Using Preventive Maintenance Audits to Strengthen Maintenance Programs
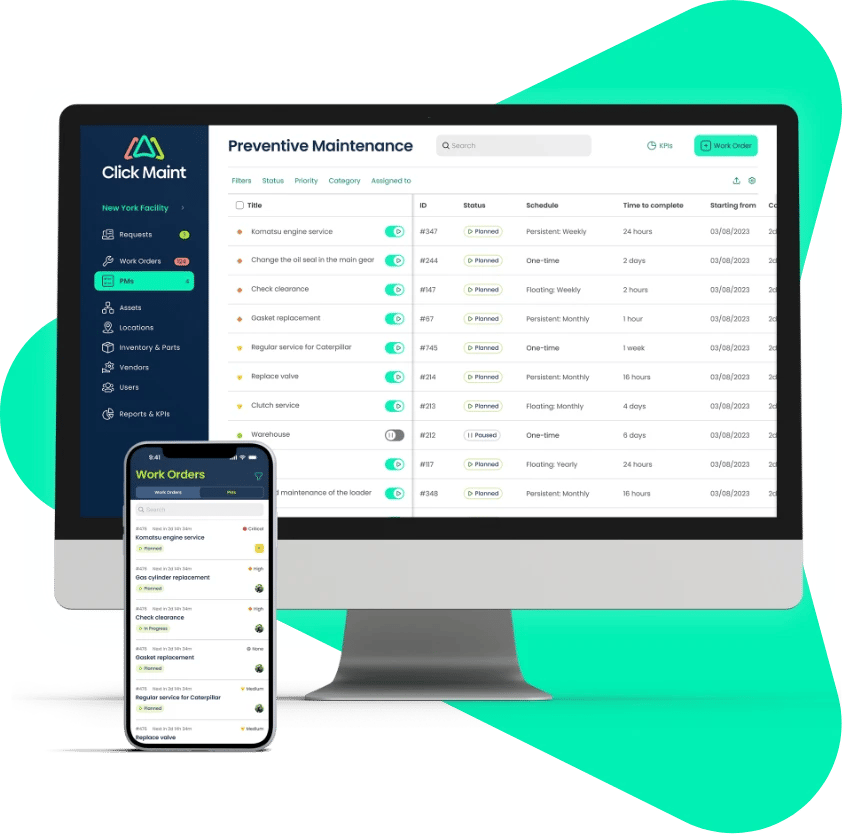
TABLE OF CONTENTS
Preventive maintenance audits serve as a critical tool in the arsenal of maintenance professionals, enabling them to assess the effectiveness and compliance of preventive maintenance programs within industrial facilities. These audits involve systematic evaluations of maintenance procedures, documentation, and adherence to established protocols. By conducting preventive maintenance audits regularly, organizations can identify areas for improvement, address deficiencies, and fine-tune their maintenance strategies to align with operational goals and industry best practices. PM audits not only enhance equipment reliability but also contribute to cost savings, regulatory compliance, and workplace safety.
What is a Preventive Maintenance Audit?
A PM audit is a systematic examination and evaluation of preventive maintenance processes, procedures, and outcomes within an industrial facility. It involves a comprehensive review of maintenance records, equipment performance metrics, and adherence to established maintenance protocols. The primary aim of a PM audit is to assess the effectiveness, efficiency, and compliance of preventive maintenance practices with organizational objectives, industry standards, and regulatory requirements.
Objectives of PM Audits
1. Evaluate Maintenance Effectiveness
PM audits seek to evaluate the effectiveness of preventive maintenance activities in achieving their intended goals. By analyzing maintenance records, equipment reliability metrics, and historical performance data, audits assess the extent to which preventive maintenance measures have succeeded in minimizing downtime, reducing equipment failures, and optimizing asset lifespan.
2. Identify Areas for Improvement
Another key objective of PM audits is to identify areas for improvement within the preventive maintenance program. By scrutinizing maintenance procedures, documentation practices, and resource allocation, audits uncover potential inefficiencies, gaps in compliance, and opportunities for enhancement. These insights enable organizations to implement corrective actions and refine their maintenance strategies to maximize efficiency and effectiveness.
3. Ensure Regulatory Compliance
PM audits play an important role in ensuring regulatory compliance with industry standards, safety regulations, and environmental requirements. By verifying adherence to maintenance protocols, safety procedures, and record-keeping practices, audits help mitigate the risk of non-compliance and associated penalties. They also promote a culture of accountability and transparency in maintenance management, fostering a safe and compliant work environment.
4. Optimize Resource Allocation
By assessing resource utilization, labor allocation, and inventory management practices, PM audits help optimize resource allocation within the maintenance department. Audits identify areas of resource wastage, redundancy, or underutilization, enabling organizations to reallocate resources more efficiently. This optimization ensures that maintenance activities are conducted cost-effectively while maximizing the value of available resources.
5. Enhance Overall Maintenance Performance
Ultimately, the overarching objective of PM audits is to enhance the overall performance of the preventive maintenance program. By addressing deficiencies, implementing best practices, and leveraging insights gained from audits, organizations can elevate the effectiveness, reliability, and sustainability of their maintenance operations. PM audits serve as a catalyst for continuous improvement, driving operational excellence and long-term success in maintenance management.
Components of a Preventive Maintenance Audit
A thorough PM audit comprises multiple components, each essential for evaluating the effectiveness and compliance of preventive maintenance practices. This section delineates the key components of a PM audit, elucidating their significance in assessing maintenance processes and outcomes.
1. Documentation Review
The foundation of any preventive maintenance audit lies in the review of maintenance documentation, including work orders, preventive maintenance checklists, maintenance schedules, and equipment manuals. This component involves scrutinizing the completeness, accuracy, and timeliness of maintenance records to ensure compliance with established protocols and regulatory requirements. A comprehensive documentation review provides insights into the consistency of maintenance practices, adherence to maintenance schedules, and effectiveness of record-keeping procedures.
2. Equipment Inspection
Conducting physical inspections of industrial equipment is integral to the PM audit process. This component involves visually inspecting equipment, machinery, and infrastructure to assess their condition, identify potential issues, and verify compliance with maintenance standards. During equipment inspections, auditors examine components such as bearings, belts, electrical connections, and structural integrity to detect signs of wear, damage, or malfunction. These inspections provide valuable insights into the effectiveness of preventive maintenance measures and the overall health of industrial assets.
3. Data Analysis
Data analysis forms a critical component of PM audits, allowing auditors to derive actionable insights from maintenance performance metrics, equipment reliability data, and historical maintenance records. This component involves analyzing maintenance KPIs such as mean time between failures (MTBF), mean time to repair (MTTR), and equipment availability to assess maintenance effectiveness and identify trends or patterns. By leveraging data analysis techniques, auditors can identify areas for improvement, prioritize maintenance activities, and make data-driven decisions to optimize maintenance operations.
4. Performance Evaluation
The final component of a PM audit entails evaluating the overall performance of the preventive maintenance program against predefined objectives and benchmarks. This evaluation involves assessing the effectiveness, efficiency, and compliance of maintenance practices based on audit findings and performance metrics. By comparing audit results against established standards, industry best practices, and organizational goals, auditors can gauge the success of the preventive maintenance program and identify opportunities for enhancement. Performance evaluation serves as a feedback mechanism, informing continuous improvement initiatives and driving the evolution of maintenance strategies over time.
Benefits of Conducting Preventive Maintenance Audits
By systematically evaluating maintenance activities, procedures, and documentation, PM Audits offer a multitude of benefits that contribute to the overall effectiveness of preventive maintenance efforts.
Identifying Maintenance Gaps
One of the primary benefits of PM Audits is their ability to identify maintenance gaps within an organization's operations. These gaps may include overlooked maintenance tasks, inconsistent adherence to maintenance schedules, or areas where maintenance procedures can be improved. By pinpointing these gaps, organizations can take corrective action to ensure that all necessary maintenance activities are being performed in a timely and effective manner. This proactive approach helps minimize the risk of equipment failures and ensures the longevity of critical assets.
Ensuring Compliance with Regulations
In many industries, regulatory compliance is a critical consideration for maintenance operations. PM Audits play a vital role in ensuring that organizations remain compliant with relevant regulations and standards. By systematically reviewing maintenance practices and documentation, audits help identify areas where compliance may be lacking and provide recommendations for bringing operations into alignment with regulatory requirements. This not only reduces the risk of costly fines and penalties but also helps uphold the organization's reputation as a responsible and trustworthy entity.
Enhancing Equipment Reliability
PM Audits contribute to enhanced equipment reliability by identifying and addressing potential maintenance issues before they lead to equipment failures. By conducting thorough inspections and evaluations, audits help ensure that equipment is properly maintained and in optimal working condition. This proactive approach minimizes the risk of unplanned downtime and disruptions to operations, allowing organizations to maintain a consistent level of productivity and efficiency. Additionally, by optimizing maintenance practices based on audit findings, organizations can further enhance equipment reliability and prolong the lifespan of their assets.
Optimizing Maintenance Schedules
Another key benefit of PM Audits is their role in optimizing maintenance schedules. By reviewing maintenance logs, records, and performance data, audits provide insights into the effectiveness of existing maintenance schedules and identify opportunities for improvement. This may include adjusting the frequency of maintenance tasks, optimizing resource allocation, or implementing predictive maintenance techniques to address emerging issues proactively. By optimizing maintenance schedules based on audit findings, organizations can minimize downtime, reduce maintenance costs, and maximize the efficiency of their maintenance programs.
Planning for a Preventive Maintenance Audit
1. Set Clear Objectives
The first step in planning for a PM audit is to establish clear objectives that align with the organization's goals and priorities. Define the scope of the audit, identify specific areas or processes to be evaluated, and articulate the desired outcomes of the audit. Whether the focus is on compliance, performance improvement, or risk mitigation, setting clear objectives provides a roadmap for the audit and ensures alignment with organizational objectives.
2. Establish Audit Criteria
Once objectives are defined, establish audit criteria that will guide the evaluation process. Determine the key performance indicators (KPIs), benchmarks, and standards against which maintenance practices will be assessed. Audit criteria may include factors such as maintenance effectiveness, compliance with regulations, equipment reliability metrics, and resource utilization. By defining audit criteria upfront, auditors can conduct evaluations systematically and consistently across different areas of the preventive maintenance program.
3. Select Audit Team
Selecting the right audit team is essential to ensure the thoroughness and credibility of the audit process. Assemble a multidisciplinary team with expertise in maintenance management, engineering, safety, and regulatory compliance. Consider including internal auditors as well as external experts or consultants with specialized knowledge in specific areas of maintenance. Ensure that audit team members possess the necessary skills, training, and impartiality to conduct objective evaluations and provide valuable insights.
4. Create an Audit Schedule
Developing a detailed audit schedule is important for organizing audit activities, allocating resources, and managing timelines effectively. Determine the duration of the audit, sequence of audit activities, and milestones for completion. Consider factors such as equipment availability, production schedules, and operational priorities when scheduling audits to minimize disruption to ongoing activities. Establish clear deadlines for audit tasks and ensure that the audit schedule accommodates sufficient time for data collection, analysis, and reporting.
5. Allocate Resources
Allocate resources, including personnel, budget, and technology, to support the audit process. Ensure that audit team members have access to the necessary tools, equipment, and information resources to conduct evaluations effectively. Allocate sufficient time and manpower to perform audits thoroughly, considering the complexity and scope of the audit objectives. Adequate resource allocation is essential for maximizing the effectiveness and efficiency of the audit process and achieving meaningful outcomes.
6. Communicate with Stakeholders
Effective communication with stakeholders is essential throughout the audit planning process. Keep key stakeholders, including maintenance managers, department heads, and senior leadership, informed about the objectives, scope, and timeline of the audit. Seek input from stakeholders to ensure that audit priorities align with organizational goals and expectations. Communicate regularly with audit team members to coordinate activities, address any issues or concerns, and ensure alignment with audit objectives. Transparent communication fosters stakeholder buy-in, promotes collaboration, and enhances the overall success of the audit process.
Pre-Audit Preparation
Before commencing the audit process, thorough preparation is essential to lay the groundwork for a successful evaluation. This phase involves reviewing documentation, gathering necessary tools and equipment, and conducting training for the audit team.
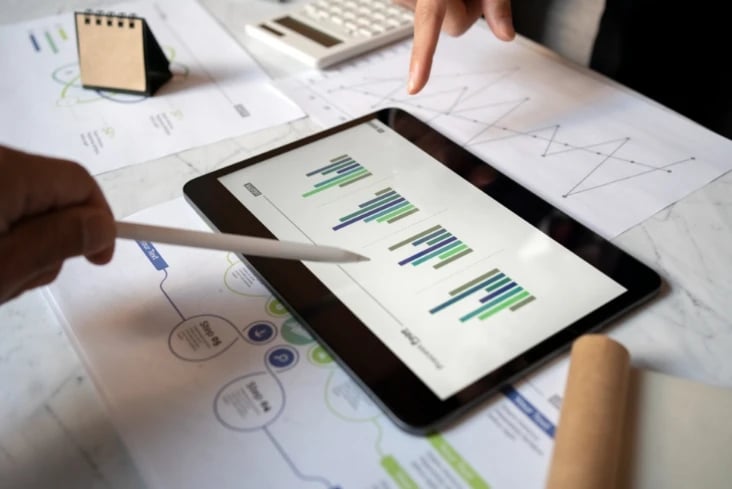
1. Review Documentation
The first step in pre-audit preparation is to review relevant documentation pertaining to the preventive maintenance program. This includes maintenance records, work orders, equipment manuals, standard operating procedures (SOPs), and regulatory requirements. Reviewing documentation provides auditors with insights into existing maintenance practices, historical maintenance activities, and compliance with established protocols. It also helps identify areas of focus for the audit and ensures that audit activities are aligned with organizational objectives and regulatory standards.
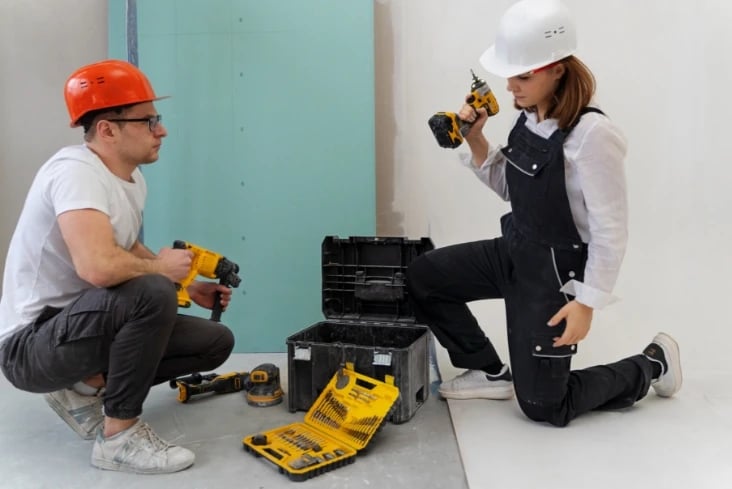
2. Gather Necessary Tools and Equipment
Next, gather the necessary tools, equipment, and resources required to conduct the audit effectively. This may include inspection tools, measurement devices, safety equipment, and documentation templates. Ensure that audit team members have access to the tools and equipment needed to perform inspections, gather data, and document findings accurately. Proper preparation ensures that auditors can conduct thorough evaluations of equipment, processes, and facilities during the audit.
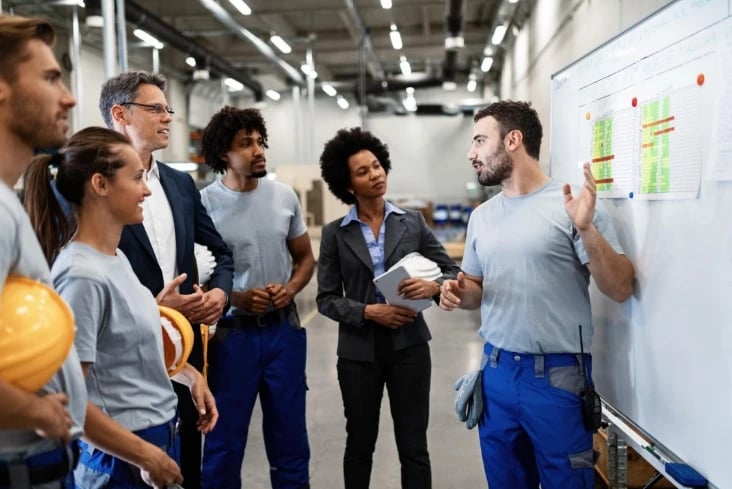
3. Conduct Training for the Audit Team
Training is essential to equip audit team members with the knowledge, skills, and competencies required to conduct the audit effectively. Provide training sessions covering audit objectives, methodologies, data collection techniques, and reporting procedures. Ensure that audit team members are familiar with audit criteria, evaluation criteria, and relevant industry standards or regulations. Training sessions may also include discussions on safety protocols, communication strategies, and conflict resolution techniques to ensure a smooth audit process. By investing in training, organizations can ensure that audit team members are prepared to perform their roles competently and contribute to the success of the audit.
On-site Audit Procedures
Once pre-audit preparations are complete, the focus shifts to conducting on-site audit procedures.
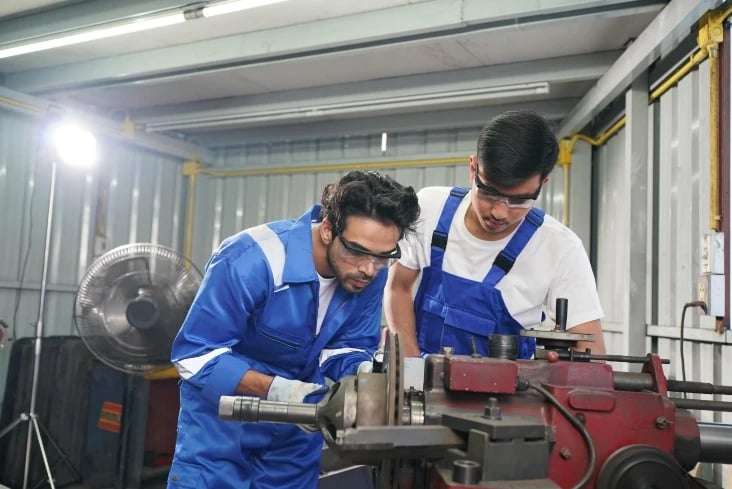
1. Equipment Inspection
The cornerstone of the on-site audit procedures is the inspection of industrial equipment and machinery. Audit team members conduct visual inspections of equipment to assess their condition, identify signs of wear or damage, and verify compliance with maintenance standards. Inspections may include checking for leaks, loose components, corrosion, or abnormal vibrations. Auditors use specialized tools and equipment to measure parameters such as temperature, pressure, and vibration levels to evaluate equipment performance accurately. The goal of equipment inspections is to identify potential issues, prioritize maintenance tasks, and ensure the reliability and safety of industrial assets.
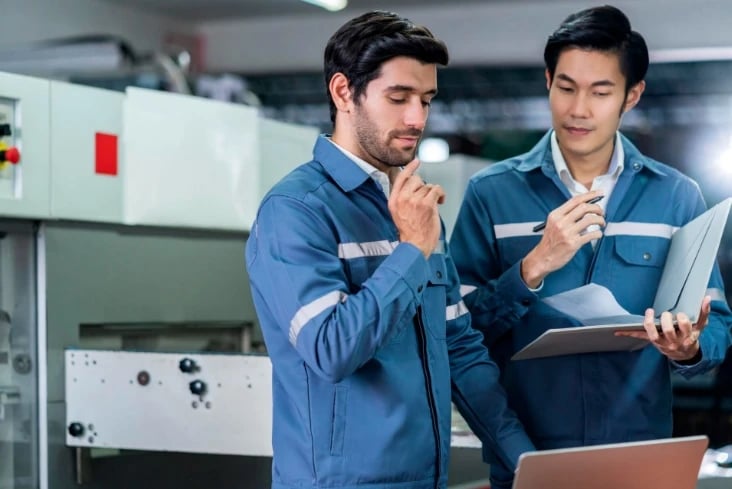
2. Review Maintenance Logs and Records
During the on-site audit, auditors review maintenance logs, work orders, and other documentation to verify the completion of preventive maintenance tasks and adherence to maintenance schedules. They assess the completeness, accuracy, and timeliness of maintenance records to ensure compliance with established protocols and regulatory requirements. Reviewing maintenance logs provides insights into the frequency of maintenance activities, trends in equipment performance, and the effectiveness of maintenance practices. Auditors may also cross-reference maintenance records with equipment history and performance data to identify discrepancies or areas for improvement.
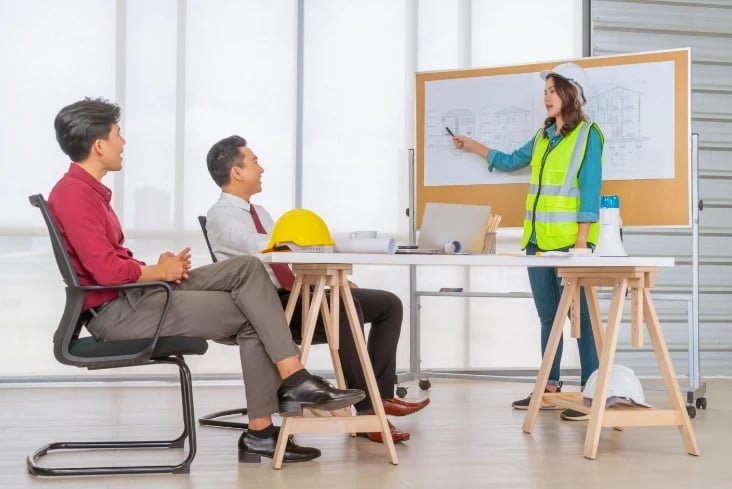
3. Interview Maintenance Personnel
Interviewing maintenance personnel is an important component of on-site audit procedures, providing firsthand insights into maintenance practices, challenges, and opportunities for improvement. Auditors conduct interviews with maintenance managers, technicians, and other relevant personnel to gather information about maintenance procedures, training programs, resource allocation, and communication protocols. Through interviews, auditors can assess the effectiveness of communication channels, identify training needs, and uncover potential barriers to successful maintenance execution. Interviewing maintenance personnel also promotes engagement, collaboration, and knowledge sharing, fostering a culture of continuous improvement within the maintenance department.
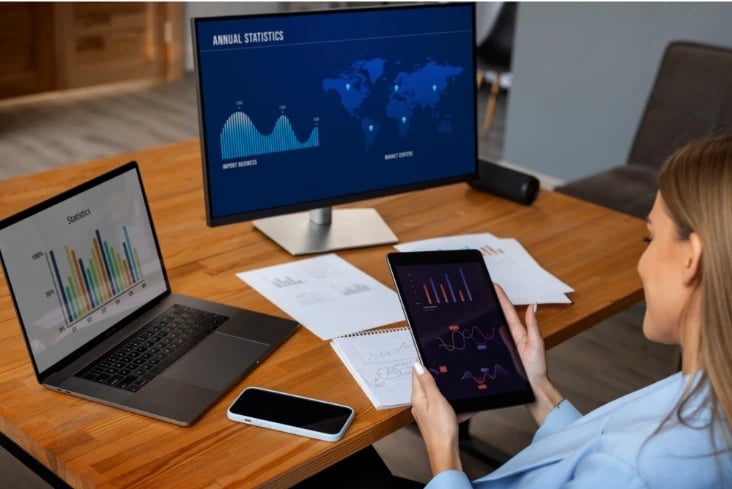
4. Data Collection
Data collection is an integral part of the on-site audit process, enabling auditors to gather quantitative and qualitative information to support their evaluations. Auditors collect data on equipment performance metrics, maintenance activities, downtime incidents, and resource utilization to assess the effectiveness of preventive maintenance practices. Data collection methods may include direct observation, measurements, surveys, and electronic data retrieval from maintenance management systems. By collecting comprehensive data sets, auditors can analyze trends, identify root causes of maintenance issues, and make data-driven recommendations for improvement.
Documentation of Audit Findings
Once the on-site audit procedures are completed, it's essential to document the findings accurately and comprehensively.
1. Record Observations
The first step in documenting audit findings is to record observations made during the audit process. Audit team members should document their observations systematically, noting any issues, deviations from standards, or areas of concern identified during equipment inspections, documentation reviews, interviews, and data collection. Clear and concise documentation of observations ensures that audit findings are accurately captured and can be effectively communicated to stakeholders.
2. Document Deficiencies
In addition to recording observations, auditors must document deficiencies discovered during the audit. Deficiencies may include equipment defects, maintenance lapses, non-compliance with regulations, or gaps in documentation practices. Auditors should provide detailed descriptions of deficiencies, including their nature, severity, and potential impact on operations. Documenting deficiencies enables organizations to prioritize corrective actions, allocate resources effectively, and address root causes to prevent recurrence.
3. Prioritize Recommendations
After documenting observations and deficiencies, auditors must prioritize recommendations for corrective actions based on their significance and potential impact. Recommendations should be categorized according to urgency, severity, and feasibility of implementation. High-priority recommendations address critical issues that pose immediate risks to safety, reliability, or compliance. Medium-priority recommendations target deficiencies that may impact efficiency, productivity, or cost-effectiveness but do not pose immediate threats. Low-priority recommendations address minor issues or opportunities for improvement that can be addressed over time. By prioritizing recommendations, organizations can focus resources on addressing the most critical issues first while planning for long-term improvements.
Analyzing Audit Results
Once the preventive maintenance audit is completed, analyzing the audit results is essential to derive actionable insights and drive continuous improvement in maintenance practices.
1. Identify Strengths and Weaknesses
The first step in analyzing audit results is to identify the strengths and weaknesses of the preventive maintenance program. Review the audit findings to identify areas where maintenance practices are effective, compliance is high, and equipment reliability is optimal. These strengths serve as benchmarks for best practices and areas to replicate across the organization. Simultaneously, weaknesses or areas of improvement should be identified where maintenance practices fall short, compliance is lacking, or equipment reliability is compromised. By recognizing both strengths and weaknesses, organizations can develop targeted strategies to build on successes and address deficiencies effectively.
2. Quantify Compliance Levels
Quantifying compliance levels is essential to assess the degree to which maintenance practices adhere to established protocols, standards, and regulatory requirements. Review audit findings to quantify compliance levels across various areas of the preventive maintenance program, such as maintenance procedures, documentation practices, and safety protocols. Use quantitative metrics, such as the percentage of completed maintenance tasks, adherence to maintenance schedules, and compliance with regulatory standards, to measure compliance levels objectively. Quantifying compliance levels provides organizations with actionable data to identify areas of non-compliance and prioritize corrective actions accordingly.
3. Evaluate Performance Metrics
Evaluating performance metrics is critical to assessing the effectiveness and efficiency of preventive maintenance practices. Analyze performance metrics, such as mean time between failures (MTBF), mean time to repair (MTTR), equipment uptime, and maintenance costs, to evaluate maintenance performance and identify areas for improvement. Compare performance metrics against industry benchmarks, organizational targets, and historical data to assess trends, identify deviations, and benchmark performance against best practices. Evaluating performance metrics enables organizations to identify opportunities to optimize maintenance practices, enhance equipment reliability, and reduce downtime and costs.
4. Root Cause Analysis of Identified Issues
Conducting root cause analysis for identified issues is essential to uncover the underlying factors contributing to maintenance deficiencies and equipment failures. Analyze audit findings to identify recurring issues, patterns, or trends that may indicate systemic problems within the preventive maintenance program. Use techniques such as the 5 Whys, fault tree analysis, or fishbone diagrams to trace issues back to their root causes, which may include factors such as inadequate training, insufficient resources, or outdated procedures. Root cause analysis provides organizations with insights into the fundamental causes of maintenance issues, enabling them to implement corrective actions that address underlying problems and prevent recurrence.
Using a CMMS to Conduct a Preventive Maintenance Audit
A Computerized Maintenance Management System (CMMS) plays a vital role in conducting a preventive maintenance audit by streamlining processes, centralizing data, and providing valuable insights into maintenance activities. Here's how a CMMS helps in conducting a PM audit:
1. Centralized Maintenance Data
A CMMS serves as a centralized repository for maintenance data, including work orders, equipment history, maintenance schedules, and asset information. During a PM audit, auditors can access this centralized database to review maintenance records, track equipment performance, and analyze historical maintenance activities. Centralized maintenance data simplifies the audit process by providing auditors with a comprehensive view of maintenance operations across the organization.
2. Documentation Management
A CMMS software facilitates the management of maintenance documentation, including preventive maintenance procedures, SOPs, and regulatory compliance documentation. Auditors can review and verify the completeness, accuracy, and currency of documentation within the CMMS during the audit process. The CMMS ensures that all relevant documentation is readily accessible, organized, and up-to-date, enabling auditors to assess compliance with maintenance protocols and regulatory requirements effectively.
3. Automated Workflows
A CMMS automates maintenance workflows, including work order generation, scheduling, assignment, and completion. During a PM audit, auditors can evaluate the efficiency and effectiveness of these automated workflows by reviewing workflow configurations, approval processes, and turnaround times. Automated workflows streamline maintenance processes, reduce manual errors, and improve accountability, contributing to overall maintenance performance.
4. Tracking Maintenance Activities
A CMMS enables real-time tracking of maintenance activities, including preventive maintenance tasks, inspections, and repairs. Auditors can monitor maintenance activities within the CMMS to assess compliance with maintenance schedules, identify trends in maintenance performance, and track adherence to established maintenance protocols. Real-time visibility into maintenance activities provides auditors with insights into the timeliness and completeness of maintenance tasks, facilitating accurate assessments of maintenance effectiveness.
5. Reporting and Analytics
A CMMS offers robust reporting and analytics capabilities, allowing auditors to generate custom reports, dashboards, and KPIs to support the audit process. Auditors can analyze maintenance data within the CMMS to identify trends, anomalies, and areas for improvement. Reporting tools enable auditors to communicate audit findings effectively to stakeholders and track progress on corrective actions. Analytics capabilities provide insights into maintenance performance, resource utilization, and equipment reliability, empowering auditors to make data-driven recommendations for optimization.
Implementing Corrective Actions
Implementing corrective actions is a critical phase following the analysis of audit results.
1. Prioritize Recommendations
The first step in implementing corrective actions is to prioritize the recommendations derived from the audit findings. Recommendations should be categorized based on their significance, urgency, and potential impact on operations. High-priority recommendations addressing critical issues should be addressed promptly to mitigate risks and prevent further disruptions. Medium and low-priority recommendations can be addressed sequentially, considering available resources and organizational priorities. Prioritization ensures that corrective actions are focused on addressing the most critical issues first, maximizing the effectiveness of resource allocation.
2. Develop Action Plans
Once recommendations are prioritized, develop action plans outlining the steps required to address each recommendation. Action plans should specify the objectives, tasks, timelines, and responsible parties for implementing corrective actions. Break down larger recommendations into smaller, manageable tasks to facilitate implementation and monitoring. Clearly defined action plans provide a roadmap for executing corrective actions systematically and ensure accountability for follow-through.
3. Assign Responsibilities
Assigning responsibilities is important to ensure that corrective actions are carried out effectively and efficiently. Identify individuals or teams responsible for implementing each task outlined in the action plans. Assign clear roles and responsibilities, specifying who is accountable for completing each task, providing oversight, and reporting progress. Ensure that individuals assigned to tasks possess the necessary skills, resources, and authority to fulfill their responsibilities effectively.
4. Allocate Resources
Allocate resources, including manpower, budget, equipment, and materials, to support the implementation of corrective actions. Assess resource requirements for each task outlined in the action plans and allocate resources accordingly. Ensure that adequate resources are allocated to address high-priority recommendations promptly, while also considering the resource constraints and competing priorities within the organization. Effective resource allocation is essential to ensure the successful execution of corrective actions and achieve desired outcomes.
5. Establish Timelines
Establish realistic timelines for completing each task and achieving the objectives outlined in the action plans. Set target dates for milestone achievements and final completion of corrective actions, considering the urgency and complexity of recommendations. Ensure that timelines are achievable and align with organizational priorities and constraints. Regularly monitor progress against established timelines, identify any deviations or delays, and take corrective actions as necessary to keep the implementation on track.
Monitoring and Continuous Improvement
Monitoring and continuous improvement are integral aspects of effective preventive maintenance management.
Track the Progress of Corrective Actions
Monitor the progress of corrective actions regularly to ensure that recommendations derived from the audit are being effectively implemented. Track the status of action items outlined in the action plans, including milestones achieved, tasks completed, and any deviations from established timelines. Use project management tools, communication channels, and reporting mechanisms to facilitate tracking and ensure transparency in progress monitoring. Timely tracking enables stakeholders to identify potential issues, address challenges, and take corrective actions to keep the implementation on track.
Review Performance Metrics
Review performance metrics to assess the effectiveness of corrective actions and measure improvements in maintenance practices and equipment reliability. Compare current performance metrics with baseline data collected before the implementation of corrective actions to evaluate progress and identify areas of improvement. Performance metrics may include mean time between failures (MTBF), mean time to repair (MTTR), equipment availability, maintenance costs, and compliance levels. Regular performance reviews provide insights into the impact of corrective actions and inform future decision-making to optimize maintenance operations further.
Conduct Regular Follow-up Audits
Schedule regular follow-up audits to evaluate the sustainability and effectiveness of corrective actions over time. Follow-up audits assess whether recommended changes have been successfully implemented, compliance levels have improved, and maintenance practices have been optimized. Use similar audit methodologies and criteria as the initial audit to ensure consistency and comparability of results. Follow-up audits also provide an opportunity to identify any new issues or emerging trends and make adjustments to maintenance plans accordingly.
Update Preventive Maintenance Plans
Based on the findings from follow-up audits and ongoing performance reviews, update preventive maintenance plans as needed to reflect changes in maintenance practices, equipment conditions, and organizational priorities. Incorporate lessons learned from corrective actions into revised maintenance plans, adjusting maintenance schedules, procedures, and allocation of resources as necessary. Ensure that preventive maintenance plans remain aligned with industry best practices, regulatory requirements, and organizational goals to drive continuous improvement and operational excellence.
Incorporate Lessons Learned
Incorporate lessons learned from audits, corrective actions, and performance reviews into the organizational knowledge base to facilitate continuous improvement. Capture and document insights, best practices, and success stories to guide future maintenance initiatives and decision-making. Foster a culture of learning and knowledge sharing within the maintenance department, encouraging collaboration, innovation, and continuous learning. By incorporating lessons learned into preventive maintenance practices, organizations can leverage past experiences to optimize performance, mitigate risks, and drive sustainable improvements over time.
Factors Influencing Audit Frequency
Determining the frequency of preventive maintenance audits is important for maintaining the effectiveness of maintenance practices and ensuring compliance with regulatory requirements. Several factors influence the frequency of audits within an organization:
1. Equipment Criticality
The criticality of equipment or assets plays a significant role in determining audit frequency. High-risk equipment, whose failure could lead to significant safety hazards, production losses, or environmental impact, may require more frequent audits to ensure their reliability and integrity.
2. Regulatory Requirements
Regulatory agencies often mandate specific audit frequencies for certain industries or types of equipment to ensure compliance with safety, environmental, and quality standards. Organizations must adhere to these regulatory requirements and schedule audits accordingly to avoid penalties or fines.
3. Maintenance History
The maintenance history of equipment can provide insights into its reliability, performance, and vulnerability to failure. Equipment with a history of frequent breakdowns or maintenance issues may warrant more frequent audits to identify underlying problems and prevent future failures.
4. Operational Environment
The operational environment, including factors such as temperature, humidity, dust, and vibration, can affect equipment performance and reliability. Harsh operating conditions may necessitate more frequent audits to monitor equipment health and address maintenance challenges proactively.
5. Organizational Policies
Organizational policies and internal guidelines may dictate audit frequencies based on risk management strategies, budgetary constraints, and resource availability. Organizations should establish clear policies for audit frequency to ensure consistency and alignment with strategic objectives.
6. Industry Best Practices
Industry best practices and standards may recommend specific audit frequencies based on historical data, industry benchmarks, and expert consensus. Following industry best practices ensures that organizations stay abreast of emerging trends, technologies, and regulatory requirements in maintenance management.
7. Change in Operations
Changes in production volumes, equipment usage, or operating conditions may necessitate adjustments to audit frequencies. Organizations should periodically review and reassess audit schedules to adapt to changes in operational requirements and mitigate emerging risks effectively.
8. Continuous Improvement Initiatives
Organizations committed to continuous improvement may opt for more frequent audits as part of their proactive maintenance strategies. Regular audits facilitate the identification of opportunities for optimization, innovation, and performance enhancement in maintenance practices.
Best Practices for Audit Scheduling
To optimize the effectiveness and efficiency of preventive maintenance audits, organizations should adhere to best practices for audit scheduling:
Establish a Risk-Based Approach
Prioritize audit scheduling based on equipment criticality assessment matrix, regulatory requirements, and risk assessments. Focus on high-risk assets and critical systems that have the greatest impact on safety, production, and compliance.
Define Clear Audit Criteria
Develop clear audit criteria, objectives, and methodologies to guide audit scheduling decisions. Ensure that audit criteria align with organizational goals, regulatory requirements, and industry best practices.
Regularly Review Audit Frequency
Periodically review and reassess audit frequencies based on changes in equipment condition, operational requirements, and regulatory mandates. Maintain flexibility to adjust audit schedules as needed to address emerging risks and opportunities.
Integrate Audits into Maintenance Plans
Integrate audit activities into overall maintenance plans and schedules to ensure consistency and alignment with operational priorities. Coordinate audit schedules with planned maintenance activities to minimize disruption to ongoing operations.
Utilize Technology and Automation
Leverage technology and computerized maintenance management systems (CMMS) to automate audit scheduling, data collection, and reporting processes. Utilize predictive maintenance and condition monitoring techniques to optimize audit frequencies based on equipment health and performance data.
Promote Collaboration and Communication
Foster collaboration and communication between maintenance teams, operational staff, and management to coordinate audit scheduling, share insights, and align audit activities with organizational goals. Encourage feedback and participation from stakeholders to enhance the effectiveness of audit processes.
Monitor Audit Performance
Continuously monitor and evaluate the performance of audit processes, including timeliness, thoroughness, and effectiveness. Collect feedback from audit teams, stakeholders, and external auditors to identify areas for improvement and implement corrective actions as needed.