance. Predictive maintenance, in the other hand, increased efficiency by analyzing the data to predict breakdowns, though it still remained a human process. However, today, industries like manufacturing, logistics, energy, and infrastructure are adopting autonomous systems that minimize human intervention.
This transformation, powered by AI, robotics, and the Industrial Internet of Things (IIoT), would allow machines to self-monitor, self-diagnose, and even self-repair. The result would be reduced downtime, minimal management costs, and increased efficiency.
As industries scale and their progress deepens, self-maintaining systems may no longer be futuristic. This is where autonomous maintenance systems come in; they're necessary for staying competitive in a rapidly evolving world.
The Structure of Autonomous Maintenance Systems
Autonomous maintenance uses innovative technology to keep machines running with little human effort. With AI, IoT, sensors, and data analysis, it monitors machines, spots problems early, and fixes minor issues automatically.
Thus, it helps reduce breakdowns, improve efficiency, and extend machine life, making it a big advantage in modern manufacturing.
AI-Driven Decision Making
In today's technologically advanced world, a large number of businesses are using Artificial Intelligence (AI) to enhance their maintenance operations through CMMS solutions. The union of AI and CMMS has created a dynamic partnership that transforms the way businesses operate.
According to Gartner, 70% of captured manufacturing data remains unused due to several complexities. AI brings advanced capabilities to CMMS software, which allows businesses to understand ample maintenance data and derive data-driven insights from it.
AI-powered algorithms also analyze sensor data in real time, detecting patterns that predict equipment failures before they occur. For example, AI-driven Computerized Maintenance Management Systems (CMMS) can autonomously schedule repairs, reducing downtime by up to 50%.
Digital Twins and Self-Optimization
This type of computer program uses real-world data to create simulations of how a product would actually behave. The simulation is generally based on the current state of the asset and historical data.
Digital twins can predict equipment failures with 100% accuracy by simulating different operating conditions. As technology advances, self-sufficient maintenance will eventually replace human maintenance of machines.
The Rise of Self-Healing Machines
What if machines don’t just warn us about problems and fix themselves before we even notice anything is wrong? Amazing right?
Self-healing machines use tiny nanotechnology to fix themselves when damaged. For example, some car paints can repair small scratches on their own. In robotics, flexible robots can heal minor tears in their outer layer. Also, airplane parts made with special materials can close small cracks before they grow.
In manufacturing, self-healing machinery can significantly reduce production downtime. Machine-embedded, network-connected sensors collect massive amounts of valuable data from the machines they are attached to.
Additionally, machine learning also enables self-healing processes by registering how the machine is supposed to work and then restoring faulty components that prevent it from functioning well.
The Shift from Predictive Maintenance to Self-Sustaining Operations
Self-sustaining operations powered by AI, smart sensors, and IoT are revolutionizing industries. These technologies enable systems to autonomously adapt, heal, and optimize, marking a significant shift from predictive maintenance.
The integration of Artificial Intelligence (AI), smart sensors, and the Internet of Things (IoT) is ushering in a new era of self-sustaining operations across various industries. This technological convergence empowers systems to not only predict potential failures but to autonomously adapt, heal, and optimize their performance in real-time. This paradigm shift represents a significant advancement from traditional predictive maintenance models, where the focus was primarily on anticipating and preventing failures before they occurred.
With AI-driven autonomous maintenance, systems can leverage machine learning algorithms and real-time data from IoT devices to monitor their own health and performance. This enables them to detect anomalies, diagnose root causes, and take corrective actions without human intervention. In addition, these systems can learn from their experiences and optimize their operations over time, leading to increased efficiency, reduced downtime, and extended asset lifespans.
The implications of this technological revolution are far-reaching, with the potential to transform industries like manufacturing, transportation, energy, and healthcare. For example, in manufacturing, autonomous maintenance systems can enable factories to operate around the clock with minimal human supervision, reducing labor costs and increasing productivity. In transportation, self-healing vehicles can improve safety and reliability by detecting and repairing faults before they lead to accidents. In the energy sector, smart grids can optimize power distribution and consumption, leading to greater efficiency and sustainability. And in healthcare, AI-powered medical devices can monitor patients' vital signs and deliver personalized treatments, improving outcomes and reducing healthcare costs.
At the end of the day, the rise of autonomous maintenance systems represents a major technological breakthrough with the potential to drastically change industries and improve our daily lives. As these systems continue to evolve, we can expect to see even greater advancements in efficiency, productivity, safety, and sustainability across various sectors.
Beyond Predictive: Machines That Think and Act
Traditional maintenance relies on scheduled checkups or predictive AI, which alerts humans about potential failures. Nowadays, with the advent of smart sensors and cloud computing, machines can analyze their condition in time and adjust where it is concerned.
For example, imagine an engine detecting overheating and automatically cooling itself down or a factory machine sensing a worn-out part and ordering a replacement before it breaks. Indeed, this is superb!
But this transition is more than just a matter of convenience — it will absolutely overhaul industries. The decreased incidence of outages, lower repair costs, and near-zero human involvement mean businesses can run quicker, smarter, and more efficiently than ever before.
IIoT and the Fully Connected Maintenance Ecosystem
Think of every machine in a factory having the ability to communicate with one another, exchange data, and maximize operational efficiency instantaneously. And that's precisely what IIoT and 5G enable.
Think of it as a factory nervous system. Sensors act as nerve endings, machines as muscles, and AI as the brain, ensuring everything runs in perfect harmony. If one part slows down, another can adjust instantly.
When an error occurs, the system resolves it before it can interfere with production. Amazing, right? The autonomous maintenance system is more than simply maintenance. It’s about ensuring they don’t break, ever.
Industry 5.0: The Human-Machine Collaboration in Maintenance
Industry 5.0 is a new and innovative evolution of the maintenance concept based on the importance of human-machine cooperation rather than complete automation. While Industry 4.0 emphasizes autonomous systems, Industry 5.0 acknowledges that human mastery remains essential. This shift also converts maintenance from reactive repairs to more strategic oversight.
Traditionally, teams would fix issues only after failures occurred. Now, AI-powered predictive analytics help technicians anticipate and prevent breakdowns.
AI-driven assistants play an important role in this evolution. Rather than taking over, these systems support technicians with guided diagnostics, step-by-step troubleshooting, and real-time performance monitoring.
IBM’s Maximo AI, for instance, aids maintenance teams by delivering predictive insights and suggesting the best course of action. Microsoft’s HoloLens, for example, employs augmented reality (AR) to project repair information on top of machinery, helping technicians complete complex jobs with greater accuracy.
In the end, Industry 5.0 encourages a partnership between mankind and machines in which human intuition and machine intelligence go hand in hand. To live in a future with a symbiotic relationship with AI that augments humanity but will not replace it.
Challenges and Roadblocks to Full Autonomy
While autonomous maintenance promises efficiency and reliability, achieving full autonomy comes with challenges. From cybersecurity threats to workforce adaptation and financial constraints, industries must address key roadblocks before fully embracing AI-driven maintenance.
Data Privacy and Cybersecurity in Smart Maintenance
It is predicted that cyber threats on behalf of the burglaries will be increase as maintenance systems are getting more intelligent. Vulnerabilities in IoT-connected equipment can be exploited by hackers, resulting in the failure of a system and data breach. To avoid this, industries should adopt strict cybersecurity strategies, including real-time threat detection and encrypted communication.
Adherence to international data laws such as GDPR and CCPA means additional complexities. Businesses must guarantee compliance through AI-powered systems without slipping into negligence. They must also balance innovation with the need to remain on the right side of the law.
Workforce Adaptation and Skill Gaps
AI and automation are reshaping maintenance, and this requires new skills beyond traditional mechanical expertise. Technicians now need knowledge of data analytics, IoT systems, and AI diagnostics.
To bridge this gap, companies like Siemens and General Electric offer digital training programs. AR-assisted learning and AI-driven simulation tools can also help workers adapt efficiently.
Cost and Infrastructure Limitations
Truly autonomous driving requires major infrastructure investments in AI integration and IoT networks. Before transitioning, businesses must consider the ROI (return on investment).
One answer is Maintenance-as-a-Service (MaaS), where businesses pay for AI-backed maintenance solutions instead of large, one-time upfront costs. This model makes intelligent upkeep more available and strikes a balance between technology and monetization.
Future Predictions: What’s Next for Autonomous Maintenance?
As technology advances, maintenance is evolving from human-dependent jobs to fully automated systems . What lies ahead are smart, self-sufficient solutions that would redefine power and dependability in multiple sectors.
The Rise of Maintenance-Free Factories
Thanks to AI-driven diagnostics, predictive maintenance, and self-healing materials, human intervention will be reduced to near zero in the automotive, electronics, and pharmaceutical industries.
Sensors will detect wear and tear in real time, triggering automated repairs before breakdowns, ultimately creating a super-efficient manufacturing environment.
Quantum Computing in Maintenance
Predictive analytics is already starting to transform maintenance, but quantum computing will go further. Unlike classical computers, quantum processors sift through huge data sets at lightning speed and detect failure patterns before they occur.
This allows hyper-accurate predictions that minimize the possibility of unexpected downtimes faced by industries such as energy, transportation, and healthcare. Quantum-enhanced AI will then be able to adjust maintenance schedules, allowing machines to work at their peak performance with minimal human input.
The Role of Space Maintenance in Future Technologies
Autonomous maintenance will be key as space exploration expands. Artificially driven robots will service satellites, space stations, and factories on the moon or Mars.
Self-repairing materials, 3D-printed parts, and predictive diagnostics will keep operations running in extreme environments. These advancements will sustain space missions and inspire smarter maintenance solutions on Earth.
Conclusion: The Inevitable Future
Autonomous maintenance is being recognized as a necessity for enterprises to remain competitive. These AI, IIoT, and self-healing materials can drive efficiencies, reduce downtime, and lower costs. Those companies that put off adoption risk getting left behind.
To take that first step, businesses can implement an AI-on CMMS, leverage smart sensors for real-time data monitoring, and focus on workforce training. Cybersecurity needs to be high on the agenda as well to secure data-driven solutions.
By taking these steps now, companies position themselves for a future where machines self-diagnose, self-repair, and optimize performance. Ensuring seamless, cost-effective operations in an increasingly automated world.
TABLE OF CONTENTS
Keep Reading
Ever find yourself checking into a luxury hotel and expecting a relaxing stay, only to find a ...
11 Apr 2025
Organizations are witnessing swift changes in the business environment and confronting a ...
8 Apr 2025
Last month, news outlets and the entire internet was abuzz with the return of NASA astronauts ...
3 Apr 2025
What comes first - CMMS or predictive maintenance? If your answer is either, it is correct. ...
28 Mar 2025
Artificial intelligence (AI) talk has become commonplace. Today, engaging in business-focused ...
27 Mar 2025
A facility maintenance plan is at the core of a facility’s operations. This organized ...
21 Mar 2025
Think of managing your maintenance operations like managing a championship sports team. Just ...
21 Mar 2025
The maintenance sector is battling a severe talent shortage that threatens to undermine ...
7 Mar 2025
Manufacturing maintenance is the backbone of industrial efficiency, ensuring machines run ...
5 Mar 2025
No one likes playing a guessing game when equipment breaks down. Yet, maintenance teams often ...
4 Mar 2025
The size of the preventive maintenance software market is discussed in millions of dollars, ...
4 Mar 2025
The organizational structure and corporate hierarchy vary from company to company. Large ...
28 Feb 2025
Maintenance procedures are essential for ensuring the longevity and reliability of machinery ...
21 Feb 2025
Sustainability is no longer just a buzzword; it's a critical component of corporate social ...
20 Feb 2025
A Computerized Maintenance Management System (CMMS) relies on accurate, well-organized data ...
18 Feb 2025
In an era where technology drives operational efficiency, Computerized Maintenance Management ...
14 Feb 2025
A Computerized Maintenance Management System (CMMS) is a key component of modern maintenance ...
13 Feb 2025
Introduction Maintenance management is the foundation of maintenance operations in industries ...
11 Feb 2025
Introduction A Computerized Maintenance Management System (CMMS) is software designed to help ...
7 Feb 2025
Introduction Due to a growing awareness of the need to combat climate change, the green ...
6 Feb 2025