TABLE OF CONTENTS
- The Integral Role of Fleets in Modern Businesses
- Operational Efficiency
- Cost Control
- Safety and Compliance
- Asset Lifespan
- Types of Fleets
- Industries that Rely on Fleets
- Variations in Fleet Size and Composition
- Understanding Fleet Types for Effective Management and Maintenance
- Benefits of Effective Fleet Maintenance and Management
- Cost Savings and Resource Optimization
- Increased Operational Efficiency and Productivity
- Improved Safety, Compliance, and Risk Management
- Improved Asset Lifespan and Asset Management
- Fleet Maintenance Strategies
- Preventive Maintenance
- Corrective Maintenance
- Predictive Maintenance
- CMMS for Fleet Maintenance
- Building Fleet Maintenance Processes within the CMMS
- Developing a Fleet Maintenance Schedule
- Factors Influencing Maintenance Frequency
- Fleet Management Strategies
- Fleet Planning and Acquisition
- Vehicle Tracking and Telematics
- Fuel and Cost Management
- Compliance and Regulatory Management
- Trends and Innovations in Fleet Maintenance and Management
- Electric and Autonomous Vehicles
- Sustainability and Eco-friendly Practices
- Data Analytics and AI-driven Fleet Management
Fleet maintenance and management consist of a comprehensive set of practices, strategies, and technologies to ensure the optimal operation and upkeep of a company's fleet of vehicles and assets. It involves everything from routine vehicle inspections to data-driven decision-making, all to keep a fleet running efficiently, cost-effectively, and safely.
Fleet maintenance and management are operational necessities and strategic functions that can significantly impact a company's bottom line. This is particularly true in industries such as transportation, logistics, delivery services, and construction, where fleets of vehicles and equipment are at the core of daily operations.
THE INTEGRAL ROLE OF FLEETS IN MODERN BUSINESSES
Fleets, comprising various vehicles and assets, serve as the lifeblood of countless industries. They are the vehicles that transport goods across continents, the machinery that powers construction sites, and the service vehicles that reach customers' doorsteps. Without efficient fleet maintenance and management, the wheels of modern commerce would grind to a halt.
Fleets play a pivotal role in achieving several key business objectives:
Operational Efficiency
An optimally maintained fleet ensures that deliveries are made on time, construction projects progress without hitches, and field services are conducted smoothly. This efficiency translates directly into customer satisfaction and increased competitiveness.
Cost Control
Managing fleet costs is paramount in today's economy. Fuel expenses, maintenance, insurance, and asset depreciation are significant financial considerations. Effective fleet management can mitigate these costs and improve a company's financial health.
Safety and Compliance
Safety is paramount when operating fleets for drivers and the public. Compliance with safety regulations is not just a legal requirement but also a moral responsibility. Fleet maintenance and management are essential for achieving and maintaining high safety standards.
Asset Lifespan
Fleet assets represent a significant investment for any organization. Extending the lifespan of these assets through proactive maintenance and proper management can yield substantial returns on investment.
TYPES OF FLEETS
Industries that Rely on Fleets
Fleets serve as the logistical backbone that ensures products reach their destinations, services are delivered, and projects are completed on schedule. Understanding the vast array of industries that rely on fleets is essential for appreciating the versatility and significance of fleet management and maintenance.
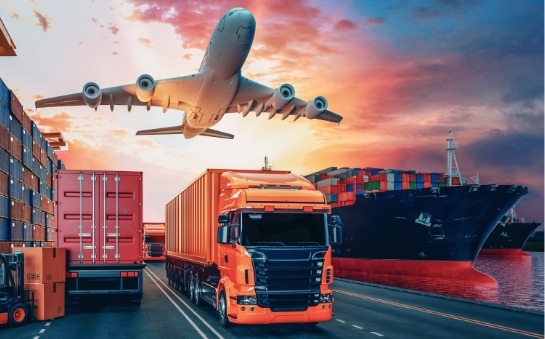
Transportation and Logistics
This is perhaps the most obvious industry that depends on fleets. Trucking companies, freight carriers, and courier services rely on fleets of various sizes to transport goods locally and globally.
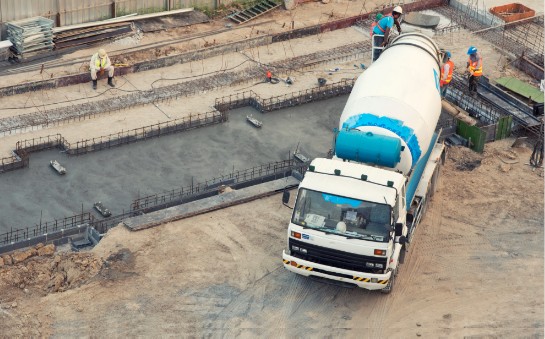
Construction
Construction firms utilize fleets of heavy machinery, including excavators, bulldozers, cranes, and trucks, to carry out building projects efficiently.
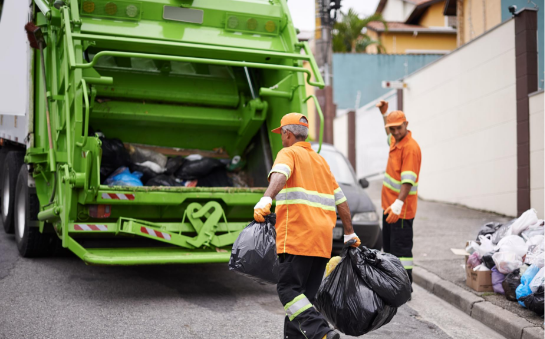
Public Services
Municipalities employ fleets of vehicles for public services such as garbage collection, snow removal, and emergency response.
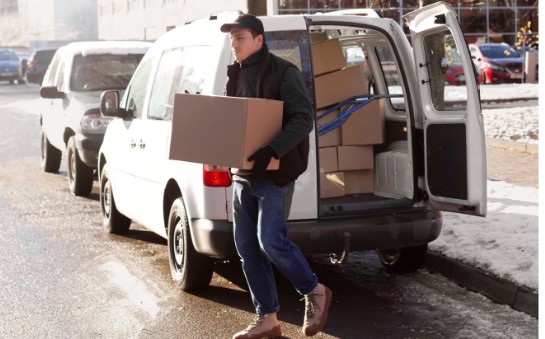
Delivery Services
E-commerce giants and food delivery services employ fleets of vans, cars, and bikes to deliver products to consumers' doorsteps.
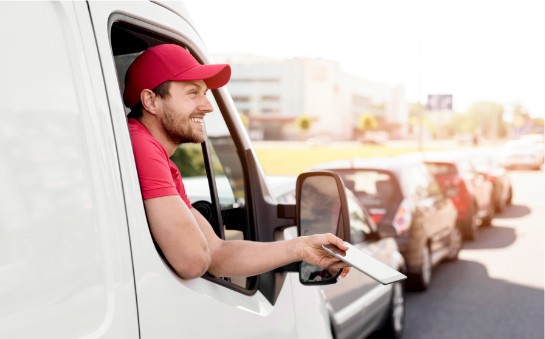
Field Services
Companies in the service sector, such as utilities, telecommunications, and HVAC, deploy fleets to send technicians to customer locations for repairs and installations.
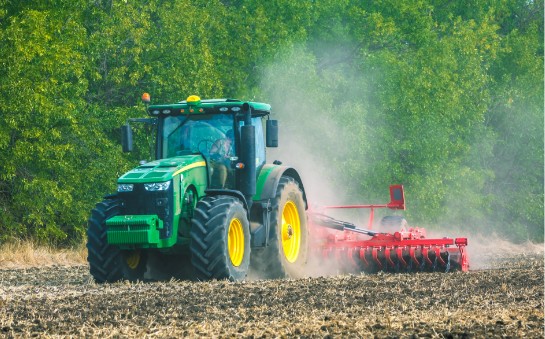
Agriculture
Farms utilize specialized agricultural fleets, including tractors, combine harvesters, and irrigation equipment, to manage crops and increase yields.
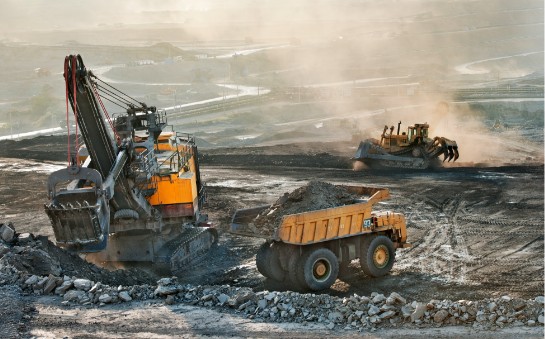
Mining and Resources
The mining industry relies on fleets of heavy equipment for extraction, transportation, and processing of minerals and resources.
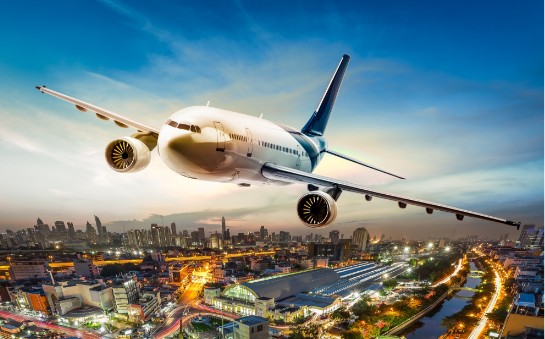
Aviation
Airlines manage fleets of aircraft, while ground handling services operate fleets of vehicles and equipment at airports.
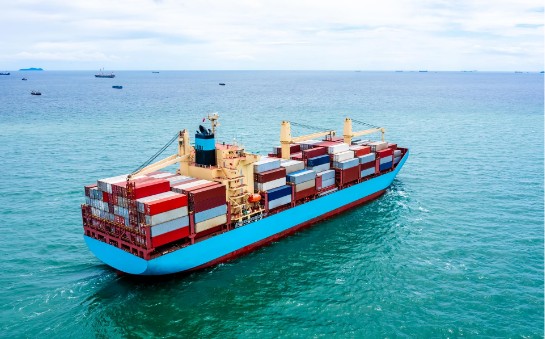
Maritime
Shipping companies manage fleets of cargo ships, container vessels, and tankers for global trade.
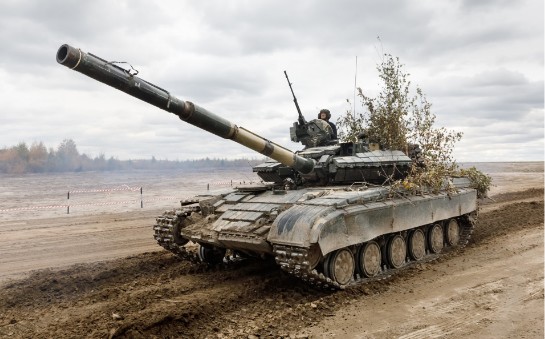
Government and Military
Government agencies and the military maintain fleets of vehicles, ranging from administrative cars to military tanks.
Variations in Fleet Size and Composition
Fleets exhibit significant variations in terms of size and composition. The specific needs of each industry, as well as the operational objectives of organizations, determine the size and types of vehicles or equipment included in a fleet. Here are some common variations:
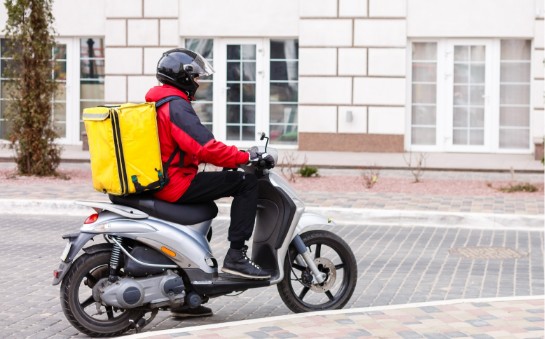
Small Business Fleets
Small businesses often manage compact fleets of a few vehicles, typically for local operations like deliveries or service calls.
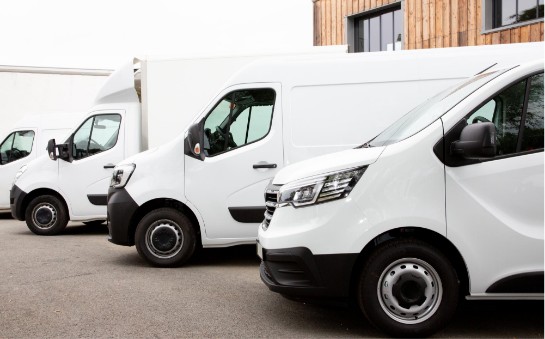
Medium-Sized Fleets
Medium-sized enterprises maintain fleets ranging from a dozen to a few hundred vehicles, covering a broader operational area or serving a larger customer base.
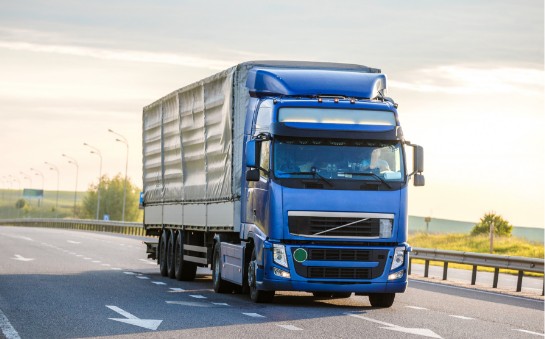
Large Enterprise Fleets
Large corporations and logistics companies operate extensive fleets that can number in the thousands, often involving various vehicle types.
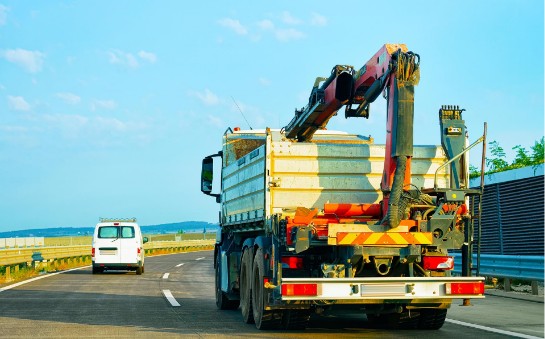
Mixed-use Fleets
Some organizations, especially in construction and field services, have mixed-use fleets that include various types of vehicles, from light-duty vans to heavy construction machinery.
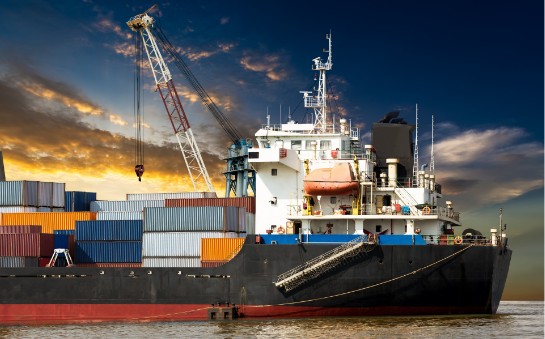
Specialized Fleets
Certain industries, like aviation and maritime, have highly specialized fleets with unique equipment designed for specific tasks, such as cargo ships or aircraft.
Understanding Fleet Types for Effective Management and Maintenance
Each type of vehicle or equipment has unique maintenance requirements, operational considerations, and regulatory compliance standards. By categorizing fleets based on their types, organizations can:
Tailor Maintenance Plans
Develop maintenance schedules and procedures specific to different fleet components' needs, ensuring optimal performance and longevity.
Optimize Asset Allocation
Allocate resources efficiently by understanding which vehicles or equipment are most critical to daily operations.
Enhance Compliance
Ensure that each type of vehicle or equipment complies with industry-specific regulations and safety standards.
Improve Budgeting
Accurately budget maintenance and replacement costs by accounting for the diverse fleet components.
BENEFITS OF EFFECTIVE FLEET MAINTENANCE AND MANAGEMENT
Effective fleet maintenance yields many advantages extending far beyond the garage. From cost savings to enhanced safety, these benefits drive the strategic importance of maintaining and managing fleets efficiently.
Cost Savings and Resource Optimization
One of the most compelling advantages of effective fleet maintenance and management is the significant cost savings it can bring to an organization. Here's how:
- Reduced Maintenance Costs: Proactive maintenance, instead of reactive repairs, can save organizations substantial sums. By identifying and addressing issues before they escalate, maintenance costs can be controlled and kept within budget.
- Improved Fuel Efficiency: Properly maintained vehicles and equipment tend to be more fuel-efficient. This translates to lower fuel costs, especially in larger fleets with substantial fuel expenses.
- Extended Asset Lifespan: Regular maintenance, such as oil changes and part replacements, can significantly extend the life of fleet assets. This means fewer new purchases and capital expenditures over time.
- Lower Insurance Premiums: A well-maintained fleet with a healthy track record for safety and compliance can lead to lower insurance premiums, reducing overall operational costs.
- Decreased Downtime: Preventive maintenance and swift repairs minimize the downtime caused by vehicle breakdowns. This means that more assets are available to be used for revenue-generating activities and operations.
- Optimized Asset Allocation: Through data-driven insights, fleet managers can identify underutilized assets and make informed decisions about which vehicles or equipment to deploy, ultimately minimizing costs.
Increased Operational Efficiency and Productivity
Fleet maintenance and management contribute significantly to enhancing operational efficiency and productivity within an organization:
- On-time Deliveries: Well-maintained vehicles are more reliable, ensuring that deliveries and services are completed on schedule. This improves customer satisfaction and loyalty.
- Reduced Workflow Disruption: Minimizing downtime due to breakdowns or repairs means fewer disruptions to daily operations, keeping employees on track with their tasks.
- Optimized Routing: Advanced fleet management systems can optimize routes, reducing travel time and fuel consumption, which is especially critical for logistics and delivery services.
- Streamlined Communication: CMMS software with features to manage fleet maintenance enables real-time communication with drivers and field personnel, allowing for efficient task assignment and status updates.
Improved Safety, Compliance, and Risk Management
Safety is paramount when it comes to fleet operations, and effective maintenance and management directly contribute to this aspect:
- Safer Work Environment: Regular maintenance checks ensure that vehicles and equipment are in top working condition, reducing the risk of accidents and injuries to drivers and operators.
- Regulatory Compliance: Fleet maintenance and management help organizations comply with industry-specific regulations and safety standards, avoiding costly fines and legal liabilities.
- Risk Mitigation: Properly maintained fleets are less likely to experience accidents, breakdowns, or safety incidents, reducing the organization's overall risk exposure.
- Driver Training: Fleet management strategies often include ongoing training programs for drivers, further enhancing safety and compliance.
Improved Asset Lifespan and Asset Management
Assets represent a significant investment for organizations. Effective fleet maintenance and management help protect and maximize this investment:
- Extended Asset Lifespan: Regular maintenance and proper management can significantly extend the life of fleet assets, ensuring a higher return on investment.
- Data-driven Asset Management: Fleet management systems provide valuable data and insights that allow organizations to make informed decisions about asset allocation, replacements, and upgrades.
- Asset Tracking: With GPS and telematics systems, organizations can track the location and condition of assets, reducing the risk of theft or loss.
- Optimized Depreciation: Well-maintained assets tend to depreciate more slowly, preserving their value on the balance sheet.
FLEET MAINTENANCE STRATEGIES
1. Preventive Maintenance
Preventive maintenance is a systematic approach aimed at proactively maintaining and servicing vehicles and equipment within a fleet to prevent potential issues and ensure their continuous and reliable operation. A fleet preventive maintenance software can help enable this strategy. The primary objectives of preventive maintenance for fleets are as follows:
- Minimize Downtime: By identifying and addressing potential problems before they lead to breakdowns or failures, preventive maintenance helps minimize unplanned downtime, ensuring that vehicles and equipment remain available for operations.
- Enhance Reliability: The primary goal is to maintain the reliability of fleet assets, ensuring that they can be depended upon for daily tasks and operations without unexpected disruptions.
- Extend Asset Lifespan: Preventive maintenance practices are designed to extend the life of fleet assets, thereby maximizing the return on investment and delaying the need for expensive replacements.
- Optimize Performance: Regular inspections, servicing, and component replacements help maintain optimal performance, leading to improved fuel efficiency, reduced emissions, and enhanced overall functionality.
1.1 Scheduled Inspections and Maintenance Tasks for Fleet Management
To achieve the objectives of preventive maintenance in fleet management, a well-structured schedule of inspections and maintenance tasks is essential. Key tasks include:
- Routine Inspections: Regular visual and functional checks of vehicles and equipment to detect wear and tear, fluid leaks, loose components, and other potential issues.
- Fluid Changes: Scheduled oil changes, coolant flushes, brake fluid replacement, and other fluid-related maintenance to ensure proper lubrication and cooling.
- Tire Maintenance: Regular inspections for tire wear, proper inflation, and alignment to improve safety and fuel efficiency.
- Component Replacement: Timely replacement of wear-prone components such as belts, hoses, filters, and brake pads to prevent failures.
- Software Updates: For modern vehicles and equipment with onboard systems, updating software to enhance performance, resolve known issues, and ensure compliance with manufacturer recommendations.
- Documentation: Maintaining comprehensive records of all maintenance activities, including dates, tasks performed, and any components replaced or repaired.
1.2 Preventive Maintenance Process and Best Practices for Fleets
Implementing an effective preventive maintenance process for fleets involves the following steps and best practices:
- Schedule Creation: Establish maintenance schedules based on manufacturer recommendations, vehicle usage patterns, and historical data. Tailor the schedule to the specific needs of each asset.
- Task Assignment: Assign specific tasks to trained maintenance personnel, ensuring they have access to the necessary tools, equipment, and parts.
- Inspection and Servicing: Conduct routine inspections, perform scheduled maintenance tasks, and document all findings and actions taken during each maintenance event.
- Record Keeping: Maintain accurate records of all maintenance activities, including dates, costs, and the condition of components before and after servicing.
- Data Analysis: Utilize CMMS and data analysis tools to identify maintenance trends, predict future maintenance needs, and optimize scheduling for maximum efficiency.
- Continuous Improvement: Continuously refine the preventive maintenance schedule and procedures based on insights gained from data analysis. Embrace a culture of continuous improvement to enhance the effectiveness of preventive maintenance practices over time.
2. Corrective Maintenance
Corrective maintenance refers to the reactive approach of addressing unexpected breakdowns and performing emergency repairs when a vehicle or equipment within a fleet experiences a failure or malfunction. The primary purpose of corrective maintenance is:
- Minimize Downtime: Corrective maintenance is focused on minimizing the downtime caused by unexpected breakdowns. Its primary objective is to restore the affected vehicle or equipment to operational status as quickly as possible.
- Emergency Repairs: Serve as a rapid response mechanism to address unforeseen issues efficiently, ensuring that vehicles or equipment can return to service promptly.
2.1 Handling Unexpected Breakdowns and Emergency Repairs of Fleets
Corrective maintenance involves a swift and structured approach to handling unexpected breakdowns and emergency repairs within a fleet:
- Diagnosis: Quickly diagnose the cause of the breakdown, whether mechanical, electrical, or related to other systems or components.
- Emergency Repairs: Perform immediate repairs or part replacements to restore the vehicle or equipment to operational status. The focus is on resolving the specific issue that led to the breakdown.
- Prioritization: Assess the urgency of the repair and prioritize vehicles or equipment based on their criticality to ongoing operations. Vehicles that are essential for immediate tasks should be prioritized.
2.2 Streamlining Corrective Maintenance Processes
To streamline corrective maintenance processes in fleet management and minimize disruptions:
- Emergency Protocols: Establish clear emergency response protocols that outline the steps to follow when a breakdown occurs. Ensure that all maintenance personnel are well-versed in these protocols.
- Spare Parts Inventory: Maintain a well-stocked spare parts inventory to facilitate swift repairs and replacements. Having critical components readily available can significantly reduce repair time.
- Communication: Implement effective communication channels and reporting mechanisms to promptly notify maintenance teams of breakdowns, track progress, and coordinate repairs efficiently.
Unexpected breakdowns can occur despite the most comprehensive preventive maintenance efforts. Corrective maintenance aims to reduce downtime and swiftly return vehicles and equipment to their operational status, ultimately contributing to the fleet's overall operational efficiency.
3. Predictive Maintenance
Predictive maintenance represents an advanced and data-driven approach to fleet maintenance. It involves the use of technology, sensors, data analysis, and predictive analytics to anticipate when maintenance is required for vehicles and equipment within a fleet. Unlike traditional maintenance approaches that rely on fixed schedules or react to failures, predictive maintenance aims to optimize maintenance schedules, reduce downtime, and enhance asset reliability by identifying maintenance needs before they lead to breakdowns. In addition, maintenance is done on an as-needed basis and not at fixed intervals, regardless if needed or not.
3.1 The Process for Predictive Maintenance of Fleets
The process of implementing predictive maintenance for fleets involves the following key steps:
- Data Collection: Advanced sensors and telematics systems installed in vehicles and equipment collect real-time data on various performance metrics, including engine data, temperature, vibration, usage patterns, and more.
- Data Analysis: Utilizing sophisticated data analysis tools and machine learning algorithms, the collected data is processed and analyzed. The goal is to identify patterns, anomalies, and deviations from expected performance.
- Maintenance Alerts: When the data analysis detects potential issues or anomalies that indicate impending failures or maintenance needs, maintenance alerts are generated. These alerts are used to predict when specific maintenance tasks should be performed.
- Scheduled Maintenance: Maintenance teams receive and act on alerts by scheduling and performing the recommended maintenance tasks. This can include anything from component replacements to software updates, depending on the nature of the predicted maintenance need.
- Continuous Monitoring: Predictive maintenance is an ongoing process. Continuous monitoring of vehicle and equipment data ensures that maintenance needs are constantly assessed and addressed promptly.
3.2 Benefits of Predictive Maintenance in Fleet Management
Implementing predictive maintenance in fleet management offers numerous advantages, including:
- Reduced Downtime: By predicting maintenance needs in advance, fleets can schedule and perform maintenance during planned downtime, minimizing the impact on operations and reducing costly unplanned downtime.
- Extended Asset Lifespan: Predictive maintenance helps extend the life of fleet assets by addressing issues before they escalate and cause significant damage, thereby maximizing the return on investment.
- Cost Savings: Optimized maintenance reduces unnecessary servicing and part replacements, leading to cost savings in labor, materials, and overall maintenance expenses.
- Improved Safety: Addressing potential safety issues proactively enhances driver and operator safety, reducing the risk of accidents or incidents caused by equipment failures.
- Data-driven Decision-making: Predictive maintenance provides valuable data insights that inform strategic decisions related to fleet management, asset allocation, and resource planning.
CMMS FOR FLEET MAINTENANCE
CMMS software plays an important role in streamlining fleet maintenance operations, improving efficiency, and optimizing asset management. Here's why it's indispensable:
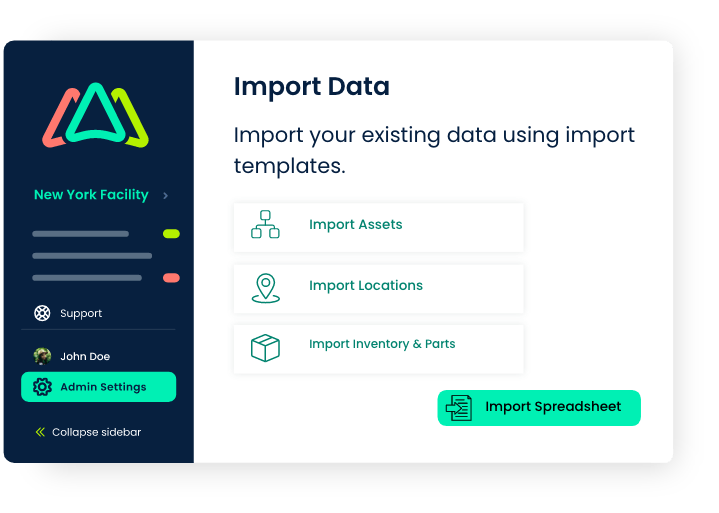
Data Centralization
CMMS is a centralized repository for all fleet-related data, including maintenance records, repair history, and asset details. This ensures that critical information is easily accessible and eliminates the need for manual record-keeping, reducing errors.

Preventive Maintenance
CMMS allows for creating and managing preventive maintenance schedules. This proactive approach helps reduce unplanned downtime, extend asset lifespan, and control maintenance costs.
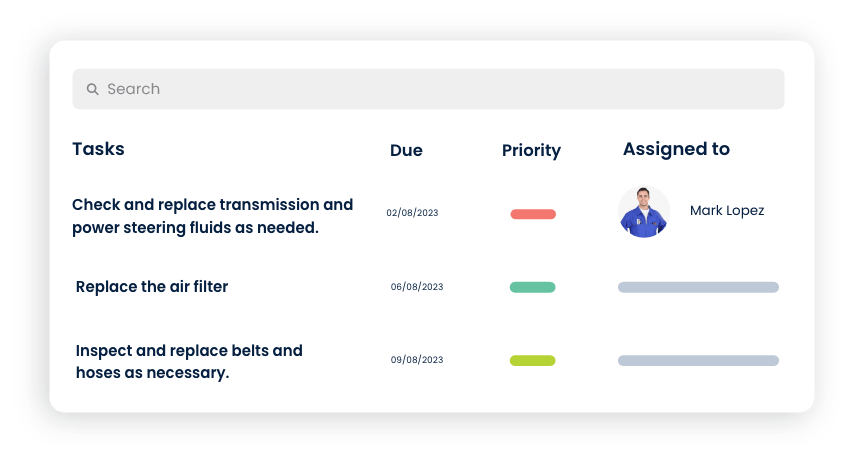
Work Order Automation
A CMMS automates the creation of work orders, either based on predefined maintenance schedules or triggered by real-time data from sensors and telematics. This automation reduces manual workload and ensures timely task assignments.
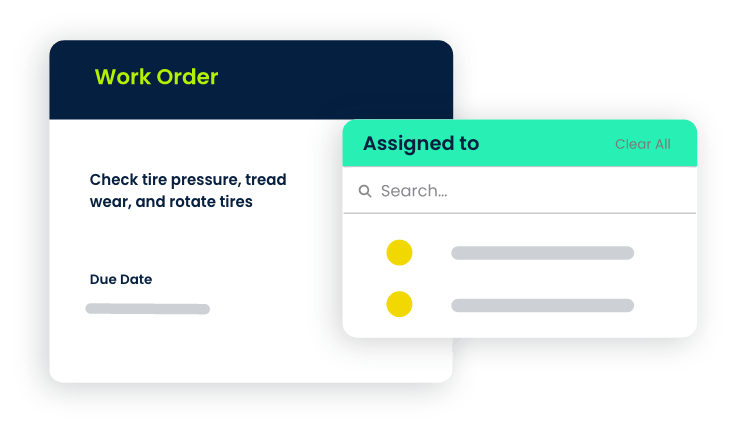
Assignment and Tracking
CMMS software allows for seamless assignment of work orders to maintenance personnel, often with built-in notifications and reminders. This ensures that tasks are promptly attended to and tracks the progress of each work order.
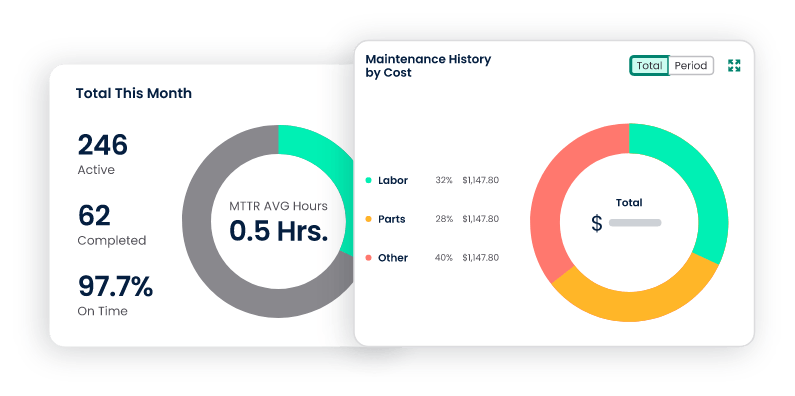
Documentation and Records
CMMS facilitates comprehensive documentation of maintenance activities. Technicians can input details about parts used, labor hours expended, and asset conditions before and after maintenance, creating a digital trail for auditing and analysis.
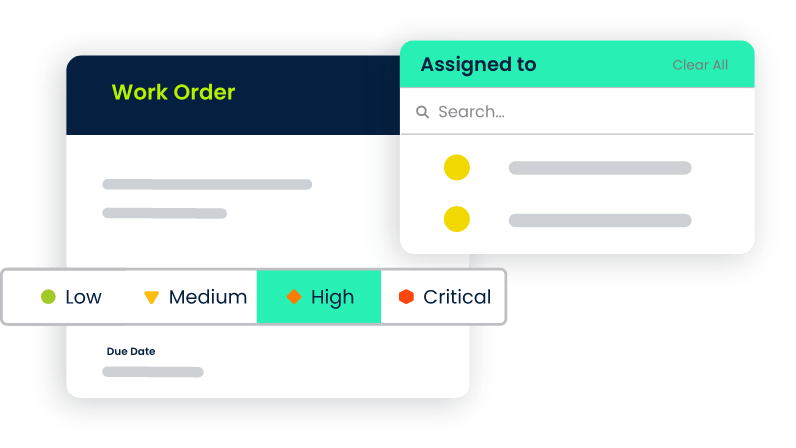
Prioritization and Scheduling
CMMS enables the prioritization of work orders based on criticality and urgency. Fleet managers can schedule maintenance tasks efficiently, ensuring that high-priority tasks receive immediate attention.
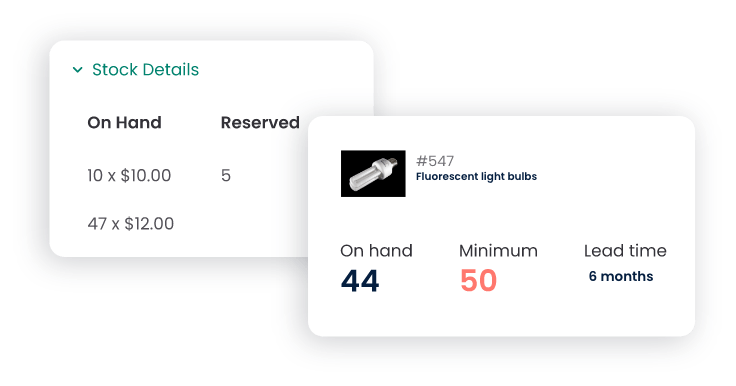
Inventory Management
CMMS includes inventory management capabilities, allowing organizations to track spare parts, consumables, and supplies. This ensures that the correct parts are available when needed, minimizing downtime.
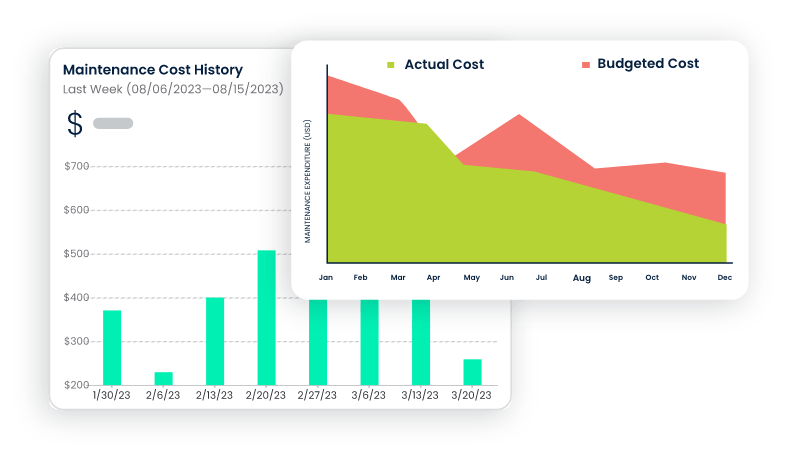
Cost Control
CMMS provides cost analysis tools, helping organizations track maintenance expenses, identify cost-saving opportunities, and make data-driven decisions to optimize spending.
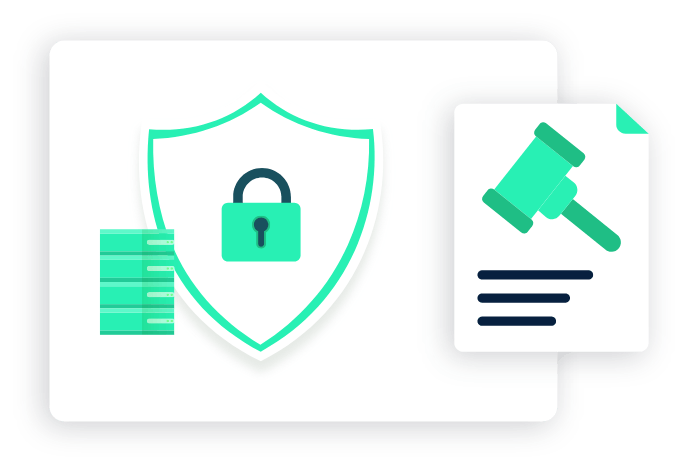
Compliance and Reporting
CMMS software ensures compliance with industry regulations and safety standards. It also generates detailed reports for audits and performance analysis.
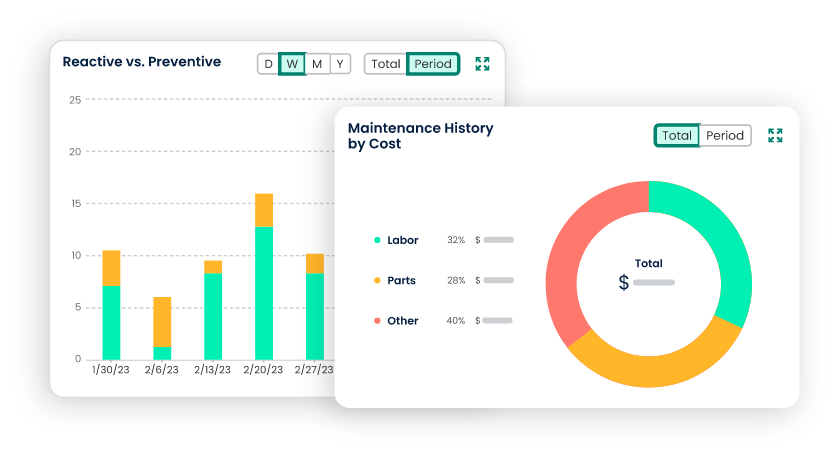
Data-driven Decision-making
CMMS systems gather a wealth of data on maintenance activities, costs, asset performance, and trends. This data can be analyzed to make informed decisions, optimize maintenance processes, and predict future maintenance needs.
Building Fleet Maintenance Processes within the CMMS
To build effective fleet maintenance processes within a CMMS, organizations should follow these steps:
- Data Import: Import existing fleet data into the CMMS, including asset details, maintenance history, and inventory levels.
- Asset Setup: Create asset profiles for each vehicle, equipment, and component, including specifications, warranty information, and maintenance requirements.
- Preventive Maintenance Planning: Develop preventive maintenance schedules tailored to each asset type. Include tasks, intervals, and associated documentation.
- Work Order Workflow: Define workflows for work order creation, assignment, and completion. Set up approval processes and notifications.
- Inventory Management: Populate the CMMS with inventory items, set reorder points, and establish a system for tracking and replenishing inventory.
- Reporting and Analytics: Configure reports and dashboards to monitor fleet performance, maintenance costs, and compliance metrics.
- Training: Train maintenance personnel and staff on using the CMMS effectively, ensuring everyone understands their roles and responsibilities within the system.
Developing a Fleet Maintenance Schedule
Creating a routine maintenance calendar is fundamental to effective fleet maintenance. This calendar serves as a roadmap for ensuring that all fleet assets receive the necessary maintenance and servicing at the right times. Key steps include:
- Asset Identification: Begin by identifying all fleet assets, including vehicles, equipment, and components. Maintain a comprehensive inventory with essential details such as make, model, age, and maintenance history.
- Manufacturer Guidelines: Consult manufacturer recommendations for maintenance intervals and procedures. These guidelines provide a baseline for your maintenance schedule.
- Usage Patterns: Analyze the frequency and intensity of asset usage. Vehicles or equipment used more frequently or under harsh conditions may require more frequent maintenance.
- Mileage or Hours: Determine whether maintenance intervals should be based on mileage, engine hours, or other usage metrics. Different asset types may have varying triggers.
- Inspection Points: Identify specific inspection points and tasks for each asset type. This may include fluid checks, filter replacements, and brake inspections.
- Maintenance Categories: Categorize maintenance tasks into groups, such as routine inspections, preventive maintenance, and major overhauls, to ensure a balanced schedule.
- Calendar Integration: Incorporate all maintenance tasks into a calendar, specifying dates for inspections and servicing. Ensure that maintenance tasks are scheduled to avoid overlapping or causing operational disruptions.
- Flexibility: Allow for flexibility in the schedule to accommodate unexpected breakdowns or urgent repairs.
Factors Influencing Maintenance Frequency
Asset Identification
Begin by identifying all fleet assets, including vehicles, equipment, and components. Maintain a comprehensive inventory with essential details such as make, model, age, and maintenance history.
Asset Type
Different asset types, such as heavy trucks, passenger vehicles, or specialized equipment, may have unique maintenance requirements.
Usage Intensity
Vehicles or equipment used heavily or continuously may need more frequent attention to maintain performance.
Environmental Conditions
Assets operating in extreme weather conditions or off-road environments may require more frequent maintenance to combat accelerated wear and tear.
Telematics Data
Utilize telematics data to monitor asset performance and trigger maintenance based on real-time usage data, allowing for more precise maintenance scheduling.
FLEET MANAGEMENT STRATEGIES
1. Fleet Planning and Acquisition
Effective fleet management begins with thoughtful planning and strategic asset acquisition. This involves analyzing the size and composition of your fleet, adopting the right acquisition strategies, and considering sustainability as a core element of your approach.
1.1 Fleet Size and Composition Analysis
Analyzing the size and composition of your fleet is the foundational step in fleet planning. Here's how to approach it:
- Right-size: Evaluate whether your current fleet size aligns with the operational demands of your organization. Identify underutilized assets and assess whether you have the right mix of vehicles and equipment.
- Asset Diversity: Consider the diversity of your fleet composition. Ensure that the range of vehicles and equipment in your fleet meets the specific needs and objectives of your organization.
1.2 Fleet Acquisition Strategies
Strategic fleet acquisition involves making informed decisions about when and how to acquire assets:
- Lease vs. Purchase: Determine whether leasing or outright purchasing of assets is more cost-effective and aligns with your long-term goals. Each option has its advantages and considerations.
- Lifecycle Management: Implement a lifecycle management approach for your fleet assets. This approach involves determining when assets should be replaced or refurbished, taking into account factors like depreciation, maintenance costs, and technological obsolescence.
- Standardization: Consider standardizing your fleet by adopting specific vehicle models or equipment types. Standardization can simplify maintenance, reduce parts inventory, and enhance efficiency.
1.3 Sustainability Considerations
Incorporate sustainability into your fleet planning and acquisition strategies:
- Alternative Fuels: Explore options for transitioning to alternative fuels, such as natural gas or electricity, to reduce emissions and environmental impact.
- Efficient Routing: Implement route optimization and load planning strategies to reduce fuel consumption and minimize the environmental footprint of your fleet.
- Emission Reduction: Ensure compliance with emissions regulations and seek ways to reduce the carbon footprint of your fleet through fuel-efficient technologies and practices.
2. Vehicle Tracking and Telematics
2.1 Benefits of Vehicle Tracking and Telematics Systems
Vehicle tracking and telematics systems have revolutionized fleet management by providing real-time visibility into the location, performance, and behavior of fleet assets. Here are some key benefits:
- Real-time Visibility: Vehicle tracking systems offer real-time tracking of fleet assets, enabling fleet managers to know the exact location of each vehicle or piece of equipment at any given time. This real-time visibility is invaluable for monitoring fleet operations.
- Improved Safety: Telematics systems can track driver behavior, including speeding, harsh braking, and rapid acceleration. This information allows fleet managers to identify unsafe driving habits and implement corrective measures, enhancing overall safety.
- Enhanced Efficiency: By monitoring routes and travel times, fleet managers can optimize routes for fuel efficiency and reduced travel times, resulting in cost savings and improved operational efficiency.
- Theft Prevention: Vehicle tracking systems act as deterrents to theft. In the event of a theft, real-time tracking can aid in the rapid recovery of stolen assets.
- Maintenance Alerts: Telematics systems can monitor the health of fleet assets in real-time, sending alerts for maintenance needs based on usage and performance data. This proactive approach minimizes breakdowns and extends asset lifespan.
2.2 Data-driven Decision-making
Vehicle tracking and telematics systems provide a wealth of data that enable data-driven decision-making processes:
- Predictive Maintenance: By analyzing telematics data, fleet managers can predict when maintenance tasks are needed. This proactive approach reduces unplanned downtime and maintenance costs.
- Route Optimization: Historical data on travel times, traffic patterns, and route efficiency allow for route optimization, minimizing fuel consumption and delivery times.
- Driver Performance: Telematics data provides insights into driver behavior. Fleet managers can use this data to identify areas for improvement, provide targeted training, and incentivize safe and efficient driving.
- Cost Analysis: The data collected by telematics systems can be used to conduct detailed cost analyses, helping fleet managers identify cost-saving opportunities and make informed decisions about fleet operations.
- Dispatch Efficiency: Real-time tracking data can be used for efficient dispatching, ensuring that the closest and most suitable asset is assigned to each task, leading to quicker response times and improved customer service.
- Inventory Management: Telematics data can be used to monitor and manage inventory levels of spare parts, ensuring that critical components are readily available for maintenance tasks.
- Reporting and Analysis: Utilize the data from vehicle tracking and telematics systems to generate reports and conduct in-depth analysis, enabling continuous improvement in fleet operations and maintenance practices.
3. Fuel and Cost Management
Efficient fuel and cost management are essential components of effective fleet management. Implementing strategies to optimize fuel usage, controlling costs, and considering environmental sustainability are important for fleet success.
3.1 Strategies for Efficient Fuel Management
Fuel is one of the most significant operational expenses in fleet management. Implementing strategies for efficient fuel management can lead to substantial cost savings:
- Fuel Efficiency Training: Provide drivers with training on fuel-efficient driving techniques, including smooth acceleration, maintaining consistent speeds, and minimizing idling time.
- Route Optimization: Utilize route optimization software to plan efficient routes, reduce mileage, and minimize fuel consumption. Real-time traffic updates can further enhance route efficiency.
- Telematics Data: Leverage telematics data to monitor and analyze fuel usage patterns. Identify areas where fuel efficiency can be improved and make data-driven adjustments.
- Maintenance Practices: Ensure that vehicles receive regular maintenance and that tires are properly inflated. Well-maintained vehicles tend to be more fuel-efficient.
3.2 Cost Control Measures
- Total Cost of Ownership (TCO) Analysis: Calculate the Total Cost of Ownership for each asset, taking into account acquisition costs, maintenance, fuel, depreciation, and other expenses. This analysis helps in making informed procurement decisions.
- Preventive Maintenance: Prioritize preventive maintenance to reduce repair costs and extend asset lifespans. Preventive maintenance practices can prevent costly breakdowns.
- Fuel Card Programs: Implement fuel card programs to monitor and manage fuel expenses. Fuel cards can provide detailed data on fuel purchases and help identify unauthorized or excessive spending.
- Cost Analysis Tools: Utilize fleet management software and analytics tools to conduct detailed cost analyses. Identify cost-saving opportunities and track expenses over time.
3.3 Environmental Considerations
- Alternative Fuels: Explore the adoption of alternative fuels, such as natural gas, propane, or electricity, to reduce emissions and environmental impact.
- Emission Reduction Technologies: Invest in emission reduction technologies, such as exhaust after-treatment systems, to minimize the environmental footprint of your fleet.
- Eco-friendly Practices: Promote eco-friendly driving practices among your drivers, including reducing idling time and optimizing routes to minimize emissions.
- Environmental Regulations: Stay informed about environmental regulations and compliance requirements related to emissions and fuel usage. Ensure that your fleet operations adhere to these regulations.
4. Compliance and Regulatory Management
Fleet management involves navigating a complex landscape of regulatory requirements and safety standards. To ensure compliance and minimize risks, fleet managers should have a solid understanding of regulatory requirements, employ effective compliance tracking and reporting mechanisms, and implement risk mitigation strategies.
4.1 Overview of Regulatory Requirements
Fleet management is subject to various regulatory requirements and safety standards, depending on factors like location, industry, and asset type. Common areas of regulation include:
- Safety Regulations: Compliance with safety regulations is paramount. This includes adherence to regulations governing driver hours of service, vehicle inspections, and load securement.
- Emissions Standards: Environmental regulations mandate compliance with emissions standards, requiring fleets to meet specific criteria for vehicle emissions, maintenance, and reporting.
- Licensing and Certification: Ensure that drivers possess the necessary licenses, certifications, and qualifications to operate specific types of vehicles and equipment.
- Reporting Requirements: Fleet managers are often required to maintain records of inspections, certifications, maintenance activities, and compliance documentation.
- Weight and Load Limits: Compliance with weight and load limit regulations is important for road safety. Overloading vehicles can result in fines and accidents.
4.2 Compliance Tracking and Reporting
Efficient compliance tracking and reporting are essential for fleet managers to demonstrate adherence to regulatory requirements:
- Compliance Software: Utilize compliance software to monitor and track compliance with various regulations. These systems can automate compliance checks and provide real-time alerts.
- Document Management: Maintain comprehensive records of inspections, certifications, maintenance activities, and compliance-related documentation. Ensure that these records are easily accessible for audits and reporting.
- Reporting Tools: Implement reporting tools that generate compliance reports, detailing adherence to safety and environmental regulations. These reports may be required for regulatory audits and reporting.
- Regular Audits: Conduct regular internal audits to identify and rectify compliance gaps. External audits may also be necessary to ensure adherence to industry-specific standards.
4.3 Risk Mitigation Strategies
- Training: Provide comprehensive training to drivers and maintenance personnel to ensure awareness of and adherence to regulatory requirements and safety standards.
- Audits and Inspections: Regularly inspect fleet assets and operations to promptly identify and address compliance issues promptly. Conduct safety audits and environmental assessments to identify areas for improvement.
- Continuous Education: Stay informed about changes in regulations and industry standards. Attend industry conferences, workshops, and seminars to keep abreast of evolving compliance requirements.
- Technology Integration: Integrate compliance tracking into your fleet management software and systems. Leverage technology to automate compliance checks and ensure real-time monitoring.
- Legal Consultation: In complex regulatory environments, seek legal counsel or consulting services to ensure your fleet operations comply with all applicable laws and regulations.
TRENDS AND INNOVATIONS IN FLEET MAINTENANCE AND MANAGEMENT
Electric and Autonomous Vehicles
- Electric Vehicles (EVs) Revolution: The shift towards electric vehicles is transforming the fleet management landscape. EVs offer reduced operational costs, lower emissions, and energy efficiency. Fleet managers are adopting electric vehicles to align with sustainability goals and reduce carbon footprints.
- Autonomous Vehicles (AVs) Advancements: Autonomous vehicles are on the horizon, promising safer and more efficient transportation. AVs can improve safety by reducing human errors, and have the benefit of optimizing routes and reducing labor costs. Fleet managers are exploring the potential of AVs for future operations.
- Hybrid Technologies: Hybrid vehicles that combine internal combustion engines with electric power are gaining popularity. These vehicles offer fuel efficiency without sacrificing range, making them suitable for various fleet applications.
Sustainability and Eco-friendly Practices
- Green Initiatives: Sustainability has become a core focus in fleet management. Organizations are adopting eco-friendly practices to reduce emissions and minimize their environmental impact. This includes transitioning to alternative fuels, implementing fuel-efficient technologies, and optimizing routes for reduced fuel consumption.
- Telematics and Eco-driving: Telematics systems are used to monitor and incentivize eco-driving practices among drivers. Real-time data on driving behavior helps reduce fuel consumption and emissions, contributing to sustainability goals.
- Alternative Fuels: Fleet managers are exploring alternative fuels such as natural gas, propane, and hydrogen to reduce carbon emissions. These fuels offer environmental benefits without sacrificing performance.
Data Analytics and AI-driven Fleet Management
- Data-driven Decision-making: Data analytics is a game-changer in fleet management. Advanced analytics tools help fleet managers make informed maintenance, route optimization, and cost control decisions. Data-driven insights improve efficiency and reduce operational costs.
- AI-powered Routing: AI-driven routing and scheduling algorithms optimize delivery routes in real-time, considering traffic, weather, and customer preferences. This results in reduced fuel consumption and improved on-time delivery rates.
- Machine Learning for Driver Behavior: Machine learning models analyze driver behavior to identify areas for improvement. This includes detecting patterns of aggressive driving, speeding, and idling, leading to safer and more efficient driving practices.